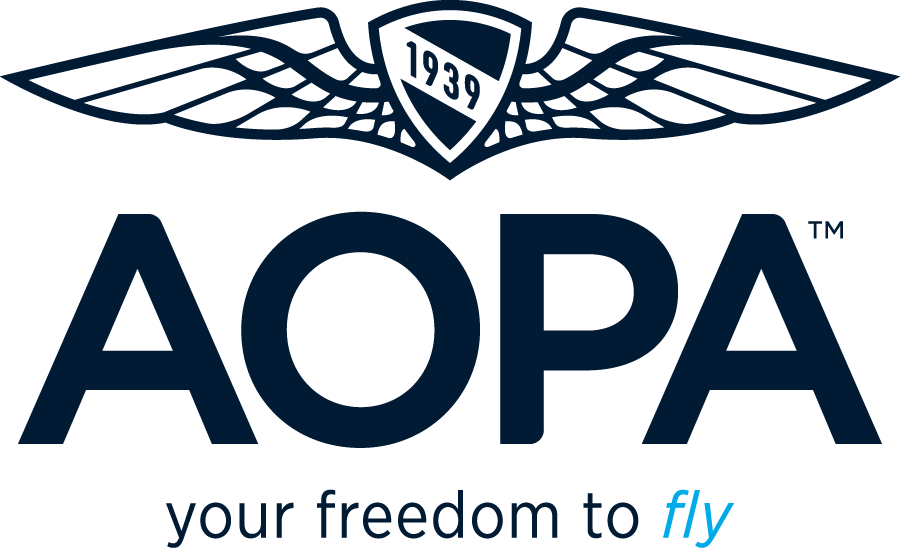
Mooney Ovation
To many in the general aviation community, the words Mooney and efficiency are synonymous. With a sleek fuselage and flush-riveted surfaces on much of the wing, Mooneys have always been top competitors in their class. Therefore, it was not surprising that some Mooney aficionados gasped when the company introduced the Ovation with its big-bore Continental engine. The Ovation is a commonsense kind of airplane. It extracts sizzling performance from a tried-and-true engine and airframe, yet makes life easy for the pilot by embracing sophisticated and modern systems.
The Ovation's faster sibling, the TLS, gets its 220-knot maximum cruise speed by utilizing a turbocharged 270- horsepower Lycoming TIO-540 engine. The turbo'd airplane is terrific for those who need to fly high and for those who don't mind paying the higher acquisition, fuel, and maintenance costs associated with such an installation. But until the Ovation debuted in 1994, Mooney customers who didn't need a turbo were shown the MSE, an efficient 200-hp, 168-knot airplane, but one that uses a shorter fuselage.
The Ovation, then, filled a gap in Mooney's lineup. Its normally aspirated 280-hp Continental IO-550-G allows a max cruise speed of 190 knots in the comfort of the TLS's 20-inch- longer fuselage. Like the TLS, the brawny Ovation carries with it enough redundant systems to get it through almost any inflight crisis short of an engine failure.
An engine-driven vacuum pump normally drives the Ovation's gyros, but another engine-driven pump is always in standby. A 100-amp alternator powers the electrics, but if that packs it in, two batteries pick up the slack. If you run down a battery in an attempt to start the engine on a cold morning, flip the switch and bring on the fresh one.
Ovations equipped with Mooney's certified TKS anti-ice system come with even more redundancies. The Ovation is the first normally aspirated piston-powered single to be certified for flight into known icing. The certification criteria demand complete electrical redundancy for the two pumps that push the anti-ice fluid through tiny holes in the titanium leading-edge skins. The fluid keeps ice from adhering to the surfaces. Ovations with the TKS option come with two alternators, using up one of the engine pads typically occupied by the standby vacuum pump. In that case, an electric standby pump is placed in the tailcone — a normal configuration for the TLS, which comes standard with two alternators and two batteries.
The Ovation brings much versatility to the pilot. A turbocharged airplane is at its peak up high; most normally aspirated airplanes don't produce much power above 10,000 feet. The Ovation, though, performs well in either regime and in between. Fly high, fly low, fly fast, fly far, the Ovation has a mission profile to fit the job.
But its 280 hp notwithstanding, the Ovation's Continental IO-550-G engine brings with it a fuel efficiency that a Mooney lover can appreciate. The Continental-claimed fuel specific of 0.38 pounds per horsepower per hour comes in part from the tuned induction system. The engine's induction-air intakes drape across the top of the engine like a tarantula sunning itself on a rock. By equaling the distance the air travels to each of the cylinders, the induction system assures a nearly balanced mixture of fuel and air in each cylinder.
A more equal fuel/air distribution means a smoother- running engine — which is noticeable in the Ovation — and the ability to lean the mixture more aggressively, since all cylinders should peak at about the same fuel flow.
Other IO-550 models typically put out 300 to 310 horsepower while turning at 2,700 rpm. Continental limits the rpm to 2,500 in the -G variant, derating the engine to 280 hp but upping the published TBO to 2,000 hours from 1,700 in other normally aspirated IO-550s.
To the Ovation pilot, the derating means simplified engine operation. For takeoff, put all the levers forward. They can stay that way through about 5,000 feet msl. Thereafter, in the climb, a flick of the mixture control every thousand feet or so will keep the exhaust gas temperatures in the blue arc on the EGT gauge. Upon leveling off, the pilot, if desired, can leave the throttle and prop full forward and lean normally. And without any cowl flaps to contend with, the Ovation comes about as close to a single-lever power control as you'll find in today's market.

Piper Launches New M600 and M350
Piper Aircraft president and CEO Simon Caldecott delivered a 1-2-3 punch of energy to the sub-6,000-pound general aviation market on April 13 when he introduced the M series of piston and turboprop singles (formerly the PA-46 series) and a new flagship at a celebration at the company’s 750,000-sq-ft manufacturing plant in Vero Beach, Fla. The M series starts at $1.1 million and ranges upwards to a little less than $3 million for a fully loaded top-of-the-line model.
First to be undraped was the M500, formerly the Meridian, featuring the leather interior (complete with USB and AC power ports) that Boston-based Blokx Design created for the full M series. The upgrade is in addition to the improvements announced in January. Those upgrades were necessary to bring it up to par with the two new M-series airframes. Each of the M series sports a full Garmin glass cockpit; digital capacitive fuel quantity sensors; digital pressurization; Aspen Avionics EFD1000 standby flight instruments; electronic stability control; auto go-around function; and stall protection. Iridium connectivity is an option.
M350
Next to be unveiled was the smaller, piston-powered M350 (formerly Mirage), a six-seat, 350-hp Lycoming TIO-540-AE2A-powered single capable of 213 knots max cruise and a range of 1,343 nm for $1.15 million. Caldecott said Piper’s engineers have revamped this pressurized airplane by maximizing the functionality of its Garmin G1000 avionics. “We have added electronic stability protection, underspeed [stall] protection and automatic level mode... and both the M350 and the upcoming M600 can now safely fly unassisted to lower altitudes in the rare case that the pilot is non-responsive at high altitudes,” Caldecott said. (Because of a variation in the M500’s Vmo, its autopilot does not have the emergency descent mechanism activated.)
Some recent high-profile accidents were caused by hypoxic pilots who either flew the aircraft outside its envelope or simply fell unconscious and stopped flying the aircraft altogether. The M350 is often the first pressurized aircraft pilots fly into the flight levels, so Piper created a stability safety zone for it that is more than just a “level up” button on the panel (similar to the Garmin-based Cirrus Perspective product). Combating loss of control, the autopilot polices the aircraft envelope, insistently nudging it back into safe flight parameters. It won’t let the aircraft stall, either, taking over and pushing the nose down, which should inspire the pilot to add power. (Without input the aircraft will drift down in an unstalled, controlled state. There is no autothrottle.)
Hypoxia prevention is integrated in the G1000 with a pilot-worn pulse oximeter and a carbon monoxide warning system, but that is just the passive side of the mechanism. Above 14,900 feet msl, if the system does not “sense” the pilot at the controls every few minutes it cues the pilot with the question, “Are you alert?” If the pilot does not answer correctly the autopilot takes the aircraft to below 14,900 feet msl, then asks the question again, demanding pilot input. If it receives no input, it will complete the controlled descent to about 12,000 feet msl and ask again. A similar emergency descent mechanism (EDM) is an option on Cirrus aircraft equipped with the Garmin GFC 700 autopilot. Caldecott announced that the M350 received its FAA certification on April 13.
M600
Finally, Caldecott pulled the cover off what he described as a clean-sheet airframe that will cap the M series properly. The Piper M600 turboprop is not a Meridian, but to look at it there is no question from whence it came. It is also clear at first glance, however, that the M600 sports a different wing: gone are the vortex generators littering the top surface; also gone are the extended swept-back leading edges at the roots; and new wingtips are twisted up into mini-winglets. Beyond that the new wing holds more fuel, promising more range. Powered by a Pratt & Whitney Canada PT6A-42A flat-rated to 600 shp, the M600 carries up to six people at a maximum cruise speed of 260 knots; max range is 1,300 nm with 45 minutes reserve. Its maximum payload is 1,200 pounds, and full fuel is 1,768 pounds. With all the seats filled it can still go 1,000 nm, a considerable bump over the M500, whose PT6A-42A is flat-rated at 500 shp and fed by a maximum of 1,156 pounds of fuel.
In the M600 panel there is a triple-screen Garmin 3000 suite paired with dual GTC 570 touchscreen controllers, backed up by the Aspen Standby 1000EFD. The additional performance provided by the wing and engine, combined with the safety features of the GFC 700 autopilot with enhanced automatic flight control system (AFCS), hypoxia prevention and EDM, ADS-B in/out and onboard radar, make the M600 a capable aircraft for a base price of $2.82 million. For passengers, its cabin comfort and richness are on par with larger aircraft. The interior features ergonomic seating with integrated lumbar support and some adjustability of the recline angle. Side panels hide retractable lightweight, laminated woodwork tables; oversized brushed-aluminum cup holders are ready to handle a Starbucks Venti.
“Our customers and dealers asked for an aircraft with more payload and range,” said Caldecott during the unveiling. “We listened and we delivered. With the advent of the M600, we have given our customers an option to travel nonstop from New York to Florida,” he said.
Launch customer Scott Middleton, a businessman whose first aircraft was a Piper Seneca, told AIN, “This airplane is going to be a game-changer for my flying; I saw that halfway through the presentation, and I asked, ‘Where do I sign up?’”
Piper expects to receive FAA type certification for the M600 in this year’s fourth quarter, in time for deliveries to start next year. So far, the aircraft has logged 800 hours of flight-testing over 470 flights. “The first 12 months’ production of the M600 is fully allocated to our worldwide dealer network,” said Caldecott.

We Fly: Beechcraft Bonanza
Today’s Bonanza is still in many ways the same kind of airplane the original was: fast, practical and stylish. While the airplane has morphed through the years, the Bonanza’s riveted metal and low-wing design has stood the test of time.
Beech launched the G36 in 2005 to usher in the era of flat panel avionics with the introduction of the Garmin G1000 fully integrated, WAAS-capable avionics — the “G” part of G36 is for Garmin. At that time, the Bonanza became the first platform with the integrated GFC 700 autopilot, a huge improvement over the G1000-Bendix/King KAP 140 autopilot combination that early G1000 platforms used.
Since the GFC 700 is fully incorporated into the G1000, the buttons for the GFC 700 are easier to access than the separate KAP 140 box was, and as would be expected, the action of the integrated system appears to be smoother and slightly more precise. Both autopilots can be coupled to IFR approaches, but some helpful functionality improvements with the GFC 700 are the inclusion of a flight director on the G1000 PFD, the ability to climb and descend at a set airspeed (a mode called flight level change, or FLC), and improved missed approach features.
In addition to the GFC 700 integration, the G36’s G1000 includes synthetic vision, XM weather, XM radio, traffic and WAAS-enabled precision approach capability. The Garmin charts, which incorporate the highly useful safe taxi feature, are included with a one-year subscription. Jeppesen’s chart view can be added for an additional $6,900.
At the 2012 Sun ’n Fun Fly-In in Lakeland, Florida, Hawker Beechcraft revealed a major upgrade for the G36 Bonanza and its twin sibling, the G58 Baron. The interior was completely redesigned with new sidewalls, seats and creature comforts. The seats, which were created by Millennium Engineering in Wichita, Kansas, are beautifully shaped, have adjustable headrests to provide comfort for occupants of varying heights and are made of variable density foam to keep the backsides of the occupants comfortable.
But perhaps the biggest improvement in the 2012 upgrade package is the CabinComfortPlus environmental system. The new system provides air inlets for all passengers — a major improvement from the previous system, which had only five inlets in the cockpit and none in the rear, according to Beechcraft’s sales director Kelly Harper.
“I was completely foreign to what climate control in a small airplane was, and it is a pure luxury, especially on days like today — 90 degrees,” says José Santana, associate vice president of leasing at the Segall Group in Baltimore. Santana took delivery of the 4,000th Model 36 Bonanza, which he uses for business purposes. “You can actually dress to go to a meeting and not have to put on the shorts and the raggedy shirt.”
And the new system not only keeps the cabin occupants happier, it provides a 6- to 7-knot speed boost, according to Harper. The speed increase is due to the lack of the exterior air scoop, which was part of the previous model G36’s environmental system.
Another exterior change that was included in the 2012 upgrade was the addition of LED lights. These lights have better longevity and visibility than the previous lights, but Beechcraft was not able to incorporate the nav and strobe lights into the wingtips, where the old lights were encased. The protruding LEDs make the wingtip look a little bit experimental compared with the superb fit and finish of the rest of the airplane. The good news? The lighting system is designed to last longer than the airplane itself, according to Beechcraft, so operators may never have to change any light bulbs.
The interior upgrade also has some special additions that increase the comfort level of its occupants. At the base of the redesigned center console are two cup holders. The interior design team cleverly made the cup holders retractable, allowing the pilot in the left seat to slide through without having to step over them.
But regardless of the fact that it is quite easy to slide through the cockpit to the pilot-in-command’s seat, the lack of a cabin door on the left side is not ideal. Incidents and accidents are rare, but having the ability to get out on either side is definitely desirable. The rear passenger door, however, is massive and makes ingress to and egress from the aft cabin very quick and easy.
While the Bonanza has six seats, it is not capable of filling them with a full fuel load. The airplane I flew has an empty weight of 2,627 pounds, leaving just 1,036 pounds for fuel, passengers and cargo to max out at 3,663 pounds. The 74-gallon fuel load leaves room for an additional 592 pounds, about three average-sized adults and one child.
Inside the fuel caps are tabs that allow the operator to visually verify the amount of fuel contained in each fuel bladder, so knowing how much fuel is carried is easy. At the bottom tab, you have 54 gallons of usable fuel, and with a fuel burn of about 15 gph and a cruise speed of around 170 knots, you can still travel about 500 nm with reserves and welcome another 120-pound passenger.
Another way to increase the load capacity is to remove some of the seats, which is quick and easy to do. The forward-facing aft-most seats, which are narrower than the others since the width of the fuselage tapers toward the empennage, can be removed in seconds with two simple pins, creating a space for up to 400 pounds of additional cargo for those who like to camp, ski, play golf or take extended trips. The middle row of seats can also be removed, making room for two-hundred pounds of cargo in their stead.
In lieu of removing the seats, you can fold down the backrests of the middle seats or rotate them so that they are facing forward instead of aft. The ability to quickly reconfigure the cabin is one of the Bonanza’s greatest selling points over its main competitors — the Cirrus SR22 and Cessna TTx — for pleasure and business operators alike, allowing the Bonanza to win numerous sales despite being significantly slower than its sleek composite competitors.
Santana looked seriously at the SR22 as an alternative to the Bonanza. “The cabin won over the chute,” he says. “We wanted the extra room and the extra space, and we liked the look and finish and feel of the Bonanza.”
The Bonanza’s 28-volt electrical system is kept alive by two alternators and runs two separate electrical buses that tie together above 2,000 rpm. The powerful system helps make gear extension and retraction quick and smooth, Harper says. Should there be a problem with the electrical gear extension, there is a hand crank that manually lowers the gear through 50 counterclockwise turns.
The landing gear is really beefy. It’s identical to that of the Beechcraft Baron, which boasts a gross weight almost 1,900 pounds greater than that of its single-engine sibling. The Bonanza is built to be tough in general. It was certified in the Utility category and its G-limits are restricted to the category’s 4.4 positive and 1.76 negative limits, provided the flaps are up.
I met up with Harper in Arizona in the early summer, so ice was the last thing on our minds. But in other seasons and climes, the white menace must be considered. The only standard ice protection Beechcraft provides for the Bonanza is the pitot heat. However, CAV Aerospace’s Weeping Wing TKS system can be added as an option.
It was a typical hot, dry day at Scottsdale Airport when I was introduced to a brand-new factory demonstrator, appropriately registered N136HB since it was built during the Bonanza’s Hawker Beechcraft days. Thankfully the airplane was parked in a hangar, where Harper and I went through the preflight.
Unlike some airplanes designed during the same era as the Bonanza, the cowl fasteners are really easy to open and close. Each side of the cowl opens fully, allowing the pilot to take a close look at the engine and all of its accessories. “You can touch it, feel it, more than just checking the oil,” Harper says.
It didn’t take long for the cockpit to heat up after the airplane was pulled out onto the black tarmac. There is no key required to start up the airplane. Instead, the starter is activated by a turning switch. The Bonanza started up without a hitch, and we set the air conditioning to 55 degrees Fahrenheit for maximum cooling.
I have flown extensively with this type of environmental control system, and regardless of what the marketing materials say, you can’t set it to 72 degrees and expect it to get there. But with the lowest setting, it didn’t take long before we were comfortable in the cockpit, even though the G1000 indicated that the outside air temperature had already reached 35 degrees Celsius — a sweltering 95 degrees Fahrenheit.
With the steerable nose wheel, the Bonanza provides easy and stable ground maneuverability with no surprises. The ground roll was long by normal Bonanza standards — I estimated about 1,600 feet — but with ISA+22 conditions, the propeller didn’t have much to grab on to.
The Bonanza version of the G1000 offers a cruise climb schedule for fuel flow with a cyan arrow underneath the fuel flow gauge that gives guidance for leaning during the climb. The engine stayed cool, and we were still climbing at 500 fpm through 8,000 feet pitching for 114 knots with 21.9 mp and 2,500 rpm. We also engaged the yaw damper, which helped smooth the ride in the turbulence that started to develop over the Arizona desert.
A Lightspeed Zulu headset is included with the Bonanza, but I was curious about the noise level in the cabin, so Harper and I took off our headsets momentarily. I was pleasantly surprised to find that we could still communicate without screaming at each other, a testament to the tight door seals.
We leveled off at 11,500 feet and saw 166 ktas burning 15 gph at a 25 degrees rich of peak setting. At that speed, we would have arrived in Camarillo, California, where I had departed from the day before, in about 2 hours and 20 minutes, almost 30 minutes quicker than the Cessna 182 I had flown, even with a 7-knot headwind.
The Bonanza is a beautifully harmonized airplane. In normal flight, it is a pleasure to hand fly. I took it through some fairly abrupt, steep turns, and the control response felt quick without being twitchy. I also flew the airplane around at 70 knots, a speed at which the Bonanza still flies with great stability, and tried a few power off stalls, which produced a slight buffet at 53 knots, five knots below the published stall speed.
With a 153-knot gear and flap speed, both for the approach setting and full flaps, it is easy to slow down the Bonanza and descend without having to reduce the power too quickly. In my previous experience with the environmental system, I’ve found the cabin gets warmer during the descent in hot weather. Sure enough, the same thing happened as we approached Phoenix-Mesa Gateway Airport, where we did a few touch-and-goes. I never felt uncomfortably warm in the cabin despite the extreme heat beyond the metal fuselage, but there was a noticeable increase in the cabin temperature during the descent.
Landing the Bonanza was easy with Harper’s verbal guidance. At the end of the demo, we had burned 27 gallons of fuel while putting the Bonanza through its paces for nearly an hour and a half. The new seats produced no pressure points during that time, and the well-designed ergonomic cockpit made me feel completely at ease. I could have flown the G36 back to Camarillo alone.
In addition to the Bonanza’s terrific handling characteristics, luxurious cabin and the history behind Beechcraft, Santana’s final decision to go with the Bonanza over the Cirrus was its resale value. According to the listing prices on controller.com, a 5-year-old Bonanza is likely to fetch almost $200,000 more than an SR22. One reason is the lower production schedule. Beechcraft produced just a few dozen Bonanzas each year during the past few years while Cirrus produced around 200 SR22s and SR22Ts.
The conservative production schedule may be one strategy to keep this terrific airplane in production for several more decades. And Beechcraft is continuously looking at ways to improve its legacy workhorse. “We’re not standing still,” says Jeff Sites, product marketing manager at Beechcraft. “We’re definitely looking at all of the latest regulatory and environmental issues and new technologies that are available.”
With the challenges that 100LL has presented in the past few years, one of the considerations that Beechcraft is seriously looking into is a diesel engine for the Bonanza. But it is not likely to be introduced any time soon. “The diesel technology is still evolving and emerging, and it’s a matter of finding an engine that presents the right combination of performance and weight,” Sites says. “As with any new technology, we’re not going to go through with something just to do it. We’re going to make sure we do it right.”
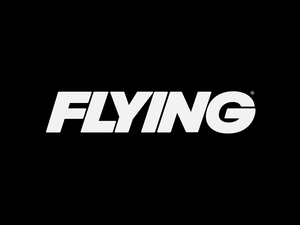
Mooney Ovation 3
At first glance the newly certified Mooney Ovation3 looks like just another Mooney (which, granted, is a little like saying "just another Porsche.") But behind the familiar long-body lines are a couple of big changes.
Even before the Ovation3 came along, these airplanes were fast, and over the past few years they've gotten faster, and they've still got those great Mooney lines that have enchanted loyal owners for decades. Over that time, Mooneys havetypically come out of the factory equipped with great panels, and today's Mooneys have the best panels yet, with the Garmin G1000 integrated avionics suite and now the Garmin GFC 700 digital autopilot. For added comfort and utility, you can get upgrades like air conditioning and known-ice-approved TKS. And I don't care what you say, despite Cirrus and Columbia having really fast fixed-gear airplanes, there's something that just feels right about retractable gear on a high-performance airplane. I've gotten used to it on the Cirrus, but the idea of a fixed-gear Mooney sounds blasphemous. (And you can save your emails: I know they built a couple fixed-gear models back in Eisenhower's day.)
So what is it about the Ovation3 that makes it so special?
Power, that's what. In terms of horsepower and electronics, the Ovation3 is the most powerful Mooney, and with the possible exception of the just-certified turbocharged Acclaim, it's also the most sophisticated airplane Mooney has ever put its name on.
The pony-power part of the equation was the easy part. Well, at least it seems that way. The engine powering the Ovation, the Continental IO-550 series, is commonly rated at 310 hp in airplanes like the Cirrus SR22 and Columbia 350, but the max horsepower of Mooneys using just about the same engine has always been 280, which is essentially "achieved" by turning down the max engine rpm to 2500, instead of the 2700 rpm of the IO-550 in the Cirrus and Columbia, among others. Mooney gets back that horsepower by using a mod engineered by Midwest M20 Mooney. The STC simply boosts the power back up to 310 horses by allowing the prop to turn at 2700 instead of 2500 rpm, which is the redline on other versions. Mooney also adds a three-blade Hartzell prop. Now with FAA approval for the mod, Mooney performs the STC in-house as part of the production process.
With the STC, the Ovation is approved for max continuous operation at 2700 rpm; although there is a "maximum recommended cruise power" setting of 262 hp and 2550 rpm, you can cruise at the higher power setting if you want to. As you'd expect, the cruise speeds on the Ovation3 are very good at typical cruise altitudes, between 5,000 and 8,000 feet, but the fuel consumption numbers go way up as you push the prop lever forward. In the Cirrus, I'm used to seeing close to 20 gph at best power and 2700 rpm, which is very similar to the fuel flows I saw in the Ovation3.
The Ovation3 comes standard with the G1000 flat-panel avionics system, but the G1000 isn't set up to show the new redline on the engine of 2700 rpm. So there are a couple of placards that advise you to use "the G1000 tachometer for reference only," and an additional "official" tachometer is added to the panel, presumably so the pilot can see the proper placement of the green and red colors there.
I had a chance to fly the Ovation3 with Brian Kendrick, Mooney's chief pilot/inspector, out of Kerrville, Texas, earlier this year. It was anything but a typical general aviation day in Central Texas when I launched out of Austin, located just about 40 SR22 minutes east of Kerrville. The weather was just over minimums at Austin, and it was only slightly better at Kerrville (KERV). But it was still just better than minimums because KERV's only approaches are non-precision ones. And the wind that day was howling. At 6,000 feet, the wind vector on the Avidyne PFD was showing winds from the south at 57 knots, so I had a hellacious crab angle as I motored my way toward Kerrville, getting slammed and bammed around the cockpit as I went.
While the ride into Kerrville was pretty wild, the wind on the ground wasn't so bad. The AWOS had it just about down the runway at 18 gusting to 25 knots. The landing was uneventful, but more on the approach later. Once the SR22 was safely in the hangar at Mooney, I headed over to the reception office to meet with Brian, and spent a little time talking about the autopilot and its G1000 interface.
While the GFC 700 is an incredibly capable autopilot, pilots who fly with a rate-based S-Tec or Bendix/King autopilot needn't be intimidated by it. There are some important differences, though, both in system architecture and operation.
Even though the GFC 700 has been certified on several general aviation airplanes, the system is still not widely known or well understood. Integrated nicely with the G1000 avionics system, the GFC 700 is an attitude-based dual-channel, digital two-axis (pitch and roll) autopilot with flight director driving smart servos. In the Mooney, the autopilot is controlled by the PFD and a control unit mounted by the pilot's side of the center-mounted MFD. There's also a go-around function, with a console-mounted switch just ahead of the throttles and a control-wheel steering button on the yoke.
In terms of flying the airplane, it's important to start thinking seriously about vertical navigation. With the GFC 700, you can set in your rate of climb or descent, which is pretty common on GA autopilots. But the part that was brand new to me was the FLC button, which allows you to set your indicated airspeed. This airspeed-hold capability is known on the GFC 700 as the "flight level change" function, which is shortened to "FLC" on the control unit and simply called "filch" by pilots. Once you get used to using it, you won't want to go back.
The airplane flown for this report was one of the first Ovation3s off the line at Mooney's Kerrville, Texas, factory. It was equipped with the Garmin G1000 avionics package, including two 10.4-inch displays, and the Garmin GFC 700 three-axis digital autopilot. The G1000 also includes the XM WX weather information utility and XM Radio satellite radio, TIS traffic alerting system, terrain awareness and Jeppesen instrument approach charts. (Some capabilities are optional or require a service fee.) As an Ovation3, the airplane had the Mooney factory-installed STC horsepower increase, which includes a modification to allow the prop to turn at a maximum of 2700 rpm and a three-blade Hartzell aluminum propeller. All performance figures are from the manufacturer and unless otherwise noted are for standard conditions.
In general, it's best to use the FLC function for climbs and the vertical speed button for descents. This approach lets you control the two most important elements in both phases. On descent, it allows you to dial in a rate that gets you down to your desired altitude efficiently but not so steeply that you get too fast or make it tough on your passengers' ears (or on yours). Conversely, when you're climbing, the FLC function-remember, that's essentially an airspeed hold-helps keep you from stalling the airplane, which can happen if you set too high a rate of vertical speed on climb, and the airplane attempts to hold that rate despite decreased performance in higher, thinner air. Once you get used to these features, and with the vertical nav presets in the G1000 flight planning page, you can create and fly an entire flight plan from just after takeoff to short final both vertically and laterally. The capability is tremendous. The performance is, too. More on that later.
When Brian and I hopped into the pretty new Ovation3 sitting on the ramp, we were already filed. Kerrville was quiet, as the field was IFR and had been all day long. We picked up our clearance and took off, battling the bumps as we went. The majority of our flight, up to Junction, down to San Antonio and back up to Kerrville, was flown in the soup and with the autopilot engaged. So it was an excellent test of the G1000 and the GFC 700. We flew the ILS Runway 12R approach at San Antonio on a busy IFR day. The GFC 700 kept the "needles" centered as we intercepted the localizer, and it kept the glideslope indicator right there, as well, as we started down.
It's not very often that you get to do a side-by-side comparison of two competitive products, but I was lucky enough to get the chance that day, as I'd flown my shared ownership Cirrus SR22, which has an S-Tec 55X autopilot, on the Runway 12 GPS approach at Kerrville earlier that day.
On the approach to Kerrville in the SR22, I set up the S-Tec 55X to fly the vertical portion of the GPS Runway 12 approach to Kerrville. Considering the conditions, it was a tall order. And for the most part, the autopilot did an excellent job of it; as good as any rate-based autopilot could be expected to do. But the 90-degree turn on to the final approach course, which required negotiating a nearly 60-knot change in headwind component, was a real challenge, and the unit commanded two good-sized correction turns as it narrowed down the focus on the desired track. A couple more, much smaller corrections and we were on course. And once we were, the 55X did a good job of holding course, even given the strong turbulence that day.
A couple of hours later when I flew the same approach, only this time in the GFC 700-equipped Ovation3, the difference was compelling. The GFC 700 made the track course change and had us flying down the final approach course with no hunting at all. Unlike with rate-based autopilots, there was no waiting or wondering involved, just a solid, predictable intercept and new track. And on altitude level offs, the performance of the new Garmin autopilot was equally impressive, smoothly and efficiently beginning the level off at just the right time. In fact, the process took me a little getting used to, as I was a little concerned the autopilot was going to miss the pre-selected altitude, but it didn't. The difference is that, unlike some other popular autopilots, it keeps the climb at an optimum rate until it needs to back off to hit the target, which is does with precision.
The high-end auto-flight package is nice to have because the Ovation3 is a fast airplane. At high-speed cruise at 8,000 feet, with the power set at 2700 rpm, max manifold and mixture set for best power, the Ovation3 can achieve 197 knots. With the power pulled back to 2550, the cruise drops off by five knots or so, putting it in the same neighborhood as the Ovation2, which is a pretty nice neighborhood, if you're lucky enough to live there. For pilots who typically cruise below 10,000 feet, the boost in power is a real bonus. And with the optional 130-gallon fuel capacity, you can go a long way down the airways in the '3, though the max advertised range of more than 2,400 nm (!) is achieved at an absurdly miserly economy power setting. Still, with the prop dialed up to 2700 rpm and putting 20 gallons an hour through the IO-550, you'd still see around 1,200 miles of no-wind range with VFR reserves, according to my calculations. That's about as long as I'd ever want to sit in any single-engine airplane.
The speed is nice, but perhaps the biggest improvement comes in climb and runway required, where the combination of the three-bladed prop and the extra rpm add up to significantly improved performance. Mooney claims a takeoff roll of just 900 feet at max takeoff weight and a rate of climb of 1,300 fpm. On my flight we were light, and the gusty conditions made it impossible to get an accurate idea of just how fast we were climbing. But suffice it to say that the 1,300 fpm was well on the low side of what we were seeing on the VSI.
What you don't get with the Ovation3 enhancement is added weight, so you have the same kinds of limitations in the '3 as you do in other Mooneys. Mooney lists the same useful load for the Ovation3 as it does for the standard Ovation2 model. With full standard (102 gallon) tanks, that gives you the ability to carry a couple of reasonably sized adults and a couple of bags.
And in the Ovation3 you'll do that at high speed. It is, after all, the fastest normally aspirated single-engine piston airplane in production. And with the new Garmin G1000 avionics suite integrated beautifully with the GFC 700 autopilot, you'll be flying with the same package as you'd get in some pretty cool twinjets.
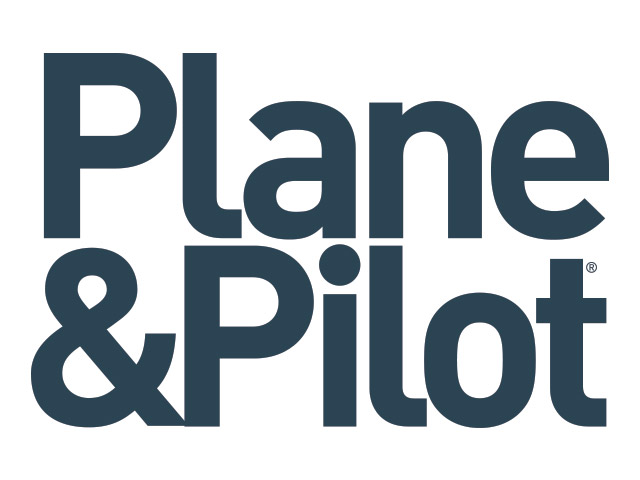
Mooney Ovation 3: Turbo Performance Without The Turbo
Say what you will about American cars, but America builds some of the best civilian airplanes in the world. In the lower rungs of general aviation, especially trainers through four-seat retractables, American flying machines have virtually no equal.
Take, for instance, the Mooney M20R Ovation 3. The current M20R is a third-generation Mooney, the beneficiary of a half century of development. Designer Al Mooney inarguably got it right the first time out of the box back in the 1950s when he created his four-seat M20. While today's airplane is light-years ahead of its ancestor in performance, comfort, systems, aerodynamics and electronics, you can still see the heritage of design—the arrogant, vertical tail; short, rubber doughnut gear; and tall baggage compartment.
Though it may not be the airplane Luke Skywalker would fly, the basic four-seat Mooney has aged at least as well as Christie Brinkley (who, more than coincidentally, is the same age) while nearly doubling climb rate and adding almost 100 knots to cruise speed.
In fact, Mooneys have consistently enjoyed speed disproportionate to their horsepower. The type has been among the world's fastest and most efficient personal airplanes since its inception. Today, the Mooney Acclaim S is the acknowledged leader in the turbocharged class, notching near-turboprop speeds on a measly 280 hp.
Similarly, the Ovation 3 is the quickest normally aspirated single—quite simply (or not so simply) the fastest production airplane above the planet without a blower under the bonnet. The Ovation 3 features essentially the same 310 hp Continental engine used on the Cessna Corvalis 350 and the Cirrus SR22-G3. (The only significant differences are associated with repositioning some items to accommodate the Mooney's retractable nosewheel.)
Mooney's Ovation 3 is actually an STC developed by Midwest M20 Mooney (www.midwestmooney.com) of Flora, Ill., but performed at the factory for the buyer who wants 310 hp rather than the standard 280 hp. The 3's Continental is rated for max continuous power at the 2,700 rpm redline, rather than the 2,500 rpm limit on the Ovation 2. The airplane can also cruise at the full 2,700 rpm, or you can pull back to 2,550 rpm, worth 262 hp or 85% power. Again, however, remember that the same engine is rated for as much as 350 hp in other applications, so the 262 hp limit represents only 75% of the max rating.
Combine big horsepower with a low drag coefficient (0.019) and you have the makings for a truly quick airplane. I recently did a story for this magazine titled "Looking For 200 Knots" [P&P July 2009], and it was interesting that all the true 200-knot contenders were turbocharged. There was only one normally aspirated airplane that threatened to sneak into the class, the Ovation 3, with a 197-knot top speed.
The 3's speed is an example of what can be done with excellent aerodynamics in combination with copious horsepower. The laws of aerodynamics are fairly immutable; drag increases as the square of speed. Every additional knot is exponentially more difficult to achieve, and the Ovation 3's brevity is all the more amazing in the thick air of low altitude.
Like so many other current Mooney buyers, Dr. Larry Marshall of San Diego, Calif., has owned a Mooney before. In his case, a totally tricked-out 1965 M20C, but he switched to a Turbo Skylane a few years ago to try the benefits of turbocharging. Marshall purchased his totally blissed-out Ovation 3 late last year as a replacement for the T-182.
"The Skylane was a great airplane," says Marshall, "but Rhondi and I found we rarely employed the turbocharger, and we wanted more speed in the bottom two miles of sky, where we operate most of the time."
Marshall's airplane is fitted with practically every option Mooney offers except TKS, the latter rarely a requirement in the Southwest. The equipment list includes the ultimate creature comfort, air-conditioning, a 66-pound extra that reduces payload proportionately.
Okay, here come the numbers. With every option tallied, Marshall's fully equipped Ovation 3 weighs in at a hefty 2,424 pounds against a 3,368-pound gross weight. That leaves a 944-pound useful load. Subtract 100 gallons of fuel, and payload is reduced to just under 350 pounds. In Marshall's case, that works out just fine, as he and his wife weigh only about 320 pounds collectively, and baggage makes up the difference.
Creature comfort is always dependent on the size of the creatures, and the Ovation's cockpit can ensconce pilots as tall as six-foot-six. The cabin is 43.5 inches across by 44.5 inches vertical, wider than an A36 Bonanza, but not as tall. Seating position is semi-supine (laid-back), however, so modern Mooneys are hardly cramped.
The Marshall Mooney also features the Jose Monroy 130-gallon, long-range tanks, in case you're one of those strange folks who likes to endure for 10 hours at a time. The bottom line is an airplane that can fly much longer than most pilots are willing to sit, but only with two lightweights up front.
(Of course, if you can make do with the standard 100 gallons, you can still endure for 5.5 hours at about 185 knots and enjoy a range of just over 1,000 nm. That ought to be enough for anyone who's not silly enough to fly across an ocean.)
The most immediate and obvious benefit of more power comes in climb. With 310 hp on tap and only 3,368 pounds to lift, the Ovation 3 sports a low 10.9 lbs./hp power loading. All other factors being equal (which almost never happens), a low power loading generally translates to good climb performance.
Better still, climb seems relatively unaffected by load, and it seems to go on forever. Back in the 1990s, I delivered nine Ovations overseas, one from the Kerrville, Texas, factory to South Africa, and eight more from Texas to Brisbane, Australia. The Pacific trips usually departed from Santa Barbara, Calif., to Honolulu at 3,900 pounds. That's about 550 pounds over gross (with 120 gallons of additional fuel on a ferry permit). Climb was certainly affected by the overweight condition, but once the airplane caught its breath, I still saw a consistent 900 fpm climb to the typical initial 6,000- to 8,000-foot cruise height.
Marshall suggests he and his wife experience better-than-book climb numbers flying near gross. Though he rarely has occasion to fly bladder-stretching legs, the long-range tanks provide a hedge for those times when you'd rather not stop, or would prefer to hold out for a cheaper fuel price.
Benefitting from over 50 years of development, the Ovation 3 offers an air-conditioned cabin with the Synthetic Vision–equipped Garmin G1000.
Flying almost exactly at gross weight with Mooney's California regional sales director, Jennie Mitchell, in the right seat, owner Marshall in the aft left and Peggy Herrera in the fourth bucket, the Ovation 3 paid little attention to the load. I always climb Mooneys at a lower-deck-angle 120 to 130 knots rather than the recommended 105 knots, the better to see what I'm about to hit. At that speed, with all the knobs against the panel, the airplane logged 1,400 fpm initially, and settled on an easy 1,100 to 1,200 fpm for the short climb to 8,500 feet.
Most folks who fly little airplanes for a living (or even just for fun) acknowledge that speed is certainly one of the ultimate aphrodisiacs, and the Ovation 3 is therefore one of the sexiest machines in the sky. For our first cruise check, we went to the whip and left the engine at its full 2,700 rpm limit, just to see the top number.
Given its head, the Ovation 3 slips through the sky with the synchronicity of a Ginsu through hot butter. On our first max cruise check at 8,500 feet, I watched true airspeed settle on an eventual 192 knots, meanwhile pouring 19 gph through the engine.
At today's fuel prices, you'd need to be in a real hurry for that to make sense, so the better alternative is to climb higher into thinner air. With so much horsepower on tap, the Ovation 3 likes to fly tall where it can score reasonable economy while notching big speed. After our max performance cruise checks, we ascended to 10,500 feet, where about 70% power was all there was. Again using 2,700 rpm, we saw 189 knots for 17 gph. And, remember folks, that's flying in breathable air without a turbo. Service ceiling is a lofty 20,000 feet in case you need to buzz the summit of Mt. McKinley.
With air-conditioning keeping everyone's cool, Garmin's all-knowing, all-seeing G1000 with Synthetic Vision on duty, the talented GFC 700 autopilot to help drive and the big Continental chortling happily, the Ovation 3 makes an excellent ride in the middle sky. The Bose X headsets make the noise level moot, and all four occupants enjoy armrests and plenty of head and elbow room in a bright, comfortable cabin. It's not a G550, but it's also about $52 million less expensive.
If I owned an Ovation, I'd probably fly it most of the time at 10,000 feet or higher. Traffic is less of a hassle up high, weather tops are usually well below, speed and efficiency are better, and the safety margin improves with every 1,000 feet. At two miles AGL, you can glide roughly 20 miles in any direction.
When it comes time to return to earth under power, the Ovation 3's standard speed brakes allow it to decelerate like the Enterprise coming out of warp drive. On such a truly slick airplane, the Precise Flight speed brakes provide an excellent hedge against shock cooling, allowing a pilot to execute those frustrating go-down/slow-down directions from ATC without TBO-shortening power reductions.
Landings are far simpler than the airplane's reputation might suggest. Dirty stall checks in at 59 knots, so a reasonable approach speed is anything over 75 knots. Mooneys have long been accused of being floaters, but if you keep the approach speed to 80 knots or less, that's rarely a problem.
We don't normally talk much about flight manuals, but the Ovation's is one of the best I've seen—well executed, comprehensive and full of more information than you'll probably ever use. That's a welcome change from the days when flight manuals often seemed written by a dozen monkeys on IBM Selectrics. In researching this article, there were hardly any questions left unanswered by the Ovation 3's POH and supplement.
Like many other general aviation manufacturers, Mooney Airplane Company is currently in a state of suspended animation, waiting for a turnaround in the economy. After years of rosy predictions of increasing sales, the aircraft companies have discovered the future isn't what it used to be, but then, it probably never was. Mooney sold 65 airplanes in calendar year 2008, probably $30 million worth—not so bad. We can only hope 2009 will be better.
By any measure, Mooney has always been a survivor. The company that helped define performance and efficiency a half century ago continues to lead the industry in the parameter that excites pilots most—speed.
Tips For Using The Garmin G1000
1 Know both the Crosswind and HeadWind Components. Both ATIS and AWOS/ASOS provide information on airport winds, but the information often is either old (ATIS) or not applicable to the approach or to the runway itself. For a good reference on the changing wind speed and direction during the approach, set the G1000's PFD display to show both crosswind and headwind components. It also provides a good last-glance crosswind reference as you prepare to land.
Choose one of three wind display options by pressing the PFD's soft key, followed by the Wind soft key, and then selecting the desired wind display. OPTN 1 and 3 provide both headwind and crosswind components so you can choose your favorite display.
2 Dim the Screens at Night. As beautiful as the PFD and MFD screens are, even with their automatic dimming, they can be too bright at night. You can dim the MFD by turning off the topography display at night, but the PFD will remain bright. Better yet, the PFD has an option that allows you to individually adjust the brightness of either display. To change the backlighting, with the Flight Plan window closed, press the PFD's MENU button to open the PFD Setup Menu window, select MANUAL and choose the brightness that works best.
3 Manage your Speed in Turbulence. It can be a handful to fly in turbulence while managing everything else. The smart pilot uses the autopilot. The G1000's GFC 700 offers both rate of climb (VS) as well as constant-speed (FLC) climbs and descents. When in turbulence, consider using the FLC option for a constant-airspeed climb or, especially, descent. Just set it for the appropriate maneuvering speed using the NOSE UP and DN buttons and use the throttle to adjust the fpm rate. If the turbulence is really bad, turn the autopilot off and hand-fly, keeping the aircraft's pitch and roll level. Remember that the POH's maneuvering speed value is for the aircraft's maximum certified weight. Decrease airspeed for lower gross weights.

Mooney Ovation
Mooney aficionados tend to be clustered in the end of the gene pool that has “I want a fast airplane” in the DNA. For years, they flocked to the marque that promised and delivered speed while sipping fuel. Starting with the single-seat Mite, they were willing to shoehorn themselves into tiny cabins in return for not having to stay in them long when going someplace, while assuming a certain look of superiority over others due to miserly demands at the gas pump.
Over the years, Mooney obliged its faithful with progressive aerodynamic clean ups, making quick airplanes steadily faster. However, Mooney eventually shocked the aviation world by tacitly admitting that they’d gone as far as was economically viable with aerodynamics, and it was time to accept that there’s no replacement for displacement when it comes to sheer speed. It dropped a big-bore Continental into the latest iteration of the M20 airframe, creating the 190-knot M20R Ovation.
Mooney M20R Ovation History
After tragic teething pains—the original Mooney M20 saw several in-flight breakups, resulting in abandoning wooden wing components—the basic Mooney airframe has been essentially the same since the M20C of the early 1960s. It consists of a semi-monocoque rear fuselage, metal-skinned steel tube cabin, a long and slender tapered wing and a distinctive tail with unswept leading edges. As well, major systems have remained unchanged throughout: Trim is accomplished via a jackscrew moving the entire empennage; controls are pushrod-driven and the landing gear still uses a stone-simple trailing link design, with shock absorption handled by stacks of solid-rubber donuts.
The company, too, has been through several cycles of good and not-so-good times, and is currently only building and supplying parts, not complete airplanes. [This article appeared in 2013, since that time Mooney is again building airplanes, Ed.] It changed hands more than once, encountering management and quality-control problems along the way. By the mid-1970s, the line was looking a bit dated and the company was in trouble yet again. Fortunately for Mooney, the right person for the job was in place: LeRoy LoPresti had earned legend status for his ability to get the utmost from an airplane through aerodynamic cleanups.
Already famous at the time for his work at Grumman-American, he applied his talents to the M20 series, resulting in the Mooney 201, which stood for the airplane’s top speed in MPH. LoPresti made a number of changes, including a new cowling and more aerodynamic windshield. The interior was redone as well, with a new panel. Gone, too, were the old Mooney naming conventions (names like “Executive” and “Statesman”).
The 201 became the pattern for all Mooneys to follow. Its first sibling was the turbocharged Mooney 231 (M20K, a designation also applied to the 252/Encore models), with its 210-HP Continental TSIO-360. In the 1986 model year, the M20K morphed into the 252, which lasted until 1990, and was resurrected with 220 HP as the Encore for 1997–98.
The short-lived Porsche-engined PFM (M20L) was the first of what today are known as the “long-body” Mooneys, even though the M20J/K models had been stretched once already when compared to their M20C/D/E forebears. Lasting only two years and for 41 copies, the PFM begat the M20M, debuting as the TLS. It was the first true “big-bore” Mooney, sporting a turbocharged Lycoming TIO-540 of 270 HP. Known as the TLS/Bravo and later, simply Bravo, it went out of production in 2006 when the company shifted all its current powerplants to Continental’s 550 cubic-inch platform. In 1999, Mooney dropped the M20J/201 in favor of the M20S Eagle, also built on the longer fuselage first used for the M20L.
The Mooney Ovation series, also using the long fuselage, first appeared for the 1994 model year, rolling out the factory door at an average equipped price of $281,500. From the beginning, it was powered by Mooney’s version of Teledyne Continental Motors’ popular IO-550, the -G, featuring a tuned induction system. The IO-550-G lacks altitude-compensating fuel metering, so the pilot must lean the mixture manually.
Mooney derated the IO-550-G to 280 horsepower by limiting maximum RPM to 2500. This probably contributed to the engine’s official 2000-hour TBO when other IO-550s saw only 1700 hours.
Prior to production ending in the 2009-2010 time frame, the Mooney lineup consisted of the M20R Ovation 2 GX (280 HP), the Ovation 3 (310 HP IO-550-G with a 2000-hour TBO), plus the Acclaim and Acclaim S, both basically turbocharged versions of the 280-HP Ovation 2 GX with 2000-hour TBOs.
Yes, It’s a Mooney
Compared to earlier Mooneys, the most noticeable difference on the Ovation’s exterior is a sculpted cowl sloping down to a pair of too-small-looking cooling inlets. These inlets still manage to provide adequate airflow. No cowl flaps are fitted, so cooling air exits past the dual exhaust pipes.
The Ovation's interior belies Mooney’s reputation for cramped and uncomfortable cockpits. The company consigned the chintzy plastic interior panels from prior models to the waste heap. All interior panels on the Ovation are a laminated composite material with very nice natural wool or synthetic coverings. This really upgrades the cabin’s looks, in keeping with the contemporary, upper-end tenor of the aircraft. The composite panels also reportedly attenuate sound better than the thin plastic they replace.
Ovation in the outback; an Australian owner reported that his Ovation is ideal for that country's variety of airports and long distances between them.
The seating position is classic Mooney; you sit low with your legs straight out in front. It takes some getting used to. The difference the longer fuselage makes is most obvious in the rear seats, which are considerably improved over the torture devices they simulate in the short-fuselage Mooneys.
A complement of six exterior lighting switches is on the overhead, two of them split switches. Mooney, to its credit, makes sure everyone has the best possible chance of seeing you coming. Inside are the traditional map lights under the yokes, area lighting in the glare shield and individual adjustable lights for each seat in the overhead.
A standby vacuum system was standard equipment, as was dual 24-volt batteries (located in the tailcone for balance considerations). A rocker switch toggles from one battery to the other. Either can be used for all operations and they can be switched at any time, but both cannot be used at the same time. It isn’t a dual bus system, just dual batteries. A second alternator was offered as an option; it was required for the “known-ice” option. It later became standard equipment. If yours is an older one without, the dual batteries at least give you ample standby reserve in case of an alternator failure.
Those first Mooney Ovations routinely came equipped with a Bendix-King KLN-90A navigator and a KFC 150 autopilot. Beginning with the 2000 model year, the model’s designation changed to Ovation 2; look for a pair of Garmin GNS430s, a KFC 225, a WX-950 Stormscope and a two-blade prop. Factory options included built-in oxygen, propeller deicing, air conditioning and a TKS certified for known icing.
For the 2003 models, Mooney brought forth the Ovation 2 DX, featuring a standard Garmin 530/430 package, data linked weather capability, a KFC 225 and a KCS 55A HSI. For 2005, a GX version was offered, which included a Garmin G1000 glass panel. In 2006, the DX version was dropped and the G1000 became standard equipment. The Ovation 3, with its 310-HP IO-550, G1000 panel, Garmin GFC 700 autopilot and $469,000 average retail price came on the market in 2007.
Mooney Ovation Maintenance
Owners also report few maintenance issues with the Mooney Ovation engine and airframe—aside from common ailments with TCM cylinders and valves—but can’t say the same for all the avionics goodies the factory installed. One owner noted problems with both his Garmin 530 and 430; another reports his 530’s screen “burned up” in flight. None of that, of course, has anything to do with the airframe and Ovations appearing on the used market likely will have all those kinks worked out. We spoke with Fred Ahles, president of Premier Aircraft Sales in Ft. Lauderdale, Florida, a long-time Mooney sales and service center regarding factory support now that production of finished aircraft has ceased. Ahles indicated that there are about 10 employees at Mooney and they are providing parts support to the field. He reported that his shop has had no problem obtaining parts. He also reported that of the dozens of different types of airplanes he’s sold over the years, Mooney Ovation and Acclaim owners have been the happiest with their airplanes over time.
Ovation panel evolution from top-of-the-line round gauges (top) to Garmin G1000 (below).
But problems have arisen, some of which were targeted by Airworthiness Directives (ADs). In one instance, the factory apparently omitted a reinforcing gusset in the aileron control links. An AD, 98-24-11, addresses that shortcoming by requiring 100-hour inspections for 41 copies of the M20R. Installing improved parts terminates the AD. Another issue arose with cracked exhaust systems, as embodied in AD 95-12-16. A repetitive inspection was called for, at least until improved parts could be installed per a factory retrofit kit. Air-conditioned Ovations were required to be equipped with a placard specifying the system’s use during cruise operations alone, or owners were to disable the system entirely, under AD 99-11-07. That action responded to what the FAA called “dangerous levels of carbon monoxide during taxi, climb and descent operations.”
Improper installation of the pitch trim actuating system—the entire tail moves for pitch trim—led to a near loss of control accident when fasteners failed. Two ADs resulted, 2012-03-52 and 2012-05-09, requiring inspection for condition and proper placing of attachment hardware and Huck Bolts.
AD 2007-05-04 was issued to prevent the upper engine mounting hardware from losing torque, which could lead to engine mount failure. The AD responds to firewall insulation and upholstery being compressed between the fuselage tubular frame and the firewall at the upper left and upper right engine mount attach points.
Additional ADs issued against aftermarket cylinders from ECI, Hartzell propeller hubs and Bendix-King autopilots came up in our research.
Mooney Ovation Operating Costs
Owners report the Mooney Ovation’s operating costs are commensurate with this class of aircraft, with annual inspections falling into the $2,000-$5,000 range. Of course, surprises can always crop up and Mooneys are not immune. The aforementioned cylinders are one possibility; accessories like starter adapters are another.
Insurance for a Mooney Ovation is available and seems to be priced in line with other high-performance single-engine retractables. As always, some of the best deals can be had through type clubs. Training, also, is easy to obtain: The Mooney Safety Foundation, www.mapasafety.com, is heavily involved with type-specific flight and ground instruction. Flight training courses are held approximately five times per year at various locations throughout the United States, using instructors with many years and thousands of hours of Mooney experience, according to the association’s Web site.
Mooney Ovation User Groups/Mods
Perhaps more so than for any other marque, many Mooney owners can rightly be termed “maniacs.” It’s no surprise then that an excellent user group has sprung up, along with many knowledgeable maintenance and modification shops. The Mooney Aircraft Pilots Association, www.mooneypilots.com, is conveniently based near Mooney’s Kerrville factory, having recently moved from San Antonio, Texas.
Modifications are available from a wide variety of sources for all models. Some, however, may not be approved for the Ovation, since earlier models are more numerous and the Ovation may already incorporate many items—a low-drag windshield, for example. In February 2006, Mooney began offering an upgrade of the Ovation (and M20S Eagle) to increase maximum horsepower to 310. According to Mooney, the mod resulted from work done by Midwest Mooney of Flora, Illinois, www.midwestmooney.com, and PowerLite LLC, a subsidiary of AvPower LLC, which the FAA blessed by awarding an STC. The mod is still available from Midwest Mooney.
In addition to Midwest Mooney, other mod shops include The Mooney Mart, www.mooneymart.com, and Lake Aero Styling and Repair, www.lasar.com. Precise Flight, www.preciseflight.com, offers its wing-mounted speed brakes for the Ovation to help slow it down. Meanwhile, LoPresti Speed Merchants, www.speedmods.com, will sell you its popular Boom Beam landing and recognition light system.
Mooney Ovation Owner Comments
I’m a great fan of the Mooney Ovation, graduating from a 1975 M20E I owned from 1996 to 2000. I’ve been flying my 2005 GX2 since it was ferried to Australia in 2006. Before that, I owned an earlier M20R that was ferried here in 2000. Having operated the M20R for over 13 years for both business and personal use, I believe the airframe and the IO-550-G engine combination is one the best in its class.
Flying here in Australia generally means long distances between refueling points—sometimes hours at a time over featureless, sparsely inhabited outback (desert). Speed, reliability and range are essential. Once away from cities, refueling stops can be problematic and prices can exceed $9.00 per gallon. Most of the time I fly at 8000 to 9000 feet, although occasionally I will operate in the flight levels to take advantage of tail winds and fuel economy or to avoid weather. The highest point in Australia is 7310 feet, so there are no imperatives to operate much above 10,000 feet.
Cleaning up and moving out; owners report taking the normally aspirated into the flight levels and cruise speeds of over 190 knots.
I particularly like the normally aspirated IO-550-G because it is relatively uncomplicated and requires less maintenance than its turbocharged cousins. It will take you to FL200 when you need to be there. With almost 800 hours on my GX2, the only unscheduled maintenance has been to reseat an exhaust valve and a minor weld repair on the exhaust. The engine is comfortable to operate LOP, although my first Ovation wouldn’t operate lean of peak. I also find my GX2 a little faster, possibly because of the switch to a Hartzell prop from a McCauley.
The Garmin G1000 glass cockpit was initially a challenge after round gauges, but now I would have difficulty with anything else. The S-Tec autopilot is okay, but nowhere nearly as smooth and accurate as the King in my earlier M20R.
From a service point of view, I’ve had little need to call Mooney, but when I have, they’ve been nothing but helpful and responsive. If I could convince them to start building airplanes again, I’d be first in the queue.
Gary McKernan, Via email
I have based my Ovation 2GX here in Denmark since I purchased it new in 2007. It is equipped with the G1000 panel and GFC 700 autopilot.
I’ve been extremely happy with the airplane because of its speed, range, high-altitude capability, known icing system and built-in oxygen—which make it the perfect airplane for long, high-altitude trips in Europe. It replaces an F33A Bonanza. I was happy with the Bonanza, but the Mooney Ovation is better for my needs as I can fly above most clouds in all seasons, which was not possible in the Bonanza.
Klaus Ostenfeld, Via email
We purchased an Ovation 2 for our company in August of 2011. We’re the second owner. We fly the airplane between 250 and 350 hours per year, all over the U.S., in all types of weather, from our home base in eastern Texas. It has been an excellent long-haul airplane for us.
Bottom line, with the Ovation you can expect to cruise at a minimum of 170 knots between 7000 and 10,000 feet at 65 to 70 percent power. It is consistently 15-20 knots faster than the Cessna 210 we owned previously and 25 to 30 knots faster than the Turbo Lance we owned before the 210. Offsetting the speed advantage is the need to watch weight in the Ovation—there’s lots of baggage space, but not the load-carrying ability. It’s a two- to three-place airplane when carrying any kind of fuel.
With full tanks (90 gallons), the Ovation is a legitimate six-hour endurance machine—we normally see under 15 GPH fuel burns. A neat feature we frequently use are the wing fuel gauges that allow partial fueling to 60 gallons for four-hour endurance and a heavier cabin load.
You have to pay attention to line personnel fueling the airplane as they tend to overfill the tanks. The book calls for stopping at the base of a one-inch neck rather than up to the cap. If fueled above the base of the neck the result is a distinct fuel odor in the cabin until fuel is burned down to the proper level.
The Ovation likes to climb—it goes up nicely in a cruise climb—something our 210 and Turbo Lance didn’t do. You can easily see 700 FPM at 140 knots indicated to over 10,000 feet. You do have to watch things when it’s time to descend. The Mooney has speed brakes for a reason. With the KFC 225 and proper planning though, you can dial in a 200- or 300-FPM descent and pick up extra speed over the last 80 miles or so.
We felt the Mooney gave us more value for the money than a Piper, Cirrus or Bonanza. The only downside is the smaller cabin—the fewer inches in width and headroom are certainly noticeable. There are no good places for the charts in easy reach of the pilot.
You need to be limber to get in and out as compared to the 210 or even the Lance—but once in, it is generally comfortable. Anyone considering a Mooney certainly needs to fly one to see if the cabin is suitable. Both of our pilots are small, so it’s not a problem for us.
Maintenance has been very good—plus Mooney did a good job in design in many areas such as the landing gear which is superior to Cessna or Piper. However, it’s not perfect—replacing one circuit breaker requires removal of rivets in the airframe skin. Replacing a wire to the dimmer switch, where there is hardly any room to maneuver, takes over an hour. Those sorts of things should have been caught prior to production.
Everything you have heard about a Mooney in flight is true. It is solid in roll, stable when trimmed and holding proper speed on final is important. It is difficult to scrub off additional speed and it will float.
The airplane gets a bum rap because it has a more abrupt stall break than a Cessna, so pilots tend to fly final too fast because they’re worried about stalling and then use up a lot of pavement. It can use short fields, but it takes practice and finesse to land well. If you need to use short or grass fields regularly, a 210 is a better choice, however.
The Mooney has proven to be the best airplane for us as compared to our earlier 210 and Turbo Lance—and boy, does it get places in a hurry. With the speed, be ready for a high workload and the need for fast thinking on arrival. Controllers don’t seem to recognize this, and it often takes some negotiating to get a descent in time to set up outside the marker.
Ted Gribble, Via email
Having purchased one of the first two glass-panel Ovations and having it upgraded to include the GFC Garmin 700 auto interface, as well as the Ovation 3 modification, I feel I am in a good position to comment.
Insuring a high-performance retractable with no experience can be difficult. Using Falcon Insurance and working closely with MAPA’s Safety Foundation, I had no problem obtaining full insurance. I immediately took intensive training. Insurance was always reasonable, but I might have had problems had I purchased a competitive aircraft.
My first annual was $1500, the second was $2500 and the last one was $4000, but it involved replacing a cylinder (burned valve) covered under warranty as well as some discretionary improvements. A reasonable estimate would be between $2000 and $2500.
Gary Gongola, Menomonee Falls, Wisconsin
In my M20R, I figure on 180 knots true on 11.7 GPH. I fly lean of peak almost all the time. The engine still has compressions of 72–76 over 80 PSI, and it is down about two quarts of oil by 30 to 35 hours.
The Ovation looks great on the ground and in the air but, better than that, the performance is outstanding. The ride is solid and comfortable. Controls are on the heavy side, especially in roll, but pitch is somewhat sensitive.
The biggest drawback, other than useful load, is headroom. On the older Ovations, the panel is high and difficult for a shorter person to see over—on the newer models, it was lowered about 1.7 inches, which made a big difference. It’s awkward to get in and out, but once in, it’s comfortable.
Compared with the 201s, the Ovation is harder to land well consistently. I strongly recommend the MAPA proficiency course for anyone buying one for the first time.
The Ovation is a fast, comfortable, good-looking hot rod. It is extremely efficient, a nice feature in this time of sky-high fuel prices. I sometimes have been asked if I wouldn’t really like to have a twin. No, thank you. I already have the performance at much lower cost in fuel, maintenance and insurance. If I needed a twin, I would be out of aviation in a heartbeat.

Mooney Acclaim Type S
There are many things to love about the turbocharged Mooney Acclaim, more than 230 of those things, in fact, and the Type S follow-on has a few more to add to the mix, bringing the total, according to Mooney's accounting, to 242 ... knots, that is.
The Continental TSIO-550-equipped Acclaim has been around for a couple of years now, and it's been a great seller for Mooney. It was the successor to the Bravo, which was powered by a turbocharged 270 hp Lycoming TIO-540. I've had a chance to fly the Bravo, and it's a nice airplane, a near 220-knot cruiser at 25,000 feet that can do around 200 knots in the mid-teens, where most pilots wind up operating these airplanes.
The Acclaim, let me say right off the bat, is a lot faster than that, and the Acclaim Type S, which features some aerodynamic improvements to the original, is faster still.
Moreover, the Acclaim has been the beneficiary of a number of notable quality of life improvements, thanks to updates on the G1000 avionics suite that is standard on all Mooneys today. (The last models of the Bravo had the first iteration of G1000.) The latest Acclaim, I just learned today, is now available with Garmin's terrific Synthetic Vision Technology (SVT). Unfortunately, you'll have to read about that in a future story.
On the Acclaim Type S, Mooney asks the Continental engine to deliver just 280 hp, this from an engine type that cranks out 310 horses in at least one other current airplane. Given the Mooney's sleek lines, 280 horses is plenty. The airplane is very fast, as fast as some turboprop twins, in fact.
It's interesting to note that while the Acclaim competes with new designs in the form of the Cirrus SR22 G3 Turbo and the Cessna 400, the Mooney does almost everything in a very different way from those models. With the Acclaim you get a relatively compact, all-metal, retractable-gear airplane that appeals to people who are looking for truly personal transportation. Many writers and owners before me have compared the airplane to a sports car, and the comparison is certainly apt. You sit low in an Acclaim, as you do in a Lotus. Rather than "sitting in" the airplane, it's more like you're wearing it. Some passengers will love it. Others won't. Like just about everything else with the Mooney, it's a very subjective thing.
Faster
When Mooney introduced its Type S Acclaim last fall, it said that it indisputably had the fastest piston single in the world, with a top cruise speed of up to 242 knots, an improvement of nearly 10 knots over the original Acclaim. It had achieved this kind of speed increase by working into the design a number of aerodynamic enhancements, though it declined, like a Nascar team working under cover of night, to go into detail about it. For the record, the competition is the Cessna 400, which is just about as fast, though I haven't heard Cessna arguing that its airplane is faster than the Type S. Some 400s are probably a knot or two faster than some Acclaims.
These days Mooney is talking more freely about the aerodynamic mods, and though they aren't the stuff of great genius, they have the unusual effect, unlike many such mods, of actually doing what the company claims they will.
What are they? The most noteworthy (and if I had to put money on it, the most effective) is the addition of a new three-bladed Hartzell prop. There's a new, smaller but still very effective air inlet, flap gap seals, and cleaned-up gear doors and flap hinges. If you'd asked me before the fact if these changes would have made a 7-knot difference in speed, I'd have bet against it. But I'd have been wrong.
Nope, the result of the cleanup is an airplane that is noticeably faster than its predecessor by a good margin. I never saw the 242 knots that Mooney claims, but I'm sure some examples can do it. During the week I was flying the airplane, it was still pretty hot out, and even at 25,000 feet, it was considerably warmer than standard. On the day that I donned the mask and climbed the Acclaim up that high, I was able to wring 236 knots out of it at the best power setting, whereas the book said that I should have been able to get 240 knots true at the warmer than standard temperature.
It seems absurd, I should add, to apologize for 236 knots, so let me point out that 236 knots made me very happy indeed. And at 50 degrees lean of peak, I was still seeing 230 knots at 21 gph.
Now, if I were to operate an Acclaim on a regular basis I doubt I'd fly it up at 25,000 feet very often, except perhaps to take advantage of great tailwinds. I'm not alone in this and I have the same reasons as other pilots of turbocharged airplanes: I hate wearing a mask and, despite the airplane's excellent climb performance (800-plus fpm all the way up), it does take a while to climb to FL 250, especially when ATC steps you up along the way, as they are sure to do in many parts of the country. But that said, once you're up there, seeing 230-anything, and on a good day 240-plus, on the true-airspeed readout on the G1000 is a sweet thing to behold. And it's no mirage. I would, in fact, flight plan for something in the neighborhood of 232 knots were I going that high. This is one smoking airplane. With a respectable tailwind, you're looking at 270 knots or better.
But the biggest reason I'd stay down in the mid-teens is because the Acclaim does exceptionally well there. Heading from Midland, Texas, back home to Austin on one flight, I was at 17,500 (yes, VFR and almost completely alone in my airspace there). At that altitude on that day I was seeing 222 knots true on the display with, again, right around 21 gph fuel flow at 50 degrees lean of peak. And you can do much better in terms of fuel consumption, if you're willing to slow down a bit. At 16,500 on the way out to West Texas, I pulled the power back to 26 inches and 2400 rpm and got right around 205 knots at 18 gph with a total range of better than 1,000 nm and a fuel efficiency of better than 12 nm per gallon. Try that in a Suburban. And if I'd settled for even less speed and wanted to stretch the leg out, I could have easily flown from Central Texas to Southern California nonstop with the standard 100-gallon tanks, no less. The airplane is available with 130 gallons of fuel, though it's an option that not many customers opt for.
A feature that comes on every Acclaim are speed brakes, and they make flying the airplane a lot easier in a few different ways. Coupled with the three big speed brakes on the belly of the airplane (often referred to as landing gear), Acclaim pilots have some great tools to help in getting the airplane heading down when it's time to descend. And they allow you to do it without building up too big a head of steam, while still letting you keep the power reductions incremental and gradual. If you fly the airplane at the flight levels, you'll need the help. Few controllers seem to understand the difference between a pressurized airplane and a non-pressurized one. The difference, of course, is about 1,000 fpm in the rate of descent. The key in the Mooney is to think ahead, to beg for lower early, to use the speed brakes right off the bat and to reduce power judiciously as you descend to keep the speed from building too high. Even when I was given unrealistic sounding crossing altitudes on a couple of occasions, I was able to make them without having to descend at much more than 1,000 fpm. But you've got to plan ahead.
Mooney at Heart
The speed brakes also help in one other respect, in landing. You've probably heard that Mooneys are hard airplanes to land, and it's true. Unless, that is, you do things right, in which case they're easy to land. The key, as you know if you've flown them, is to control your airspeed. On landings where I did this, I was overjoyed with the result. On landings where I was a little fast, the results weren't pretty. By using the speed brakes, however, the airplane tends to float a lot less. By the end of the week I was using the blades on every landing. With them, speed control is still important, but slightly less so.
In all other ways, the Acclaim is a Mooney, and that means that people who love them adore them and people who don't wonder about the ones who do.
As I said, the airplane is compact, and while the shoulder room is generous, the overall cabin size is cozy, as is the case for the back seat too. The interior, on the other hand, is elegant, verging on luxurious, with nice leather with contrasting piping. It's a nice place to while away the hours as the terrain passes below you at an impressive rate.
As with all the Mooney models, the Acclaim comes with some impressive options, including a TKS anti-icing package that is approved for flight into known icing. You can also get air conditioning, which is something I pined for during my week with the airplane in the late Texas summer (which feels a lot like the worst summer day anywhere else). The addition of those two options, I might add, while contributing mightily to safety and comfort, combine to cut the useful load tremendously. So many buyers choose to do without them, putting up with the heat on warm days on departure and arrival -- it's nice and cool up high, remember -- while practicing prudence when it comes to the icing issue. Those who live in the ice belt, not surprisingly, are Mooney's best customers for the TKS, which for much of the year can be flown with little or no fluid in the tanks.
I think that's a good way to think about the Acclaim, as an unparalleled one/two-occupant long-range rocket, but maybe more importantly as an excellent regional airplane. This is very much, in fact, how I think of turboprops and how charter companies make use of them. One of the Mooney employees who regularly flies a company Ovation 3 airplane around the Southwest on the way to and from Big 12 football games -- tough gig, I know -- says that the airlines simply can't touch the Mooney for block to block times, not to mention overall convenience. And I believe it.
On a trip out to West Texas, the Mooney delivered me in comfort and high style in just a little longer than the airlines would have, but in a much shorter time when you factor in the lines and built-in wait times of airline travel. And the schedule was all mine.
It's an appealing way of travel on many levels, and I found myself quickly getting used to the speed, continental styling and turbine level systems of the airplane. Also, after a good flight in the airplane, I felt a real sense of accomplishment, what with managing oxygen, speed brakes, landing gear, and running the beautiful G1000 flight deck. It's a lot more than mere transportation, that's for sure, and Mooney customers genuinely appreciate this aspect of ownership, in addition, it goes without saying, to the speed.
On the fence next to the taxiway leading out of the Mooney production ramp, there's a sign that reads, "Fasten your seat belt." Some might take that as a simple safety reminder to the pilots heading out for the runway at Kerrville Municipal. But the real meaning, I'd venture to say, is this: "You're in a Mooney. Prepare to go fast."
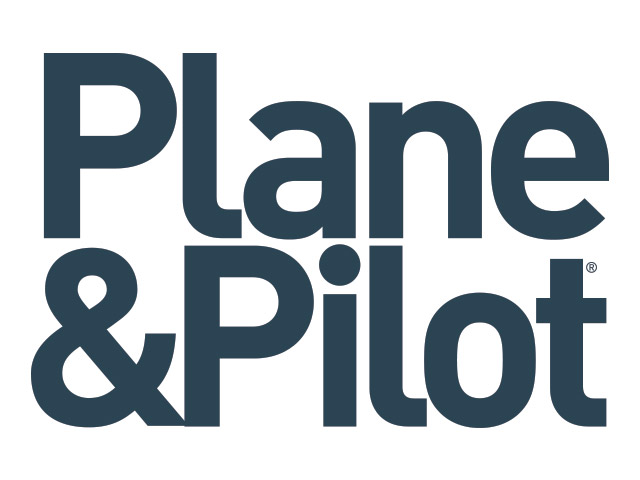
We Fly: Mooney Acclaim Ultra
Courtesy of Mooney Aviation
It was a bright early spring day in the Hill Country of central Texas—well, it wasn’t really spring, but in Texas, a nice winter day feels decidedly spring-like. Which is nice when you’re exploring unheated hangars or wide-open expanses of tarmac. In addition to being pleasantly warm, it was bright on the Mooney ramp, too, as I rose up on my tippy toes and poked my head into the open rear baggage door of the new Mooney Acclaim Ultra, the latest airplane from a formerly beleaguered company back on its feet now and looking like it’s going places.
With a long history of producing popular four-seat single-engine planes, Mooney has also had a history of ups and downs. The latest down, which happened around the same time as the global economic downturn of 2007, was a body blow. The factory stayed open producing parts, but the airplanes that had been moving down the production line stopped in place. Many thought it might be the end of the line for a once-industry-leading plane and a great American aviation success story.
Happily, such was not the case. Today, as you likely know, Mooney has new life, as Mooney Aviation. The company was acquired in 2013 by Soaring America, a firm headed by Jerry Chen and backed by Chinese investors. With Mooney, Chen is looking to capitalize on the fast and popular planes (with a famously fanatical fan base) while improving them incrementally until they’re on par with the segment leaders (read: Cirrus and its SR22). The company is also developing a clean-sheet product, the M10, at its Chino, California, facility. The M10, no relation to the old Mooney M10 Cadet, is a two-seat design with a fixed-gear version for training and a retractable-gear version for personal transportation.
Courtesy of Mooney Aviation
Perhaps one of the reasons why owners love their Mooneys so is that the planes are a bit eccentric in a few ways. The location of the baggage compartment access door, into which I was poking my head, is such a case. Unlike on Pipers or Cessnas, which situate the access doors down low for easy loading, the baggage door on the Mooney is located up high, just below chest height for me.
Using my phone as a flashlight (who doesn’t do that, these days?), I peered inside the underlying structure of the machine. Cool. It’s something that you seldom get a chance to do—see the bones of the beast from the inside—but this particular example hadn’t yet been made all pretty with interior panels and soundproofing and upholstery. The unobstructed view revealed the single secret of the new plane, the one great idea that allowed Mooney to create a new experience out of an existing product. That existing product, of course, is the M20, which in the Acclaim version is the fastest production piston single airplane on the planet, hitting 242 knots at 25,000 feet. In the new Ultra version, if it’s fair to even call it a “version,” the Acclaim will still do that, or at least that’s what Mooney is working hard to make happen; it’s trying to win back a few knots it expects to lose from the additional drag added by a second step and wingwalk covering. But the Ultra will also bring along an entirely new user experience as part of the bargain. A much improved user experience, I should add.
Courtesy of Mooney Aviation
Mooney COO Tom Bowen has been in the light aircraft manufacturing world for 25 years in various leadership roles at Mooney in the 1990s, Columbia and briefly Cessna in the 2000s, and then again at Mooney in 2010. A tall native-born Texan with an easy laugh who looks like he’d prefer a good pickup truck to a sleek sedan (and, in fact, does), Bowen is a born production guy whose eyes light up when discussing the importance of tool dies in the metal-forming process.
Bowen has overseen the transformation of the Mooney factory in Kerrville, a small town an hour up a good road from San Antonio or two hours on winding two-lane roads from Austin. A time capsule with futuristic slices scattered throughout, the factory is a patchwork of design, the old, mostly still functional tools, a steampunk throwback to the middle of last century. Industrial-green behemoths dominate the floor space, their functions still a necessary part of creating the majority of the Mooney airframe, whether bending, stamping, shaping or forming metal. Most of the tools are still functional. In some cases, they’re irreplaceable cogs in a manufacturing process that Mooney has been conducting here in Kerrville for 60 years, with a few stops and starts along the way. The old tools—some of them, Bowen proudly points out—require long experience with making settings and feeding material to get the part to come out right. The current master of one cutting machine, he said, has been building Mooneys for more than 30 years.
Today, the busy antique machine tools exist alongside an increasing number of new efficient and environmentally friendly tools that are clear evidence of the company’s investment in the brand and in Mooney’s future. One, a long tank with a robotic apparatus that automatically feeds the metal parts into a fluid bath, does a great job, Bowen said, but it’s also clean. It is, in fact, so efficient at cleaning the fluid left over after the anodizing process that the fluid, instead of being dumped into toxic effluent ponds, can be returned to the city system as simple wastewater. It’s all a fascinating mix of old and new machinery in an airplane that’s based on a 55-year-old design, but that still has industry-leading performance.
Photos courtesy of Mooney Aviation
The Secret
I’ll tell you the secret behind the new Mooney M20: plastics. In this case, it’s fiberglass, e-glass, to be precise, that’s used to create a new external skin, or shell, for the M20 that takes the place of the sheet-metal covering of the original. Unlike on most other comparable aluminum planes, Mooneys make use of a steel-tubing-frame occupant enclosure. That steel cage is remarkably strong, for the protection of the pilot and passengers in case of an unplanned off-airport arrival. It’s a feature that Mooney owners point to with pride.
Mooney has focused very smartly not on performance, but on pilot and passenger comfort and experience.
The new skin, attached to the steel tube cage with bonded-on fasteners—the bonds for the attach points are stronger than the surrounding material—allowed Mooney to do something it had never done before: add a second door. You might be asking why Mooney couldn’t have added a second door into the existing sheet-metal fuselage skin, and you’re right in asking. It could have. But Bowen says that doing it with a composite skin made the process a lot easier and it saved a lot of weight, too. It did not, he makes sure I understand, make the airplane lighter. Its lighter weight made up for the additional beefing up that needs to be done to add that driver’s side door.
Mooney took the opportunity to completely redesign the interior, grouping like functions on the panel and cleaning up the design by eliminating switches and breakers, when able. The restyled flap lever was relocated, and new-style toggle switches were adopted. The overall effect is clean and well organized, for improved ease of operation. The creature comforts are, likewise, much improved, with two-tone stitched leather throughout, even on the yokes. The seats have new bolsters, there’s a new armrest, the headset jacks in back have been relocated between the seats, and there are USB ports in front and in back now, too. The larger windows, as you can probably see in these photos, add a lot of light and improve visibility for both front- and backseat riders, giving a sense of openness brand new to Mooneys. It also improves outside visibility for the pilot, which has obvious safety benefits, as well. Photos courtesy of Mooney Aviation
Big Deal
With the Acclaim Ultra and Ovation Ultra (the non-turbocharged higher-horsepower version, which will follow on shortly), Mooney has focused very smartly not on performance, but on pilot and passenger comfort and experience.
It felt a little odd that such an important part of my test “flight” was repeatedly getting into and back out of the airplane, on the ground, of course, into every seat and from both sides of the airplane. In the hangar, Bowen and Mooney marketing leader Jared Absher pointed out the techniques I should use to help my passengers get into the airplane, and then for me to get in, too. You do need a pilot to go flying, after all. The doors themselves feel completely different, very firm and positive. The latches and hinges are new. Gone are the piano hinges for the door and new is a jet-style positive locking mechanism. Pull the door firmly closed, engage the lock, and it’s done. I can’t imagine how one could get it wrong and partially close that door, something that happens with other door designs on light airplanes all too frequently.
For passengers, it’s an even bigger quality-of-life improvement. The backseat of the old M20, which many folks feel is too low and a little claustrophobic, is transformed. The seats, with all new padding and modern contrasting stitched leather, sit taller and seem more individual than before. Previously—and Bowen nimbly demonstrated this for me—backseat riders had to slide the front seat forward, step onto the narrow strip of backseat floor sideways and then pivot around down into the seat. Now they can simply slide the seat forward and step in normally.
What makes this possible is the new door design on both sides of the airplane. So, not only is there an additional door, but both doors are of a completely new design, substantially wider and with bigger windows and a skosh more elbow room along the sidewall. That means when you open the door and slide the seat forward, while there may not be any additional floor space—the fuselage dimensions are largely unchanged—there’s more room to get in because the door openings go back much farther. The result is that getting into and back out of the rear seats is much easier than ever. I know. I tested it.
I mentioned the windows, too, and they’re just as big a deal. The feeling of a Mooney, and I’m sure the new company did some good focus testing on this, can be a bit too sports car-like. That is, you sit low and it feels a little like you’re peering up at the world. In the new plane, the experience is completely transformed. The combination of lower, wider windows and a lower glareshield makes the experience feel more open, and it made me feel more on top of things, like I was more in command and less sunken into the environment. The view out the window is just great, too. Expect a lot of iPhone shots of the landscape below with that pretty Mooney wing a permanent backdrop.
Bowen tells me that for longtime Mooney fliers, it’s a strange feeling, setting your right foot on the step on the left side of the airplane, stepping up onto the wing, opening a door there and then climbing in—directly into the pilot’s seat. Conversely, for pilots of Cessna, Cirrus and select other models that have two doors, the idea that an airplane would only have a door on one side must seem a bit ludicrous. But it’s the way it was done back in the day, especially on low-wing airplanes. Here’s why. With a low-wing plane, the occupants need to climb up on the wing to get in, so the wing in the area where they walk (the aptly named wingwalk area) needs to be strongly reinforced, with additional structural members so no damage ensues when your big buddy Jake lumbers up to climb on in. So when you see a placard that says, NO STEP, that’s the reason. The wing isn’t additionally reinforced there, and you actually can do structural damage to the airplane if you’re not careful.
Even on the ground, the sense of being on top of the world is there.
So, when Mooney decided to add that extra door, it was also deciding to add the extra wing structure (weight), another doorframe (more weight) and another step (again, a few more pounds). The lighter composite skin allowed the company to do all of that and still come in at around the same weight. It also eliminated a lot of complicated and time-consuming manufacturing processes in creating the doorframe, as Bowen points out. The frame is a one-piece composite affair that has all the curves and grooves designed into the single composite part and not built up from dozens of individual pieces of metal.
Inside Design
Not all of my testing could be done on the ramp in Kerrville, so Tom and I hopped onboard an Ultra (they’re currently rolling down the assembly line) and took to the blue, and surprisingly tranquil, skies above the live oaks and rolling scrub brush hills of Kerr County, Texas.
I have a good bit of time in Mooneys, including the Acclaim, Acclaim S and Ovation, and some of that time was built on long trips with family and friends, so I had a baseline for comparing the new and slightly less new models. From climbing in and first taxi, it was clear the experience in the Ultra would be, well, ultra-nice. Even on the ground, the sense of being on top of the world is there. You have better visibility thanks to the wider and lower windows, and even though the glareshield is only an inch lower, Bowen tells me, it seems to give better visibility over the nose.
Courtesy of Mooney Aviation
As I intimated, and as you can see in the accompanying photographs, the Acclaim Ultra has the best Mooney interior yet. It also has the best avionics package, with the Garmin G1000 integrated flat-panel system with redundant dual 10.4-inch diagonal displays with Mid-Continent Avionics standby gauges nestled snugly between them; the autopilot controls are oriented vertically along the left-hand side of each display. There’s WAAS as standard, RNAV approach capability, available ADS-B, which every buyer should get, standard synthetic vision and extensive vertical navigation features. Many of these capabilities weren’t available to previous Mooney buyers.
The secret to the Mooney Acclaim Ultra’s improved comfort and view is a one-piece composite shell, which allows an additional pilot-side door, larger windows and a wider door while keeping the weight the same. The shell merges with the existing steel cage design, using bonded fasteners stronger than the material they’re fastening. The old piano hinges on the door(s) give way to heavy-duty, jet-style hardware for a more precise fit. Photos courtesy of Mooney Aviation
Other functions on the panel have been rearranged, too. There’s a new, higher-up gear lever with the same sight gauge on the floor between the seats to check gear status. The flap lever is new, with clearly marked settings. New-style toggle switches, which look like turtle shells, incorporate an on/off light, and the avionics keypad has been repositioned and its layout improved. Mooney designers put function controls into sub-group categories and grouped them together for a more intuitive layout; the switches for either TKS or air conditioning (it’s an either/or proposition) are all situated around a rotary dial on the left-hand-side subpanel. It’s an easy cockpit layout to get used to.
Flying The Acclaim Ultra
As you’ve doubtless figured out by now, the real changes to the Acclaim Ultra aren’t related to its flying qualities, which Bowen told me he expected to remain essentially unchanged. Whether any of the numbers on the spec sheet would change is an open question, but if they do, Bowen said, it won’t be by more than a couple of knots or feet per minute up or down. That’s an important detail, as the Acclaim Ultra isn’t a new type certificate. Its upgrades, even the all-new composite shell, are being addressed by the FAA as “minor changes,” an official term the FAA uses to assess the potential effect on the aircraft’s airworthiness. In this case, it means the FAA expects there to be little or no effect on the M20’s handling and performance due to the new shell, doors and a few other added features. There were, in fact, just a handful of parameters the FAA required Mooney to look at in flight test, Bowen told me. They included a dive test, presumably to see if the shell holds tight under increased air loads. It’s a sure bet that it will, which the FAA knows, but no one would blame the agency for covering its bases.
Takeoff, as I expected, was completely Mooney-like; you need to apply a good bit of back pressure to rotate, and once you do, you can commence the trimming. The airplane is a strong climber. We were light, with just Tom and myself and half tanks, and it was right around a standard day, temperature-wise. We headed up at better than 1500 fpm at best rate, an airspeed I seldom use in real life, as it robs you of a lot of the view out the front, where the airplanes coming right at you will be as they’re descending into the airport you’re currently departing.
Once we got up to 8,500 feet, I had to pull back on the power to avoid going too far into the yellow—oops, this is a fast airplane. We did a series of maneuvers that all resulted in me becoming absolutely convinced that if there are any differences in handling from previous Mooneys, I’m not good enough to be able to make out the distinctions, if they did exist at all. It made me feel better that Bowen isn’t either, though. One thing I was easily able to perceive was the difference in the view from the front seats. I assume it’s a big upgrade from in back, too. The larger and wider windows make spotting traffic easier, though we were apparently all alone up there on a fine spring-ish afternoon.
The new windows also make it easier to appreciate the view and the overall experience of flying, and flying a Mooney. That upgrade alone—and it’s just one of many—makes the change from one door to two a big deal, even if the FAA says it’s just a minor one.
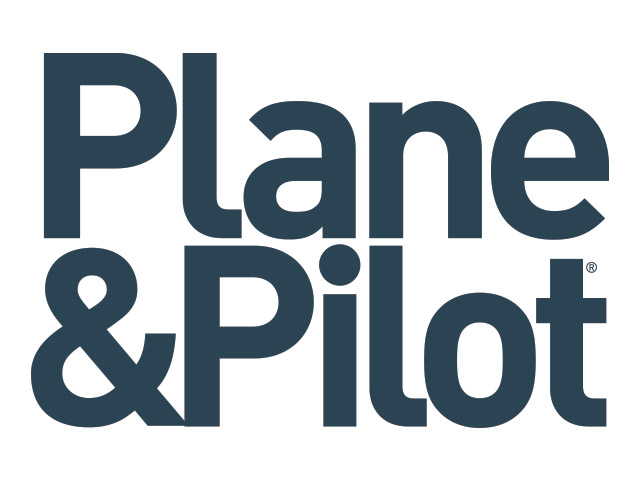
Mooney Acclaim Type S: Still The Fastest
A few inches away, the world isn’t a friendly place. I’m cruising in a new Mooney M20TN Acclaim Type S at 25,000 feet over central Florida, and despite clear skies and warm temperatures on the ground, the air is cold and thin nearly five miles above the ocean. Without the Mooney’s protective bubble of aluminum and Plexiglas, plus oxygen masks to provide supplemental O2, I’d be in trouble.
The outside air temperature is about minus-30 degrees C, and the air is so thin at this height, we mere mortals would be tempting fate without our masks. If we were scaling K2 or Everest, we’d be only 1,000 feet below what climbers call the death zone. Technically, atmospheric pressure at FL250 is only about a third of that at sea level, and humans don’t do well at such heights without supplemental O2.
The new, production Acclaim Type S that has us surrounded doesn’t seem to mind the conditions. The airplane’s big Continental TSIO-550G engine features twin turbos and dual intercoolers; it thrums happily in the cold, high sky.
Loaded up with full standard fuel and two big pilots up front, the airplane is nearly at gross weight as it gradually sneaks up on its max cruise number. I watch the true airspeed readout on the Garmin G1000, and the numbers slowly count up to 239 knots. That’s 275 mph in nonpilot speak, about four times legal freeway speeds and faster even than a Bugatti Veyron. Normally, 239 knots is the beginning of turbine country, recorded by C90 King Airs and the like, but the fastest of the Mooneys takes truly high cruise in stride.
Speed has always been Mooney’s strongest suit. The type has consistently manifested among the highest knot count per hp in general aviation. In today’s world of $6-per-gallon avgas, the airplane’s ability to wring every possible knot out of each gallon serves it well. The gold standard of performance was previously one mph per hp, and a Mooney is one of very few production airplanes to realize that goal (achieved 30 years ago on the 201, flying 200 mph on 200 hp). Better still, the turbocharged Mooney 231 came close to realizing one knot per horsepower in 1979, delivering more than 200 knots on only 210 hp.
Alas, the days of the 200 hp Mooneys are long gone, though some of Mooney’s old guard still regard the 201 as the best Mooney ever built. Today’s Mooneys fly behind engines with far more power, but because drag increases at the square of speed, what was possible with 200 hp is highly unlikely with 280 hp. The current state of the aerodynamic art isn’t up to 280 mph on 280 hp.
To accelerate the Acclaim Type S, Mooney took the advice of LoPresti Speed Merchants and faired in the nosegear door, creating a smoother passage for air. The aircraft features a three-blade, constant-speed Hartzell propeller (bottom) and tricycle-retractable landing gear (above, middle). It also has a 43.5-inch-wide front cabin, spacious enough for two large pilots, and a sophisticated Garmin G1000 dual flat-screen avionics suite.
Still, by any standard, the new Mooney consistently achieves more with less. The Acclaim Type S is the second iteration of the Acclaim, and it’s arguably the fastest production, piston single in its class, period. Even if you’re not inclined to file for the flight levels on every flight, you can see impressive numbers at lower levels. At 15,500 feet, plan on 220 knots, and down at 10,000 feet, the Acclaim Type S should still trip along at 205 knots or more.
Mooneys weren’t automatically born to such speed. The Texas company’s original Acclaim was a notably quick airplane, but Columbia Aircraft used to claim that its Columbia 400 was a knot or two quicker. Accordingly, Mooney launched into a speedup campaign to raise the ante and reassert its claim as fastest airplane. Cessna (which purchased the Columbia 350/400 assets and type certificates when Columbia went bankrupt last year) no longer fuels the competition. Cessna now claims the 400 as simply the fastest, fixed-gear, production piston single, with a top speed of 235 knots. Mooney suggests a top speed of 242 knots, and no one disputes the claim.
Top speeds are pretty worthless numbers, as hardly anyone is dumb enough to flog an engine at continuous max power unless they’re turning the pylons, even if the engine is rated for it (as is the Mooney’s). The Acclaim Type S spec is 237 knots at 75%, and I’ll take 239 as a close approximation of that any day.
Such brevity isn’t possible without plenty of horses out front. The Acclaim Type S features a Continental TSIO-550-G, considerably derated on the fastest Mooney, but pushed to as much as 350 hp in other applications. Mooney claims the engine is turbonormalized, which might suggest a manifold pressure red-line of 30 inches. Instead, twin Kelly Aerospace blowers provide the big Continental with a limit of 33.5 inches all the way to the critical altitude of 25,000 feet.
However you choose to define “turbonormalized,” power is copious and may be limited only by the size of the airplane’s vertical stabilizer. A former president of Mooney suggested that it was unlikely the airplane’s comparatively small tail could accept a 310 hp engine, like the one mounted on the Cessna 400 or Cirrus SR22-G3. (Obviously, any major aerodynamic change, such as a larger vertical stabilizer, would require a completely new—and very expensive—flight-test regimen for certification.)
Of course, pure power installed in any airplane is rarely an end in itself unless the airplane is named Rare Bear. [For more about Rare Bear and the Reno Air Races, read “Days Of Thunder” in Pilot Journal March/April 2008.] Power can introduce all kinds of expensive problems—higher fuel burn, a more forward CG, reduced range, lower payload—and doesn’t come close to generating a proportional, offsetting benefit. (The formula suggests that the speedup is roughly equivalent to the cube root of the power increase.) Given enough power, you could probably blast the Queen Mary into orbit, but power has never been Mooney’s overriding philosophy.
The most efficient answer may be a combination of power and improved aerodynamics, and Mooneys have always offered more than their share of slick designs, a tough task with a predominately all-metal airplane that’s, by definition, more difficult to mold and shape than composites.
In this case, Mooney brought in one of the grand gurus of speed innovation to accelerate the Acclaim, Curt LoPresti of LoPresti Speed Merchants (www.speedmods.com) in Vero Beach, Fla. More than coincidentally, Curt’s father, the late Roy LoPresti, headed the design team that produced the remarkable Mooney 201 in 1976, wringing another 14 knots from the basic Mooney Executive fuselage and wing without a power increase. The elder LoPresti lived by the motto, “Life is short—fly fast.” Roy went on to become president of Mooney in 1984.
His eldest son, Curt, along with mom Peggy and brothers David and Jim have been working on Piper/Cessna/Beech/ Cirrus/Grumman American products, along with older Mooneys, for the last 20 years, and Curt was happy to apply his considerable aerodynamic skills to the new, ultimate Mooney.
“All the Mooneys are very clean designs, so there’s not a lot left to improve,” says LoPresti. “We analyzed the airplane’s drag profile and did find a few areas where we could clean up the airplane. Our calculations suggested the changes would generate about five knots more speed, and that’s about what they got.
“We discovered the most significant areas of excess drag were the nosegear and main landing-gear doors. The stock nosegear door had a bulge that was causing air to separate, creating burble,” LoPresti explains. “Mooney faired that in, creating a smoother passage for the air. The main gear doors also were a little too fat where the gear trunnion extends. Mooney also solved that problem.
“Additionally, we recommended installing a flap gap seal to keep air from leaking through the slot between the flap leading edge and wing trailing edge,” LoPresti continued. “Our final recommendation was that they remove their current flap hinge fairings, as they were causing more drag than they were curing.”
Before you can log the big numbers in cruise, you have to reach the flight levels, and the Acclaim Type S does that with dispatch. Flying from near-sea-level at Plant City, Fla., a few miles west of Lakeland, we lifted off and started the stopwatch on our climb to the flight levels.
I held a modified cruise climb of 110 knots pointed uphill, rather than Vy, in the interest of better engine cooling and improved over-the-nose visibility. ATC was willing on the day of our flight, and we were able to high jump all the way to FL250 without any level-off at interim altitudes. When I clicked the button at the top, time was 25 minutes and nine seconds, almost exactly 1,000 fpm. The rate varied from about 1,200 fpm initially to 900 fpm when I pushed over at 25,000 feet.
With such climb on tap, many Bravo and Acclaim pilots tend to fly high much of the time, especially eastbound, where the prevailing winds usually give you a push. Flying in the opposite direction, you can always opt to stay low where winds are lightest.
Standard fuel on the Acclaim Type S is 100 gallons. That’s plenty for most pilots, but for those aviators with the inclination to cover long distances at one sitting, the optional, 128-gallon long-range tanks provide truly bladder-stretching reach. Max cruise extracts about 22 gph from the quickest Mooney, so its apparent standard endurance is roughly four hours plus reserve. If you’re willing to settle for 200 knots at FL250, however, you can reduce fuel burn to just under 13 gph.
Opt for the 128-gallon tanks, and that translates to 8.5 hours of endurance and 1,700 nm of range, provided, of course, that you’re willing to sit in the seat for a full work day. Even I’m not that masochistic, but the message is clear: Any reasonable mission you can conceive, the Acclaim Type S can probably fly. Perhaps even better, if the cabin load will allow, you can buy the long-range tanks, fill them with the cheapest fuel you can find and fly an out-and-back without having to refuel.
No matter what your mission profile, you’re almost certain to notice the room and comfort of the Acclaim Type S. That’s because its dimensions have always been better than most pilots realize. The myth is that Mooneys are universally cramped and compact airplanes. The myth is just that—a myth. Width at the elbows in the front seat of the Acclaim Type S is a significant 43.5 inches. To put that in perspective, it’s 1.5 inches wider than a G36 Bonanza or G58 Baron’s cabin. True, seating is more laid-back in the Mooney than in other airplanes, so the vertical dimension is admittedly shorter, but legroom is excellent, and overall comfort is better than you might expect. Baggage goes behind the rear seats in a huge compartment limited to 120 pounds.
If comfort is better than you expect, avionics sophistication is also equal to anything in the class. Mooney has embraced the Garmin G1000 dual flat-screen avionics suite, along with the Garmin G700 autopilot. The level of avionics sophistication is only slightly below that of a Gulfstream, and the Mach number is just under 0.40.
Make no mistake, no matter what its other talents, the Mooney Acclaim Type S is all about speed. It makes no compromise with comfort, yet flies behind less horsepower and still manages to go faster than anything else in its class. It’s designed for the pilot for whom nothing but the fastest will do. Roy LoPresti would be proud.
Mooney Acclaim Sets World Speed Records
Alex Coley of Jacksonville, Fla., recently set a new world speed record between San Diego, Calif., and Jacksonville in a new Mooney Acclaim. Coley, along with flight instructor Tim Wadsworth, flew from San Diego’s Lindbergh Field to Mooney’s home airport in Kerrville, Texas, refueled the airplane and people in 12 minutes and continued their flight to Craig Airport in Jacksonville. At an average speed of 265 knots, Coley and Wadsworth made the 1,848 nm transcontinental crossing in only six hours and 59 minutes.
Here at Plane & Pilot, we know a little about Mooney speed records. Back in March 1994, Senior Editor Bill Cox piloted a stock Mooney Bravo, the Acclaim’s predecessor, slightly farther (1,867 nm) from Los Angeles to Jacksonville in seven hours and nine minutes, for an average speed of 261 knots. Cox also set new, Class C1C speed marks for Los Angeles to Albuquerque (294 knots), Los Angeles to Dallas (285 knots) and Dallas to Jacksonville (258 knots). Fourteen years later, those records still stand.

Cirrus SR20
Unless you are brand-new to general aviation or have been under a rock for the past decade, you know by now the Cirrus Design story. Wisconsin brothers Dale and Alan Klapmeier started building kit airplanes, but soon recognized that the real market was for a new-generation mainstream-certificated airplane. In 1995, they announced, with much fanfare, that they were going to produce just such an airplane. The airframe would be composite and incorporate the latest thinking in aerodynamics and survivability. Unusual doors that lift upward and forward (actually, in the mock-up they were sliding doors like your minivan has), opening to a wide and comfortable cabin. The plan was to incorporate the latest avionics and engine management systems to reduce pilot workload and improve situational awareness. And deliver it all at a higher "value" than was then available in the market.
Safety
At first, Cirrus planned to offer a unique rocket-powered parachute as an option. Later, the Klapmeiers decided that the parachute would be standard equipment. The parachute is designed to lower the aircraft to the ground in such a way that those inside would survive. However, the 1,800-foot-per-minute descent rate beneath the deployed parachute will most likely damage or destroy the aircraft upon impact in the worst case scenario. Still, as a last-ditch effort in the event of a loss of control, it's not a bad safety net. “In 2002, the Cirrus Airframe Parachute System™ made aviation history with the first safe landing by a private pilot after deploying the parachute.” (Cirrus Design Corp.)
Development and certification of the parachute system took many months and many tests. Eventually, the system, dubbed CAPS, for Cirrus Airframe Parachute System, earned FAA approval.
Hidden in an area in the aft fuselage, the parachute and its rocket, along with the extra structure to accommodate the system, weigh less than 80 pounds. A pull forward and down on the handle ignites the rocket motor and propels it out through the skin of the aircraft, pulling the parachute with it. Wide straps buried just below the composite exterior skin of the fuselage, running beneath the door openings, are ripped free by the force. In the end, the fuselage is suspended by the straps, which are attached to the firewall and the aft cabin. The system requires almost no maintenance, just an inspection and repacking of the chute every 10 years and perhaps replacement of the rocket motor.
The Klapmeiers believe that the aircrafts’ avionics and navigation systems will improve situational awareness. On Cirrus Aircraft, the Avidyne Multi Function Display has always been standard. Later models are equipped with the Avidyne Entegra Integrated Flight Deck, providing the pilot with a new level of situational awareness and safety.
SR20- Handling and Performance
The SR20 has a very solid, stable feel to it in flight. At slow speeds, the unusual leading edge cuff comes into play to prevent the aircraft from easily entering a spin. Cirrus certified the SR20 in the "spin resistant" category, thanks to the cuff. The cuff causes the air flowing over the ailerons to remain "attached" to the wing at very high angles of attack. As a result, the ailerons remain effective even after the inboard portions of the wing have stalled. Because of this, you can easily fly the airplane, feet on the floor, despite much of the wing's being stalled. You'll be descending at several hundred feet per minute, but with complete aileron control. The intent is to prevent the common base-to-final-turn stall-spin accident by allowing the pilot to simply roll wings-level even in a stall. There is plenty of natural buffeting to alert even the most distracted pilot that the aircraft is entering a stall. It's a good system and a significant safety enhancement.
Part of the reason for the SR20's stellar cruise speeds on such a small, efficient engine is the composite fuselage. The fiberglass material allowed the designers to carefully shape the fuselage to be aerodynamically efficient. In the beginning, the airplane was to be all composite, but Cirrus engineers discovered fairly early in the process that it was difficult to make strong and stiff flight control surfaces out of fiberglass because of the tight spaces inside, particularly at the trailing edges. As a result, the SR20 has aluminum ailerons, flaps, rudder, and elevator.
The engine itself delivers other efficiencies. The Continental IO-360-ES utilizes both tuned induction and tuned exhaust to efficiently extract every horsepower while keeping fuel flows down. A tuned induction system delivers an equal amount of air at the same velocity to each cylinder, allowing efficient and consistent combustion from cylinder to cylinder. A tuned exhaust system, evidenced by the long parallel stacks along the belly, decreases exhaust back pressures, allowing the engine to efficiently deliver rated horsepower with minimal fuel burn.
Overall, the SR20 combines a unique blend of tried-and-true systems married to many advances in safety and avionics, all bundled into a robust and efficient airframe.

Cirrus SR20 G3
To be perfectly honest, I'd forgotten just how basic an airplane the first generation SR20 is. Sure it has a chute and it is all-composite, but despite that, the basic airplane feels pretty Spartan and, to be even more honest, a little rough around the edges.
I'll forgive myself the lapse of memory. After all, the airplane has been more or less constantly changing since its introduction almost 10 years ago, getting avionics upgrades on a few occasions, improved doors (thank heavens) a while back, upgraded interiors on a couple of occasions, not to mention the transformative addition of flat-panel avionics as standard equipment a few years back. Whether you want to call it polished, evolved or simply improved, you won't get an argument from me. Regardless of how you phrase it, the G3 is far and away the best SR20 that Cirrus has built yet.
I don't think Cirrus planned it that way in the beginning, but for years now the SR20 has played second fiddle to the company's faster and more powerful SR22. Consequently, people don't get very excited about it, and we've all but forgotten the commotion that accompanied the then-startup company's first delivery of the all-composite SR20 200 hp single back in 1999. The excitement was justified. The SR20 was the first high-profile new piston single-engine airplane to earn FAA Part 23 certification in years, and it came at a time when the industry was ready for a change and even more ready for some success.
In the years prior Cirrus co-founders and brothers Alan and Dale Klapmeier had all but abandoned the experimental market and their earlier kitplane, the sleek but problematical VK30 four-seat pusher. The brothers and their team retreated into the secrecy of Hangar X to plot their to-be-certified follow-on effort.
But much to the dismay of aviation rebels, the airplane that emerged was a very conventional looking four-seat fixed-gear single with the engine in the front and the tail in the back. Cirrus called it the SR20, which sounded pretty corporate, as well.
But if the iconoclasts were disappointed by the outward conformity of the new airplane, there was more to it than met the eye: a whole-airplane recovery parachute, side yokes, a big flat-panel MFD and more.
Their conservative industry counterparts, however, were skeptical about the prospects across the board. The airplane didn't go through the conventional flight test certification spin matrix, relying instead on the presence of the chute for credit on that testing. And the chute just rubbed traditionalists the wrong way (still does, for many).
But Alan and Dale Klapmeier were true idealists, hellbent on creating an airplane that did things differently. And they did just that.
A New Generation
With the introduction of the SR22 G3 with its all-new carbon fiber wing last year, I figured that the introduction of the next-generation SR20 was only a matter of time.
It's simple economics, really. It just saves a lot of time and money to build more of the same thing than to build two different kinds of parts. Detroit has known that since the days of Henry Ford, and it's no different for 800 airplanes a year than it is for half a million cars.
Besides, the new wing was a clear improvement over the old one. How so? Let me count the ways.
For starters, it's both lighter and stronger, resulting in a 50-pound increase in max takeoff weight, which, in identically equipped airplanes, translates directly into additional useful load. Unlike the SR22, which got around 40 minutes of additional fuel (11 gallons, to be precise) with the G3 makeover, the SR20 doesn't get more fuel despite there being plenty of room -- it is, after all, the same wing. Apparently the rationale is, because the '20 is an airplane with limited horsepower, giving the pilot the option of seriously overloading the airplane with passengers and fuel was a bad idea. Granted, some pilots of small airplanes do have a hard time leaving fuel out of the tanks.
The new wing is longer, around three feet longer, in fact, and it features greater dihedral than its predecessor. It is simply a much better flying wing than the old one, so much so that Cirrus was able to eliminate the rudder-aileron interconnect that provided improved stability on previous models, so handling is far smoother.
Another G3 change the '20 inherited was a landing gear that's lankier by about two inches, which doesn't sound like much but somehow still winds up making the airplane look noticeably taller. You can even feel it when you climb up onto the wing.
There are numerous other little and not-so-little things, an improved fresh air inlet, better wing root fairings and the addition of LED recognition lights.
While it does nothing for the performance of the airplane, perhaps the biggest overall change is to the interior, which features newly designed backlit switches, one-piece bolsters and new choices of leather and fabrics, all features the SR22 got with the G3 edition, as well.
As you've no doubt read in Flying and elsewhere, the latest news from Cirrus is the introduction of the Garmin Perspective avionics suite. Perspective is not an option on the SR20, and there are no plans to make it one. There surely will be customers who will complain about the omission, at least until they think about the approximate $50,000 price increase the Garmin panel brings with it, an increase that would make the SR20 a $400,000 airplane, which is more than the SR22 topped out at not too long ago.
Besides, the Avidyne Entegra flat-panel system, which is standard in the SR20, is a marvelous package with an impressive list of standard and available safety functions, like TAWS, traffic awareness, IFR charts and XM Weather, not to mention a very nice rate-based autopilot, the S-Tec 55X, as standard equipment, as well.
On top of that, the Garmin GNS 430 navigators that come standard in the SR20 are WAAS equipped. WAAS, as you probably know by now, makes a lot of new vertical nav semi-precision approaches available to the instrument pilot, many of them at airports that never had vertical nav approaches.
Faster, Gentler, Smoother
****I recently traveled up to Dallas' Addison Airport to fly the newly released SR20 G3 GTS with Cirrus representative Reid Nelson, with whom I first flew the SR22 G3 model. With no turbocharging, TKS, oxygen or air conditioning, the SR20 is no SR22, nor is it meant to be.
That said, the SR20, often dismissed as a first airplane or an advanced trainer, is actually a surprisingly good cross-country airplane, especially with the new wing and especially when outfitted with the upscale GTS trim package.
Flying out of Addison it seemed that the longer wing was indeed doing exactly what longer wings are good at, climbing fast. Cirrus lists an initial rate of climb of better than 800 fpm, and we seemed to be doing a little better than that. (Though why is it that every demo pilot I fly with seems to leave the tanks half filled?)
Keeping the airplane down low to stay below Dallas' Class Bravo airspace, I had a chance to hand fly the airplane, and I liked what I saw. The improvement in handling is even more dramatic in the SR20 than it is in the '22, and that's saying a lot. The feel of the side yoke is much smoother and the interaction of the controls is much more harmonious than on the previous SR20 models, even in slow flight and down into the stall.
And that's a big help, as the side yokes, which are fundamentally different than side sticks, feel better than ever. Unlike the sticks in Cessna's Bend, Oregon, airplanes, the yokes in the Cirrus airplanes are like having little Cessna- or Piper-style yokes complete with a forward and backward travel component, just mounted along the side (and canted a little inward, at that). As is the case with the G3 upgrade to the SR22, the smoother handling of the SR20 G3 makes it seem as though the yokes are improved, when in fact they're just doing an easier job. Either way, it's a nice enhancement.
At cruise, the realm where fully decked-out airplanes like the one I was flying will spend most of their time, I saw a big improvement in speed, as well. While Cirrus only advertises 156 knots true, we saw readings as fast as 162 knots at 3,500 feet, and around 158 knots up at more typical altitude of 6,500. To put it in perspective, that's about 20 to 25 knots faster than a Piper Arrow, a retractable-gear airplane, on the same power and about the same fuel flow in a totally modern airplane with a much larger cabin and with lots of extra features. It's an interesting commentary that we've come to think of the SR20 as a midperformance airplane, and it's only because of the remarkable performance of its stable mate and a few remarkably fast models from its competitors.
After checking out the handling of the airplane, we stopped into a couple of Dallas-area airports to fly some approaches and shoot some touch and goes.
As I expected from its slow flight manners, the G3 model has significantly improved handling in the pattern and on landing. With the rudder interconnect gone, the feel of the airplane is much more natural than before. That's good for everyday flying, sure, but it's also a real bonus for flight schools, whose students are going to love the way the new airplane handles, and the flight schools are going to love the additional clearance, thanks to the longer gear.
As we've written before many times, the addition of WAAS to the Garmin navigators gives pilots more precision and more instrument approach options, and the Avidyne EX5000 multifunction screen can show Cirrus' CMax Jeppesen approach charts, giving the pilot a nicely integrated set of tools, from navigators to displays to autopilot.
Heading back to Austin from Dallas, a typical midrange trip, an airplane like the SR20 really shines. With traffic on I-35 the trip at crunch time can take four hours, but with the SR20, we did it in just over one. (I made it up to Dallas that morning in less than an hour in my PlaneSmart SR22). Flying a '20, I could have easily flown up, conducted a day's worth of business, flown back down and been home in time for dinner. In fact, that's exactly what I did that day, in comfort and high style.
For more information about the SR20 and the many programs that Cirrus has developed for it, visit cirrusdesign.com.

Cirrus SR20 in the Limelight
June 2010 — BACK IN 1998 FLYING sent ace photographer Paul Bowen to Chicago to photograph a revolutionary new airplane, the Cirrus SR20. Editor-in-chief Mac McClellan flew the airplane and weighed in on such eye-opening new features as the BRS whole-airplane recovery parachute system, the down-and-welded landing gear (unusual at the time for such a fast single) and the signature Cirrus side-yoke. It's a little hard, 12 years after the fact, to remember the kind of controversy these features — the chute, in particular — generated, but they did. And it might be a little hard for those of us who have flown the two Cirrus airplanes to remember just how unrefined those first-generation airplanes were, but this, too, is true. The fact is that we were all just getting to know the airplane, the company and, indeed, the whole concept of the fast, composite, fixed-gear four-seater. The SR20 was that true pioneer.
That said, with Cirrus' introduction shortly after of the substantially more powerful and better performing SR22, the SR20 suddenly seemed like a footnote. It wasn't that there was anything wrong with the SR20; on the contrary, it was pretty much everything the company said it would be. But the lure of the 180-knot SR22 made the 150-knot-on-a-good-day SR20 look a lot less tempting. And that's not a casual observation. The SR22 outsold the 20 by a margin that some years approached 10 to 1.
Article Continues Below:
Aerobatics with Matt Chapman at Oshkosh 2016
Flying magazine met up with airshow performer Matt Chapman in Oshkosh for ...
It wasn't that Cirrus wasn't trying to sell 20s. From the start, it has felt that this 200-horsepower cruiser was a solid performer that was a great fit for a certain kind of customer. There just didn't seem to be that many of those customers.
The SR20 was simply overshadowed by its star teammate. I saw it firsthand. A few years ago I had reserved an SR22 with my shared-ownership provider PlaneSmart to fly from Texas to Sun 'n Fun in Lakeland, Florida, with a friend. When a minor mechanical issue grounded my airplane just before the trip, the folks at PlaneSmart sheepishly offered me an SR20 instead. A bit surprised by their apologetic attitude, I responded that I would be very happy indeed to fly the 20 to Florida. I did fly it out, and it was a great trip. It took noticeably longer than it would have in the SR22, but that was for a maximum-range trip. And it was about 10 knots faster than the comparably powerful Piper Arrow on around the same amount of fuel and without the cost, risk and complications of the retractable gear. Not to mention the far nicer interior of the Cirrus. I was happy.
It should also be noted that over the years the SR20 has become a much better airplane. Part of that is a reflection of Cirrus getting better and more efficient at building airplanes. The first sub-$200,000 SR20s, it's widely believed, were sold at a loss, and Cirrus didn't start improving its profitability until it started being able to produce airplanes with many fewer labor-hours invested in each one. A few years back Cirrus introduced its SR22-G3, which featured, among other improvements, an all-new wing that included a redesigned interior structure and a carbon fiber spar. It was stronger, lighter (around 40 pounds lighter in the wing alone) and much easier to produce. Before too long the SR20 got that same G3 treatment, including the new, longer wing, along with a higher profile gear designed to get the prop farther off the ground. The result was a faster and more durable airplane that, in my opinion, handles better than the original does, with increased dihedral in the wing eliminating the need for the rudder/aileron interconnect on previous Cirrus airplanes.
The G3s also benefited from the many quality-of-life improvements Cirrus made to its airplanes, including a better looking and more durable interior, much better functioning and easier-to-use entry doors, improved soundproofing and better fit and finish, which included recessed switches, a whole new, easier-to-reach circuit-breaker panel and available premium interior options.
There were, of course, improvements in the avionics. While Cirrus originally thought the SR20 might remain a steam-gauge airplane while the 22 went glass in 2003, that notion was quickly dispelled when almost no one ordered either with anything but the Avidyne Entegra flat-panel avionics system that pioneered flat panels in small airplanes.
Then, two years ago, the same thing happened when Cirrus launched its Perspective by Garmin cockpit, an enhanced version of the G1000 integrated system with a remote data-entry keypad, larger displays and synthetic vision. At first Perspective was available only in the SR22, though Cirrus soon made it available in the SR20, and it has become a popular choice for private individuals who buy an SR20 — most flight schools stick with the Avidyne Entegra system in their more-pared-down SR20s.
Flying the SR20
My numerous long cross-countries in the SR20 have been excellent experiences. They are comparable to flying the same trips in the normally aspirated SR22, though the airspeed, it goes without saying, is slower, about 155 knots in the 20 compared with around 180 knots true in the 22. So a 500-mile leg in the SR20, figuring climb, which is slower in the less-powerful airplane, takes about 45 minutes longer. Tack together two of those legs, as is typically done for many of my trips, including Austin, Texas, to Phoenix or Austin to Orlando, Florida, and you've got a substantially longer day in the SR20 — longer, though still very doable.
The range of the SR20 is, likewise, less than that of the SR22, because the fuel capacity of the new SR20 is just 56 gallons, compared with 92 for the SR22. Still, with the miserly fuel consumption of the six-cylinder Continental IO-360-ES engine — 11.6 gph at 8,000 feet and 75 percent power — the SR20 manages a cruise range of 627 nautical miles, a figure that will put you in the air for just over four hours (with a 45-minute reserve), which is about as long as most folks want to be flying between stretches of the legs. This is about 200 nm less than the range of the SR22.
I recently flew a new SR20 with Cirrus' Matt Bergwall, who was kind enough to bring the airplane down to Austin from Duluth, Minnesota, for the evaluation. For the flight, I chose to go from my home airport of Austin Bergstrom International (KAUS) to Scholes International Airport (KGLS) in Galveston, because the trip from Central Texas to a Gulf Coast Texas city represents an excellent demonstration of the capabilities of the SR20. At 160 nautical miles, AUS-GLS is the kind of trip that takes far too long in a car. And if you want to take the airlines, well, you'd better plan for that journey to take longer than it would if you drove. Flying a small airplane is by far the best way to get from this particular Point A to that particular Point B. It's also a distance that underscores the utility of the SR20, which made the trip, including short vectors on departure, a climb to 5,500 feet and a jog around the southern end of Houston's Class Bravo airspace, in just over an hour. A flight in an SR22 would have beat that figure by maybe 10 minutes, about the amount of extra time you'd spend on the ramp with the SR22 if you, for instance, had to add a quart of oil before departure.
Even though it was the value-package SR20 S, the airplane we were flying that day was equipped with a lot of optional equipment, including the Perspective cockpit. Because it was headed for a European delivery, it also had DME and ADF.
In the SR20, the Perspective cockpit is almost identical to that in the SR22, but it has displays that are smaller, 10.4 inches diagonally compared with 12.4 for the SR22. I know that Cirrus has made a point of lauding the larger displays in the Perspective SR22, but I'm very happy with the 10.4-inch Entegra LCDs in the PlaneSmart G3 Turbo Cirrus I regularly fly.
I'm a big fan of the Perspective cockpit, and in the SR20 the Garmin system is an excellent, scalable fit. Apart from the smaller displays, there are few differences between the systems in the SR20 and the SR22, and most of those have to do with installed equipment. We've written at length about Garmin's Synthetic Vision Technology (SVT), and in the SR20 it's a great fit. On our way back from Galveston, we were scouting photo locations and, heading from one potential location to the next, we flew much lower — around 2,500 feet agl — than I'd normally fly while en route, and the Perspective was invaluable in several respects. While terrain is not a factor in the area, SVT helped me keep track of the many obstacles, namely towers and traffic, both of which show up on the primary flight display in a way that's hard to miss. You do still have to keep your eyes peeled, though, because there can be airplanes with no transponder in the kind of uncontrolled airspace we were namely towers and traffic, both of which show up on the primary flight display in a way that's hard to miss. You do still have to keep your eyes peeled, though, because there can be airplanes with no transponder in the kind of uncontrolled airspace we were flying through, as well as big birds, two of which we narrowly avoided hitting on our trip back home.
In addition to SVT, there were safety features galore on the airplane I flew for this report, including traffic and terrain alerting, Garmin charts, Garmin SafeTaxi and WAAS. The one thing missing was XM Weather, because, as I mentioned, the airplane is bound for Europe, where XM is unavailable. There's also the standard BRS whole-airplane recovery parachute system, a feature that Cirrus pilots overwhelmingly like having on board.
Along the way I was reminded of just how roomy the SR20 cockpit is. With a cabin width of 49 inches, and excellent headroom and legroom, the space you have available in the 20 is truly luxurious. It's hard to overstate this fact. I hadn't yet flown an SR20 with the X-Edition interior, but it was impressive in its fit and finish. The airplane we were flying was trimmed out with black leather and premium detailing. Despite its plain Jane reputation, this is one SR20 that has a lot of sex appeal.
The SR20 is often used as a transition airplane for new or inexperienced pilots who are looking to move up to an SR22, and it's an excellent platform for that purpose. It's a lighter airplane than the SR22, and it feels that way. It lands better than does the 22, which in my humble opinion is not the best-landing airplane in the world. The slightly slower approach speeds of the 20 and its natural stability, not to mention the excellent avionics, would make it a great instrument-training platform too.
For pilots looking for a good cross-country-capable airplane with sophisticated available equipment, great comfort and excellent economy, the SR20 is worth a long look, and not just as a transition airplane but also as one you could fly and love for many years to come.
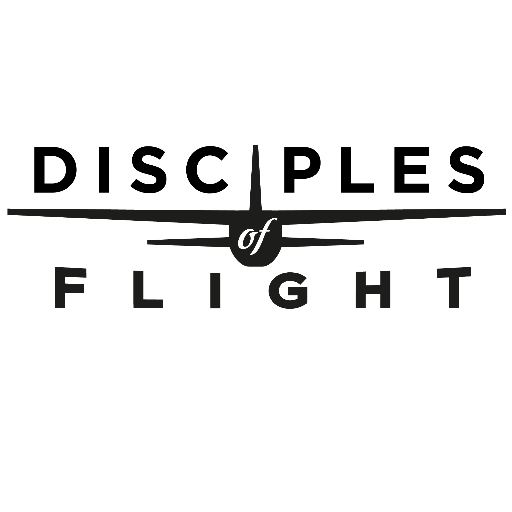
Cirrus SR22: The Plane with the Parachute
All About the Cirrus SR22, from the history to a mechanic’s perspective on how the aircraft stacks up.
“What we’re after is making aviation safer. We want our airplanes to be the safest airplanes. That’s why we design them, that’s how we design them.”
– Dale Klapmeier, Co-Founder and CEO, Cirrus Aircraft
Anders
Cirrus Aircraft Corporation, originally Cirrus Design, was founded in 1984 by brothers Alan and Dale Klapmeier to produce the VK-30 kit aircraft. Over the years, Cirrus has transitioned from being a kit building company to a full fledged aircraft manufacturer, all the while navigating some serious business turbulence. During the tough times, however, Cirrus never stopped refining their designs and pushing forward in their quest to produce the safest airplanes possible. In 2001, they released the aircraft that they are most recognized for, the Cirrus SR22. With the first SR-22s rolling off the line in 2001, it very quickly became a wildly popular aircraft. By 2004, the Cirrus SR22 was the world’s best selling single engine aircraft, a title it has retained every year since, and currently holds.
So, how did the SR22 come about? What features make it stand out from other aircraft? How exactly does its CAPS (Cirrus Airframe Parachute System) work? Does its safety record hold up? What does a seasoned, veteran mechanic think of the Cirrus SR22? I’m going to tackle these questions and more, and to make it easier for you, I’ve broken the information up into sections. So if you aren’t as interested in the history of the company or the aircraft, then skip those sections. Though if you do skip any of this article, just know you will make me sad, and I will shed one tear for each section you skip. So without further delay, grab your favorite beverage, park yourself in a comfy chair, and let’s get to it!
A Brief History of Cirrus Aircraft Corporation
In the early 1980s, the VK-301 was conceived as a kit plane project by three college students: brothers Alan and Dale Klapmeier and Jeff Viken2. They formed Cirrus Design in 1984 and started building a prototype of the Cirrus VK-30 in the basement of the Klapmeiers’ parent’s barn in Baraboo, Wisconsin.
The VK-30 was designed as a five-seat aircraft from the beginning, making it significantly larger than most home and kit built aircraft at the time. It featured an all composite construction, had a low drag design, and mid-engine placement for a 300 hp Continental IO-550-G engine. This engine, through an extension shaft, drove a three-bladed pusher propeller that was mounted behind the tail of the aircraft.
A few years into the design phase, the Klapmeier brothers were able to borrow some money and move the project to their own factory located at the Baraboo airport. After completing the design3, the first test flight of the VK-30 took place on February 11th, 1988 and Cirrus began delivering kits a short time later.
In 1994, Cirrus relocated to a much larger facility in Duluth, Minnesota, and in 1996, announced plans to build a new factory at the Grand Forks International Airport in Grand Forks, North Dakota. Around this same time, the company discontinued production of the VK-30 and began developing the Cirrus SR20. The SR20 was type certified in October 1998, and they began delivering the aircraft in July of 1999.
In November of 2000, they received a type certificate for their next model, the Cirrus SR22. The following year, they began delivering the SR22s and sold a controlling stake in the company to an international investment group for $100 million. By 2004, the Cirrus SR22 had become a huge hit, propelling Cirrus to a record-breaking 69% increase in sales over the previous year. In 2006, Cirrus celebrated rolling their 3,000th aircraft off the production line after only 7 years. Business was good, and Cirrus rode this high, increasing sales and operations each year until 2008 when the global sales slump in piston engine aircraft hit.
Over the next few years, Cirrus struggled, cutting costs wherever possible and having to lay off employees at their various locations. Finally, after circling closer and closer to a possible bankruptcy, the company was purchased in 2011 by CAIGA (China Aviation Industry General Aircraft, owned by the Chinese government) for $210 million. Though some concern was expressed over ownership of the company leaving the US4, CEO Dale Klapmeier gave assurances that production of Cirrus Aircraft would remain in the US.
In 2012, Cirrus was recovering nicely on the financial front and indicated that they were making good progress on certifying the Vision SF-50 Jet. They began hiring new workers, and in 2013, they had their best year since the 2008 slump. And finally, on March 25th, 2014, they had the first test flight of the Vision Jet.
(The Vision SF-50 , Photo by Kentaro Iemoto, CC2)
The Path to the Cirrus SR22
So, let’s rewind a couple of decades to the mid-1990s when grunge musicians were mumbling their way to fame and fortune, and James Cameron was blowing people’s minds at the dawn of full-fledged CG artistry. Cirrus had just discontinued production of the VK-305 kits and was transitioning from being a kit plane business to becoming, with the Cirrus SR20, an airplane manufacturer. And though they were moving away from kit planes, the legacy of the VK-30 was important.
(A very rare, completed VK-30)
The VK-30 had been a fairly obscure and unconventional design, and Cirrus estimated that only 13 VK-30 kits were ever completed6. Through the process of designing and marketing this kit, Cirrus realized two things: they needed to go with a more conventional design, and it needed to be a certified production aircraft and not a kit. So, by 1998 they had certified the SR20, and by 1999, they were delivering it to customers.
The SR20 was a boundary-pushing aircraft and set a number of firsts. It was the first production general aviation aircraft that had a parachute (the debut of CAPS). It was also the first manufactured aircraft to be completely constructed from composite materials, have side-yoke flight controls and feature the option for full flat panel avionics with dual 10 or 12-inch flight displays. And in 2004, the SR20 also became the first aircraft to receive the new European Aviation Safety Agency certificate for aircraft being imported into the European Union.
(The Cirrus SR20, Photo by Dbreemeersch, CC3)
That’s a pretty impressive first effort for an airplane manufacturer. So how did Cirrus decide they were going to top that? With an even more refined, powerful, capable aircraft: the Cirrus SR22. Rather than taking a breather and basking in the success of the SR20, Cirrus pushed forward and by November 2000, had received the type certificate for the Cirrus SR22. By 2001, they began delivering the plane to customers.
The Cirrus SR22 Models
The original Cirrus SR22 models featured all-composite construction, came standard with CAPS, had four seats, a nose mounted 310 hp Continental IO-550-N piston engine, and standard analog flight instruments accompanied by a 10-inch multi-function display. Starting in 2003, select SR22s featured the Avidyne Entegra primary flight display in place of the traditional instruments, and later that same year this became a standard feature on the aircraft. This made the Cirrus SR22 the first aircraft of its type to come standard with fully integrated flat panel avionics, or a “glass cockpit.”
In 2004, Cirrus introduced the 2nd generation SR22 or SR22 G2. In addition to the now-standard glass cockpit, the G2 featured a variety of other changes. Included among those changes, the fuselage underwent some small redesigns, resulting in fewer overall parts and better maintenance access points; the engine now featured a six point mount instead of a four point mount, which cut down on engine vibration; the interior was redesigned to be a little more comfortable; and the front seat shoulder harnesses now came standard with airbags.
2006 saw the introduction of the first turbocharged model, the SR22 Turbo G2. This turbo model featured a factory installed (under a Supplemental Type certificate) Tornado Alley turbo-normalizing upgrade kit, featuring twin turbo-normalizers and twin intercoolers. Cirrus also included built-in oxygen with this conversion and added a new Hartzell 3-blade lightweight composite propeller. The additional weight from these conversions reduced the useful load of the aircraft7, but gave the aircraft a certified 25,000 (7,600 m) foot ceiling, a maximum cruise speed of 211 knots (243 m/h, 391 km/h) and a top speed of 219 knots (252 m/h, 406 km/h). There were also cosmetic upgrades to the interior of the aircraft, including black leather seats.
The third generation aircraft, or Cirrus SR22 G3, arrived on the scene in 2007 and featured a whole slew of changes (more than 700 individual changes according to Cirrus) and upgrades. And though many of those were subtle refinements, there were plenty that were much more noticeable. To start, the wing was redesigned with a more pronounced dihedral angle, which added enough stability to the plane that Cirrus could eliminate the rudder/aileron interconnect which further enhanced the quality of the flying. The wing also had a longer internal spar, built from lighter, stronger carbon fiber, which allowed for shorter wingtips and more room for the fuel tanks. This meant fuel tank capacity increased from 81 to 92 gallons (310 to 350 L). More impressively, due to the stronger, lighter material used in the wings construction, the overall weight of the wing was decreased by 66 pounds (30 kg), meaning the increase in range came without a resulting decrease in the full fuel payload. In addition, the improved wings featured better recognition and taxi lights and improved aerodynamic shaping on the trailing edge of the airfoils. Cirrus also redesigned the landing gear to be taller, allowing for better prop
More impressively, due to the stronger, lighter material used in the wings construction, the overall weight of the wing was decreased by 66 pounds (30 kg), meaning the increase in range came without a resulting decrease in the full fuel payload. In addition, the improved wings featured better recognition and taxi lights and improved aerodynamic shaping on the trailing edge of the airfoils. Cirrus also redesigned the landing gear to be taller, allowing for better prop clearance and adopted the composite Hartzell propeller from the previous year’s turbo model. Many refinements were also implemented in the interior, including improved environmental controls, a nicer switch panel and improved door opening and locking mechanisms. Optional upgrades included XM Weather and Radio, a 60/40 split back seat configuration allowing for five passengers and additional shoulder harness airbags for all seats.
In 2009, Cirrus partnered with Garmin to develop a new glass cockpit, the Cirrus Perspective. The current Avidyne system and the Cirrus Perspective were both offered in new G3 models, though the Perspective eventually won out and became the new standard system for the SR22. 2009 also saw another important upgrade for new Cirrus SR22 G3 models. In January 2009, Cirrus finished testing its TKS anti-icing system, aimed at providing private pilots with additional protection against icing. The FAA certified the system in April 2009, and installation of this upgrade was offered immediately. This involved adding larger, 3.5-gallon tanks to the wings for de-icing fluid, and installing the lines and ports necessary for the TKS “weeping wing” system. This system delivered de-icing fluid to the leading edges of the wings as well as the horizontal and vertical leading edge surfaces on the aircraft’s tail. With the two tanks of fluid, it was estimated that a pilot could endure icing conditions for an extra 2.5 hours, but Cirrus stressed that this was not meant to encourage flight into known icing conditions, but rather give them an additional margin of safety should they hit icing conditions.
The Turbo model saw the next upgrade, in 2010. Dubbed the SR22T, this model featured a ground-boosted 315 hp Continental TSIO-550-K engine. Equipped with low compression pistons (with a 7.5 to 1 compression ratio), the engine was capable of using a lower octane fuel, 94UL. The SR22T maintained the certified flight ceiling of 25,000 (7,600 m) feet and increased the cruise speed to 214 knots (246 m/h, 396 km/h).
Finally, in 2013, Cirrus debuted the fourth generation standard and turbo models. However, just to keep private pilots everywhere on their toes, they skipped G4 designation and instead called the new models the Cirrus SR22 G5 and SR22T G5. The aircraft’s maximum takeoff weight increased by 200 pounds (91 kg); the speed at which flaps could be deployed was increased; the ADS-B transponder, Garmin GFC700 autopilot and 60/40 split backseat configuration that allowed for five passengers now came standard; and improvements were made to CAPS. In previous models, CAPS used a pyrotechnic based rocket ignition system to deploy. The G5 models introduced a new, failsafe electronic ignition, a larger parachute canopy to account for the increase in takeoff weight and a more powerful rocket. This meant deploying the parachute was now possible at speeds of up to 140 knots (161 m/h, 259 km/h) versus 133 knots previously.
Cirrus SR22 G5 Specs
Here are the specs for the current Cirrus SR22 G5 base model:
General Characteristics
Crew: one
Capacity: four passengers
Fuel capacity: 92 US gallons (348 liters)
Base price: $499,900
Weight
Empty weight: 2,260 lb (1,009 kg)
Gross weight: 3,600 lb (1,633 kg)
Useful load: 1340 lb (607 kg)
Cabin Payload with 3-hour trip fuel and 45-minute reserve: 974 lb (442 kg)
Engine
Powerplant: 1 × Continental IO-550-N Six cylinder horizontally opposed aircraft engine, 310 hp (230 kW)
Propellers: 3-bladed, Hartzell composite
Dimensions
Wingspan: 38 ft 4 in (11.68 m)
Length: 26 ft 0 in (7.92 m)
Height: 8 ft 11 in (2.72 m)
Cabin width: 49 inches (124 cm)
Cabin height: 50 inches (127 cm)
Performance
Takeoff: 1082 feet (330 m)
Takeoff over 50-foot obstacle: 1868 ffeet (569 m)
Rate of climb: 1,270 ft/min (6.5 m/s)
Max Operating Altitude: 17,500 ft (5,300 m)
Stall speed: 60 kn (69 mph; 111 km/h) flaps down
Cruise speed: 183 kn (211 mph; 339 km/h)
Range: 1,049 nmi (1,207 mi; 1,943 km) with reserves at 65% power
Landing groundroll: 1178 feet (359 m)
Additional Airframe and Powerplant Information
Cirrus Airframe Parachute System™ (CAPS)
Airbag Seatbelts (Front Seats)
Single Movement Power Lever
Dual Side Yoke
Dual Alternators
Advanced Wheel Fairings
High-Performance Brakes
Tubeless Tires
Surface Illumination Lights
60/40 FlexSeating™ – Seats up to 5
USB Power Ports
Standard Interior
2 Year Spinner-to-Tail Warranty
Avionics
Cirrus Perspective™ by Garmin® Cockpit
Synthetic Vision Technology (SVT™)
10’’ Screens
GMA 350 All-digital Audio Panel
Keyboard Controller
Dual WAAS GPS/Comm/Nav Radios
Engine & Fuel Monitoring
FliteCharts® & SafeTaxi® integration (subscription required)
XM® Weather and Audio integration (subscription required)
Garmin GFC700 Autopilot with Electronic Stability and Protection
Dual AHRS
Hypoxia Check & Automated Descent Mode
Blue Level Button
Autopilot stall protection
406 MHZ ELT
ADS-B Transponder
Popular factory offered upgrades to the Cirrus SR22 G5 include:
Perspective Plus
This upgrade adds a yaw damper to the aircraft, practically eliminating the need for rudder input during extended climbs and turns, offering a smoother ride for both the pilot and passengers. It also includes the Enhanced Vision System (EVS), which uses infrared technology to provide you with an image of the outside world during the night. It also adds a second Air Data computer, which adds redundancy and the ability to cross check information to your Perspective glass cockpit.
Known Ice Protection
As described previously, you can outfit your Cirrus SR22 with the TKS anti-icing system. In addition to the dual tanks, you get automatic tank switching, three flow rate options for the system and the full range of fluid duration and system operating information on your Cirrus Perspective. This option also comes with a Tanis engine pre-heater.
Premium Select
This upgrade package allows you to take to the skies in true style. It adds tinted rear windows, a polished spinner, sterling or two-tone paint for the aircraft exterior, a leather interior, and 12-inch screens on the Cirrus Perspective displays. It also comes with a solid gold cane, feathered hat, royal purple suit jacket and Certificate of Aviation Pimphood. (OK, OK, I may have made that last bit up, but I think it definitely should come with official Aviation Pimp (TM) gear.)
GTS
If you want everything, then this is the package for you. This deluxe package includes all the benefits of the Perspective Plus, Known Ice Protection, and Premium Select packages, and adds UV Protected windows, the Carbon or Platinum appearance paint options, and the new Cirrus Digital 4-in-1 Standby Instrument. According to Cirrus, this “combines the three standby instruments into a single instrument organized similar to the primary flight display, which provides a more familiar display to pilots whose scans and techniques are accustomed to electronic integrated flight displays.”
Cirrus SR22: Let’s Look at a Few More Features
So, the Cirrus SR22 is a pretty impressive aircraft. And though I’ve covered many of the features already, I’d like to spend a little time digging into a handful of interesting features found in the Cirrus SR22.
Fixed Gear Configuration
OK, so it has a fixed gear tricycle configuration. Why is that a feature? Well, even with fixed gears, the SR22 manages a cruising speed of just over 180 knots and outperforms many comparable high-performance aircraft in its class who are using retractable gears. This provides some nice benefits. A fixed gear setup is lighter and less mechanically complex, which brings down the cost of maintenance. It also eliminates the possibility of a gear up landing, which is nice for both the pilot and insurance companies. Pilots, especially low time pilots, also generally have an easier time finding insurance (and better rates) on a fixed gear aircraft.
The Sidestick
Adopting the sidestick setup was definitely an interesting move. It certainly looks radical, and though it serves as a source of anxiety for pilots unfamiliar with the setup, Cirrus has provided excellent training material, and the word from many pilots is that it’s not at all difficult to pick up. In addition, once they’ve learned the sidestick setup, many pilots report preferring it to the traditional yolk. The sidestick setup offers some other nice benefits: it cuts down on structure and weight and opens up the center for better viewing of the instruments and displays. Though the sidestick setup is still limited to Cirrus when it comes to production general aviation aircraft, and it’s not likely to take over the industry anytime soon, it’s a testament to Cirrus’ hard work that it’s become accepted with no controversy.
(Photo by: ObserveTheBanana, CC2)
Glass Cockpit
Though the adoption of the glass cockpit as standard isn’t always viewed as a positive8, it has allowed Cirrus to integrate with the latest technologies and offer pilots easy access to such things as instrument approach charts, remote-mount lightning detection, satellite weather, traffic awareness and GPS steering. Add to this the integration with other Cirrus specific systems like the TKS de-icing and ENV infrared vision system, and the pilot has easy access to a variety of additional safety features.
CAPS
More than any other design feature (and it’s important to note that this is a standard feature, and not an accessory or optional upgrade), CAPS is the one that most people are aware of and talking about. But before we get to how CAPS works, where did the idea come from?
In 1985, Cirrus co-founder Alan Klapmeier survived a harrowing mid-air collision. Almost three feet of wing was ripped off his airplane, including half the aileron. This experience inspired the brothers to work on figuring out a way they could implement a safety device on an aircraft that could give a private pilot a way out of bad situations. After years of thought and refinement, the Cirrus engineering team began work on the CAPS system in the mid-1990s and began testing it in aircraft by 1998. And, as the SR20s started rolling off the line in 1999, they became the first production general aviation aircraft to come standard with a parachute system. The first emergency use of the CAPS system took place in 2002 over Lewisville, Texas9. The result? The pilot survived, uninjured.
So how does this “whole plane” ballistic parachute recovery system work? The parachute is housed in the aircraft’s frame, in the aft of the fuselage, along with a small rocket. In an emergency, the pilot can activate the rocket, which shoots out, pulling the parachute behind it and deploying it within a matter of seconds. The plane then floats, rather than falls, to the ground.
It has provoked much debate over how much additional safety it actually provides. And until recently, a brief glance at the safety data might have led one to believe that it didn’t provide much additional safety at all. Between 2001 and May 2014, there were 147 US-registered Cirrus SR22 airplanes involved in accidents, resulting in 122 deaths. This accident record prompted Aviation Consumer to do a detailed review of the SR20 and SR22 in 2011. They found that the overall accident rate for the series was better than average for light aircraft, and only the Diamond DA40 and DA42 had a better record. However, they found the fatal accident rate was 1.6 per 100,000 flight hours, which meant it was higher than the average rate of 1.2 for general aviation aircraft in the US and much higher than other light aircraft like the Diamond DA 40 (0.35) or the Cessna 172 (0.45). And this was in spite of the CAPS system.
Cirrus decided that the reason for this was two-fold: pilot’s weren’t receiving enough training on CAPS, and they considered it an absolute last resort. So they began working with their training partners to provide Cirrus owners with more options to get trained on the system, including in simulators. The idea was to get them very familiar with the process of activating CAPS. In addition, they also worked with pilots to get them in the mindset of considering CAPS a part of their overall emergency training, and not just as a final, no options left, last resort. Some people even jokingly started using the mantra “Pull often, pull early.” It appears that Cirrus was correct with their guess, and their hard work started to pay off.
In 2011, there were sixteen fatal Cirrus accidents. That number dropped to ten in 2012, nine in 2013 and only 3 in 2014. At the same time, the number of fatal accidents was dropping, the number of CAPS deployments started to rise. With 12 deployments and 3 fatal accidents in 2014, this marked the first year where the number of deployments exceeded the number of fatal accidents. During the three year period from 2012 – 2014, the fatal accident rate has dropped to .84 for Cirrus, and in 2014, it dipped to .42, which places close to the top, safety wise
.
Accident rate aside, there is one other consideration: when CAPS is deployed, how effective is it? Well, as of March 1st, 2015, CAPS has been activated 65 times in Cirrus aircraft, and successfully deployed 52 of those times. In the cases where CAPS was successfully deployed, there were 105 survivors and only 1 fatality. There have been no fatalities or anomalies (with a single exception still being investigated) when CAPS has been deployed within the certified and specified speed and altitude parameters.
Based on everything I’d read and seen, CAPS appears to do its job well.
A Mechanic’s Perspective on the Cirrus SR22
Jim
A plastic airplane? I am an old school mechanic who loves aluminum. Consequently, in the beginning, my attitude toward these new composite airplanes was not so good. The first time I was asked to do an annual inspection on one, I was a little apprehensive because I had never looked at one before. Being unfamiliar seems to generally lead one more towards the negative than the positive, especially when the design is new or different and I fell into that mindset. But I was also curious: what all the talk was about? I wanted to poke around and see what I could see.
In general, that first look didn’t impress me all that much. It seemed very much like a home built composite aircraft once I got behind the upholstery and inside the wings, much like a Glasair. With my predetermined lack of enthusiasm for composites, it’s not much of a surprise that it didn’t make me want to go out and buy one. It wasn’t until a year later when I had the chance to fly one that my opinions started to change. As I sat back in the comfortable leather pilot’s seat and lightly held the control stick with my left hand, it seemed completely natural. The unobstructed view of the instrument panel and excellent view out the window were welcome and I immediately felt at home. The flight impressed me from a pilot’s perspective. It was smooth, stable and powerful, not to mention fun. The side stick with built in thumb control for the pitch and roll trim was ergonomically comfortable and offers the pilot some kind of macho feel during flight.
When I took off the headsets after that flight, my attitude was different. I had become friends with the airplane and could no longer hold a grudge against it. I decided to take a fresh approach the next time I would do an inspection on one. Now, don’t get me wrong, I am still a “metal guy” and prefer to work on traditional aluminum airplanes, but that is my own bias. I have come to see that Cirrus has developed an incredible aircraft and it does what it is designed to do very well. They are quite simple and easy to maintain. There is nothing unusual about the engines and they require the same upkeep and maintenance as any other Continental. Composites don’t rust or corrode. They are strong and flexible and I realize there are many benefits to them, but did I mention I really like aluminum?
On one occasion a few years ago, I had a Cirrus arrive at my shop for some maintenance and as the pilot pulled the aircraft near my hangar, he misjudged the wingtip clearance and struck a power box next to the taxi way. When the wingtip impacted the box, it seemed as if an explosion of fiberglass fragments and splintered bits flew all around the vicinity as the material flexed and broke. The damage seemed most apparent right out on the tip itself and my first thought was that we could easily obtain a new tip, put it on, and it would be no big deal. Such was not the case. Upon a closer inspection, we found cracks in the wing root fairings and adhesive bonds broken where cosmetic strips and fairings are attached. But the big problem was found when we removed the rear seats and pulled up the carpet around the structure in the aft cabin. The rear carry-through spar was broken from a compression fracture. As the wing flexed rearward, the relatively weak structure in this area was crushed. The aft wing attach area on the fuselage was also damaged, evidenced by visible white stress fractures around the fixture. I was shocked to see this much damage from what appeared to be a minimum impact. The aircraft was barely moving.
Had this been a Cessna, most likely the wing tip would have needed repair or replacement and it would be off flying again. I learned that these aircraft are very strong in ways they are designed to be strong but are very fragile when loads are imparted in ways they are not designed to receive. In order to repair the aircraft, we had to get engineered drawings from Cirrus, which were very expensive and took months to obtain. We were required to use composite resin and cloth material supplied by Cirrus that was temperamental and required very sensitive temperature control in order to cure properly. The whole process was time-consuming and tedious. This little incident ended up costing the owner over $20K. I was a little disappointed with Cirrus in the whole process because of the time involved in getting an approved method of repair, as well as the necessary parts to do the work. Moral of the story: Don’t damage your Cirrus.
Composites require different inspection criteria and training to understand and adequately maintain these aircraft. This could be a factor in my hesitations about it since I am still learning. I have found them to be very durable and strong in normal use and have come to have a good appreciation for it.
These airplanes have a few little quirks I am aware of that need periodic attention as well as awareness from the pilot. One example is the castering nose wheel steering mechanism. Differential braking is used by the pilot to steer the aircraft on the ground. The untrained and unaware pilot many times rides the brakes too much while taxiing the aircraft in an effort to have positive control. This leads to serious heat buildup and has even caused some wheel fires. Proper technique will alleviate this problem. High temperature O-rings should be installed in the brake calipers and the manufacturer recommends the replacement of these O-rings on a regular basis. They also put temperature indicators on the calipers to alert mechanics of previous overheat problems.
The design of the nose gear is subject to shimmy problems if the preload on the steering becomes too loose or tire balance is compromised. If these aircraft start to shimmy it becomes a violent event and often leads to cracked and broken wheel fairings. With periodic maintenance, this is not usually a problem.
The airplane is very electric and I have noticed several glitches with sensors, displays, and annunciators over the years. Usually, I get an avionics shop involved to help resolve these problems. They also have 2 standby emergency batteries in the aft fuselage that require replacement every other year.
Overall I think the maintenance on these aircraft is straight forward, although the parachutes and airbag seat belts require periodic parts replacement. These tasks must be accomplished by an authorized Cirrus shop. The 10-year chute replacements are starting to ramp up now because of the high number of aircraft produced in ’05 and I have noticed it takes a few weeks for the shops to obtain the parts for this invasive and expensive job.
I like the Cirrus. I think they are good looking, comfortable and fun to fly. But now I am going to rant a little bit. I think sometimes these airplanes promote a sense of security that may be inappropriate in the aviation world. My perceptions may not be exactly accurate but I think sometimes a lack of respect for the importance of training and the hazards of flying exists among Cirrus pilots. A new well-equipped Cirrus SR22 with turbos, TKS, glass cockpit, autopilot, airbags and that life-saving parachute can give flyers a sense of security that may be inappropriate. Don’t get me wrong, I hope the day I have an engine failure at night over the mountains, I have a parachute to save me. No doubt the chute saves lives. And I like the idea of having a powerful turbocharged engine so I can climb up above the weather. I also like a capable autopilot to reduce the workload when I am picking up ice looking for the TKS switch so that it will keep me going.
I’m really not trying to be too sarcastic but I do have a problem when pilots use these tools onboard the aircraft as a crutch for poor airmanship and bad judgment.
I have heard some of these folks use phrases like “I can always pull the chute if I get in real trouble” or “the autopilot is so easy to use and with TKS, it can handle a lot of weather”. These statements may be true but hazards of flying are still present, even in these super planes, and I hope people will not take anything for granted.
Autopilots require training and practice to use successfully. Instrument flying is a skill that should not be taken lightly. It requires good training and practice to be competent and safe. Even the parachute is a topic that must be discussed to know how, when and where to use it. Each of these systems should be studied and understood through and through.
I see busy business owners and executives purchase these aircraft but not budget the time and effort to become proficient. They often slack off on the higher levels of training after getting the private certificate, thinking they will work on it next month or next year when “things slow down”. If we are going to fly, lets make it a priority and make it a serious business. Technology is a great thing, but it requires effort, especially for some of us older guys to get good at. And, when it fails (which happens) you need good stick and rudder skills to safely get the aircraft home in one piece.
The Future of Cirrus Aircraft
Anders
So, what does the future hold for Cirrus and the Cirrus SR22? Sadly, I lost my Magic 8-Ball, so I’m unable to provide concrete answers. But if the past in any indication, Cirrus will continue to refine their existing aircraft, making them more powerful, more technologically capable, while always pushing continually toward making them safer. Oh, and they’ll be bringing us Cirrus Vision SF50 Jet soon. Very soon. Final flight testing concluded in December last year, and Cirrus has expressed confidence that certification for the SF50 will proceed on schedule, without need for modification. They’re so confident, in fact, that the first SF50 production aircraft began being assembled last month in April, in order to meet the current demand for 550 aircraft already on order. The future is looking bright for Cirrus. So bright, they might need to wear shades.
Footnotes:
1 – The VK in VK-30 stands for Viken-Klapmeier.
2 – It should be noted here that Viken’s wife, Sally, designed the VK-30’s flap system.
3 – The initial VK-30 prototype used parts from other production aircraft, including the nose gear from a Piper Cherokee and the main landing gear from a Lake LA-4.
4 – In mid-2011, aviation industry analyst Brian Foley revealed he was attempting to organize a group of US investors so they could make a counter offer to the Chinese buy-out, and keep Cirrus a US owned company. Though he said he received an “overwhelming response” from the US aviation community regarding keeping Cirrus in the US, he was never able to produce a counter offer.
5 – In 1995, the final VK-30 kits sold for $64,000, not including the cost of the engine.
6 – As of 2011, ten VK-30 aircraft are still registered with the FAA in the US.
7 – Air conditioning was also offered as an option for the SR22 Turbo G2, but this further reduced the useful load.
8 – Some pilots claim the glass panels and computers wear out quicker than traditional instruments and cost more in maintenance and repair. There’s also concern over losing access to all the instruments if a glass panel goes down, versus single instruments in the traditional arrangement where they aren’t all tied to one system.
9 – The goal of the CAPS system is the survival of the pilot and passengers, and not necessarily preventing damage to the aircraft. Cirrus assumed that most aircraft, after deploying CAPS and landing, would be damaged beyond repair. However, after looking over the aircraft involved in this first deployment, they found out it was actually not badly damaged, and they purchased it back, restored it, and used it as a demo plane.
Tags : aircraft, airplane, cirrus, cirrus SR22
Noel Wien: The Father of Alaskan Aviation
World’s Greatest Pilots: Jimmy Doolittle
Anders Clark
Anders Clark was introduced to aviation a few short years ago, and has developed an interest in aviation history and what the future of aviation will bring. A writer and editor, Anders enjoys researching and sharing the stories of aviation.

Generation 5 Cirrus SR22
Cirrus SR22 G5
Cirrus SR22 Generation 5
Cirrus calls the latest edition of its SR22 the Generation 5, which some customers have begun to refer to informally as the SR22 G5. There are a number of really big changes that make the model a strong upgrade, one that took clever design decisions to achieve.
How appealing is the new model? As of mid-March, Cirrus was sold out of Generation 5 SR22 production slots through July. It is shaping up, Cirrus vice president of sales and marketing Todd Simmons told me, to be the best year for Cirrus in many moons, and it is thanks to the G5. Customers are eating it up.
Article Continues Below:
Aerobatics with Matt Chapman at Oshkosh 2016
Flying magazine met up with airshow performer Matt Chapman in Oshkosh for ...
Why the love fest? Easy. Through a series of smart and complicated engineering decisions, Cirrus found a way to increase the gross weight of the airplane by 200 pounds, to 3,600 pounds.
In order to accomplish this, Cirrus had to do a number of things to the airplane that were complex, expensive and time-consuming. (Do those three things ever not go hand in hand when it comes to certification?) The company’s goal was to add some capabilities to the SR22 that owners have been asking for from day one. More on that in a bit.
Now, 200 pounds is a lot of weight increase for a light airplane, and it’s a number that resonates with pilots, as it is the ballpark weight we use for an FAA-standard passenger. (Your standard passenger may vary.) So, all other things being equal, you can add another passenger to today’s SR22 and go flying. While the numbers differ on differently equipped models because their rough empty weights are dissimilar, the bottom line is that every SR22 gets a sizable increase in useful load and full fuel payload.
The standard equipped nonturbo, non-FIKI, non-A/C SR22 is the best-case example, as it’s the lightest SR22 that Cirrus offers. With that model, you get a useful load of 1,340 pounds and a full-fuel payload of 788 pounds, which means you can take four 190-pound occupants, 25 pounds of bags and full fuel — 92 gallons — enough to fly no wind with reserves and then some from Portland (KPDX) to Santa Monica (KSMO). Leave out 10 gallons of fuel, and you can bump up the bags to nearly 100 pounds and you’re good to go from Atlanta to West Palm Beach, Florida.
For the more commonly ordered SR22s, with turbocharging, A/C and approved de-ice package, it’s still a big win. You can fly with three 180-pound occupants and full fuel, or load enough 100LL for a three-hour flight with reserves and fly with four 180-pounders. There are no other four-seaters in production that we know of that come close to these numbers.
How Cirrus arrived at a 200-pound weight increase is a complex tale. Of course, the company started by realizing that it had to beef up the spar, and interestingly, Cirrus says this aspect was relatively straightforward. Cirrus engineers added a few layers of composites and did the necessary analysis. The gear had previously been strengthened to handle the higher weight, so that work was already done (which also tells you something about how far in advance Cirrus plans its product upgrades). Had they left it at that, though, the 200-pound strength increase would have been lost to weight added on the spar and elsewhere to support the greater structure (the Catch-22 of every gross-weight-increase project). For the first time, there’s also a zero fuel weight, a figure that’s new to most piston-single drivers but common to jet pilots. The restriction in the G5 is a zero fuel weight of 3,400 pounds, which essentially means 3,400 pounds of nonfuel weight; so you need 200 pounds of fuel at max weight.
To counteract the hit they knew they would take in terms of a beefier structure (and one other big item), they went to work lightening the airplane. Cirrus engineers redid the structure of the rear seats to save 10 pounds; they shaved some weight with the oleo strut (actually new on an earlier SR22 model); they improved manufacturing processes throughout to cut an unspecified amount of weight; and they used new interior materials to cut some weight as well. They were also able to remove around eight pounds of ballast from the tail, which had been added on a previous model in order to keep the CG more tolerant of front-seat-only loading scenarios.
The one place they took a hit was with the parachute, which is all-new. Because the airplane weighs as much as 200 pounds more, the parachute has to lower the airplane with the same dynamic forces on touchdown, so the chute has to be bigger: It went from 55 feet in diameter to 65 feet in diameter. An added benefit of the larger chute is that the airplane will now touch down at lighter weights at very low speeds. While the handle, cables and system of channeled webbing that make up the extraction system are the same, the rocket had to be bigger because the chute itself is bigger and heavier and needed more power to fire it. The new rocket is longer and more powerful. Cirrus also went with a new firing system, which makes use of solid-state ignition instead of an incendiary device, as on the former models.
Other Weighty Gains
Another big plus with the G5 is the improvement in two critical airspeeds. The first of those is max flap extension, which increases from a too-low 119 knots for the first-notch to a fantastic 150 knots. The second notch of flaps, formerly set at a max deployment speed of 104 knots, has climbed a modest 6 knots to 110 knots but has gained an additional 3.5 degrees of extension in order to keep landing speeds low. The strengthening of the main spar helped provide the structure needed for the increase, as did improvements to the flap hinge and hinge attach points.
The speed for the deployment of the parachute has also increased, from 133 to 140 knots, which adds to the margin of safety for deployments.
There are some trade-offs to the weight increase and all that went into it. Liftoff speeds (which are calculated at max weight, as most specifications are) have increased from about 72 knots indicated to about 80 knots, increasing takeoff run but only by about 60 feet. The stall speed increased from 58 knots to 60 knots, and the best rate and angle of climb both increased marginally. Landing performance figures are virtually identical to those of previous SR22s.
In terms of climb and cruise performance, the G5 airplane will climb a bit less quickly (same wing, same power plant, higher weight), taking around eight instead of seven minutes to get to 8,000 feet at max weight. Likewise, the range decreases by about 50 nautical miles on average (of course, range figures are all dependent on weight, winds, equipment and other conditions).
Cruise speeds theoretically will be affected too, though in my tests (and according to the pilots I know who’ve flown the G5), it was hard to see any differences. At 9,000 feet in the turbo (with FIKI, which cuts a couple of knots off the top end), I was seeing 175 knots true. At 24,000 feet, a friend reported seeing 205 knots. The new model will burn slightly more fuel for the same performance.
The new model also rolls into the standard package a number of features that were recently introduced on other models. The Garmin GFC 700 autopilot (you thought it was standard, didn’t you?) now is in fact standard. Also, the remarkably accurate fuel sender units are there too. They are so accurate, they are used to send CAS messages apprising the pilot of any coming fuel imbalance; at eight gallons of imbalance, you get an alert; at 10 gallons, you get a caution; and at 12 gallons and beyond, it’s a master warning. The fifth seat (which Cirrus calls 60/40 Flex Seating) saw universal adoption by buyers over the past year. It is now in every SR22 (SR20s as well, actually). ADS-B is also standard.
The lineman at my airport spotted one other new feature, the redesigned wheel pants. As far as I could tell, they are completely unrelated to the gross weight increase, and they don’t seem to affect the airplane’s performance either. But they do have access doors for the inflator valve, which explains why the line guy spotted them right away. On older SR22s, it’s a pain to inflate the tires.
G5 In Flight
I had an extended opportunity to fly the Vision Inspired Generation 5 SR22 over the course of two weeks, flying it on cross-country trips, on local hops and even on training flights.
The creature comforts of the model are remarkable. The seats are the most comfortable yet (though they could use another recline notch between the “bolt straight” and “kicking back” settings). The soundproofing and fit and finish are better than ever too. The doors on the G5 (an issue with some older airplanes) worked like a charm, and the stylish tone of the interior hits the perfect note.
Even though the SR22 feels very familiar to me — I fly an SR22 G3 model regularly — there was something about the G5 that was more solid than any SR22 I’d previously flown.
On my heaviest flight, we were a few hundred pounds under gross with full fuel, but I still kept it on the ground for the additional few knots the book says is needed at gross weight just to get a feel for it. My conclusion is that it’s really not needed for rotation, as the airplane was ready to fly not at 80 knots but at 70. For clearing obstacles, use book values.
I had a hard time discerning differences in performance between the G5 and the G3 I normally fly (for the record, there is no G4, for no other reason than it wasn’t as mellifluous-sounding a designation as G5 is). Climb was strong, around 1,200 fpm on the cool morning that I headed down to the Texas Gulf coast for the photo shoot. If there’s a difference, and physics dictate there must be, then it is surely slight. Likewise, in cruise it felt like any G3 I’ve flown: nice, comfortable and fast.
It was in arrival and approach that the airplane showed its great new powers. With a first-notch speed of 119 knots in previous generations of SR22s, you needed to be clever at times to get down to approach speeds. Start the approach a little too fast, and you’ll be struggling to both descend on the glide path and keep the speed below the flap limit. With the new settings, you can throw in the first notch of flaps at 150 knots, which is a huge deal to Cirrus pilots. We’ve all talked about how nice speed brakes would be on this airplane in the past. With the new flaps, there is no need — none, nada, zilch. You can now tailor your approach speeds to fit the traffic, the procedure and the needs of ATC.
Landing the SR22 G5 is different than in previous models, and there are a couple of reasons for that. For one, it has an extra bit of travel on the second notch of flaps, so you tend to sink nicely even while carrying a little power. The other thing is that the airplane is heavier, so with the power being equal, you are going to sink just a bit more. If any of that sounds bad, it’s not. Actually, it’s great. The G5 is by far the best-landing SR22 ever. And it is the best-flying SR22 by a long shot.
|
Vision Inspiration
When Cirrus began showing its SF50 Vision jet around with a new iridescent blue paint scheme, it received a warm welcome from potential customers. So Cirrus decided to create a marketing tie-in with the soon-to-be-announced Generation 5 SR22, allowing buyers of the G5 airplane to get a position on a jet for $1.19 million instead of $1.96 million, or to allow jet position holders to pick up a G5 SR22 with guaranteed brokerage when they take delivery of their jet in a few years.
Cirrus called the special-edition SR22 the “Vision Inspired” model, which I flew and photographed for this story. In addition to the cool paint scheme, the Vision Inspired SR22 comes with a package of special features, including black baffling, stainless-steel cam locks, carbon-inspired interior with suede-look headliner and side panels and yoke covers, and Vision Inspired badging. The airplane also comes with three years of tail-to-spinner maintenance, the sat/comm/data package and air conditioning. The cost of the Vision Inspired SR22 is an eye-popping $829,000. Standard SR22T (turbo) models start at $569,900 for the well-equipped base model and go up to $724,900 for the decked-out GTS model.
Cirrus has delivered more than 5,300 airplanes to date, and the SR22 G5, with its 200-pound increase in gross weight, greatly improved flaps, enviable performance and features list, is the best one yet. While not everyone will be able to fork over the dough for the latest model, many pilots are jumping at the chance to do just that; a few are taking the opportunity to get a Vision Inspired airplane and a spot in line for a jet to match.

Cirrus SR22
Cirrus SR22
Overview
Performance Summary
Specifications
Unless you are brand-new to general aviation or have been under a rock for the past decade, you know by now the Cirrus Design story. Wisconsin brothers Dale and Alan Klapmeier started building kit airplanes, but soon recognized that the real market was for a new-generation mainstream-certificated airplane. In 1995, they announced, with much fanfare, that they were going to produce just such an airplane. The airframe would be composite and incorporate the latest thinking in aerodynamics and survivability. Unusual doors that lift upward and forward (actually, in the mock-up they were sliding doors like your minivan has), opening to a wide and comfortable cabin. The plan was to incorporate the latest avionics and engine management systems to reduce pilot workload and improve situational awareness. And deliver it all at a higher "value" than was then available in the market.
Safety
At first, Cirrus planned to offer a unique rocket-powered parachute as an option. Later, the Klapmeiers decided that the parachute would be standard equipment. The parachute is designed to lower the aircraft to the ground in such a way that those inside would survive. However, the 1,800-foot-per-minute descent rate beneath the deployed parachute will most likely damage or destroy the aircraft upon impact in the worst case scenario. Still, as a last-ditch effort in the event of a loss of control, it's not a bad safety net. “In 2002, the Cirrus Airframe Parachute System™ made aviation history with the first safe landing by a private pilot after deploying the parachute.” (Cirrus Design Corp.)
Development and certification of the parachute system took many months and many tests. Eventually, the system, dubbed CAPS, for Cirrus Airframe Parachute System, earned FAA approval.
Hidden in an area in the aft fuselage, the parachute and its rocket, along with the extra structure to accommodate the system, weigh less than 80 pounds. A pull forward and down on the handle ignites the rocket motor and propels it out through the skin of the aircraft, pulling the parachute with it. Wide straps buried just below the composite exterior skin of the fuselage, running beneath the door openings, are ripped free by the force. In the end, the fuselage is suspended by the straps, which are attached to the firewall and the aft cabin. The system requires almost no maintenance, just an inspection and repacking of the chute every 10 years and perhaps replacement of the rocket motor.
The Klapmeiers believe that the aircrafts’ avionics and navigation systems will improve situational awareness. On Cirrus Aircraft, the Avidyne Multi Function Display has always been standard. Later models are equipped with the Avidyne Entegra Integrated Flight Deck, providing the pilot with a new level of situational awareness and safety.
SR22- Handling and Performance
To go faster or farther than a similarly shaped airplane, yours must either be smaller or it must have more power. Period. With that in mind, it is no wonder that the Cirrus SR22, with its 310-horsepower engine, outperforms its 200-hp little brother, the SR20, in every way. Horsepower is an amazing thing, and in this case it transforms the perky Cirrus into a real get-up-and-go traveling machine.
At cruise settings, the horsepower also makes a difference. The increase from the SR20's 160-knot cruise speed at 75-percent power to the SR22's 181 knots is impressive, but you might ask whether the additional fuel burn is worth it. If your budget can stand it, yes, it is worth it for those who plan to travel long distances. Even if you're not flying in the shadow of the Rocky Mountains, the excess horsepower available for improved climb is something you can use to your advantage on every flight. Getting to altitude more quickly and to higher altitudes altogether allow you to fly more efficiently.
The SR22 also carries a longer wing, about three feet longer. The greater span improves the climb rate, decreases stall speed, and gives the SR22 really nice landing characteristics. I found the SR22 to be easier to land than the SR20, partly because it seems more stable on approach, but mostly because the larger wing provides more opportunity in ground effect to finesse the landing.
The SR22 maintains the unusual leading-edge cuff on the outboard sections of the wing that debuted on the SR20. The cuff helps direct the airflow over the ailerons at high angles of attack, allowing the pilot to maintain roll control with the ailerons at very slow speeds. The devices make the Cirrus airplanes docile in stalls and virtually impossible to spin. Cirrus test flights show that both airplanes behave conventionally in spins, but, like most high-performance airplanes, neither is approved for the maneuver.
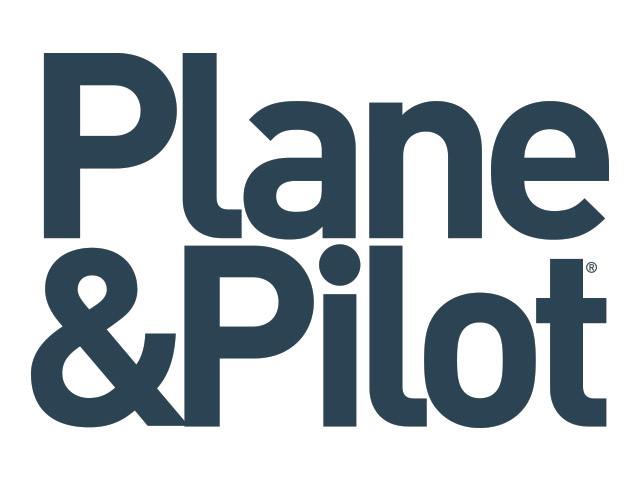
Cirrus SR22 GTS: The Perfect Plane?
Rated at a conservative 315 hp, the Continental TSIO-550-K factory-turbocharged engine is limited at 2,500 rpm, giving the engine a smoother feel and making the cabin even quieter while reducing its noise footprint. Single-lever performance adjustment means there's no propeller control.
Some aircraft change the game. Looking back, designs like the Cessna 172, the Beechcraft Bonanza, Piper Cub, Mooney M20 and a handful of others have changed the way aviators—and outsiders—perceive general aviation. These aircraft led GA in a new direction the minute they were introduced. Since 1994, when a nascent company named "Cirrus Design" unveiled a revolutionary airplane called the SR20, that list has grown to include the SR22 and SR22T. These aircraft have turned GA on its side.
That's not to say everybody has embraced the Cirrus design aesthetic. Any fair review of an aircraft like the newest SR22T has to include both sides of the like/dislike argument. What's interesting is that this Cirrus has sparked so passionate a reaction. The company's dogged pursuit of innovation in safety is equal only to its revolutionary advances in design, construction and performance, and it's these advances that have fueled the passionate arguments.
I didn't want to like the newest SR22. Standing firmly in the stick-and-rudder-and-tailwheel camp, my instincts told me the Cirrus couldn't be a "real" airplane. The technology was surely dumbing down the aviating experience, and only "airplane drivers" (and not real pilots) would like such an airplane. I wondered what all the hoopla was about.
Cross-Country Adventure
Already one of the most advanced glass-panel systems, the 2012 Garmin Perspective adds integrated satellite phone, global weather and SMS text messaging, along with the new GMA 350 audio panel with 3D audio.
That was before the brand-new SR22 charmed me like Audrey Hepburn riding her Vespa scooter in that scene from Roman Holiday. The Cirrus seduced me over the course of a San Francisco adventure, slowly transforming each of my objections into a chin-rubbing understanding of why this airplane deserves a place right next to that venerable Cub.
Along with me for this mini odyssey was Cirrus' own Matt Bergwall and Plane & Pilot editor Jessica Ambats. Both are experienced Cirrus pilots, so I felt out of place as they offered the left seat to me. Our flight would take us from John Wayne Airport in Southern California up to the Bay Area for a photo session around the Golden Gate Bridge. The next day, we would return home. My biplane-honed skills would be fairly useless on this flight, and I was rusty, to boot. I offered a quick plea to the aviation gods to anoint me with a decent performance as I sat down on the buttery-leather seats and took in the new-plane smell.
By now everyone has seen a Cirrus, and the company recently celebrated their 5,000th airplane. One of the most impressive features of the SR22 is the enormous cabin. When Cirrus conceived the airplane, they started with a sphere instead of a rectangle, so the interior vibe is completely different from, say, a Mooney, where the rear cabin can be claustrophobic. I'm not a big guy, of course, but the rear space is positively cavernous. One major enhancement to the 2012 SR22T is the three-seat rear space, allowing three people in back and two up front. In truth, three full-size adults would find it overly cozy, but a couple with a child or three average teenagers would be comfortable. The new LATCH child- restraint system also has been added in 2012.
The year 2012 brings a major redesign of the rear cabin. Enhancements include a transition to over-the-shoulder seat belts, 60/40-split reclining rear seats, re-engineered side bolsters to increase cabin area, an additional third seat and LATCH child-safety restraints. The redesign saves 10 pounds over existing models.
Speaking of seats, another new feature for this year is the reclining and 60/40-split seat option in the back. The FlexSeating allows for skis, fishing poles, golf clubs and the like, but it was the reclining rear seats that won me over. Besides giving the SR22T ample cargo space for hauling large items by folding both seats (or just one seat) flat, the gaping cabin combined with the reclining seats allow a lounger-like sleeping position.
With the weather providing nothing but blue skies and good visibility across the entire nation that day, we began our trek, and I settled in with the SR22. The Garmin Perspective display is so darned pretty to look at, and its capabilities are nothing short of mind-blowing—transforming the five-seat Cirrus into much more than a mini airliner. From start-up to shutdown, the richness of information provided by the Perspective system is deservedly an enormous part of the Cirrus' appeal and success.
Immediately on takeoff, as we winged over the Pacific Ocean and its Gold Coast beaches, I was struck by how intuitive everything in the Cirrus is. I also noticed how a large part of the mission of the SR22 is to make the job of piloting easier. For example, our takeoff flap setting was "50%," the first detent on the simple switch. How many degrees 50% translates to isn't apparent, and it's these kinds of contradictions that have some old-timers saying the airplane oversimplifies flying. But understanding the logic of the non-complicated system deflates such arguments. The settings could be in Russian, and all that counts is the proper procedure for this airplane. Sometimes, I think many of us are enamored with flying's complexity; it's a sort of a mysterious veil to outsiders. Cirrus is trying to invite outsiders into aviation by removing that veil, and then everybody wins.
I had decided to hand-fly for the first 30 minutes or so to get the feel of the airplane. It's no wispy featherweight. The Cirrus is maneuverable, but it feels somewhat like the bigger Cessnas—especially in the elevator. The controls are balanced, but the side stick takes some getting used to if you're new to it. It was strange for me not to have a stick or yoke in front, though I liked the additional space that the side stick provides.
Another example of Cirrus' commitment to make flying simpler is leaning the SR22T's engine. The avionics system, turbocharger and MFD display work together to eliminate the complexity of current methods. Just bring the throttle back and match a little blue line on the engine display with an indicator, and you're flying at lean-of-peak performance for a given condition. Not knowing the technical minutiae took nothing away from the aviating experience. Simple is beautiful on a long trip.
There, above the breadbasket valley of California, my epiphany about the Cirrus began to take form. We were riding at 8,500 feet along a lower part of the Sierra Nevada mountains that seemed to stretch for eons. At our true airspeed of 175 knots, the golden hue of the spring crops nestled against the jade hills reflected in the ample windscreen, we set the autopilot, and Bergwall began to show me more of the SR22T's hidden charms.
The Enhanced Vision System uses sensors to offer a hyper-realistic view in low-visibility conditions, increasing situational awareness.
In 2012, gee-whiz features that Cirrus aficionados already know well were added: 12-inch PFD and MFD screens, Cirrus' Synthetic Vision and Enhanced Vision System (EVS) for use at night or in limited visibility, Electronic Stability and Protection (ESP), Certification for Flight Into Known Icing (FIKI), Hypoxia check/Automated Descent Mode, Air Conditioning, yaw damper, and a five year spinner-to-tail warranty.
Our 2012 GTS model also had the Garmin GMA 350 audio panel with "3D audio," which turned out to be a surprise in coolness. The unit separates audio signals into two distinct sides of your headset. For example, you could be monitoring ATIS on one frequency and listening to Approach on another. One channel goes to each ear, and the unit processes the signal, so the effect is unlike anything you've experienced before. The resulting communication is unexpectedly distinct and easy to understand, even with both sides transmitting at the same time.
Suspended there, over terrain that looked like giant paper grocery bags crumpled everywhere, the talk turned to the Cirrus' famous Cirrus Aircraft Parachute System (CAPS).
"If you lost an engine here, would you pull the chute?" we asked Cirrus' Bergwall. After a few seconds he responded, "Definitely, yes." The ground below was teeming with tall pines and not a single stretch of open or otherwise flat land. The best you could do here would be to stall it into the trees. Maybe a broken back or leg would be the worst of it; maybe not. But the Cirrus opens a world of chances for you with the 'chute. Of course, it's not a substitute for proper flight planning nor an excuse for ignoring weather, but CAPS is unequivocally a lifesaver. "It has been deployed 33 times," noted Bergwall. "And when pulled within the design parameters, it saves lives."
The Perspective Global Connect system includes an integrated satellite telephone, text messaging and worldwide weather.
Another brilliant option for 2012 is the $14,900 "Perspective Global Connect," which brings an integrated satellite phone to the Cirrus' cabin, along with SMS text messaging from the MFD and worldwide weather through a subscription service. We tested the sat phone by calling Michigan while we hummed along nearly two miles above Paso Robles and well out of reach of any cell-phone reception. Imagine the possibilities of flying over Central or South America; the remote deserts of Africa or even the Bahamas, and being able to call or text anybody around the globe or retrieve weather from locations not served by XM.
The descent and landing into San Carlos were easy events, with the SR22 trucking down final in a flat approach and flare. A good dose of practice would get me comfortable, though the side stick still felt a bit alien. The capabilities of the Garmin Perspective go without much comment here, other than it can do just about anything, and the Cirrus' FIKI certification and supplemental oxygen combined with the Perspective mean there isn't much the airplane can't handle.
Once the SR22T was prettified for her photo session, we launched for the Golden Gate Bridge with the sun sitting low over our shoulders. Against the backdrop of San Francisco and her radiant bay, the SR22T looked handsome. The year 2012 brings two color schemes: "Carbon" and "Platinum." The two appointments are targeted at different audiences, with "Carbon" being a more aggressive look, featuring carbon-fiber interior accents, two-tone paint, leather seats and a flat-black spinner. "Platinum" is the conservative (the marketing folks call it "distinguished") motif, with single-color seats, platinum accents and a polished spinner.
Cirrus feels good to non-aviation passengers. The interior is sumptuous and very un-aviation like, which reduces the shock that non-aviators feel sitting in the back of most GA airplanes. It's yet another thing Cirrus has done right, and another reason these airplanes sell. Between the air conditioning, big cabin, customizable audio feeds, and three-position reclining seats, flying in an SR22 is downright decadent. I tested that myself on the way back home as Ambats took the left seat and I spread out in the rear cabin, reclined with a book and enjoyed the irony of Carly Simon singing her 1977 hit, "Nobody Does it Better."
Ok, so the Cirrus SR22T isn't a perfect airplane—there's no such thing—but my epiphany stands that this is a supernal cross-country machine when you just want to enjoy the ride. It's true that if I want a pure, stick-and-rudder, wind-in-the-hair, don't-screw-up-the-landing, aviating experience, I'll take out the biplane (or drop the window on a Cub or Husky). But if I want to go to a vacation destination and arrive relaxed, or if I want to bring non-flying friends on an enjoyable flight that beats the airlines in almost every way, I'll grab the Cirrus keys every time.

We Fly: 2016 Cirrus SR22T
When the Cirrus rep handed me the keys to a brand new 2016 SR22T for an evaluation flight, I could only nod my head and smile at one of the new features in the latest iteration of this sports car with wings: a key fob with remote keyless entry. Press the button just like you would standing outside your Mercedes or Porsche and the doors to the plane automatically unlock. Shouldn’t all new planes have this feature, I thought?
That’s not all. The latest SR series models come with a full complement of luxury features, including Bluetooth calling and music connectivity, wireless flight plan transfer from an iPad to the Garmin Perspective avionics, and control of the XM radio from your smartphone.
Article Continues Below:
Aerobatics with Matt Chapman at Oshkosh 2016
Flying magazine met up with airshow performer Matt Chapman in Oshkosh for ...
New 2016 exteriors incorporate exclusive Sherwin-Williams colors in three premium design “collections:” Carbon, Platinum and Rhodium. Cirrus also offers an Xi personalization package with an endless array of exterior and interior color choices. The five-passenger interior, meanwhile, is on par with any luxury automobile sold today.
And well it should be. A fully loaded 2016 SR22T has crossed over the $900,000 price threshold for the first time. That will make some readers gasp, I’m sure, but let’s face it: If you’re in the market for one, money isn’t your major concern. In fact, the day of my evaluation flight a new owner was scheduled to arrive on his Gulfstream private jet to take delivery of his SR22 and fly it home.
If you think the price tag is simply too steep for a light piston single, we have news for you: Cirrus produces the best selling piston airplane in the world. The company could actually sell more but they’ve capped production of piston models at around 300 a year as preparations are made at the factory in Duluth, Minnesota, to start building the Cirrus Jet. Pre-orders of that airplane have been brisk, to say the least, as SR22 owners dream of moving up to a Mach readout.
As for my flight in the 2016 SR22, it was quite simply unlike any other GA airplane I’ve flown. And I’ve flown some nice airplanes. This new SR22 is the best yet. If you can afford one, and you can get your order in before they’re sold out, you owe it to yourself to schedule a test flight. Look for more details in an upcoming issue of Flying.

Cirrus SR22T: More of a good thing, Useful-load increase amps Cirrus SR22 utility
We put the biggest “what’s new” about the new Generation 5 Cirrus SR22T to work right from the start in our ultimate cross-country trek—the 200-pound increase in maximum takeoff weight. With the increase in MTOW to 3,600 pounds, a normally aspirated SR22 can now actually carry four adults and full fuel.
Furthermore, the now-standard three-abreast back seat means a pilot has even more versatility to swap fuel for useful load to potentially carry five souls.
As a cold March rain drummed the steel hangar roof in Frederick, Maryland, Matt Bergwall, Cirrus product marketing manager, skeptically studied the pile of luggage and gear next to N551JW. AOPA Live Executive Producer Warren Morningstar produced a small portable scale and began weighing each of his many bags of video gear. With the 60-part of the 60/40 split back seat folded down, I loaded the bags through the SR22’s generously sized baggage door. Tripod cases protruding across the folded back seat, camera bags carefully nestled on top, and other smaller bags and suitcases tucked into every corner. With the gear and a load of fuel to carry us all the way to Illinois, we bumped 3,600 pounds on the scale.
Mount Vernon, Illinois, would be our first stop on a headwind-hindered westward trip from Frederick to Santa Fe, New Mexico. On one of those no-wind days that live only inside pilot operating handbooks, we could have made the 1,360-nm crossing with only one fuel stop in just 6.8 flight hours up in the flight levels, where the 22T can crank out more than 200 knots true airspeed.
But in the realities of pre-springtime flying, ever increasing headwinds at higher altitudes forced us to stay below 10,000 feet almost the entire trip. Even then, an average of 25- to 40-knot headwinds all day long forced two stops and led to some 10 hours of flying. But with big windows to watch the continent scroll by, friends to share pilot tales, and XM stereo through the headsets, what’s not to like about a nice day of flying?
And a nice day it was, once we left the rainy Appalachians behind us. Despite the wind we enjoyed a smooth ride and clear skies for the rest of the trip that had us making a second stop in Pratt, Kansas, just downwind of the cattle yards. We climbed to 12,000 feet and dog-legged a bit south before hanging a right just past Las Vegas, New Mexico, to turn into the valley that is home to Santa Fe. The setting sun brilliantly back-lit the chocolate brown mountains just west of the airport.
While we had spent most of the day at 8,000 to 10,000 feet, the Earth had come up to meet us, meaning a short descent to Santa Fe. Across the bottom of the Garmin Perspective’s multifunction display, the horizontal contour display showed the rising terrain. Garmin’s active terrain warning system painted peaks near or higher than our altitude yellow and red. The high-resolution synthetic vision technology (SVT) provided further clarity about the nearby features. Need yet more comfort? We turned on the ship’s MaxViz infrared camera, which clearly showed the mountains in real time even as darkness spread across the valley. The camera is housed on the bottom of the left wing.
Our ride this day was not your average Generation 5 SR22T. N551JW is a Vision Inspired model, which gives an aesthetic and badging nod to the Cirrus Vision single-engine jet in development. Those buying the Vision Inspired package get a price break on their jet order as well as an SR22T with a host of unique features, such as tri-color paint and honeycomb exterior decal that replicates the look of the carbon-fiber structure prevalent on the jet.
Among the other exterior details are black baffling, sterling spinner, and stainless steel cowling Camlocs. Inside, the model is replete with nuances, such as a Vision Inspired door threshold badge and another such badge below the audio panel.
Spec Sheet
Cirrus SR22T
Base price: $569,900
SR22T GTS as tested: $829,900
Specifications
Powerplant | Continental TSIO-550-K, 315 hp
Recommended TBO | 2,000 hr
Propeller | Hartzell, composite three-blade, 78 in
Length | 26 ft
Height | 8 ft 11 in
Wingspan | 38 ft 4 in
Wing area | 144.9 sq ft
Wing loading | 24.8 lb/sq ft
Power loading | 11.4 lb/hp
Seats | 5
Cabin length | 10 ft 10 in
Cabin width | 4 ft 1 in
Cabin height | 4 ft 2 in
Empty weight | 2,340 lb
Empty weight, as tested | 2,485 lb
Maximum gross weight | 3,600 lb
Useful load | 1,260 lb
Useful load, as tested | 1,115 lb
Payload w/full fuel | 708 lb
Payload w/full fuel, as tested | 563 lb
Maximum takeoff weight | 3,600 lb
Maximum landing weight | 3,600 lb
Zero fuel weight | 3,400 lb
Fuel capacity, std | 94.5 gal (92 gal usable)
567 lb (552 lb usable)
Oil capacity | 8 qt
Baggage capacity | 130 lb, 32 cu ft
Performance
Takeoff distance, ground roll | 1,517 ft
Takeoff distance over 50-ft obstacle | 2,080 ft
Max demonstrated crosswind component | 21 kt
Rate of climb, sea level | 1,203 fpm
Cruise speed/endurance w/45-min rsv, std fuel (fuel consumption)
@ 85% power, best economy | 213 kt/3.8 hr
25,000 ft | (110 pph/18.3 gph)
@ 55% power, best economy | 171 kt/5.5 hr
25,000 ft | (76.2 pph/12.7 gph)
Max operating altitude | 25,000 ft
Landing distance over 50-ft obstacle | 2,535 ft
Landing distance, ground roll | 1,178 ft
Limiting and Recommended Airspeeds
VX (best angle of climb) | 88 KIAS
VY (best rate of climb) | 103 KIAS
VO (operating maneuvering) | 140 KIAS
VPD (Max demonstrated parachute deployment) | 140 KIAS
VFE (max flap extended) | 150 KIAS
VNO (max structural cruising) at 25,000 ft | 150 KIAS
VNO (max structural cruising) up to 17,500 ft | 176 KIAS
VNE (never exceed) at 25,000 ft | 175 KIAS
VNE (never exceed) up to 17,500 ft | 205 KIAS
VS1 (stall, clean) | 74 KIAS
VSO (stall, in landing configuration) | 60 KIAS
For more information
Contact Cirrus Aircraft, 4515 Taylor Circle, Duluth, Minnesota 55811; 218-529-7292; www.cirrusaircraft.com
All specifications are based on manufacturer’s calculations. All performance figures are based on standard day, standard atmosphere, sea level, gross weight conditions unless otherwise noted.
Extra
Puts out 36.5 inches of manifold pressure at takeoff, burning about 36 gph.
The all-black leather seats incorporate inserts and detailed panels that mimic the carbon-fiber theme. Similarly, carbon fiber touches adorn the panel. Cabin light housings and air vents come in brushed aluminum. The Vision Inspired package can be added to a well-stocked SR22T, which typically includes air conditioning and a certified anti-icing system along with the infrared camera and the Global Connect Iridium satellite phone for making calls and sending texts. Global Connect also allows for datalink weather for customers outside the range of the Sirius-XM satellite constellation.
Meanwhile, the Generation 5 upgrades focus mostly on changes necessary to accommodate the higher MTOW. In case you thought you missed something, there was no Generation 4 Cirrus. Generations 2 and 3 were upgrades and manufacturing improvements over earlier models. Bergwall confessed, rather sheepishly, that Generation 5 just sounded better from a marketing standpoint than 4; and, he said, 4 is an unlucky number in some countries.
Tom Arnold, vice president of sales, described the Generation 5 project as a one-year program that took 25 months. Bergwall concurred, saying that certifying a new, larger parachute to accommodate the higher weight set the project back nearly a year. The 65-foot-diameter parachute (earlier ones are 55 feet) is made of a new and lighter material, but still weighs more than the old one. But the larger diameter allows the heavier airplane to settle to the ground at the same rate as a 3,400-pound model. A new electrically actuated rocket igniter blasts the chute from the airframe when the pilot pulls the still mechanical handle over head. Independent electrical connections to the ship’s main and emergency batteries assure a continuous supply of power. The new system replaces the 1990s technology in the old models.
To meet the demanding need to have a single-engine stall speed below 61 knots, Cirrus increased the flap travel by 1.5 degrees on the Generation 5 airplanes, according to Bergwall. The strengthened flap hinges provide a much bigger benefit though—initial flap deployment speed jumps from a modest 119 knots indicated airspeed to a much more useful 150 KIAS. The change gives the pilot a very useful tool for managing descents in the slippery airplane and essentially eliminates the need for speed brakes. Deployment of the second notch of flaps can now occur at 110 KIAS, up from 100.
And, speaking of small things that make a big difference, Bergwall reports that while the 200-pound MTOW boost is a big deal with customers, the most prevalent comment from current Cirrus owners is accolades for the redesign of the wheel fairings to incorporate a small hinged door so you can easily check tire pressure—a long-requested feature. Structurally, many parts of the airplane required changes to accommodate the extra weight. For example, the one-piece carbon fiber spar was strengthened, as was the landing gear.
The highly integrated Cirrus Perspective by Garmin avionics suite now incorporates the formerly mechanical fuel gauges; the old round gauges on the center pedestal are gone. New digital fuel senders in the tanks provide highly accurate fuel quantity readings for display on the MFD, a much needed upgrade from earlier models. The accurate fuel readings make it easier to trade some of those 92 gallons of fuel for payload.
With the fuel system change, the level of systems integration is remarkable. Perspective manages all of the airplane systems, including oxygen distribution
and quantity reporting; TKS anti-icing fluid quantity and tank balancing—even alerting the pilot to high carbon monoxide levels and unbalanced fuel levels.
Flying it could hardly be simpler. An automatic wastegate controller manages the turbocharger, allowing the pilot to push the throttle full forward and leave it there, and the mixture full rich, until leveling for cruise. Then the pilot simply pulls the power back to about 85 percent as shown on the MFD. Slide the mixture control back and watch as the fuel flow indicator matches up with a blue hash mark on the fuel flow gauge.
You’re done, set for lean of peak economy cruise. No cowl flaps to close, no tedious charts to consult, no intense juggling of fuel flow against cylinder head or exhaust gas temperatures. In our case, at 8,000 to 10,000 feet at about 85 percent power and burning about 18 gph, we saw true airspeeds of about 177 to 180 knots on a slightly colder than standard day. The POH, which contains only FAA certified data, says at 25,000 feet it will do 213 KTAS on about the same fuel.
Meanwhile, the GFC 700 flight control system guides the airplane with a deft digital hand, managing every phase of flight until just short of touchdown. The SRs like to land a little flat, more like a jet, which will help those transitioning up to the Vision.
I remembered that attitude and slipped the airplane gracefully onto the runway at Mount Vernon. Forty-eight hours later when we had moved from Santa Fe to our final destination at South Valley Regional Airport near Salt Lake City I got distracted and reverted to a more Bonanza-like attitude, wanting to flare a bit too much and a bit high. With Bergwall’s encouragement I pushed the nose over and waited for the runway. All the pieces remained attached as we arrived, but it reminded me that every model has its own way of doing things.
With all of the capabilities baked into a late model SR22—known-ice certification, air conditioning, air bags, parachute, the incredibly integrated and capable Perspective panel, seating for five, and the possibility of turbocharging—one is hard pressed to ask more from a single-engine piston except for a much-needed boost in payload, which is exactly what the Generation 5 models provide. Not surprisingly, Cirrus reports that sales have jumped dramatically this year thanks to the greater useful load. Generation 6? Well, one can only imagine.
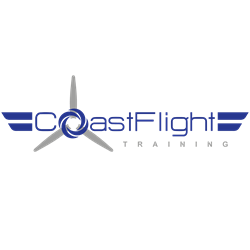
Cirrus Releases SR22T: Generation 6
Just as we thought Cirrus couldn’t get any better, they’ve outdone themselves again with the release of the SR22 Turbo – Generation 6 (G6) Aircraft. Per Cirrus, this is, “the smartest, safest, and most advanced models ever of the best-selling SR22T, SR22, and SR20 piston airplanes,” and we see this model changing the recreational aviation industry.
No doubt about it, one of the best parts of owning a Cirrus is being seen. Who doesn’t want others to see them flying around in a sleek, well-crafted airplane? What’s even more impressive about the Cirrus G6 is just how easy it is to be seen with the Spectra Wingtip lights. The design for these lights is based on the look and functionality of high-performance luxury automobiles, and makes seeing your aircraft much easier both on the ground and in the sky. Cirrus has added wingtip halo lights, and more impressively, pulsing “wig-wag” ability to guarantee your presence is always known.
But there’s more to being seen than the lights. Cirrus has always been about the luxury look and functionality of its aircraft. From the outside, it is easy to see the G6’s extended windows, which were created to bring more light into the cabin area. Once inside, you can see floor lights reading “step this way” to help navigate inside the aircraft, as well as overhead lights for Cirrus Releases SR22T: Generation 6 personal needs such as reading. After taking your seat you’ll feel more comfortable than ever in the durable, suede-like, reclining seats – also available in hand-stitched European leather. All seats in the aircraft are flexible allowing for more comfort with passengers, and more cargo room without them. Finally, as with all things Cirrus, the magic really is in the details. The G6 comes equipped with cup holders and storage pockets for your mobile device, as well as headset holders and four USB charging ports to ensure you can use your personal devices when you want, and store them when you don’t.
Perhaps the most exciting feature of the G6 is the brand-new Cirrus Perspective+ by Garmin. This sleek new system enables connectivity between aircraft and pilot, and works 10 times faster than prior Cirrus Perspective avionics. So, what are the features of this new system?
Bluetooth Connectivity
Seamlessly transfer information between your wireless devices and the Cirrus Perspective+ flight deck.
Cirrus Global Connect
It’s now easier than ever to keep communications going while in flight. The new G6 offers satellite connectivity to allow for telephone and text messaging services. Additionally, you can get the added Datalink Weather for outside of North America.
Flight Stream
Now transfer your flight plans, weather, traffic, and GPS information between you mobile device and aircraft, as well as receive Database Concierge via the Garmin Pilot app.
Database Concierge
Now transfer your flight plans, weather, traffic, and GPS information between you mobile device and aircraft, as well as receive Database Concierge via the Garmin Pilot app.
QWERTY Flight Management System
The new Perspective+ features a QWERTY keypad with larger, easy-to-read keys. Perhaps the most exciting feature of this is the new HOME button, designed to bring you back to the main navigation functions with the push of a button.
With all of these upgraded features, Cirrus is changing the way we look at recreational flying. The Cirrus SR22T G6 is now available for purchase and delivery.
If you are considering purchasing one of these new G6’s, Coast Flight would be happy to schedule an appointment with you to discuss all of the necessary details and any potential flight training you may want with the your new purchase.
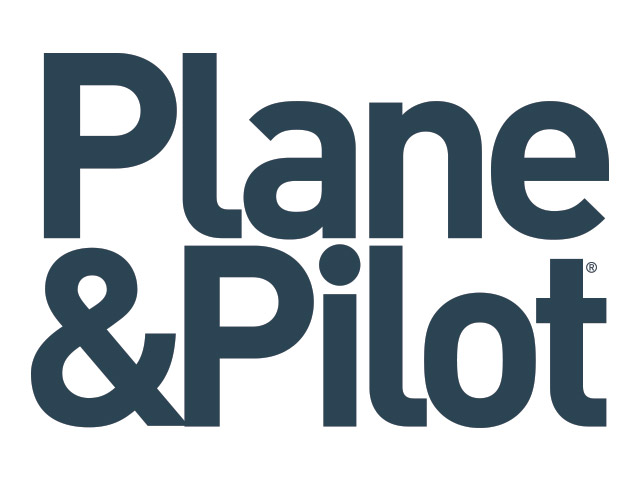
Cessna TTx Shines
After more than 10 years in production, this remarkable and too often overlooked single has become the star it was always meant to be.
I sometimes get calls out of the blue asking me for my advice about airplane buying decisions. Sometimes the caller isn’t so much seeking guidance as much as getting confirmation that the decision they’ve already made is the right one: “Yeah, a Cessna 180 sounds like a great airplane for you,” I’ll often concur.
When it comes to new planes, far and away the most common call I get is from someone who’s looking to buy either a Cirrus SR22 or a Cessna TTx. Almost without exception, they hope that I might have some secret knowledge that would help them make the call, because they can’t really figure it out.
I don’t blame them. It’s a complicated decision, and the truth is, I don’t have any secrets to expose. Both the SR22 and TTx are terrific airplanes, though both of them, in my estimation, are misunderstood, except, that is, by people who fly them a lot. And I’ve had the opportunity over the years to fly them both. While I have around 1,000 hours in SR22s, I have far less time in the TTx, a grand total of 46 hours, but that has been enough experience to get to know the airplane well. It’s a remarkably honest airplane.
The long and winding story of the TTx precedes it, and I’d argue that it’s not particularly relevant anymore. Still, this is the story in a nutshell.
“What kind of pilot is the Cessna TTx for? The TTx is a great choice for pilots who want to fly long distances (as much as 1,000 nm legs) at great speed and do it in style and comfort. An instrument rating is a must for this kind of flying.”
The original ancestor of the TTx was a fixed-gear four-seater called the Lancair ES. Over the years that plane would morph from a concept-driven kitplane built by Lancair into a production four-seat speedster originated by Columbia Aircraft into the polished speedster it is today under Textron Aviation’s ownership. Lancair’s very good idea was to create in the ES an airplane that was easier to fly than the company’s notorious Lancair IV, a retractable kitplane that was crazy fast but a handful to fly, with questionable stability and ridiculously fast approach and engine-out speeds. They also decided upon fixed gear, for cheaper insurance and less pilot workload and mechanical complexity. Sound familiar?
The ES would eventually become the basis for the certificated Columbia-series airplanes, of which there were eventually two, a normally aspirated and a turbocharged model. The planes were very well received, but unable to deliver on their promise because of a series of financial, production and act-of-God calamities that wound up putting the company into bankruptcy.
The TTx is often overshadowed by the popular Cirrus SR22, leading some to forget that the TTx is much faster for the same horsepower.
Which is where Cessna entered the tale. The Wichita giant bought the program, got production humming again at the former Columbia Aircraft factory in Bend, Oregon, and then proceeded to work the airplane, a rare adoptee, into the Cessna family lineup. After Cessna moved component production to its Mexico facilities and got some substantial teething problems worked out, the airplane was on its way to being a major player in the single-engine game.
“What are the TTx’s strengths? It’s the fastest in its class, it’s stylish, very technologically advanced and strong. The TTx has great flying manners and tremendous ramp appeal.”
While the complicated story of the TTx—it has had a few different names, including the Oregon-inspired moniker “Corvalis”—is interesting, it makes little practical difference today, except to underscore the high regard that Cessna had for the speedster. The investment is finally paying off. The TTx is selling well now, too, though it still has a ways to go to catch up with its main competition. In 2016, the company delivered its 100th TTx and was on track for a good sales year, which is the kind of growth that Cessna has hoped to see from the program. After all, the TTx is the fastest in its class, by a good shot, too.
“What are the TTx’s weaknesses? It’s expensive, though slightly cheaper than its main rival, there’s no whole-airplane parachute, it’s limited to four seats, and the cabin comfort and visibility aren’t quite as good as the competition.”
Which brings up the other part of the TTx story, that of the Cirrus SR22, the TTx’s main competitor and I would argue it’s only true competitor. The only problem, and it was a big one, for the TTx is that considering its rough early years, the SR22 got a very substantial head start on what would become its main rival, though mostly in theory at the time. Until recently, few folks at Cirrus Aircraft have been losing sleep over the TTx. While Columbia and then Cessna were spending time and money developing the airplane into the mature and very satisfying product it is today, Cirrus was selling SR22s, lots of SR22s. Which they continue to do.
And while the SR22 thrived and quickly attracted a cult-like following, the Columbia struggled, which is a shame, because in many ways, it’s more of an airplane than the SR22 is, and I believe the SR22, as those of you who’ve been reading me for a while know, is one heck of an airplane. It’s nice to have some real competition.
Feeling It
It was still warm in Central Texas, which means “really hot,” when I went flying with demo pilot Will Klein from Textron Aviation recently. As you know, Textron Aviation is the parent company of both Cessna Aircraft and Beechcraft, which makes it hard for journalists to know how to refer to airplanes and employees alike. Textron gets that, and has no problem with both media types and customers sticking with the legendary brands. (No worries: The Cessna 172 is not about to become a Textron Skyhawk.)
The TTx is not a new airplane to me, though it has had a number of improvements of late that I haven’t had the chance to get to know well. But the bones of the plane I know well. I’ve flown every iteration, from that first Experimental concept plane in the early ’90s to the latest Garmin G2000 touch-controlled avionics model. So my recent flight was as much a reacquainting as anything. Like a number of other planes I love, the TTx is like family in that way.
What’s The Difference Between TTx And SR22?
There are numerous differences between the Cessna TTx and the Cirrus SR22, and there are numerous similarities.
First, the elephant in the baggage compartment. The Cirrus SR22 has a whole airplane parachute. There have been more than 100 confirmed saves of occupants thanks to the chute, which lowers the entire airplane in the event of something terrible happening, such as the pilot losing control in some instances. The chute is expensive to maintain—repacks are required every 10 years and cost around $15,000. The chute takes up some payload, too, around 80 pounds, and you lose some baggage capacity. But it has proved to be a lifesaver in many instances and you can’t get it on the TTx.
Both are low-wing composite construction models. New versions of the SR22 (the G5 model) are five-seat planes, though the rear seating area is really only for two adults and a child or two. Both have remarkable interior room compared with legacy models, but the SR22’s interior dimensions are more pleasing to many who have flown in both planes. The TTx has inflatable door seals for some improvement in noise reduction, but both are so noisy—it’s the nature of high-performance singles today—that you’ll need a good headset in either one.
Both use the Continental TSIO-550 engine, though the Cirrus has a power control setup that uses only a throttle and a mixture (no prop), and power control is dirt-simple, giving pilots some of the advantages of single-lever power but all done mechanically. The TTx has conventional power controls, and they require much more hands-on and heads-down time than in an SR22. Both airplanes are easy for pilots to transition into. The TTx has more pleasing response,
better-harmonized controls and easier landing manners. The SR22 has better forward visibility.
The TTx has superior avionics, the G2000 touch-control suite, and the latest-gen electronics from the world leader in light plane displays. The SR22 has the previous-gen G1000 panels, remarkably capable. Both have tremendously advanced safety utilities that accompany the electronics suite. These include envelope protection, synthetic vision, extensive autopilot capabilities with great vertical nav, and weather and charts, among many others.
The TTx feels different than any airplane I’ve flown—they all feel different, true, but there’s something very distinctive about the TTx. Even in taxi it feels very solid, like an airplane larger than it is, in fact, and the sense I get is more like driving a Porsche Panamera than a family sedan. Like the SR22, you steer the TTx on the ground by use of differential braking, so it can turn on a pivot, making both sharp taxi turns and parking a breeze. The gear is solid feeling but damps bumps and uneven pavement well enough.
We were flying out of KAUS, Austin’s Bergstrom International Airport—it was a south operation that day so we got the two-mile taxi from the Atlantic Aviation FBO location.
The sound of the TTx is all its own, too. The tower cleared us for takeoff, and I rolled the corner, paused briefly to advance the power—you don’t want to just cram and go with a turbo—and felt the TTx push us back in our seats as the turbo took hold. We were at 72 knots before we knew it, I glanced down for the gear lever—oh, yeah—retracted the flaps through 400 feet, and soon started the gradual turn to the west as instructed by the tower.
The handling is awesome, and this is one area where the TTx has it all over the SR22. With the sidestick, the feel is smooth and intuitive. Unlike the side yoke in the Cirrus, the stick is just like a stick in a vintage warbird, a single point of attachment that gives you infinite aileron-elevator control input options while being mixed to perfection. On the Cirrus, the side yoke is exactly like a yoke on a Skyhawk, for instance, with the two axes being separated into two different planes of control—back and forth for the elevator and side to side for the ailerons. Both work, but the TTx’s sidestick is more pleasing.
As you might imagine, the TTx gets up to altitude in a hurry. With 310 hp up front, it can climb at a maximum rate of 1400 fpm. Knowing that ATC expected us to get out of their hair without climbing at the slow but steep best rate of climb, I settled for a cruise climb at 120 knots, which still produced over 1,000 fpm.
The electronics are a wonder. As I’ve said, the TTx is the only single-engine piston airplane with the G2000 suite, though I’ve been suspecting that Cirrus might roll it out in its SR22 anytime now, but it has given no indication that it would do that. It seems very happy with its excellent G1000-based Perspective flight deck. The G2000 goes many steps beyond G1000, though. The entire user interface paradigm is new, and this is a good thing. Instead of having the menu hierarchy system of the G1000, the G2000 (just like the new Garmin suites in jets) makes use of a graphical interface that’s very shallow, which in this usage is a good thing. Shallow means that you’re never more than a selection or two away from where you want to be, so even complicated stuff, like programming in vertical nav, is greatly simplified.
TOP: The TTx is the only piston single currently sporting the next-gen Garmin G2000 touch-controlled avionics suite. ABOVE: A single touch controller located on the center console gives the pilot access to just about every conceivable systems function.
Like the SR22, the TTx handles really nicely at low airspeeds with the flaps extended—the gear is always helping. There are also speed brakes, a really nice addition for managing airspeed, especially when approach asks you to “keep your speed up” to help with jet arrivals. The speed part is no problem, but when you have to transition from near-cruise speeds to approach speeds, the speed brakes make it a faster and easier process to manage.
The sight picture from the TTx is different from the SR22, or for that matter, from any other single I’ve flown. The front area is small, as part of that overall aerodynamic slipperiness I mentioned earlier, so the view out front seems a bit narrow, at least compared with that of the SR22, which I’d call expansive. Speeds in the TTx are typical for an airplane in this class—90 knots on final transitioning to 80 knots at 50 feet and slowing from there to a slow flare and landing. Like the Mooney Acclaim and SR22, the TTx lands best when there’s not a lot of extra speed to bleed off. Otherwise, it just wants to keep flying, a trait we like in our airplanes.
For pilots looking for a combination of speed, simplicity, reliability, high-tech electronics and fine flying manners, the Cessna TTx is right at the top of the list. There are competitors, including the Cirrus SR22, but for pilots who, among a number of other choices, don’t need or don’t want the chute, the TTx offers a fast, sexy and technologically advanced alternative catching the eye of more buyers than ever.
Cessna TTx Specifications
What’s In A TTx?
There are a number of things about the plane that I take for granted that should probably be said out loud, both for those of us who aren’t as familiar with it and for those of us who are, but are apt to forget how big a deal things we take for granted can be—okay, I’m talking mostly about myself here.
It’s a fixed-gear airplane. That means a lot of additional drag, but a great deal less mechanical and user complexity, as well as much lower insurance premiums. None of that has changed in the more than two decades since the concept was launched.
Construction: The TTx is constructed mainly out of fiberglass with carbon fiber used in places it makes the most sense. Its aerodynamics are really slick, and that’s not just spouting the manufacturer’s standard line: You don’t get 230 knots out of a fixed-gear single unless it’s incredibly efficient.
Power: The powerplant is the Continental TSIO-550-C, a 310 hp turbocharged, six-cylinder, air-cooled opposed engine that’s for all intents and purposes the gold standard in high-performance GA. The TTx has conventional power management, with separate throttle, mixture and propeller controls.
The TTx is really fast, just over 230 knots at 25,000 feet. It’s probably more instructive to ask how fast is it at the altitude you fly at, since not many of us use anything over 17,000 feet on a regular basis. The answer: around 220 knots at 16,000, on my last flight at that level. That’s hauling.
Fuel flow is around 18 gph at high cruise. That’s about half of what a twin of less performance consumes per hour. The TTx has one engine, however, so engine-out scenarios are a bit more attention-getting.
The TTx is a utility category airplane, not a normal category one, as most four-seat planes are. This means it has gone through more rigorous strength testing, so its structure is not only as strong as it needs to be, it’s even stronger than that.
Control is via a true sidestick, like the one in the F-16 fighter.
Check out the TTx and other fantastic single-engine airplanes in our latest Piston Singles Buyer's Guide.
5 thoughts on “Cessna TTx Shines”
Robert Skiles says:
As a former fighter pilot I wonder if you can swap the EFIS displays and put the flight displays on the right side, so you can fly from the right seat with the stick in your right hand??
Thanks
Bob Skiles
Stephen Potter says:
I am a former fighter pilot as well, currently a B-767 Captain. I had wondered about the transition to left handed flying until I did it in my captain upgrade….it was very easy. You will never miss flying with your right hand, I expect. Plus, you have your favored paw available for interface with the Garmin.
Clement Tshipa says:
This is really a very nice aircraft. I’m so in love with its cockpit. A very nice one. I would love to have a taste of flying it one day.
Robert Allen says:
I purchased a Cessna T206H new back in 2008, in early 2016 i decided to upgrade to something a little (or a lot) faster and something with Ice capability, i found that i wasn’t utilizing all the carrying weight of the T206H and i was burning 20gph to push the big bird thru the air, After much research, in March of 2016 i purchased a TTX over its competitor the Cirrus Sr22T, as of todays date i have flown the New Bird TTX N523RA close to 400 hours, i use her to commute from PIH to HLN and from PIH to LAS, SEA, VGT, SDL CPR and i few other places not mentioned, this aircraft has been amazing, i am 6’2″ and 230 lbs… my wife is 5’6″ and 125 (maybe) we load up with luggage, (shopping bags in my wife case) and it will take us just about anywhere, the majority of the time it flys just me for a 1-2 day mission, above the weather, thru the weather or quickly around the weather, its quiet, it flys where you look, its responsive, i flew the cirrus several times but never could get a good feel for it, shut the ya damper off and not sure if craft is controllable enough to land …HA.. the TTX is like they say “A true pilots airplane” it is much more comfortable than i ever imagined, i can fly longer in it with less fatigue than i did in the larger T206H. it doesn’t carry the payload that the old bird did, but then i haven’t had the need since i traded up.
the TTX is also much cheaper apples to apples than the media leads us to think, and then Cessna service centers are everywhere, i fly in the high Teens most of the time with the use of a Bose headset with a Built in O2 cannula, i fly at 30″ 2450 rpm’s and i burn 16.5 gah.. C.H.T.’s are about 365 on climb out burning 36 gph once up to altitude and leaned out C.H.T’s stabilize around 330-345 depending on the time of year. she flys T.A.S. (with me just me) 205, up higher FL 230-250 ..T.A.S 220 still lean of peak. 16.5 gph
my advice, if you need a great bird to get you where you’re going fast and affordable, its a TTX…. going back to a G1000 would be like looking at steam gauges again, thats how much i enjoy the G2000

We Fly: Cessna TTx
We cruised along under a high gray overcast at 13,500 feet, solitary in the sky over the winter patchwork Kansas countryside. On the gauges were figures that a pilot of any single-engine nonturbine airplane would be delighted to see: 210 knots true while burning 18 gph. This was the kind of true airspeed that 30 years ago you’d only see in a cabin-class twin. Today, we were doing it in a low-wing carbon fiber Cessna, the newly recertified TTx.
It has been more than a dozen years since the introduction of a new breed of airplanes — starting with Cirrus Aircraft’s SR20 and SR22. The Lancair Columbia joined the fray a few years later. These composite-construction, fixed-gear, high-powered speedsters boasted innovative design features and high-tech avionics. Today, these airplanes have become so much a part of the fabric of the general aviation fleet that it’s easy to forget that not too long ago they were the stuff of science fiction, or at least the futuristic-looking kit-built world.
It’s heartening to see that Cessna has not moved away from single-engine production over the past few years, as many feared might happen as business slowed during the economic downturn. Instead, the company has invested in the segment. After a production hiatus of almost two years, the TTx, which was newly recertified last summer, is back and not only ready to go but also ready to compete in the high-performance single-engine marketplace.
We flew a late preproduction model a couple of years ago and raved about the G2000 avionics system. Today the TTx is a mature product with a number of new capabilities. There’s also an increased payload, a flight into known icing-approved ice protection system, new standby instruments and a nicely upgraded interior.
Rebirth
The TTx started life as a Columbia, an airplane that was developed by a startup aircraft manufacturer and based on an early 1990s kitplane design by Lancair founder Lance Neibauer, the Lancair ES, a fixed-gear carbon fiber four-seater with a big engine. With the encouragement of the FAA’s various programs promoting the development of new certificated lightplanes, Neibauer created a company to do just that and based it in the central Oregon community of Bend. The airplane that emerged was the Columbia, a highly refined development of the ES. The company was beset by financial woes — certifying an airplane is a staggeringly expensive proposition — and by 2008, it declared bankruptcy. Cessna bought the program and worked to weave the airplane, which it renamed the Cessna 350 and 400 and later the Corvalis, into the Cessna family while continuing production in the Bend facility. The Oregon adventure was short-lived, however. Following the economic downturn of 2008, Cessna was forced to close the Bend plant and relocate manufacturing to Wichita, Kansas, and then to Mexico.
In late 2010 on an FAA acceptance flight, a section of one wing debonded in flight. No one was hurt, but the event led to the shutdown of Corvalis production, a big fine from the FAA and a complete redesign of the plane and its manufacturing processes.
New Certification, New Airplane
It wasn’t until last summer that the airplane, now known as the Cessna TTx, emerged from a recertification program complete with a new designation, the T240. The redesign cut weight from the airplane by optimizing the composite construction methods and re-engineering numerous airframe components to make the TTx lighter and stronger — the holy grail of aviation engineering — than its predecessor. The TTx’s carrying capability rose accordingly, giving it a useful load in excess of 1,000 pounds for the first time. With 92 gallons (552 pounds), that means a full fuel payload of around 450 pounds, enough for a couple of 200 pounders and bags or three lighter occupants. When filled to the tabs, the TTx, like its competitors, becomes a true four-place airplane.
One of the TTx’s main attractions is it is an undeniably sexy airplane. It always has been, but today’s model is even hotter thanks to Cessna’s focus on enhancing every element. As you approach the airplane on the ramp, this is apparent, but the source of the appeal might be a mystery. The answer is the new TTx is painted just like in the olden days. The paint adds a degree of class and style to the airplane, even while admittedly cutting down on customizing options. Therefore, it is a good thing Cessna’s current paint schemes are so pleasing and classic, especially when compared with the Corvalis models that graced our covers in years past, including a neon-lime green example and a yellow-and-black-striped demo model, which inspired a number of letters to the editor critical of the schemes.
Climbing in, you get the second treat, a completely redesigned and restyled interior. The interior of the airplane I flew for this story was tan with contrasted stitching and leather accents throughout. It’s a big improvement on an already great interior. The redesign accomplished one other thing I applaud: It replaced the big wooden fuel selector knob on the console with a metal one. Though it’s been a trademark since the Lancair days, I’ve always thought the wooden selector was out of place in such a modern wonder and looked like something from the local boat shop. This sounds like a bit of a rant, but it underscores the fact that Cessna left no component unturned in its quest to update the TTx.
The panel too is brand-new, and it is a remarkably clean and well thought out place to do the business of flying. The selection of the Garmin G2000 helped a great deal in eliminating boxes and switches, but Cessna didn’t stop there. The panel includes as standard the brilliant L3 Trilogy backup instrument, so your backups in the TTx are numerous, independently powered and rely on different software engineering, which all adds to the redundancy of the electronics. It is the best lightplane panel in the industry.
Sliding In, Heading Out
I flew the TTx with Cessna demo pilot Dave Richardson on an ideal, cold and dry day out of Cessna’s single-engine building at its Wichita Mid-Continent Airport (KICT) campus. The TTx makes a pretty picture on the ramp. Indeed, it looked as though some big shot had flown it in from hundreds of miles away for an important same-day meeting with business associates, a mission the TTx is tailor-made for. The light-colored interior is roomy and gives the impression it is bigger than it is. The seats are situated snugly in the cabin, and the controls to adjust them are identifiable by touch, a necessity due to the tight fit of the doors to the side and the console in between the pilots. The G2000 touch controller frees up space with its all-in-one goodness, and the side sticks bring additional breathing space, as there’s no conventional yoke intruding. The seats are low-slung, so Cessna provides custom cushions to elevate pilots who aren’t as tall as others. Since I played point guard in high school, compared to Richardson, who at 6 feet, 5 inches would have played center, I needed the view afforded by the extra padding. It’s not an ideal solution, but it’s one that makes it easier to meet high G force requirements for modern seats.
Richardson ran through the checklist with me for the pre-start and start sequences. One item includes inflatable door seals, a feature that seems odd in a single-engine airplane (though it’s not the first to have the seals) but quickly makes its value known. The interior is pretty quiet, if you can use that word for a single-engine airplane with a 310 hp engine a few feet in front of your nose.
Taxi is accomplished with differential braking, a method that has become so common it’s hard to remember that not too long ago it was mostly kitplanes and oddballs that used the brakes to taxi. Suffice it to say, the TTx taxies easily and can turn within its own wingspan.
As is the norm, we were light for our flight with 65 gallons on board and no TKS installed — no one ever tops it off to take a journalist flying. Richardson had no need to bother, though. Going out of KICT with the temperature barely in the double digits on the Fahrenheit scale and a stiff breeze on the nose, we were off and out of there, scarcely taking 1,000 feet to hit a rotation speed of 70 knots and then climbing at best angle at nearly 2,000 fpm. We hit 400 feet and made the tower-requested turn before we ran out of runway below us.
Richardson knew I was familiar with the flying qualities of the TTx — nothing aerodynamically has changed on the airplane. So we spent our time heading out to lunch at one of the best airport restaurants around, Enrique’s in Ponca City, Oklahoma, which serves excellent Mexican cuisine. I had the gorditas. Highly recommended.
Performance and Safety
We wanted to play around VFR, so we headed up to 13,500 feet and were seeing 210 knots true — a typical cruise speed, Richardson says — at around 17 gph at 50 degrees lean of peak. At that altitude, the TTx is considerably faster than the SR22, though the Cessna I was flying was not outfitted with TKS panels, which normally steal a few knots in drag. That, coupled with our light weight — we were a few hundred pounds below max takeoff weight — combined to put the estimated speed difference at around 10 knots, not an insignificant advantage of the Cessna and one pretty much confirmed by the books. Up into the flight levels, you can see speeds into the mid-220s or higher, according to the book, though I’ve never coaxed a TTx to its top published speed of 235 knots. Regardless, it is a smoking-fast airplane.
In addition to high-speed capabilities, we wanted to check out the airplane’s slow-speed manners, which I know from prior experience are very docile. In this case, we did it by intentionally engaging the airplane’s ESP envelope protection mode, a function of the G2000 avionics package. In a climb with the autopilot engaged and the throttle pulled way back, the system would intervene at 80 knots and lower the nose to maintain that airspeed. The result is a hands-off controlled descent. ESP also has overbanking control, hypoxia descent mode and overspeed protection, all fantastic safety advances.
One huge advance is the TTx’s ability to fly the missed approach completely coupled, a rare capability in a GA airplane, let alone a light single-engine model. We tried it out at Stillwater, Oklahoma, flying the south approach down to minimums and then going missed. You apply full throttle, lose a notch of flaps, check that the gear is indeed permanently down and clean up that last notch while you monitor the GFC 700 as it flies the procedure, including the vertical nav part. Considering the workload and potential stress during the missed approach phase, a fully coupled miss (save autothrottles, that is) is a great safety bonus.
I’ve written about G2000 before, but every time I fly it, I get to see new capabilities. The G2000 represents a quantum leap in avionics design. G2000 does everything differently, and by that I mean it does most everything. By integrating all of the functions of navcoms, transponders, audio panels and other system controllers, such as the environmental controls, it eliminates the need for those other federated boxes and their attendant switches, buttons, dials, knobs, displays, and well, you get the idea. The G2000 is managed through a touch-screen controller, and in the case of the TTx, it’s mounted at the front of the console just below the panel. It’s easy to reach and to control, even in turbulence. With G2000, you get one controller for every “box,” instead of having multiples, which is still the case with all Garmin G1000 systems. Want to adjust the intercom settings? Go to the touch-screen controller. The temperature in the cockpit? Touch-screen controller. Monitor systems status? You got it. It’s one-stop shopping for airplane management.
G2000 has the added advantage of being easy to learn. If you’re familiar with any G1000 system, all you need to do is spend a little time with the new touch-controlled version to get the hang of it. There are a few new ways to do things, like swapping frequencies and configuring the audio, but all of them require less head-down time, less inputting of data and fewer “button” pushes. G2000 is a huge advance in GA avionics and a strong selling point for the TTx.
We missed the approach to Stillwater that day and headed to Ponca City for lunch and then back to KICT. I love the TTx’s stability as an instrument platform. I hand-flew a practice ILS — the nearest cloud was in Ohio — keeping things centered with synthetic vision on the big PFD.
With its relaunch, recertification and extensive reworking, the Cessna TTx is in a more competitive place than it has arguably ever been. It’s the fastest in its class, has the best avionics, boasts a number of highly desirable safety features and has terrific ramp appeal. In many ways, the dream that was the ES two decades ago is finally coming to fruition in the form of a fast, comfortable and technically advanced carbon fiber marvel called the TTx.

Cessna TTx: Prime Performer Power and panel to the max
Cessna, maybe for decades, wanted to expand its single-engine piston line to include a 200-plus-knot airplane, and in 2007 the company saw its opportunity. That was when it bought the Columbia line of certificated aircraft made by renowned kitbuilder Lancair: the Columbia 350 and 400. For a company like Cessna, which traditionally designs its airplanes in house, this was a big move. But Lancair was in bankruptcy at the time, and Cessna snapped up the Columbia line for a mere $20 million to $26 million, depending on whom you believe. That’s a fraction of what it would have cost to certify an in-house design—and instantly Cessna had its piston-single hot rod.
Cessna TTx
SPEC SHEET
Cessna TTx
Base price: $689,000
Average equipped price: $810,785
Specifications
Powerplant | Continental TSIO-550-C, 310 hp
Recommended TBO | 2,000 hr
Propeller | McCauley, three-blade, constant speed
Length | 25 ft 2 in
Height | 9 ft
Wingspan | 36 ft
Wing area | 141.2 sq ft
Wing loading | 25.5 lb/sq ft
Power loading | 11.6 lb/hp
Seats | 4
Empty weight | 2,530 lb
Max ramp weight | 3,600 lb
Max useful load | 1,070 lb
Payload w/full fuel | 458 lb
Max takeoff weight | 3,600 lb
Max landing weight | 3,420 lb
Fuel capacity | 106 gal (102 gal usable), 636 lb (612 usable)
Baggage capacity | 120 lb, 25 cu ft
Performance
Takeoff distance, ground roll | 1,280 ft
Takeoff distance over 50-ft obstacle | 1,900 ft
Takeoff distance over 50-ft obstacle, 5,000 ft msl | 2,460 ft
Max demonstrated crosswind component | 23 kt
Rate of climb, sea level | 1,400 fpm
Cruise speed/range w/45-min reserve (fuel consumption) @ 85% power, rich of peak TIT | 235 kt/830 nm
25,000 ft | (25 kph) @ 55% power, lean of peak TIT | 208 kt/1,250 nm
25,000 ft | (13 gph)
Service ceiling | 25,000 ft
Landing distance over 50-ft obstacle | 2,640 ft
Landing distance, ground roll | 1,260 ft
Limiting and recommended airspeeds
VR (rotation) | 60 KIAS
VX (best angle of climb) | 82 KIAS
VY (best rate of climb) | 110 KIAS
VA (design maneuvering) | 158 KIAS
VFE (max flap extended) | 117 KIAS
VNO (max structural cruising) | 181 KIAS
VNE (never exceed) | 230 KIAS
VS1 (stall, clean) | 73 KIAS
VSO (stall, in landing configuration) | 60 KIAS
For more information contact Textron Aviation.
All specifications are based on manufacturer’s calculations. All performance figures are based on standard day, standard atmosphere, sea level, maximum weight conditions unless otherwise noted.
Cessna changed the Columbia 350’s name first to Cessna 350, then Cessna Corvalis. Likewise, the Columbia 400 became the Cessna 400, then Cessna Corvalis TT, then Cessna Corvalis TTx (when the Garmin G2000 avionics suite was introduced in 2011), and, finally, Cessna TTx. The “TT” stands for “twin turbocharged” (the TTx has a dual bank of intercooled turbos); Corvallis is the name of a town west of Lancair’s Bend, Oregon, location; and the little triple-mountain logo is a nod to a set of mountain peaks near Bend. While we’re at it, there’s one L in the airplane name, but two for the town of Corvallis. Whew—got all that?
As for sales, the TTx has been challenged by Cirrus’ SR22T, and, to a lesser extent, the Mooney Acclaim Type S. Did all that confusing nomenclature play a part? Hard to say. It may sound trifling, but so many name changes can bring consequences. Then again, Cessna didn’t sufficiently apply itself in promoting the Corvalis/TTx line. In all, Cessna sold a total of 261 400s, Corvalis TTs, and TTxs since 2007. Lancair sold 604 of its certified Columbia predecessor designs between 2000 and 2007.
It’s the 310-horsepower Continental IO-550 and those twin turbos that give the TTx its satisfying true airspeeds. Cessna says it’s the world’s fastest production fixed-gear piston single on the market today. The company advertises 235 knots as a maximum cruise speed—but that’s up at 25,000 feet where you’ll need oxygen (which is standard); where many probably won’t fly; and at 85 percent power and a fuel-hungry 24 gallons per hour, at a 50-degrees rich of peak EGT power setting. Still, it’s nice to have the option of flight-level flying for weather avoidance, or to take advantage of rip-roaring tailwinds.
A more typical cruise altitude and power setting would be below 10,000 feet, and at lean-of-peak mixtures, where true airspeeds at 65 to 75 percent power run around 170 to 180 knots and fuel burns average 14 to 18 gallons per hour, respectively. Of course, if you’re in a hurry, at 7,500 feet you could push the throttle up to the manifold pressure redline of 37.5 inches of mercury, dial up the prop to 2,500, fly at rich of peak, and see 190 knots true airspeed. The penalty is that 24-gallons-per-hour fuel burn. The reward is seeing the scenery roll past at near-turboprop speeds.
Inside and out, the TTx is a full-featured airplane—and strong. Twin carbon fiber spars run the entire wingspan. And embedded in the fuselage structure is a protective carbon fiber roll cage that surrounds the cabin. The airframe has an unlimited life, and has been fatigue tested to the equivalent of 25,200 flight hours. To top it off, the TTx is certified in the Utility category, one of the benefits of which is a comparatively high, 158-knot maneuvering speed. This means you can still make decent time in turbulence, if that’s an issue. For slowing down, there are speed brakes—standard. For battling ice, there’s a flight into known icing (FIKI)-certified TKS weeping-wing ice protection system—a $55,180 option that most people order. For avoiding thunderstorms, there’s XM weather ($7,725 extra) via Garmin’s GDL 69A datalink receiver. There are plenty more options—Garmin’s GTS 800 traffic advisory system ($14,525); terrain avoidance and warning system ($10,610); GSR 56 Iridium satellite datalink receiver for worldwide reception of weather information; and more. Oh, and air conditioning, which rings up at $29,870. Keyless entry for the gull-wing doors is standard.
The wing leading edge uses an outboard cuff that’s set at a lower angle of incidence than the rest of the laminar-flow wing. This keeps the airflow energized over the outboard wing section and ailerons, and assures that the inboard wing sections stall first. This bit of design work is an adoption of NASA’s Advanced General Aviation Transport Experiments (AGATE) initiative, conducted in the early 1990s with the goal of improving the safety and efficiency of general aviation airplanes. In case you want to disrupt that airflow to, say, hasten a descent or slow down in the pattern, you can pop the speed brakes. The TTx is a slippery machine, so there are times you’ll need them.
Inside and out, the TTx is a full-featured airplane—and strong.In case all that slipperiness gets away from you, the TTx’s Garmin GFC 700 autopilot has electronic stability protection (ESP). With the autopilot off, its servos will automatically exert corrective force in pitch when attitudes reach 17 degrees nose up or 19 degrees nose down. Exceed 45 degrees of bank, and ESP will apply force to roll the airplane back to 30 degrees. Fight the corrective forces for any 10 seconds of a 20-second period, and the autopilot automatically engages.
As for the panel, its clean, well-organized look is dominated by Garmin’s G2000 avionics suite. This comprises two huge, 14.1-inch-diagonal screens in landscape arrangement. To control the display views and system functions there’s a Garmin GTC 570 touchscreen controller, mounted ahead of the armrest. The leather seats are very comfortable, thanks to cushions that adapt to your contours and still provide good ergonomic support.
Cessna says that from 14,000 feet the TTx can glide 30 nautical miles; that beats the competition by 10 nm.The view of the panel is wide open, thanks to the sidestick flight controls. The sticks pivot around a central point, and are connected to push rods. There are no springs for artificial control feel or cables that can stretch over time. There’s no aileron-rudder interconnect, either. There is a servo tab on the left aileron that operates passively to reduce aileron control input forces; the TTx can have high roll forces at airspeeds above 120 knots or so. There’s also a rudder limiter that reduces rudder throw as airspeed slows below 100 knots. This, the aft fuselage belly skeg, a limited elevator area, and those wing cuffs preserve directional stability and control at stall angles of attack.
The G2000 and its autopilot make serious IFR cross-country flights a piece of cake. You can even split the multifunction display (MFD) screen and show two different views at the same time: XM datalink weather on one, for example, and Jeppesen approach plates on the other. Or traffic and a map view showing flight plan legs. You get the idea. Another nice touch is the panel-mounted pulse oximeter, a nice feature for high-altitude or night flying. Insert your finger in the sensing unit and your blood-oxygen saturation and heart rate appear in a window of the G2000 MFD.
Maneuvering in the pattern and elsewhere is a breeze. Fly downwind at 100 knots, base at 90, and use 80 to 85 knots on final using full flaps. Here’s where the speed brakes can come in handy if you need to “slow down and go down” at the same time. For takeoffs it’s rotate at 60 knots, lift off, and climb away. At the VX of 82 knots you’ll see about a 15-degree nose-up pitch attitude, and a lot of sky, as the TTx at lighter weights can hit 1,800 fpm in the initial climb.
Now let’s say you’ve botched an approach and must go around. But you’re having a bad day and forget to retract the flaps or stow the speed brakes. Go to full power, pitch up for VX, and the TTx’s 310 horses will still let you climb out at 700 to 800 fpm.
It’s impossible to discuss the TTx without addressing its main competitor in the marketplace: the Cirrus SR22T. Yes, the SR22T has a bigger cabin and more baggage space, but the TTx beats its speed; has bigger displays, a touchscreen controller, and speed brakes; and holds more fuel—all standard. Cessna, now part of Textron Aviation, also says the TTx has better runway performance, a better climb rate, and at a high-speed power setting can fly an 800-nm trip 26 knots faster than an SR22T—arriving at the destination 19 minutes quicker, while burning just 12.7 gallons more fuel. The TTx can glide farther, too. Cessna says that from 14,000 feet the TTx can glide 30 nautical miles; that beats the competition by 10 nm.
Last but not least, Cessna says the TTx’s typically equipped price is some $49,000 less than the SR22T’s ($810,785 versus $859,800). This assumes a TTx with FIKI, XM datalink weather, Garmin’s TAS, TAWS-B, air conditioning, and Jeppesen’s ChartView electronic charts—which is how many TTxs are ordered.
No, the TTx doesn’t have a parachute, and if you top off the 102-gallon fuel tanks you can carry perhaps two people and bags, or maybe three light people and their equally light bags. The value of having a ballistic recovery parachute is debatable. Some say it’s not essential to their buying decision, citing traffic- and terrain-avoidance technology as prime defenses against the threat of midair collisions, terrain, and obstacles. As for the most common accidents, the TTx’s roll cage and Utility-category construction provide protection. And its glide performance offers more options in case of a power loss. That said, Cirrus’ ballistic parachutes have saved a significant number of lives from catastrophic events. Truth to tell, the TTx’s structure doesn’t allow enough interior space to accommodate a parachute system.
As for the full-fuel useful load situation, the TTx is like any other light airplane—if you want to carry more passengers and their bags, then you’ll have to take on a partial fuel load. Then there’s this: How many times do you really need to fly with full seats and a packed baggage compartment? Typical flights usually involve one or two passengers, max.
Maybe here’s the takeaway. If you need to fly a family hauler, then the SR22T may be your airplane. But if you want gobs of performance, sports-car-like handling, strength, and durability, then the TTx is for you. To use a well-worn phrase, the SR22T is more of a passenger’s airplane. The TTx is definitely a pilot’s airplane.

Cirrus SR22T vs Cessna TTx
The last time I flew a TTX it was called Columbia. It also had EXPERIMENTAL placarded to the door.
I’d flown to central Oregon in my Cessna 205. In the Columbia, climbing at well over 1,200 FPM toward 17,500 feet, I noticed our airspeed was faster – a lot faster – than my 205 in cruise. Yep, the Columbia was fast. The Cessna TTX is faster.
The SR-line has been a perennial top seller for Cirrus. Equipped with a parachute and continually refined to add value every model year, Cirrus has done much to increase the pilot population by marketing so effectively to non-pilots. They call it #CirrusLife. And its SR22T GTS is at the top.
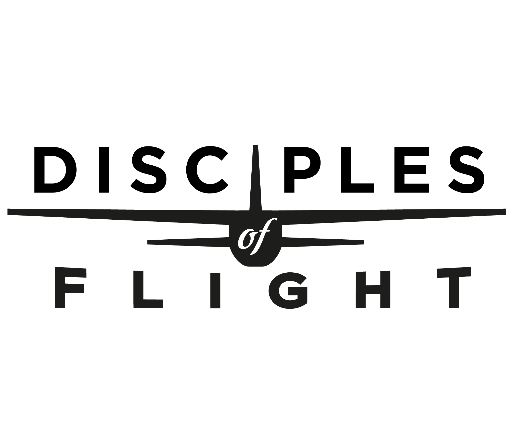
The Beechcraft A36 Bonanza
The Beechcraft A36 Bonanza: Reliability, Comfort, and Performance
The Beech Aircraft company was founded in 1932 in Wichita, Kansas, by Walter Beech and his wife Olive. Beech had previously founded Travel Air in 1924, but after they were bought by Curtiss-Wright in 1929 and Beech was moved to a position as VP of Sales, he longed for a return to airplane production. So he quit, founded a new company, and set up shop in an idle Cessna factory.
Fifteen years later in 1947, they shipped the first airplane from the Beechcraft Bonanza line, a Model 35.
As a tragic side note, it was an original 1947 Model 35 Bonanza that was involved in the famous plane crash that claimed the life of musician Buddy Holly. On the February 3rd, 19591, at about 1 in morning, rock stars Holly, Richie Valens, JP “the Big Bopper” Richardson and pilot Roger Peterson took off from Mason City Airport in Iowa in a light snow. Shortly after takeoff, they crashed into a cornfield, killing all four men on board.
In a follow-up investigation, the crash was attributed to pilot error. The generally accepted theory is that the 21-year-old Peterson couldn’t accurately read the plane’s Sperry F3 attitude indicator, and thought the plane was ascending when it was actually descending. A couple of other factors contributed to the crash: Peterson did not hold an instrument rating and was not aware of the adverse weather conditions until shortly before taking off.
(Photo by: Spartan 7W, CC3)
Since 1947, Bonanzas have been in continual production, and this line of aircraft hold the record for the longest production run of any aircraft in history. During the ongoing 68 year run, they have built more than 17,000 Bonanzas between all the many models and variants. But out of the many models, the Beechcraft A36 Bonanza reigns supreme. First built in 1970, 2,128 A36 models have been delivered and are still in service. And though the A36 model came to an end in 2005, its legacy lives on with the G36.
So what makes the A36 Bonanza such a great airplane, and lands it high on the dream list for many private pilots, next to other comparable aircraft like the Cessna 210? Reliability, comfort, and performance.
A Quick A36 Bonanza History
By the time the Model 36 arrived, Beechcraft had been making Bonanzas for over 20 years. This meant that they could draw on years of experience and knowledge, and deliver a reliable, dialed in model with a sleek, aerodynamic design right out of the gate. The first Model 36, delivered in 1968, used a modified Model 33 Bonanza fuselage, which was 10 inches longer, with the length split fairly evenly for and aft of the wing. This extra length allowed them to add a third row of seats, making it a six-seat aircraft, and the largest single Beechcraft made. The Model 36 also featured four cabin windows on each side, starboard rear double doors for the aft cabin, and a 285 hp Continental IO-520-B engine.
Two years later, in 1970, they released the A36 Model. It had an improved deluxe interior, a new fuel system, and higher takeoff weight. And for the next 35 years, that was it. No B, C or D (or all the way to S, like the Cessna 172) models2, though they did produce a turbocharged version in 1979, the A36TC. This version had a three blade propeller and a 300 hp turbocharged Continental TSIO-520-UB engine.
Twenty-two years after “The Day That Music Died,” another accident occurred that may have had a similarly large impact on our culture if it had gone a little differently. On February 7th, 1981, Apple developer and co-founder Steve Wozniak took off from Sky Park Airport in Scotts Valley, California in his Beechcraft A36TC Bonanza. As he was starting to climb, the aircraft stalled, and then bounced down the runway, breaking through two fences and crashing into an embankment. Wozniak suffered severe head and face injuries, including anterograde amnesia, or the inability to form new memories. He suffered from this amnesia for almost five weeks, and couldn’t remember the crash, the hospital where he was taken, or what he did after being released from the hospital. He eventually recovered and continued his long and ongoing involvement with the world of computers.
The turbocharged version received an upgrade in 1982, the B36TC, which featured a longer wing span, redesigned instrument panel and controls, a higher take off weight and an increase in range. This variant remained in production until 2002.
Occasional updates to the A36 were made through the years, from updating to a 28-volt electrical system in the late 70s3 to changing to a Continental IO-550-BB engine in 1984, but the A36 remained in production until 2005, weathering multiple general aviation slumps, continuing to sell and remaining a widely admired aircraft. Finally, in 2005, Beechcraft introduced the G36 model, which was a glass cockpit update of the A36, equipping it with a Garmin G1000 system.
The Beechcraft A36 Bonanza Hallmarks
Reliability
Because of the years of experience behind the production of the A36, the airframe was a very conventional construction, which led to it being durable and generally easier to repair. In addition, with production of the A36 model lasting so long, and the G36 featuring the same basic construction as the A36, parts are widely available. This helps simplify the maintenance and repair process and keeps costs down. Having been in production so long, it also means the most of the quirks and issues with this aircraft are more well known, so there are generally fewer surprises.
Comfort
With 50 inches of height in the cabin, the A36 Bonanza offers enough headroom for most pilots, even taller ones. Large windows surround the pilot and wrap up onto the roof of the aircraft, providing excellent visibility and light. And vibration and sound levels in the cabin better than most other single engine piston aircraft. Additionally, though a few very early A36 models have all six seats facing forward, the club configuration very quickly became standard, with the middle 2 seats facing aft. This allows for passengers to stretch out a little more when not flying at max capacity. Coupled with the large rear doors, access and use of the aft cabin is simple. And if you need a little more room for cargo, taking out the rear seats is a simple process, using quick release pins.
Performance
At 176 kn, the A36 was at the front of the pack for cruise speed during much of its time. And though other more powerful singles and turbocharged aircraft have passed it up, it still remains one of the more fuel efficient, generally burning around 15 gallons an hour at cruise speed. So how does it fly? In a write up a few years back, Flying Magazine had this to say about how the A36 Bonanza handles:
“The flying qualities of the A36 are legendary for excellent harmony of forces and smooth response. The short V-tail and Model 33 Bonanzas may have slightly lighter control force, but the A36 more than makes up for that with enhanced pitch stability. The longer fuselage length and big horizontal tail provide very precise pitch control that lends itself to smooth and predictable approaches and landings, not to mention lower workload when hand flying.”
And if you’re interested in enhancing the performance aspects of the A36, another benefit of having been around a long time is that there are a lot of modification options. AVWeb put together an excellent mod primer a few years ago, and it’s well worth checking out if you’re considering investing in an A36.
A Solid Investment
The Bonanza G36 starts at roughly $780,000 new, which may put it out of the range of many pilots. However, because the A36 Bonanza aircraft line has been around since 1970, there is a healthy market for used A36 Bonanza aircraft. Prices can range from around $70,000 for an older year A36 that will require work, to the $3-400,000 range for more recent model years in good flying shape.
When shopping for a used aircraft, of course, the usual caution applies. Be sure to have any prospective purchase checked out by a mechanic knowledgeable and versed with working on Beech aircraft. This will help you understand any potential quirks or problems with the aircraft you’re purchasing, and how much of an immediate investment you’ll be making in maintenance to get your plane in the sky. The Bonanza aircraft also have one of the most active owner’s communities in aviation, and the American Bonanza Society can be an invaluable resource for those looking for information, opinions, and views from current A36 pilots.
The Beechcraft A36 Bonanza Just Looks Cool Too
So, spending some time reading up on the A36 Bonanza, one thing I came to really admire is that this is a sleek aircraft, with a very cool design. For a plane with such a long history, they got the look right, from the beginning. Like many classic muscle cars, it has a look that is at once classic, familiar, and distinct. You usually don’t mistake an A36 Bonanza for other aircraft. And in general, it seems like most people don’t want to mess with that classic look, with paint jobs tending to be low key, with different stripe patterns on the fuselage. However, I did come across a few paint jobs that I felt were a little bold and very nice, without conflicting with or overpowering the basic cool nature of the A36 design. Interestingly, I found myself drawn to designs that used grey and black.
The first paint job I found on Airliners.net, and it has a beautiful mix of blacks on the belly and grays on the upper half of the fuselage that lend a little more class and power to a newer G36 model. Click Here to view the photo.
The second, also on Airliners, follows a similar idea to the first, using blacks and greys. However, they invert the order, with a grey belly, and a black upper half, which still works incredibly well. Click Here to view the photo.
This third paint job comes from a G36 Bonanza that was up on Global Air. I particularly like the use of black to highlight the cowling and tail on the aircraft.
Whether you choose to new or used, the G36 / A36 Bonanza is a great all around aircraft. Sleek, reliable, comfortable and well-established, this aircraft will likely continue to be a favorite of pilots for years to come.
SIDENOTE: During its production, many Bonanza’s were built with a distinctive “V-Tail” configuration. In this brief video, Jim Hoddenbach and Bryan Stewart discuss how this configuration led to the nickname “Fork Tailed Doctor Killer.”
Beechcraft King Air: Over 60 Million Flight Hours and Counting
The Beechcraft King Air is iconic in the pressurized twin turboprop world. Most charter departments have one because they are reliable, couch comfortable for the passengers, and have a spectacular safety record. To know King Airs is to know that there are so many variations of each model that it makes salesmen pull their hair out. Pilots know that you can jump into any model variation of the Beechcraft King Air and recognize instantly they are definitely from the same family, but like all children, each model [Click to read more…]
Current Beechcraft G36 Bonanza Specs
General Characteristics
Crew: one
Capacity: five passengers
Length: 27 ft 6 in (8.38 m)
Wingspan: 33 ft 6 in (10.21 m)
Height: 8 ft 7 in (2.62 m)
Empty weight: 2,517 lb (1,142 kg)
Gross weight: 3,650 lb (1,656 kg)
Powerplant: 1 × Continental IO-550-B , 300 hp (224 kW)
Propellers: three-bladed Hartzell Propeller, 6 ft 8 in (2.03 m) diameter
Fuel capacity: 74 gallons (280 l)
Cabin Interior
Height: 50 in (1.27 m)
Width: 42 in (1.07 m)
Length: 12 ft 7 in (3.84 m)
Performance
Cruise speed: 177 kn (204 mph; 328 km/h)
Range: 221 nmi (254 mi; 409 km) with full passenger load
Ferry range: 920 nmi (1,058 mi; 1,704 km)
Takeoff distance: 1,913 feet (583 m)
Ground Roll: 962 feet (293 m)
Landing distance: 1,450 feet (442 m)
Service ceiling: 18,500 ft (5,600 m)
Rate of climb: 1,230 ft/min (6.2 m/s)

Beechcraft Bonanza
From the original Model 35 (which first flew on December 22, 1945) to the versions rolling off Beech's — now Raytheon's — assembly lines today, the Bonanza has cut a swath through general aviation like a timeshare salesman through a clutch of snowbirds.
To understand the Bonanza, it helps to know something about the period during which it was designed. In postwar America, most aviation companies were staffing up for an expected boom of pilots coming home and demanding new airplanes. During the war, unprecedented research and development in aviation took place, and the state of the art had progressed tremendously since the late 1930s. Walter Beech wanted to take advantage of the knowledge amassed during wartime research and, in particular, to build an aluminum airplane that would be a clean break from the models available before the war and new designs expected to emerge after.
Into this burgeoning marketplace Beech thrust the Bonanza. Distinctive in form and construction, the swift Bonanza offered unmatched-in-class speed and daring good looks. It also embodied some genuinely forward thinking. The tricycle gear, of course, was uncommon at the time. Beech attempted to make it rugged enough to stand up to the many unpaved strips in use then; even the wing's angle of incidence (a lot of it by today's standards) and the gear placement were aimed at making this nosedragger survive cobbly strips. Weight savings were a high priority with the Bonanza, too, leading in part to the distinctive V-tail.
In addition to its distinctive appearance, Beech believed that the V-tail would save weight and possibly create a bit less drag. Wind-tunnel tests then showed that it was comparable to a three- surface design for stability. Later, the V-tail would become the focus of controversy with regard to the airplane's structural integrity. (After decades of 35s breaking up in flight, the matter came to a head in 1987 when extensive wind-tunnel time and flight testing revealed that the tail was not up to certification standards in one corner of the airplane's envelope. Beech had contended all along that the 35s broke up when flown outside the normal speed/G- loading limits; the vast majority of the break-ups came from the ranks of the oldest airplanes. Amid much controversy and hand- wringing, Beech introduced a fix in the form of tail reinforcements- -a leading-edge cuff for some models, with additional stiffeners for others.) Still, the airplane is considered highly desirable, capable of performance in delicate mixture that few other airplanes have achieved.
In 1960, Beech introduced the Model 33 Debonair (name later reverted back to Bonanza), a stripped Bonanza with a conventional tail. Sharing the 35's cabin and wings, the Deb carried a 225-hp Continental IO-470. It sold reasonably well but hardly made a dent in the more desirable Model 35's popularity.
According to Larry Ball, Beech management met repeatedly in the late 1960s and early 1970s to talk about a Bonanza replacement. Engineers at the firm knew that the V-tail airplane's CG and control- authority issues meant that the configuration had reached its maximum potential with the then-current airplane. More power and more weight surely would call for a new design. A cabin-class Bonanza replacement was floated — and a mockup constructed — but it didn't fly past Beech management. (Other design concepts were circulating at Beech in the late 1960s, one a six-place single that looks remarkably like a Piper Malibu.) Ultimately, Beech found the answer to the 35's shortcomings right at home, in the 36. Basically a Model 33 stretched 10 inches ahead of the wing, the 36 went on to become one of the most desirable Bonanzas ever made.
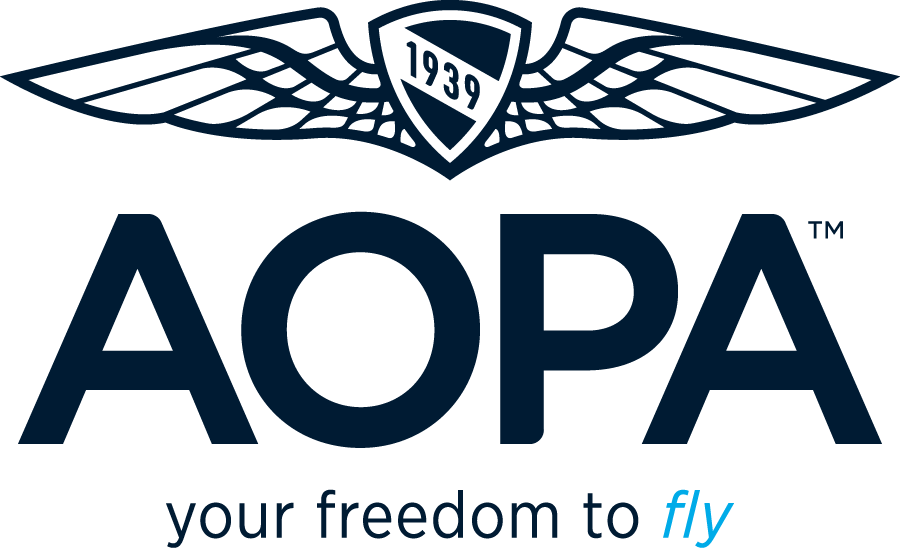
Best in Class
It’s almost as if Piper created the new M600 single-engine turboprop just for James (Scott) Middleton. A frequent trip for the entrepreneur was from his medical supply company’s headquarters in North Florida to Denver, where he owns a respiratory equipment company. Distance: Just shy of 1,300 nautical miles. IFR range with reserves on the new M600: 1,300 nm.
“When they told me about the extra 90 gallons, they had me,” said Middleton, who is the first customer for the new model and expects to take delivery this fall. Middleton knew what he was getting into; he already owns a 2014 Piper Meridian and loves the airplane. “My first 15 months were the perfect ownership experience,” he said. “I had zero squawks in the first year of ownership. I’ve never had that in 30 years of owning airplanes.”
Middleton learned to fly in 1986 after a friend took him for a flight in a Citabria, lifting off from the grass at a family picnic. “That was on a Saturday. I was at the airport for my first lesson on Monday.”
He soloed in about eight hours and immediately bought a Piper Seneca II. You know a student is all in when he buys a twin right after solo. Middleton owned the Seneca for 16 years, but with a growing family he moved up to a Cessna 414. When the aging Cessna started becoming a maintenance burden, his wife, Patty—a frequent passenger—said, “You should buy a new one.”
Understanding that permission is good, he purchased the new 2014 Meridian—or, as Piper CEO Simon Caldecott likes to put it, Middleton “saw the light and came home.”
However, even with the new Piper, he longed for more range to simplify that trip to Denver. His Piper dealer encouraged him to visit the Piper factory to see what they were working on. On a trip there in a 2015 M500 turboprop—an upgraded Meridian—he experienced some of the new autopilot features and saw what the engineers were doing with the all-new wing, which can carry an extra 90 gallons of fuel. “I always thought with an extra 75 to 100 gallons, it would be the perfect airplane.”
That clean new wing, fat with extra fuel and the structure to allow for a maximum takeoff weight of 6,000 pounds, boosts the Piper Meridian from a personal airplane to a serious business-aircraft contender. The smooth new wing includes no aerodynamic devices, short of stall strips. Gone is the wing root glove found on the Meridian, added to house jet fuel as the PA–46 transitioned from the piston-powered Mirage to a single-engine turboprop in 1999. Instead, the new M600 wing is straight, with a much wider chord.
More important, though, the higher weight—along with the extra fuel—give M600 owners a great deal more flexibility in trading fuel/range for passengers. In fact, with a standard useful load of 2,400 pounds, the M600 can carry 700 pounds more than the standard M500. A fully fueled M600 with 260 gallons can carry only about 107 pounds more than an M500 with full tanks (170 gallons), but the 53-percent increase in fuel capacity provides a range of payload options not available to the M500 owner.
Piper’s Caldecott believes that flexibility opens a new market for the M600—that of a true business-class airplane, because it has the capacity to carry a professional pilot as well as reasonable payload for passengers and bags. Prior to the upgrade, most Meridians were flown by owners on personal missions, at least in part because of the payload limitations.
Although the M600 weighs considerably more, it gives up no cruise speed to its lighter cousin. When it is certified this fall, the M600 is expected to have a maximum cruise speed of 260 knots true airspeed, on par with the M500. The speed comes in part from a 100-shaft-horsepower boost, to 600, for the Pratt & Whitney PT6A-42A. Also contributing are that clean wing, and moving the radar antenna from an under-wing pod to a pod embedded in the leading edge—worth about 3 knots, according to the Piper test pilots.
In addition, the M600 carries a VMO of 250 knots indicated airspeed, compared to just 188 for the M500. The higher VMO means M600 pilots can descend more quickly, saving fuel by staying high longer and reducing block times.
Besides the wing and slightly wider gear track, the M600 sets itself apart—and earns the $600,000 cost difference, compared to an M500—through the use of the latest in cockpit technology. The M600 is the first single-engine turboprop to use the Garmin G3000 cockpit, which includes a pair of touch-screen controls to manage the PFDs and MFD. The three 12-inch screens create an all-new, clean panel with a minimalist feel, even though its capabilities are tremendous. To the left of the pilot’s PFD, an Aspen EFD1000 with an internal battery serves as emergency backup, eliminating the need for any mechanical instruments. In addition, all of the placards are now backlit, improving night operations.
The G3000 incorporates an automatic digital pressurization controller, meaning the pilot need only set the destination’s field elevation; the system does the rest. Taking note of the recent spate of accidents seemingly related to pressurization and hypoxia problems, the G3000 includes a hypoxia recognition system. If the pilot hasn’t interacted with the avionics in some way for a period of time, or if the cabin has climbed to an unsafe altitude, the GFC700 flight control system will descend the airplane to a safe, breathable altitude.
In a further attempt to improve safety, Piper and Garmin worked together to leverage other capabilities of the GFC700, including ESP—Electronic Stability and Protection; USP—Underspeed Protection; LVL—Level Mode; and GA—Go Around. ESP automatically nudges the airplane back closer to the center of the flight envelope when it strays with the autopilot off—the pilot feels higher resistance as the airplane gets closer to departing controlled flight. USP causes the nose to pitch down, preventing a stall. LVL allows the pilot to return the airplane to straight-and-level flight with the touch of a button.
GA permits a pilot to fly a coupled missed approach, especially critical during a low approach when the pilot decides to go around. Too frequently, pilots lose control when forced to hand-fly a missed approach as they reenter instrument conditions while transitioning from a nose-low, low-power situation to a nose-high, high-power climb. Allowing the autopilot to fly the procedure can improve safety. The pilot must then manage only power.
“The ESP and underspeed protection, it really works,” said Middleton, who experienced it in the M500, which began deliveries earlier this year. “We all think we’re great pilots, but not everybody is completely on your best game every day. If you lose attention for a moment, this can save you. It was amazing.”
The cockpit changes represent a significant advancement in safety—so important that Piper decided to infuse them into all of the M Class airplanes. The M Class includes the M600, the M500—the Meridian still with a Garmin G1000 panel, but with the flight control upgrades and interior refinements—and the M350, the rebranded piston-powered Mirage that also includes the flight control upgrades and interior changes. In fact, the M350 also includes a panel-mounted pulse oximeter that allows the pilot to keep track of his blood oxygen saturation level and pulse rate. In addition, the device warns if carbon monoxide levels become dangerous.
The M500 does not yet include the emergency descent mode, but Piper officials say that is in development.
The new family of airplanes gives Piper customers a clear path to more performance and capabilities. The 350-horsepower, 213-knot M350 is the only pressurized six-place, cabin-class single in production. Standard equipped price is $1.16 million. The 500-shaft-horsepower M500, at $2.26 million, brings turboprop speeds of 260 KTAS and turbine reliability, but at less range and more fuel burn. The M600, at $2.82 million, keeps the speed and adds the more sophisticated cockpit, but nudges the range out to 1,300 nm—close to the M350’s 1,340-nm range. It’s interesting that the slowest model with the least amount of fuel (120 gallons) has the greatest range—that says something about the efficiency of piston engines.
Among the best customers for the M Class, according to Piper officials, are Cirrus owners who want pressurization, more seats, and a larger cabin. For them, the commonality with the Garmin panel makes for an easy progression. Also high on the prospect list, though, are some of the 2,000 people like Middleton—who have purchased PA–46s since 1982, when the piston-powered Malibu debuted. As Caldecott says, “We welcome them back into the family.”

Piper Malibu: A New Airplane for a New Day
Back in 1983, the new Piper Malibu was a revolution. In the nearly 30 years that have passed since its introduction, the ride has been anything but silky smooth, though the resultant product is a very satisfying one. Owners, it should be said, have pretty much always felt that way. There are options galore when it comes to buying one of these airplanes on the used market (as you’ll read in a bit), but Malibu/Mirage owners adore their airplanes, and rightly so.
When the Malibu was first introduced in 1983, it was very much the same airplane as it is today and a very different airplane, too.
Article Continues Below:
Aerobatics with Matt Chapman at Oshkosh 2016
Flying magazine met up with airshow performer Matt Chapman in Oshkosh for ...
The creation of the PA-46 was a risk that seemed worth taking when it was launched in the late 1970s. Piper, along with just about everyone else in aviation, was coming off a series of heady years in which tens of thousands of airplanes of every description were being sold — contrast this with today, when 2,000 airplanes is considered a big year.
There was probably no way for Piper to know that the Malibu would have as long a life as it’s turned out to have — even early airplanes are highly desirable and maintain their value well, thanks to a number of upgrade programs. Surely, there was no way for the company to know what struggles lay ahead. Those struggles included a few bankruptcies, several economic downturns and the complete transformation of the light general aviation market. Through them all, the PA-46 has been a steady performer for Piper.
The concept of the PA-46 was in many ways far from revolutionary. It was, after all, an all-metal pressurized six-seat cabin-class airplane. That was nothing that Piper or Cessna or Beech hadn’t been doing for decades. The big difference was that the Malibu was a piston single, and that was big news.
It wasn’t the first pressurized single. Mooney had a highly unsuccessful model, the M22 Mustang, of which only a handful were built. It had all the downsides of a Mooney of the day, with its small interior and limited visibility, but none of the upsides, including the great economy and excellent speed per weight. It was never a player.
The Cessna P210, on the other hand, was a big success. Cessna sold more than 800 of them, though it is not a cabin-class airplane, but rather a pressurized version of the 210, which was an outgrowth of previous Cessnas. And as much as folks like the P210 (and continue to like it), its speed and cabin paled in comparison to the Malibu, which was a clean-sheet design.
How Piper achieved those two critical goals — speed and cabin size — was not easy. The wing is beautiful, long and thin — 43 feet long in fact; be careful for signs and snow banks. The cabin was intended to compete with those of cabin class pressurized piston twins of the day, like the Cessna 421 or Beechcraft Duke, and it did just that, for single-engine pennies on the big-twin dollar.
The cabin is still recognizably a PA-46, but its barely-post-disco styling and sparse creature comforts make it look positively antique compared with the cabin of today’s airplane.
So it’s all too easy to forget what a trailblazer the Piper Malibu was. Today we take the concept of pressurized singles — even turboprop singles for granted, but in 1983 few pilots were ready to take that step. In his first review of the airplane in Flying,__ Richard Collins talked at length about the features a high-flying pressurized single would need to safely travel at the flight levels and he correctly identified several trouble spots for the airplane in the years to come — the exhaust and intake systems, the weather radar and the anti-icing system, which was de-activated on early airplanes waiting for FAA approval. Collins went so far as to suggest that if he had a Malibu, he might take it upon himself to get the system up and running pending FAA approval.
The airplane was outfitted with a beautiful King Silver Crown avionics package with full autoflight capability and flight director. The radar was indeed soon upgraded optionally to a wing-mounted pod from the unsatisfactory in-wing transmitter. Piper was listening. While the avionics system looks old fashioned by G1000 standards, it is still today a capable system.
The wonder of the Malibu was its economy. Collins reported that the airplane got nearly 200 knots on right around 17 gph. That was 20 knots faster on the same fuel flow as the P210 and with a much better cabin, the latter detail being my observation long after the fact.
What was the secret behind the economy? Well, the wing was a big part of it, and so was the 310 hp Continental six-cylinder TSIO-520 in the airplane. Designed to run efficiently while lean of peak, a foreign concept to many pilots of the day, the engine did just that, giving the Malibu a remarkable range, around 1,500 nm. Now, 310 horsepower doesn’t seem like much, and it isn’t. The Duke, for example, had 70 more horses … per side!
With the relatively modest engine, the Malibu suffered from marginal takeoff and initial climb performance compared with other single-engine airplanes.
But the bigger issue was heat, which Collins noted on his very first flight. The engine was remarkably unreliable, though whether that was a design or operator issue was and is hotly debated.
Eventually this led to Piper abandoning the Malibu and relaunching it with a whole new engine as the Malibu Mirage (the “Malibu” part being typically dropped from popular usage). The efficient Continental engine got swapped for a more powerful (350 hp) and slightly less fuel efficient Lycoming six-banger and the airplane received a number of other quality-of-life improvements, including a better anti-icing package (including a heated windshield to replace the hot-plate on the original), upgraded interior and improved avionics.
Still, there are people who prefer the original Malibu to the current airplane, thanks to its lighter weight, tremendous range and arguably better economy. There are, as you might know, a number of STCs available to upgrade the Malibu. You can even swap engines, substituting a Continental TSIO-550 for the ‘520 series engine, or even a Pratt turboprop, with the JetProp conversion.
Collins closed his piece by saying that, “Most of all, the engineers have given us an airplane that offers performance and comfort that people were only dreaming about for singles a few years ago. The Malibu is a remarkable achievement, and lessons learned in developing it will undoubtedly be put to good use in the development of other airplanes.”
Little did Collins know that those lessons would be applied to the Piper Malibu itself, and other PA-46s that would follow. Or maybe he did know.


Shiny New Diamond: Flying the DA62
Diamond’s new DA62 may well serve to reverse that trend. Skies magazine was invited to evaluate the innovative composite twin at Diamond Aircraft’s factory in London, Ont. The flight revealed an airplane that combines impressive cruise efficiency with unprecedented simplicity of operation and easy handling.
Anyone seeking to eulogize the light twin will no doubt quote two factors that purportedly led to its demise: fuel economy and safety. There is no question that it is more expensive to feed and service two powerplants, and today’s fuel prices will give anyone pause to think before buying an airplane with an “extra” engine.
Furthermore, the primary attraction of a twin-engine airplane is redundancy in the event of an engine failure; however, accident statistics have conclusively proven that a light twin is no safer than a single-engine airplane after an engine failure. Sure, there’s a second engine, but among the legacy piston twins the complex systems, tricky handling and marginal single-engine performance all erode the presumed safety margins.
Diamond Aircraft’s new all-composite DA62 fits a myriad of missions: twin-engine trainer, charter aircraft, corporate shuttle and personal transport. Production is being transferred from Diamond Austria to the plant in London, Ont.
The DA62 shines where legacy twins were weak.
Shiny New Diamond
It’s hard to identify the single coolest thing about the DA62, but its Austro Engine AE330 powerplants must be high on the list. They are liquid-cooled, four-cylinder, four-stroke compression-ignition designs, featuring common rail fuel injection, intercooled turbochargers and gear reduction, producing 180 horsepower.
That’s quite a hyphenated mouthful, but did you notice the “compression ignition” part? Yes, as in “diesel.” Diamond has been an industry leader in the development of jet fuel compression-ignition piston aircraft engines, and from my brief exposure to the DA62 I can understand the appeal. In addition to being smooth and quiet, their electrical engine control units (ECUs) perform digital magic that greatly simplifies engine management. Liquid cooling also eases operation by eliminating the risk of shock cooling. In further happy news, the overhaul interval (TBO) has recently been increased to 1,800 hours.
A notable advantage of the DA62’s novel engines is that they burn Jet A; a big benefit not only because jet fuel is typically cheaper, but because in some locales avgas is simply not available.
The cockpit is accessed via gull-wing doors that, together with the control sticks and interior layout, bring a high-end sports car to mind. Rob Erdos Photo
The DA62 shares a superficial similarity to Diamond’s other twin, the DA42; however, with seven seats it’s a completely different aircraft. Both cockpit seats are accessed via spacious gull-wing doors, plus a third on the left fuselage for access to the back seats. There is a 60/40 split flat-folding three-seat centre row and an optional third row incorporating two seats. I took a turn climbing into all of the seats, and found the combination of generously sized doors and ample hand-holds made it a breeze. Two forward baggage compartments, accessed via two small gull-wing doors on the nose, had a capacity of 66 pounds per side, simplifying management of the centre of gravity.
The DA62 features a 60/40 split flat-folding three-seat centre row and an optional third row incorporating two seats. Rob Erdos Photo
The optional equipment list provides considerable operator flexibility and includes air conditioning, 36-gallon auxiliary fuel tanks, weather radar, satellite datalink for weather and entertainment, and a TKS “weeping wing” anti-icing system certified for flight into known icing (FIKI). An upgrade to the latest Garmin G1000 NXi avionics system will also prove a popular option.
Climb Aboard
It was my privilege to fly the DA62 with Diamond’s chief pilot, Bill Scott. He compared the DA62 to a flying luxury SUV, but I was thinking sports car as I hefted myself up the trailing edge step and then lowered down into the sporty cockpit. The interior layout, gull-wing doors and control sticks in lieu of yokes conspired to whisper “Ferrari.” It’s the sort of airplane that makes you wish someone was taking a picture of you. Once settled, I found the seats comfortable and the field of view outstanding. The backrests and rudder pedals are adjustable.
Starting the DA62 was almost comically simple. Once the electrical master switch was selected on, the G1000 displays were online within about 30 seconds. Following a quick poke at some self-test buttons, the procedure called for the left engine master switch to be selected on, followed by a brief pause until the engine glow annunciator extinguished, after which the starter button was depressed. Vroom! The process was repeated with the other engine, and we were ready to taxi before I found a place to hide my pen.
The optional equipment list includes air conditioning, 36-gallon auxiliary fuel tanks, weather radar, satellite datalink for weather and entertainment, and a TKS “weeping wing” anti-icing system certified for flight into known icing (FIKI). An upgrade to the latest Garmin G1000 NXi avionics system will also be available.
The run-up check was similarly straightforward, after we had taxied for a few minutes to warm up the engine oil, coolant and gearbox temperatures. Run-up literally required two steps: depress the ECU test buttons and wait while the engines underwent a programmed test routine, then momentarily test each of the duplex ECUs with another switch. The absence of engine warning annunciations after the test indicated that we were good to go. The checks can be completed simultaneously, making the warm-up the longest part of the pre-flight routine.
It was a long taxi from Diamond’s factory to the active runway. I found that the pedals required nearly continuous small nudges to deflect a slightly stiff nosewheel steering mechanism, but otherwise taxiing was pleasant. The two engines sounded like distant sewing machines. Under all that glass, I was already in love with the air conditioner.
Our DA62, registration N628DC, serial number 38, had an empty weight of 3,749 pounds. We added two ostensibly adult humans, 66 pounds of gear, and seven gallons of TKS de-icing fluid, bringing our zero fuel weight to 4,257 pounds. Fuel onboard was about two-thirds of maximum capacity of 89 gallons, bringing our gross takeoff weight to 4,718 pounds. Maximum takeoff weight for the North American models is 5,071 pounds, which left an available payload of 360 pounds. From another perspective, our demonstrator aircraft had a very respectable full fuel payload of 717 pounds, notwithstanding that it was carrying a generous list of options.
Smooth Cruising
It was a perfect day for a test flight, with a quartering crosswind of 15 knots, gusting to 20, as we lined up on London’s Runway 15. Full throttle yielded an ECU-regulated 100 per cent power; however, upon advancing the throttles I recall mild confusion because the ample acceleration didn’t seem to be accompanied by enough noise. Among their other virtues, the Austro diesel engines are quiet!
Diamond’s DA62 boasts impressive cruise efficiency. During the test flight, fuel flow was just 9.4 gallons of Jet A per engine, per hour. Diamond Aircraft Photo
The published takeoff distance at maximum takeoff weight under sea level standard conditions is 1,574 feet with the flaps set to the takeoff position. The DA62 is also approved for operation from unimproved strips.
I used the recommended cruise-climb airspeed of 120 knots indicated airspeed (KIAS), which resulted in slightly better than 1,000 feet per minute climb rate. I selected the Flight Level Change mode and watched the GFC 700 autopilot smoothly climb through mild turbulence with less than a two knot speed variation. Nice.
We levelled off at 10,000 feet (2C air temperature) and 95 per cent power, letting the slippery twin accelerate until we were rewarded with 188 knots true airspeed (KTAS, or 160 KIAS).
Test pilot Rob Erdos was a fan of the DA62’s conventional stick and throttle arrangement, finding control response pleasant for hand flying, with just a bit of adverse yaw in evidence at low speeds.
If the reader needs a gentle prod when I reach the punchline, this is it: Our fuel flow was 9.4 gallons per hour of Jet A per engine! I simply cannot imagine another production twin-engine airplane that can approach the DA62’s impressive cruise efficiency.
Higher altitudes or lower power settings offer even more efficient cruising options. The certified ceiling for normal operations is 20,000 feet. For example, at 16,000 feet, standard conditions and realistic operating weights, a 75 per cent power setting yields a published speed of 177 KTAS burning 14.8 gallons per hour. On missions where endurance is the objective, a 50 per cent power setting delivers 144 KTAS and 9.7 gallons per hour. With a published no reserve maximum range of 1,345 nautical miles, or a maximum endurance of 9.5 hours, full fuel tanks in the DA62 broaden one’s options.
Skies test pilot Rob Erdos, right, with Diamond chief pilot Bill Scott.
Looking around the DA62’s tidy cockpit, I was struck by what was missing. In lieu of the usual forest of knobs and levers–throttle, propeller speed, mixture, cowl flaps, carburetor heat, magnetos–the DA62’s engine controls consisted of a power lever and an engine master switch. Propeller speeds were set and synchronized by the ECUs. Mixture control was automatic, as was everything else. It was simplicity itself. One can hardly wish for less.
Handling
Advertisement
We found a few minutes to assess the DA62’s handling. I was a big fan of the conventional stick and throttle arrangement, even in a twin, and found the controls all fell comfortably to hand. Control response was pleasant for hand flying, with just a bit of adverse yaw in evidence at low speeds. I found the rudder forces firm.
We did a few power-off stalls in various configurations. They were uniformly benign, with a gradual crescendo of airframe and control buffeting, in addition to the mandatory lights and tones, to awaken even the most obtuse pilots. At our loading condition, I could comfortably sustain full aft stick while retaining adequate lateral control.
Diamond has described its DA62 as a “flying SUV,” in large part due to its spacious cabin which offers optional three-row, seven-passenger seating.
Scott talked me through an engine shut-down. The procedure was as follows: Shut off the switch. Okay. I wanted to simulate a worst-case engine failure on takeoff, so I applied full power with the speed still low following a practice stall in the takeoff configuration. Passing the normal rotation speed of 80 KIAS, I selected the critical left engine master switch off. Faster than I could say, “identify, verify, feather,” the engine shut down and the propeller feathered. The transition to a single-engine climb at the recommended 87 KIAS presented no undue challenges. Again, rudder forces were high, but trim authority was sufficient. The certified single-engine ceiling is 13,000 feet.
En route back to London, Scott made quick work of the set-up for an autopilot coupled instrument approach on the Garmin G1000 avionics suite. I used the opportunity to feign distraction, allowing our roll attitude to increase toward a dangerous spiral divergence. Fortunately, the G1000’s Electronic Stability Protection (ESP) system was paying attention, activating to gently nudge the controls back toward a safer flight regime; an invaluable safety feature in a light airplane.
All too soon, the DA62’s solid trailing link undercarriage lowered us onto the runway at London. It speaks well of an airplane when I need to consciously restrain myself from adding power and taking it around the pattern again. I was smiling. In the DA62, there’s a lot to like.
Utilitarian Efficiency
I foresee the DA62 fitting into myriad missions. Given its jet-like operating simplicity, the DA62 would be an ideal twin-engine trainer for those pilots intent upon flying “grown up” airplanes.
The DA62’s engine controls consist of a power lever and an engine master switch. It is simplicity itself.
With seven seats, it’s certainly not the cheapest dedicated trainer, but some operators will appreciate an aircraft with legitimate charter capability. It would make an ideal light corporate shuttle, especially for flight departments with mixed fleets where the crews have all but forgotten concepts like cowl flaps and mixture controls, since its operation is “turbine simple.”
Skip to content Home News Features Press Releases Subscribe Search no alt text set What's Inside Our 2017 Photo Contest issue serves up some of the best images yet! Plus, we examine the Bombardier/Airbus deal. More inside. Read More Buy Now skies Digital Edition Sign up for your free Digital Alert from Skies magazine. skies Daily News Sign up for free daily email updates from the aviation industry’s top news source. Skies Magazine Since its debut, Skies has quickly gained a loyal and escalating following for its fresh approach to covering North American aviation and aerospace news. Each issue is packed with insightful stories, news, reports and feature profiles from all sectors of aviation! no alt text set no alt text set Subscribe Today View Past Issues Search no alt text set no alt text set Read More Purchase Now Shop Shop Canada Shop International Browse Digital Edition Wallpapers Insight Calendars Photo of the week 2018 Media Kit Categories Airline Airport Avionics Business Aviation Faces of Flight Flight Test News From the Web Categories Helicopters Instrument IQ Military NBAA Press Releases Training and Simulation Diamond Aircraft’s new all-composite DA62 fits a myriad of missions: twin-engine trainer, charter aircraft, corporate shuttle and personal transport. Production is being transferred from Diamond Austria to the plant in London, Ont., with the Canadian branch converting the type certificate to Transport Canada authority, a process it hopes to conclude by mid-November 2017. Photos by Eric Dumigan Shiny New Diamond: Flying the DA62 Posted on July 20, 2017 by Robert Erdos The years haven’t been kind to the light piston twin. Several decades ago, in the heyday of general aviation manufacturing, there were dozens of light piston-powered twin-engine airplanes on the market. Today, there are but a few. The DA62's Austro Engine AE330 180-horsepower powerplants are liquid-cooled, four-cylinder, four-stroke compression ignition designs. Yes, The DA62’s Austro Engine AE330 180-horsepower powerplants are liquid-cooled, four-cylinder, four-stroke compression ignition designs. Yes, “compression ignition,” as in diesel. Photos by Eric Dumigan Advertisement Diamond’s new DA62 may well serve to reverse that trend. Skies magazine was invited to evaluate the innovative composite twin at Diamond Aircraft’s factory in London, Ont. The flight revealed an airplane that combines impressive cruise efficiency with unprecedented simplicity of operation and easy handling. Anyone seeking to eulogize the light twin will no doubt quote two factors that purportedly led to its demise: fuel economy and safety. There is no question that it is more expensive to feed and service two powerplants, and today’s fuel prices will give anyone pause to think before buying an airplane with an “extra” engine. Furthermore, the primary attraction of a twin-engine airplane is redundancy in the event of an engine failure; however, accident statistics have conclusively proven that a light twin is no safer than a single-engine airplane after an engine failure. Sure, there’s a second engine, but among the legacy piston twins the complex systems, tricky handling and marginal single-engine performance all erode the presumed safety margins. Diamond Aircraft's new all-composite DA62 fits a myriad of missions: twin-engine trainer, charter aircraft, corporate shuttle and personal transport. Production is being transferred from Diamond Austria to the plant in London, Ont., with the Canadian branch converting the type certificate to Transport Canada authority, a process it hopes to conclude by mid-November 2017. Photos by Eric Dumigan Diamond Aircraft’s new all-composite DA62 fits a myriad of missions: twin-engine trainer, charter aircraft, corporate shuttle and personal transport. Production is being transferred from Diamond Austria to the plant in London, Ont. The DA62 shines where legacy twins were weak. Shiny New Diamond It’s hard to identify the single coolest thing about the DA62, but its Austro Engine AE330 powerplants must be high on the list. They are liquid-cooled, four-cylinder, four-stroke compression-ignition designs, featuring common rail fuel injection, intercooled turbochargers and gear reduction, producing 180 horsepower. That’s quite a hyphenated mouthful, but did you notice the “compression ignition” part? Yes, as in “diesel.” Diamond has been an industry leader in the development of jet fuel compression-ignition piston aircraft engines, and from my brief exposure to the DA62 I can understand the appeal. In addition to being smooth and quiet, their electrical engine control units (ECUs) perform digital magic that greatly simplifies engine management. Liquid cooling also eases operation by eliminating the risk of shock cooling. In further happy news, the overhaul interval (TBO) has recently been increased to 1,800 hours. A notable advantage of the DA62’s novel engines is that they burn Jet A; a big benefit not only because jet fuel is typically cheaper, but because in some locales avgas is simply not available. The cockpit is accessed via gull-wing doors that, together with the control sticks and interior layout, bring a high-end sports car to mind. Rob Erdos Photo The cockpit is accessed via gull-wing doors that, together with the control sticks and interior layout, bring a high-end sports car to mind. Rob Erdos Photo The DA62 shares a superficial similarity to Diamond’s other twin, the DA42; however, with seven seats it’s a completely different aircraft. Both cockpit seats are accessed via spacious gull-wing doors, plus a third on the left fuselage for access to the back seats. There is a 60/40 split flat-folding three-seat centre row and an optional third row incorporating two seats. I took a turn climbing into all of the seats, and found the combination of generously sized doors and ample hand-holds made it a breeze. Two forward baggage compartments, accessed via two small gull-wing doors on the nose, had a capacity of 66 pounds per side, simplifying management of the centre of gravity. The DA62 features a 60/40 split flat-folding three-seat centre row and an optional third row incorporating two seats. Rob Erdos Photo The DA62 features a 60/40 split flat-folding three-seat centre row and an optional third row incorporating two seats. Rob Erdos Photo The optional equipment list provides considerable operator flexibility and includes air conditioning, 36-gallon auxiliary fuel tanks, weather radar, satellite datalink for weather and entertainment, and a TKS “weeping wing” anti-icing system certified for flight into known icing (FIKI). An upgrade to the latest Garmin G1000 NXi avionics system will also prove a popular option. Climb Aboard It was my privilege to fly the DA62 with Diamond’s chief pilot, Bill Scott. He compared the DA62 to a flying luxury SUV, but I was thinking sports car as I hefted myself up the trailing edge step and then lowered down into the sporty cockpit. The interior layout, gull-wing doors and control sticks in lieu of yokes conspired to whisper “Ferrari.” It’s the sort of airplane that makes you wish someone was taking a picture of you. Once settled, I found the seats comfortable and the field of view outstanding. The backrests and rudder pedals are adjustable. Starting the DA62 was almost comically simple. Once the electrical master switch was selected on, the G1000 displays were online within about 30 seconds. Following a quick poke at some self-test buttons, the procedure called for the left engine master switch to be selected on, followed by a brief pause until the engine glow annunciator extinguished, after which the starter button was depressed. Vroom! The process was repeated with the other engine, and we were ready to taxi before I found a place to hide my pen. The optional equipment list includes air conditioning, 36-gallon auxiliary fuel tanks, weather radar, satellite datalink for weather and entertainment, and a TKS The optional equipment list includes air conditioning, 36-gallon auxiliary fuel tanks, weather radar, satellite datalink for weather and entertainment, and a TKS “weeping wing” anti-icing system certified for flight into known icing (FIKI). An upgrade to the latest Garmin G1000 NXi avionics system will also be available. The run-up check was similarly straightforward, after we had taxied for a few minutes to warm up the engine oil, coolant and gearbox temperatures. Run-up literally required two steps: depress the ECU test buttons and wait while the engines underwent a programmed test routine, then momentarily test each of the duplex ECUs with another switch. The absence of engine warning annunciations after the test indicated that we were good to go. The checks can be completed simultaneously, making the warm-up the longest part of the pre-flight routine. It was a long taxi from Diamond’s factory to the active runway. I found that the pedals required nearly continuous small nudges to deflect a slightly stiff nosewheel steering mechanism, but otherwise taxiing was pleasant. The two engines sounded like distant sewing machines. Under all that glass, I was already in love with the air conditioner. Our DA62, registration N628DC, serial number 38, had an empty weight of 3,749 pounds. We added two ostensibly adult humans, 66 pounds of gear, and seven gallons of TKS de-icing fluid, bringing our zero fuel weight to 4,257 pounds. Fuel onboard was about two-thirds of maximum capacity of 89 gallons, bringing our gross takeoff weight to 4,718 pounds. Maximum takeoff weight for the North American models is 5,071 pounds, which left an available payload of 360 pounds. From another perspective, our demonstrator aircraft had a very respectable full fuel payload of 717 pounds, notwithstanding that it was carrying a generous list of options. Smooth Cruising It was a perfect day for a test flight, with a quartering crosswind of 15 knots, gusting to 20, as we lined up on London’s Runway 15. Full throttle yielded an ECU-regulated 100 per cent power; however, upon advancing the throttles I recall mild confusion because the ample acceleration didn’t seem to be accompanied by enough noise. Among their other virtues, the Austro diesel engines are quiet! Diamond's DA62 boasts impressive cruise efficiency. During the test flight, fuel flow was just 9.4 gallons of Jet A per engine, per hour. Diamond Aircraft Photo Diamond’s DA62 boasts impressive cruise efficiency. During the test flight, fuel flow was just 9.4 gallons of Jet A per engine, per hour. Diamond Aircraft Photo The published takeoff distance at maximum takeoff weight under sea level standard conditions is 1,574 feet with the flaps set to the takeoff position. The DA62 is also approved for operation from unimproved strips. I used the recommended cruise-climb airspeed of 120 knots indicated airspeed (KIAS), which resulted in slightly better than 1,000 feet per minute climb rate. I selected the Flight Level Change mode and watched the GFC 700 autopilot smoothly climb through mild turbulence with less than a two knot speed variation. Nice. We levelled off at 10,000 feet (2C air temperature) and 95 per cent power, letting the slippery twin accelerate until we were rewarded with 188 knots true airspeed (KTAS, or 160 KIAS). Test pilot Rob Erdos was a fan of the DA62's conventional stick and throttle arrangement, finding control response pleasant for hand flying, with just a bit of adverse yaw in evidence at low speeds. Test pilot Rob Erdos was a fan of the DA62’s conventional stick and throttle arrangement, finding control response pleasant for hand flying, with just a bit of adverse yaw in evidence at low speeds. If the reader needs a gentle prod when I reach the punchline, this is it: Our fuel flow was 9.4 gallons per hour of Jet A per engine! I simply cannot imagine another production twin-engine airplane that can approach the DA62’s impressive cruise efficiency. Higher altitudes or lower power settings offer even more efficient cruising options. The certified ceiling for normal operations is 20,000 feet. For example, at 16,000 feet, standard conditions and realistic operating weights, a 75 per cent power setting yields a published speed of 177 KTAS burning 14.8 gallons per hour. On missions where endurance is the objective, a 50 per cent power setting delivers 144 KTAS and 9.7 gallons per hour. With a published no reserve maximum range of 1,345 nautical miles, or a maximum endurance of 9.5 hours, full fuel tanks in the DA62 broaden one’s options. Skies test pilot Rob Erdos, right, with Diamond chief pilot Bill Scott. Skies test pilot Rob Erdos, right, with Diamond chief pilot Bill Scott. Looking around the DA62’s tidy cockpit, I was struck by what was missing. In lieu of the usual forest of knobs and levers–throttle, propeller speed, mixture, cowl flaps, carburetor heat, magnetos–the DA62’s engine controls consisted of a power lever and an engine master switch. Propeller speeds were set and synchronized by the ECUs. Mixture control was automatic, as was everything else. It was simplicity itself. One can hardly wish for less. Handling Advertisement We found a few minutes to assess the DA62’s handling. I was a big fan of the conventional stick and throttle arrangement, even in a twin, and found the controls all fell comfortably to hand. Control response was pleasant for hand flying, with just a bit of adverse yaw in evidence at low speeds. I found the rudder forces firm. We did a few power-off stalls in various configurations. They were uniformly benign, with a gradual crescendo of airframe and control buffeting, in addition to the mandatory lights and tones, to awaken even the most obtuse pilots. At our loading condition, I could comfortably sustain full aft stick while retaining adequate lateral control. Diamond has described its DA62 as a Diamond has described its DA62 as a “flying SUV,” in large part due to its spacious cabin which offers optional three-row, seven-passenger seating. Scott talked me through an engine shut-down. The procedure was as follows: Shut off the switch. Okay. I wanted to simulate a worst-case engine failure on takeoff, so I applied full power with the speed still low following a practice stall in the takeoff configuration. Passing the normal rotation speed of 80 KIAS, I selected the critical left engine master switch off. Faster than I could say, “identify, verify, feather,” the engine shut down and the propeller feathered. The transition to a single-engine climb at the recommended 87 KIAS presented no undue challenges. Again, rudder forces were high, but trim authority was sufficient. The certified single-engine ceiling is 13,000 feet. En route back to London, Scott made quick work of the set-up for an autopilot coupled instrument approach on the Garmin G1000 avionics suite. I used the opportunity to feign distraction, allowing our roll attitude to increase toward a dangerous spiral divergence. Fortunately, the G1000’s Electronic Stability Protection (ESP) system was paying attention, activating to gently nudge the controls back toward a safer flight regime; an invaluable safety feature in a light airplane. All too soon, the DA62’s solid trailing link undercarriage lowered us onto the runway at London. It speaks well of an airplane when I need to consciously restrain myself from adding power and taking it around the pattern again. I was smiling. In the DA62, there’s a lot to like. Utilitarian Efficiency I foresee the DA62 fitting into myriad missions.

We Fly: Diamond DA62
With a single, obviously, there's only one engine to care for, and the chances of it quitting are low — and if it does quit in the Cirrus, there's a full-airframe parachute to save the day.
That's what makes the emergence of an all-new light-piston twin in this class something of a surprise. With the elegantly sculpted DA62's arrival amid a field of brawny gasoline-powered singles, suddenly we have to ask ourselves if the market for twins isn't quite as dead as we thought. Perhaps it has merely been in a state of prolonged hibernation, slumbering peacefully through a long winter, awaiting the arrival of a new kind of light twin, one that can do more with less.
In developing this airplane, Diamond Aircraft founder and CEO Christian Dries challenged his team to create a simple-to-operate, fuel-efficient twin and wrap it around a passenger compartment mimicking the latest luxury SUVs.
Still, it's not quite time to announce a comeback for the piston twin segment. The DA62 is an anomaly, an outlier. After all, most pilots coming up through the ranks today who aren't dreaming of an airline career feel no pressing urge to “move up” to a twin. Those who used to — the pilots who flew twin-engine bombers in World War II and trusted two engines more than one — have all but stopped flying and, for the most part, offering advice to younger pilots.
The resulting shift in attitudes and buying habits in favor of single-engine airplanes is clear. In the late 1970s, for example, there were 33 different piston twins on the market. Today, there are only five serious contenders — and apart from the seven-place DA62, only two of these, the Beech Baron G58 and Piper Seneca V, offer more than four seats.
A Flying SUV
Seven seats in a twin in this class, by the way, is quite an engineering feat. I'm not a fan of describing any airplane as an “aerial SUV” — even if, yes, it's roomy inside and has a decent payload — because the label is almost always an exaggeration dreamed up by someone in the marketing department. But in the case of the DA62 it would be ignoring a glaringly obvious design characteristic not to mention it. With its third-row seating option, oversize doors and seats that fold flat to accommodate bulky items, there's no other way to say it — the DA62 is a sport utility vehicle with wings.
That's no accident. In developing this airplane as an evolutionary step up from the four-seat DA42, Diamond Aircraft founder and CEO Christian Dries challenged his engineering team to create a safe, simple-to-operate, fuel-efficient twin and wrap it around a passenger compartment mimicking the latest luxury SUVs. Unlike gas-guzzling sport utility vehicles, though, the DA62 boasts outstanding fuel economy. Its twin 180-horsepower Austro AE330 diesel engines burn less than 10 gallons per hour per side at maximum continuous power, propelling the airplane to a top speed of right around 200 knots. Pull the throttles back to 75 percent power and the speed is still a respectable 187 ktas, but fuel burn drops to just 7.4 gph per side — an impressive 14.8 gph total that's lower than a number of light-piston singles can manage on one engine.
The DA62's cabin features two seats up front, three in the middle row and two more in back. They fold flat for an SUV-like experience.
Florian Pfaffstaller
I had the chance to spend a couple of days flying the DA62 recently on a visit to the Diamond Aircraft factory at the company-owned Wiener Neustadt East Airport south of Vienna. I came away from the experience persuaded that, for the right buyer, this is very nearly the ideal airplane. If, for example, you need seven seats versus the five or six offered in competing airplanes, the DA62 makes perfect sense. If you also don't have access to a ready supply of 100LL avgas, the DA62 is a great alternative to gasoline-powered models. And if you simply feel more comfortable flying over inhospitable terrain or water, sometimes at night, and desire the power and systems redundancy that come with a second engine, the DA62 should absolutely be on your shopping list.
There are other reasons to like the DA62 as well. One of the characteristics that left an impression on me is how dirt simple this airplane is to operate. Take the engine start procedure, for example. It involves the easy-as-pie steps of hitting the master switch, flipping the engine master on, waiting a moment to ensure the glow plug annunciation is out and then pushing the engine start button. That's it. The Austro diesels come to life in an instant as the dual-channel full authority digital engine controls (fadec) manage rpm and continuously check for faults while your only other job is to glance at the oil pressure indication. As long as the gauges are in the green, you're good to go.
The before-takeoff run-up procedure is equally as stress free. It involves setting the parking brake, manually selecting the A and B channels of the electronic engine control units (EECU) to ensure both are online, and then pushing and holding the engine run-up buttons. Here's where the magic starts as the AE330's fadec computers automatically increase power to 1,950 rpm and perform a number of health checks, including cycling the props. The throttles never physically move and there aren't any prop levers to move in the first place. If no fault messages appear on the Garmin G1000 primary flight display when the test sequence is completed, you're ready for departure.
In this case, that meant swinging the airplane onto Wiener Neustadt's Runway 10 with a 25-knot direct crosswind blowing from the left. I added a fistful of that smooth diesel power and, per the book, rotated at 80 knots. Acceleration to 95 knots for the climb-out was brisk as I began the bizarre sequence of noise-abatement twists and turns designed to keep air traffic away from residential areas as well as a military airfield right next door to the airport.
The DA62's diesel engines are encased in cowlings that seem oddly misshapen, a result of packaging Mercedes-Benz car engines on an airplane.
Florian Pfaffstaller
Climbing to 5,000 feet at 110 kias, the DA62 maintained a 1,450 fpm rate of climb at our midweight with two on board and half fuel. Accelerating to a cruise climb speed of 128 kias produced a 1,200 fpm rate through 8,000 feet. That's when I asked my host in the right seat, Diamond Aircraft director of flight operations Martin Scherrer, for a demonstration of the DA62's single-engine performance. Still climbing, at his direction I flicked off the left engine master switch (the left is the critical engine in the DA62). The propeller immediately stopped, automatically feathering as it did so.
The airplane lurched left as a result of loss of thrust on that side, and I instinctively raised the left wing, stepped on the rudder, and then dialed in rudder trim to compensate. After that, the airplane was as easy to fly on one engine as on two. Earning a multiengine rating in a DA62 with its two power levers (opposed to the usual six levers found in most piston twins) would almost be cheating, I decided. I let the speed come back to the 87-knot blue line (single-engine best rate-of-climb airspeed) and was impressed to see us still climbing at 450 fpm.
Speed Test
Next I wanted to evaluate the DA62's cruise performance to see if this really is a 200-knot airplane as Dries originally envisioned. I leveled off at 14,000 feet with the throttles pushed full forward to max continuous power of 95 percent and let the speed build. On this day, slightly warmer than standard and a little lower than optimal, I managed to coax 195 ktas from those twin AE330s while burning 18.6 gph. Hitting 200 knots in a Beech Baron in similar conditions would result in a fuel consumption of around 30 gph, so I wasn't terribly disappointed with the results I was seeing.
I tried out a variety of power settings and found what I considered a sweet spot at 60 percent power showing 170 ktas and 11.8 gph fuel consumption. After heading lower and trying a series of steep turns and power-on and -off stalls (which were, predictably, nonevents with nothing more dramatic than a slight wing drop in the stalls), I shut down the right engine for some engine-out maneuvering. Here's where the economy really improved. Loafing along at 100 knots in level flight we were showing a fuel burn of an eye-popping 3.6 gph. I did a quick mental calculation and realized that, even with less than half fuel on board, at this rate our flight endurance would still be more than 11 hours.
There would be virtually no way to stave off boredom on such a long flight, in part because the pilot doesn't have much to do in the DA62 in cruise. By design, pilot workload is low in all flight regimes, something I think nonprofessionals will come to greatly appreciate. Even performing aerial engine restarts is an almost total no-brainer for the pilot. The single-lever power controls don't require any special adjustments, meaning all the pilot has to worry about is maintaining the proper airspeed so the prop will windmill back to life when the engine master is switched back on.
In fact, fitted as it is with the latest generation of Garmin G1000 avionics with synthetic-vision technology (SVT) and electronic stability and protection (ESP), plus a three-axis Garmin GFC 700 autopilot and GWX 70 weather radar, there's an argument to be made that the DA62 is the among the most capable and easiest-to-fly piston airplanes ever produced. It's a 21st century technological marvel wrapped in a slippery and sensual carbon-fiber package.
Diamond DA62 in flight.
Florian Pfaffstaller
After a sightseeing detour through some breathtakingly gorgeous valleys in the Alps southwest of Vienna (where handling in the bumps was rock solid), we headed back to Wiener Neustadt so I could try my hand at landings in the DA62. The wind was still blowing at 20 knots for my first arrival, which involved flying the strangest pattern I've ever performed as I was compelled to wheel around small towns at odd altitudes to accommodate for departing traffic and the bordering military airspace.
The landing culminated with a tight descending turn at the edge of the adjacent military airfield as I targeted 90 knots on final with full flaps selected. Max demonstrated crosswind component with full flaps in the DA62 is 25 knots, slightly better than in the DA42, and I found that the DA62 handled the wind with no problem, even with its slender wing spanning nearly 48 feet.
Creature Comforts
Inside, the DA62 has the same center control stick, throttle placement and cockpit display layout that are familiar to pilots of the Diamond DA40 and DA42. Round-dial backup instruments have been replaced with an electronic standby instrument with emergency battery. The seats are leather with seatback adjustments, but they don't move fore and aft. Instead, the rudder pedals can be adjusted forward and back to accommodate a variety of pilots. I found that I had plenty of headroom and adequate forward visibility from my vantage point in the left seat. My companion in the right seat, at 6 feet, 8 inches tall, fit the space surprisingly well. A welcome touch is an armrest in the center of the cockpit between the pilots that is just the right width and height.
Diamond was the first to commit to Garmin G1000 avionics, so it's no surprise to find it carried over here.
Florian Pfaffstaller
The DA62's three large gull-wing doors and the forward-folding seats, plus smart placement of handholds, make entry and exit from the DA62 extremely easy. There are cup holders for the front-seat occupants and a variety of LED interior lighting options throughout the cabin. Options include air conditioning, a 36-gallon aux fuel tank, Garmin weather radar and satellite data receiver, and Avidyne TAS600 traffic advisory system. New for the DA62 is an upgraded metallic paint option that lets buyers choose colors other than the standard white found on many carbon-composite aircraft.
Although it isn't offered with a parachute, the DA62 benefits from a variety of standard and optional safety features. Its benign, big-airplane handling makes it easy to hand-fly. It also features aluminum fuel tanks sandwiched between the carbon-fiber main wing spars for exceptional crashworthiness, and incorporates Diamond's trademark high-impact fixed seats that are attached to strategically located crush points in the floor. The composite monocoque cabin design was borrowed from the Formula 1 racing world. Like all Diamond products, the airplane has undergone crashworthiness testing similar to what is performed in the auto industry. The DA62 also offers full icing protection with its TKS weeping wing option.
The U.S. spec version that goes on sale this month offers a 5,071-pound gross weight (versus 4,400 pounds for the European version to avoid the ATC fees levied on heavier airplanes) and a 1,300-nautical-mile range with a full-fuel payload of over 1,000 pounds. Its 2.0-liter Austro compression ignition engines, meanwhile, sip jet-A fuel while offering the peace of mind that comes with a 13,000-foot single-engine service ceiling (at max gross weight) and the turbocharged power to propel it to respectable top speed. The cabin is the roomiest in its class, plus there are two spacious baggage compartments in the nose that can accommodate full-size suitcases, golf bags and more.
One of the big questions I had about the DA62, obviously, is whether this really is a bona fide seven-person airplane with those two extra seats way in the back. There's ample room in the front seats and in the middle row as well with its three seats, but the rear seats would be cramped for two adults. I hopped in back and felt there was plenty of room for me alone, but I wouldn't want a seatmate. It would be ideal, though, for two children.
The DA62's useful load in the international spec version is 1,609 pounds — about 100 pounds more than a Baron G58 — meaning that with half fuel the average weight of each passenger could top out at around 190 pounds. I ran through a number of weight and balance scenarios and came away convinced that with those fuel-efficient Austro diesels, this truly is a seven-person airplane that still offers decent range and speed. A real-world scenario I plugged in involved loading five full-size adults, two children, bags and 60 gallons of fuel for a 644 nm range at standard cruise power at 14,000 feet.
At $1.08 million for the U.S. model before typical options, the DA62 compares well with the competition, slotting in above the price of a new Piper Seneca V and below the Baron G58. What could give some buyers pause is the short engine overhaul interval, which at the moment is a mere 1,000 hours for the new Austro AE330s. Based on the Mercedes-Benz diesels in B-class automobiles, the engine is a proven design, and the 1,000-hour limitation is projected to be short-lived as Diamond gains experience with the aero engine. The company hopes to increase TBO to as high as 2,400 hours eventually. Other required engine maintenance, meanwhile, includes inspection of the generators at 300 hours, and replacement of the high-pressure fuel pump and inspection of the two-mass flywheel at 600 hours.
The DA62 earned its type certification in Europe last April and should have received its Part 23 approval papers from the FAA by the time you read this. Sales are slated to begin in North America before the end of the year, meaning it won't be long before you start seeing the DA62 appear on airport ramps.
With its long, tapered high-aspect ratio wing featuring slightly upswept tips, unusual engine cowl shape and silky-smooth composite fuselage, it'll be hard to miss. Once you see it in person, it will probably take all of about five seconds before you decide you want to fly it. It's an experience I highly recommend, but don't be surprised if you suffer from a serious case of twin envy afterward.
Spec Box
The Diamond DA62 flown for this report was an international spec model with optional third-row seating accommodating seven people, increased 5,071-pound maximum takeoff weight, built-in oxygen, air conditioning, TKS icing protection, Garmin GWX 70 weather radar and GSR 56 satellite data receiver, Avidyne TAS600 traffic advisory system, 36-gallon auxiliary fuel tank, metallic paint and more.
2016 Diamond DA62
Standard price$1.08 million
Price as tested$1.24 million
EngineAustro Engines AE330 (2 x 180 hp)
PropsMT 3-blade (2 x 76 inches)
Length30 feet 1 inch
Height9 feet 3 inches
Wingspan47 feet 10 inches
Wing area184.1 square feet
Wing loading27.54 pounds per square foot
Power loading14.08 pounds per hp
Max takeoff weight5,071 pounds
Standard empty weight3,461 pounds
Max useful load1,609 pounds
Payload with full fuel1,021 pounds
Max usable fuel86.4 gallons (with aux tanks)
Max rate of climb1,346 feet per minute
Single-engine rate of climb288 feet per minute
Service ceiling20,000 feet
Max speed204 kias
Cruise speed(14,000 feet, max cont. power) 193 kias
Max range1,275 nautical miles
Stall speed (clean)70 kias
Stall speed (full flaps)64 kias
Takeoff distance1,265 feet
Takeoff distance over 50 feet2,097 feet
Landing distance1,259 feet
Stunning from every angle, we couldn’t resist showing off the DA62's sensuous underbelly on our photo flight over the Austrian alps.
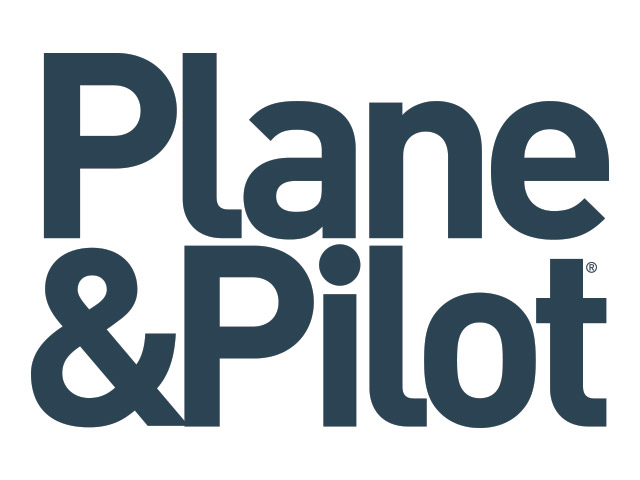
Ultimate Piston Twin: Diamond DA62
I know that other aviation journalists have described the “sleek” and “sexy” look of the new DA62, but that’s not how it strikes me at all. With its long, angular and jutting lines, the DA62 looks to me more like a scorpion than a swallow, and if fate is kinder to Diamond Aircraft with this product introduction, it might just wind up being that kind of silent stalker. The prey, in this case, could be the high-end, high-performance single-engine airplane.
The Diamond DA62 is the only next-generation piston twin. Unlike mature all-metal products from Beechcraft and Piper, the DA62 takes innovative approaches to propulsion, with its economical and fuel-smart Jet-A diesels and materials, including all-carbon-fiber construction.
It’s been a while since the well-heeled personal transportation pilot was tempted to look seriously at twin-engine airplanes when looking to get into a late-model speedster. With the arrival of the DA62, a fast, roomy, utilitarian and technologically capable plane, the choice is there, just as it was 50 years ago when buyers looked with equal interest at Beech Barons and Cessna Centurions. The DA62, in some ways, restarts that conversation because it brings to the table one element that the B58 Baron or Cessna 421 couldn’t: economy.
Flying the Diamond DA62 out of San Marcos, Texas.
Rough Ride
Since its inception 20 years ago, Diamond has prided itself on doing things differently, not for the sake of doing them differently, but for the sake of doing them right. Diamond innovated in terms of materials, including carbon fiber, which it used in increasing amounts as its models became more advanced; with crashworthiness; with 26-G seats, seatbelt airbags and a carbon-fiber cage; with quiet flight; with a high-aspect-ratio wing and quiet engine/prop combinations; and, of course, with the engines themselves, helping drive the development of the first modern aviation diesel engine, the Thielert Centurion, and then, when Thielert failed, creating its own company, Austro Engine, to take up the mantle of the aero diesel.
The Diamond twin has a long heritage. The original, the TwinStar, was developed in the early 2000s and earned FAA approval in 2005. The plane was the first Diamond in any number to be powered by a diesel engine, a technology that the company had eyed from the start as making a lot of sense, not only for its primary intended market, Europe, where 100LL is exorbitantly priced, but for the future when regulators might put a stop to the production of the world’s only leaded gasoline. While the Jet-A Thielert engines were very impressive in a number of ways, including consuming a remarkably small amount of fuel per hour (around 4 gph at typical training power levels), they proved prohibitively expensive to maintain. Of chief concern were the gearboxes that turned down the rpms of the engine to a more usable prop speed. The complex mechanical boxes needed to be removed and sent back to the factory in Germany after only a couple hundred hours and at a cost that made 100LL look like a bargain.
As is universal with Diamond aircraft, the wingspan of the DA62, at nearly 48 feet, is sailplane-like in both length and aspect ratio. The effect is excellent climbing ability and fuel efficiency.
Eventually, Diamond stopped production of the DA42, Thielert entered insolvency (the German equivalent of bankruptcy) amid financial improprieties, and the future looked dark for the TwinStar. Sadly, after Diamond had created its own sibling company to manufacture engines for its diesel birds, the global financial crisis hit and Diamond was thrown for a loop once again.
The good news is that the DA62 looks like it could be the medicine that the doctor ordered to get Diamond back up on its feet again. The DA42, by the way, is back in production with its own Austro engine.
Diamond chose to stick with the G1000 platform, adding a center-mounted Mid-Continent self-powered standby instrument. Another commonality in Diamonds: sticks.
I earned my multi-engine rating in the four-seat DA42 at Europe-American Aviation in Naples, Florida, 10 years ago now, and I remember every moment. The DA42 was, as advertised, a great little twin, but with just 135 hp per side, it was a bit anemic. Its single-engine rate of climb was weak, and the plane’s single-engine handling, while good, took a lot of force. My leg would often give out before the lesson did.
The addition of the 168 hp Austro AE-300-series engines to the DA42, resulting in a new model Diamond called the DA42 NG (for, you guessed it, Next Generation), brought a level of performance that made it not only an improved trainer, but a viable personal transportation platform, too. Still, most of the orders that Diamond got for the DA42 were from flight schools, and for good reason. The savings a busy flight school can realize from the low fuel burn on the DA42’s Austro engines could be enough to justify the cost of the plane.
Thanks to a more powerful (read, “larger”) rudder, the DA62 boasts outstanding single-engine flight characteristics, along with impressive single-engine climb: We saw 450 fpm.
Enter DA62
While the DA62 looks like a version of the DA42, it is, if not a clean-sheet airplane, then for all intents and purposes, a brand-new model. Everything about it is different. Its wing is even longer than the already wide wing of the ’42, its tail is taller, its cabin is wider, and its heft, at just over 5,000 pounds max weight, is heftier.
Entry is easier and more substantial a process. There are twin gull-wing doors up front and one in back that allow for easy entry and egress, and the third-row occupants simply have to step in over the middle-row seats, the backs of which fold down for easy in and out for the rearmost passengers.
That’s right, I said, “third row.” The DA62 is not only larger than the ’42, but it seats nearly twice as many people. That’s right, the DA62 seats up to 7 people, with two in the front, three in the middle and two in the back. And the rear seats are usable by adults, unlike some of the compromises you see in some six-seat singles or the tiny middle seat in the ostensibly five-place G5 Cirrus.
They’re usable operationally as much as ergonomically. That is, not only can a grownup fit in the seat, but once they’re in it, the airplane can still take off legally. Angel City Flyers, a Long Beach, California flight school and Diamond dealer, has a cute video demonstrating that it, indeed, can.
With twin forward luggage lockers and a third-row seating area that will mostly get used as a cargo hold, the DA62 boasts impressive cargo capacity along with a good payload to carry it.
The DA62 has a remarkable useful load of just under 1,600 pounds and a full-fuel payload of right around 1,000 pounds. So you can’t take seven FAA-regulation-sized adults with you; you can take five 170-pounders and still have enough payload for 140 pounds of luggage. You can’t come close to that in an SR22.
The slick and narrow-fuselage DA62 needed additional side area, and its designers went to town, with a huge vertical fin and sizable ventral, as well.
Here, the matter of efficiency comes to the fore. With the Austro AE-330 engines, the fuel capacity can be lower so that even when you top off the tanks, there’s still enough payload left to carry those people. The DA62 carries 86 gallons of fuel, which seems like less than the 92 gallons the latest SR22 holds, but it’s not. Wait a minute. How is 86 gallons not less than 92 gallons? It’s because Jet-A weighs more than 100LL, so the fuel the DA62 carries weighs around 30 pounds more than that in the wings of the Cirrus.
But let’s remember that there are two engines on the DA62, as opposed to a single engine somewhat intuitively on the Cirrus single-engine model. But because the two Austros in the DA62 burn less fuel (around 12 gph total, which I guess is a lot less fuel) than the one 550-series Continental in the Cirrus (which burns around 16 at an equivalent power setting), the DA62 has a lot more range than the SR22. With a range of 1,283 nm, compared to 853 nm for the SR22, the DA62 has more than 300 nm more range than the Cirrus. For many, many of my missions, that’s the difference between a one-stop and a nonstop trip.
The DA62 is fast, too, around 190 knots at 14,000 feet, where you’ll be going through around 17 gph total. That’s a tad slower than the Cirrus, but not by much. One thing the Cirrus has going for it is the parachute. The DA62 doesn’t have a chute. One thing the DA62 has going for it is a second engine. The SR22 only has one engine. The SR22 comes with optional TKS anti-icing, built-in oxygen, air conditioning and the G1000 avionics system. The DA62 does, too.
In terms of safety utilities, the DA62 is the most advanced Diamond, to date, with ADS-B In/Out, TKS, Garmin’s impressive ESP envelope protection to help prevent loss of control and the best-in-class Garmin GFC 700 autopilot. There’s that second engine I mentioned, too.
ABOVE, LEFT: Thanks to the FADEC Austro engines, the DA62 boasts single-lever power for ease of operation and safety, too, due to the system’s auto-feathering capability. ABOVE, RIGHT: There’s no keyboard FMS controller, as there is in the Cirrus Perspective cockpit, among others, so you need to reach out to touch the controller directly. Autopilot, audio panel and standby instruments are centrally located for easy access from either side of the cabin.
It’s an impressive package when it comes to user-friendliness, as well. The Austro engines are FADEC, so the starting amounts to two button pushes, and once both mills have come to life, there’s no magneto check (as there are no mags), just an electronic circuit test, which requires the flick of a switch. With FADEC also comes easy power management. The FADEC takes care of all the management, so there are no prop or mixture levers, just two thrust levers, one for each engine.
Flying The DA62
I went flying in the DA62 with Diamond’s Trevor Mustard out of San Marcos, Texas (KHYI), recently, and as has been the case of late, I brought the wind with me. It was howling. Getting into the DA62, thanks to its gull-wing doors, is easy, and even though I was worried about the safety of the doors in the big winds that day, I realized in short order that they’re sturdy enough that it will take a lot more than a breezy Texas day to do them any damage.
Startup, as I said, is dirt-simple. You’ve gotta love FADEC. The push of a big silver button jolts the engine to life, then you repeat for the other side. Test the electronic ignition and you’re good to go. Taxiing is easy. The airplane sits high up, thanks to its long gear legs, and the visibility out of the wall of Plexiglas surrounding you is excellent to begin with.
As multi-engine pilots know, there’s nothing especially different about taking off in a twin, except that you do just about everything differently just in case an engine fails. We were lucky, whew, and the takeoff was uneventful, except that we used very little runway thanks to the big wind, and we climbed away, thanks to the big wing and powerful engines, at quite an angle and rate, around 1,200 feet per minute (though we were admittedly pretty light that day; book rate of climb is around 1,000 fpm).
It’s not often that the bigger version of an existing airplane, if that is, indeed, what the DA62 is, flies better than the smaller one, but that’s the case here. The ’62 feels better harmonized than the DA42, which is a good flying airplane, too. The visibility in the DA62 is nothing short of spectacular, and with the availability of air conditioning, pilots have a fighting chance of fending off the dreaded greenhouse effect that most scientists agree contributes to global cockpit warming. The climate control worked great.
We flew a number of maneuvers—steep turns, stalls, slow flight—and there were no surprises, except that the airplane feels much lighter than it actually is. The sailplane-like wing surely helps in that regard.
I was really looking forward to flying the airplane on one engine, so the nice Mr. Mustard talked me through the simple process of shutting down an engine in flight. As soon as you shut it down, the FADEC automatically feathers the prop for you. There’s no chance to feather the wrong prop, another great safety feature. I found that the plane flies much better on one engine than the DA42 does, and that’s surely because of the greater power and giant rudder. With the left engine shut down and around 95 percent power on the right engine, I was able to coax 400 fpm climb out of the airplane at 6,500 feet, and with an Alps-friendly single-engine ceiling of 14,000 feet, the new Diamond has terrific safety margins when operating on a single engine.
Landing the DA62 is about as easy as can be. The trailing link landing gear is forgiving of all but the most dramatic arrivals, and the speeds are very similar to those you’d use for a high-performance single, and with so much glass, it’s a lot easier to see the other traffic than it is in some other planes. In our case, we had the airport to ourselves, well, except for a lot of big birds, including, and this is a Texas first for me, a bald eagle. He avoided us on short final. Though it had been years since I’d landed a Diamond twin, I still managed a couple of very serviceable arrivals even with the gusty conditions, using very little runway in the process.
The Value Proposition
The DA62 would be an easier airplane in which to tackle the multi-engine rating than the DA42, or Seminole, for that matter, though it remains to be seen how much interest the airplane gets from flight schools, as it’s substantially more expensive to buy than the DA42.
The airplane I flew was outfitted with air conditioning, TKS and built-in oxygen, all three of which I’m guessing just about every customer will opt for, bringing the total to around $1.3 million, about $400,000 more than a tricked-out SR22.
For a million-plus-dollar airplane, you want ramp appeal, and the DA62 has it, with its distinctive, aggressive styling that oozes carbon-fiber cool.
That’s a pretty good upgrade, but at the same time, the DA62 gives pilot-owners the opportunity to fly farther with more payload and the safety of an additional engine. For many potential DA62 buyers, it might come down to one of the oldest arguments in the book, whether it’s safer to fly a twin or a single, in this case, a single with a chute.
While it’s too early to tell if the DA62 will steal away large numbers of potential Cirrus buyers, the new model from Diamond, which in many ways is the most advanced piston twin ever, has surely reinvigorated the conversation.

Pilot Report: Diamond DA62
Pilot Report: Diamond DA62
There’s a new twin in town — and Diamond Aircraft’s DA62 represents a major step forward when compared to the two other airplanes in its class: The Beechcraft G58 Baron and the Piper Seneca V.
The differences are numerous, but the three most obvious include a sleek carbon fiber fuselage, seating for seven, and Austro turbo-diesel engines with full electronic controls.
But Diamond doesn’t want its new flagship to be limited by comparisons to other twins. With total fuel consumption and operating simplicity on par with many high performance singles, Diamond is also aiming to attract attention from single engine pilots needing more seats and useful load, plus the comfort that comes from having two engines when flying at night and over inhospitable terrain or open water.
Having owned a Seneca and a couple of Barons for use in our family business, I got the enviable assignment to fly Diamond’s distinctive new twin when it visited Florida this spring during SUN ‘n FUN.
However, since Diamond did not have a display at the Lakeland air show this year, you were disappointed if you looked for the DA62 there. Instead, Diamond focused on demonstrating the new twin and the rest of its product line to prospective customers with demo flights based out of Plant City Airport, a few miles west of LAL.
After spending almost an hour flying the DA62 with Sales Manager Brent Eddington in the right seat, I came away agreeing that there’s no substitute for experiencing how the plane performs.
I had an idea of what to expect from the DA62 since I had flown the smaller four-seat Diamond DA42 twin several years ago at Oshkosh, but this new model is not merely a DA42 on steroids.
Twin gull wing doors for the pilot and co-pilot are a significant improvement over the tip-forward canopy of other Diamond models, while the large top-hinged left side rear passenger door facilitates loading the second and third rows.
The second row is wide enough to accommodate three medium-size adult passengers and the optional third row seating for two is best suited for children. With seven seats occupied, baggage space is limited to the two nose compartments and I predict that many purchasers will choose to delete the optional $27,725 third row of seats in favor of more baggage capacity in the cabin.
Like an SUV, both rows of rear seats can be folded flat to accommodate cargo, but access for loading the cabin with bulky items is probably not quite as easy as with the big “barn doors” of both the Baron and Seneca. However, golfers will appreciate that the dual baggage compartments in Diamond’s gracefully pointed nose can accommodate clubs.
Having always preferred flying with a control stick instead of a yoke, I was delighted to see that Diamond has continued its use of sticks in the DA62 twin. Dual throttles are mounted in the center console and a computer automatically controls engine mixtures and synchs the composite MT constant speed props.
Once seated in the comfortable pilot’s position, I noticed that the plane’s interior is upscale and a full suite of Garmin G1000 avionics is standard.
The front seats offer excellent visibility and Eddington pointed out that their locations are fixed and both sets of rudder pedals are electrically adjustable to accommodate different size pilots. Unlike the track-mounted front seats in most aircraft, this feature allows the seat design to be optimized for crashworthiness and removes any concern about losing control if the pilot’s seat were to come loose and suddenly slide back at rotation.
Once the glow plugs did their job, starting the 180-hp Austro AE330 diesels was quick and easy. Based on a Mercedes car engine, the twin turbo-charged power plants started smoothly.
While the introductory TBO is currently only 1,000 hours, it is expected that this limitation will be progressively expanded well before anyone accumulates that much flight time. Based on successful fleet experience, the similar 170 hp AE300 Austro engines installed in the DA42 went from 1,000 hours to 1,800 hours in three years.
The run-up is completely computer controlled and the pilot just sits there and monitors the automated process. And, with dual channel full authority digital engine controls (FADEC), problems with cold and hot starts are a thing of the past.
Once warmed up and ready to go, the DA62 accelerated nicely down Plant City’s 3,950-foot runway with only two of us aboard. I can only imagine how the plane would handle a gross weight takeoff, but it has a generous payload of 1,004 pounds when topped off with 86 gallons of fuel.
More power would be nice, of course, such as the dual 300-hp Continentals of a new Baron G58, but Austro does not offer a larger engine and one of the DA62’s distinctives is efficiency.
Instead of the Baron’s 32 gph fuel flow at 75% cruise (202 knots), the DA62 burns a total of only 14.8 gph of Jet-A at 75% while cruising at 187 knots. At its max power top speed of 198 knots, the Diamond burns 18.6 gph and economy cruise at 60% yields 12 gph and a range of over 1,300 miles.
Upon reaching a safe altitude, several clearing turns gave me the feel of the plane, which was solid and fun to fly with the stick. While maneuvering, Eddington demonstrated the Electronic Stability Protection (ESP) feature of the Garmin GFC 700 autopilot, which, although disengaged, automatically “nudges” a hand-flying pilot to recognize and correct excessive pitch attitude, roll attitude and airspeed excursions.
Eddington then demonstrated the DA62’s engine-out performance, which was a non-event because the plane was easy to handle with the critical left engine shut down and the prop auto-feathered. Getting the engine back online was quick and easy, just like starting a car engine.
With demo flights booked every hour, it was soon time for us to return to the airport. Eddington suggested we do a touch-and-go first and then return for a full stop landing. With flaps deployed, 90 knots felt good on final and the trailing-link landing gear and a set of large tires suitable for rough strips helped make my first landing in the DA62 acceptable. Although not current in a twin, my second landing was even better and I felt that I could quickly get comfortable in the plane.
It would take a little longer to get comfortable with the price of the new DA62, which can exceed $1.3 million when equipped with all the desirable options, such as air conditioning, TKS anti-ice, weather radar and built-in oxygen. However, to put it in perspective, a new Beechcraft Baron G58 with all the goodies carries a price of around $1.4 million.
Piper recently reduced the price of a new Seneca V by $50,000, one of its typically-equipped twins goes out the door at $1.03 million.
After operating twins for many years, our company switched to heavy singles during the past decade due to the cost of feeding two engines. The diesel-powered Diamond solves that problem, however, since the DA62’s 14.8 gph total fuel burn in cruise is less than the 16.5 gph of our turbo-normalized A36 Bonanza. Also, Jet-A typically costs less than avgas.
The ongoing debate between the relative safety of a single versus a twin will probably never be settled and, although we’ve experienced excellent reliability from our Bonanzas and Mooneys, we must concede that a twin looks safer to non-pilot passengers and their families.
With safety in mind, it’s routine for us to spend another night on the road when faced with flying home in a single after dark, especially in hard IFR conditions, but a capable twin could give us the confidence to continue on and avoid the extra cost of rooms and meals.
If you’re fortunate enough to run a profitable business with income that needs to be sheltered, the significant tax savings currently available under IRS Section 179 are another incentive to buy a new Diamond. With bonus depreciation, it’s possible to write off 75% of the purchase price in the first year.
Diamond has three target markets for the DA62 — corporate use, charter/air taxi, and families who want a flying SUV — and the plane’s ability to burn Jet-A rather than avgas will be particularly attractive to prospective customers outside the United States, where avgas is often unavailable.
Personally speaking, the DA62 would work well for our company and having seven seats available would allow me to carry all six of my grandchildren.
Now, if we can just arrange an easy time payment plan…
Be a better informed pilot.

DA62 Dawn
DA62 dawn
A second chance for the light twin market
Have a preconception of Diamond Aircraft as a manufacturer that dwells on modestly powered singles and twins, principally aimed at the entry-level market? Better rethink that. With the introduction of Diamond’s new DA62, the company has massively redesigned and upgraded its predecessor twin—the DA42-VI—and in the process created what might be called a re-imagining of the light-twin concept. Or at the very least, Diamond’s light-twin concept.
For more information
For more information, visit www.diamond-air.at/twin-engine-aircraft/da62.html. All specifications are based on manufacturer’s calculations. All performance figures are based on standard day, standard atmosphere, gross weight conditions unless otherwise noted.
Extra
At 40-percent power and 11,000 feet, range can extend to 1,540 nm.
With the DA62, Diamond has raised the bar in almost every aspect. First, the DA62 is physically larger, with a nearly 48-foot wingspan and a 30-foot length; that’s four feet and two feet more, respectively, than the DA42. The DA62 is some 660 pounds heavier, too, with a maximum takeoff weight of 5,071 pounds for those bound to the U.S. market. (Diamond posts a lighter, 4,407-pound weight for European DA62s—and the DA42, as well—in order to avoid user fees.)
Where the DA42 uses 168-horsepower Austro AE300 turbodiesel engines, the DA62 is fitted with more powerful Austro AE330 engines of 180 horsepower driving three-blade MT composite-construction propellers. The interior is wider, longer, and more luxurious than Diamond’s previous designs; dual gull-wing doors replace the forward-hinged single canopy of yore; and the extra cabin width permits three seats in the second row. An option for two more aft seats yields a total of seven seats, but aft baggage space is sacrificed.
And there’s upscale leather seating and trim details, complete with stitching along the glareshield, and a fancy center console and armrest. “Frankly, we haven’t been going for a luxury look in the past,” said one U.S. Diamond dealer. “But with the DA62 we made a conscious effort to go upscale. For example, we looked at what Cirrus does with its interiors and decided that we needed to up our game in order to stay competitive.” That said, the DA62 retains Diamond’s fixed-position, reclined, sailplane-style pilot seat design and central control-stick placement. If there have been any complaints, they’ve been about that control stick, because it can interfere with smooth boarding and get in the way of charts or iPads. Maybe there will be a sidestick in Diamond’s future?
The thigh-support portion of the DA62’s pilot seats folds down for easy boarding, meaning that you no longer have to step on the seat to get in. The seat-back position is adjustable, and the seats have inflatable lumbar support. And what’s this? Cup holders, and even customized fixtures on the forward sidewalls that are designed to hold water bottles. Meanwhile, the airplane’s monocoque cabin structure is designed for optimal crashworthiness.
The airplane’s avionics and systems are exemplary. Full-authority digital engine controls (FADEC) mean virtually automatic engine starts under all conditions; single-lever power controls; and protection against engine exceedances. The Garmin G1000 avionics suite includes flight envelope protection—dubbed Electronic Stability and Protection (ESP)—offered by a function of Garmin’s excellent GFC 700 autopilot/flight control system. The airplane flown for this report was a European demonstrator that was on display at the 2015 National Business Aviation Association (NBAA) convention, and showed off the DA62’s many options: a TKS ice-protection system with flight-into-known-icing (FIKI) approval; Garmin’s GWX 70 weather radar; global datalink weather over the Iridium satellite network using Garmin’s GSR 56 datalink receiver; a Garmin GDL 69A receiver for SiriusXM datalink weather and music; Avidyne’s TAS 605 traffic advisory system; an oxygen system; and air conditioning.
A desert cross-country
I flew the Austrian-registered DA62—OE-FGZ—from Las Vegas’ McCarran International Airport to Sedona, Arizona. With me was Seosamh Somers, president of a Diamond Flight Center and flight school based in Long Beach, California. During the walkaround Somers explained the airplane’s classy gray-and-silver paint job by saying that Diamond had come up with a new ultraviolet-tolerant composite construction process that doesn’t limit the exterior to a plain white treatment.
As with any automotive diesel engine used in an airplane application (Austro engines use Mercedes-Benz crankcases, and top ends designed to Diamond specifications), DA62 engine starts involve turning on the engine master switches and then waiting for the glow plug annunciators on the primary flight display to extinguish. Then it’s a matter of momentarily pressing an engine start button. The engines instantly come to life; there are no cold- or hot-start procedures with FADEC.
Runups consist mainly of FADEC checks. Hold down the engine control unit switches for 30 seconds while a test cycle runs the engines up to 45-percent power, and then check both the A and B FADEC channels for each engine by moving a toggle switch manually between the channels, then return it to the Auto position. You’re looking for any caution or advisory system messages on the G1000. No messages? Then it’s time to taxi.
It takes firm rudder pressure to maneuver the DA62 while taxiing. That’s because the airplane is approved for operations on unimproved runways, and thus has larger tires.
This turns out to be an advantage during takeoffs and landings, when the airplane seems more sure-footed. With the ship’s weight and steering feel, there’s definitely a “big airplane” sensation as the DA62 accelerates to its 76-knot rotation speed. Then it’s a liftoff into a 90-knot initial climb doing 1,100 fpm. Initially we used a 130-knot en route climb speed, and then went to 150 knots once passing through 7,000 feet. This produced a 900-fpm rate of climb. Density altitude at Las Vegas was 4,000 feet for takeoff.
The first cruising altitude of the 180-nm trip was 13,500 feet, where I made a check of high-speed cruise performance. With power set at 93 percent we trued out at 194 knots while burning 9.4 gph per side, with the FADEC giving us 2,200 propeller rpm. With our optional 86 gallons of Jet-A, our endurance would have been around four hours with IFR fuel reserves, and our range approximately 770 nm.
At a more reasonable setting of 60-percent power, we did a respectable 167 KTAS while realizing a 12 gph total fuel burn that would give us an endurance of seven hours. And at 40-percent power, fuel burn dropped to 4.2 gph per side, for a whopping 11-hour endurance and 1,540-nm range at 140 KTAS. You’d need a relief tube (which is not available, by the way) to take advantage of this kind of performance, but it does demonstrate the DA62’s impressive fuel efficiency—and confirms another reason for Diamond’s commitment to diesel power. (The scarcity and price of avgas in Europe, and the virtual absence of avgas in Diamond’s large Russian and Asian markets are others).
Down at a more typical, nonoxygen altitude of 9,500 feet, the DA62 gave us 173 KTAS on a 14-gph fuel burn for a range of 680 or so nautical miles. Ultimately, even with all the climbing, descending, and power changes, we reached the red rocks and dramatic vistas of Sedona in just one hour, 12 minutes. Not bad at all.
Landing, photos, and single-engine
I wish I could tell you that landing the DA62 gave me the chance to show off my superb energy management in the pattern, and my flawless judgment at the moment of touchdown. But no. The airplane is completely conventional in its behavior, and if you can land any complex single or light twin, then you’ll have little trouble.
Well, at Sedona, the landings are a tad unusual. For our entry to the downwind leg for Runway 3, we flew hard by the east edges of Thunder Mountain for a close-up view of that dramatic checkpoint, then reduced power. Then gear down abeam the touchdown point, and at 130 knots the first notch of flaps came out. On final, a power setting of 37 percent and full flaps produced a speed of 85 to 90 knots for short final.
With the FADECs, there’s no propeller or mixture controls to fool with, so it’s just fly to the threshold, adjusting power and crosswind correction as necessary. Runway 3 slopes uphill, so there’s the illusion of being too high. Fall for it, and you’ll find yourself too low, so using the VASI is the way to go. Power off at 20 feet or so, hold your pitch attitude, and—erk-erk!—you’re down in style.
The next day was photo day. With AOPA Senior Photographer Mike Fizer leaning out the back of a Beech Bonanza A36, Somers and I flew in formation over the sun-drenched mesas and crag-lined valleys as daylight cast ever-longer shadows. Of course, the DA62 had no trouble matching the Bonanza’s speed. Sometimes, for video shots, I did breakaway maneuvers where I banked sharply away from the camera airplane. Then, when rejoining for more shots, I’d have to do steep banks toward the Bonanza to quickly fall into place. A couple of times, my banks were 45 degrees, or maybe a little more. That’s when I felt the ESP kick in. Go past 30 degrees or so, and the ESP will begin to fight your stick pressure; the steeper your bank, the more resistance you feel. It’s a fly-by-wire-style method of keeping you safely within the flight envelope, and there are pitch limits as well. I can see where ESP could keep you out of trouble, especially when hand-flying in challenging instrument conditions.
The photo shoot finished, it was time for some engine-out work. Again, the FADECs help. Use standard dead foot/dead engine identification (with a check of engine gauges to verify a loss of power), and then simply switch off the bad engine’s master switch. The engine stops—as in instantaneously. Use a feathering switch to complete prop feathering, and then retrim for the new configuration. Thanks to the turbos, single-engine climb rates at 7,000 feet came in at 350 fpm, but there were just two of us aboard. Down low, at maximum takeoff weight, single-engine climb rates run in the range of 200 fpm, depending on density altitude. Hey, it’s a 5,700-pound airplane climbing on 180 horsepower.
On the last day of the trip, we were joined by Michael Dubrow, a local video producer. Now there were four in the cabin, with both Fizer and Dubrow shooting video. They had plenty of room, so it was an enjoyable half-hour doing steep turns and slow flight over scenery that every pilot should experience at least once in a lifetime. We even saw a group balloon launch far below us.
Diamond sees a short-haul charter market for the seven-seat version of the DA62. That may be, but baggage space is sharply curtailed by that aft two-seat option. And the GWX 70 takes up much of the room in the nose baggage compartment. So the DA62 may have stronger appeal to those wanting to fly four or five passengers in comfort, style, and economy. True, its million-dollar price tag rivals that of a competitor, the Textron/Beechcraft Baron G58. But the DA62’s fuel efficiency means that less fuel is needed to carry larger loads over typical trip lengths. In models without TKS and air conditioning, that means five passengers and their bags theoretically can fly 400 nm in 2.3 hours or so, with IFR reserves, depending on winds and assuming 70-percent power at 9,500 feet. On the other hand, if range is what you want, then two aboard with full fuel can let you fly more than halfway across the nation.
Diamond announced in February that the DA62 had earned FAA certification. We’ll see how this new light twin is received. Orders have been placed, Diamond says, but it doesn’t say how many. In the meantime, the company is selling its DA40 and DA42, and remains ever focused on research and development. Diamond continues its experiments with autonomous landing and other concepts at its Wiener Neustadt, Austria, manufacturing site. The autonomous landing idea is to bring an airplane in distress to a safe landing by remote control using GPS and ground-based guidance. Until that project comes to fruition, a second engine will have to serve as the emergency backup.
Email tom.horne@aopa.org
Spec Sheet
Diamond DA62
Base price: $1.08 million
Price as tested: $1.32 million
Specifications
Powerplants | (2) Austro Engine AE330, 180-hp turbodiesels
Recommended TBO | 1,800 hr
Propellers | (2) MTV-6-R-C-F/CF 194-80 3-blade constant speed, full-feathering
Length | 30 ft 1 in
Height | 9 ft 3 in
Wingspan | 47 ft 10 in
Wing area | 184.1 sq ft
Wing loading | 27.5 lb/sq ft
Power loading | 14 lb/hp
Seats | 5 or 7, depending on configuration
Cabin length | 9 ft 2 in
Cabin width | 4 ft 5 in
Cabin height | 4 ft 3 in
Empty weight | 3,461 lb
Empty weight, as tested | 3,765 lb
Max ramp weight | 5,089 lb
Max gross weight | 5,071 lb
Useful load | 1,610 lb
Useful load, as tested | 1,306 lb
Payload w/full fuel | 1,275 lb
Payload w/full fuel, as tested | 971 lb
Max takeoff weight | 5,071 lb
Max landing weight | 5,071 lb
(Max) zero fuel weight | 4,850 lb
Fuel capacity, std | 52 gal (50 gal usable) 348.4 lb (335 lb usable)
Fuel capacity, w/opt tanks | 89 gal (86.4 gal usable) 596.3 lb (578.9 lb usable)
Oil capacity, ea engine | 7.0 l
Performance
Takeoff distance, ground roll (MTOW) | 1,575 ft
Takeoff distance over 50-ft obstacle (MTOW) | 2,733 ft
Max demonstrated crosswind component | 25 kts
Rate of climb, sea level (MTOW) | 965 fpm
Single-engine ROC, sea level (MTOW) | 163 fpm
Max level speed, 14,000 ft | 192 kt
Cruise speed/endurance w/45-min rsv, std fuel (fuel consumption, ea engine) @ 95% power, 14,000 ft | 192 kt/3.9 hr (120 pph/17.1 gph) @ 75% power, 20,000 ft | 188 kt/5.0 hr (104 pph/14.8 gph) @ 45% power, 8,000 ft | 134 kt/8.8 hr (63 pph/9.0 gph)
Maximum operating altitude | 20,000 ft
Service ceiling | 20,000 ft
Single-engine service ceiling | 13,000 ft
Landing distance over 50-ft obstacle (MTOW) | 2,556 ft
Landing distance, ground roll (MTOW) | 1,447 ft
Limiting and recommended airspeeds
VMC (min control w/ engine inoperative) | 70 KIAS (flaps T/O) 76 KIAS (flaps Up)
VSSE (min intentional one-engine operation) | 86 KIAS
VX (best angle of climb) | 86 KIAS
VY (best rate of climb) | 89 KIAS
VYSE (best single-engine rate of climb) | 89 KIAS
VA (design maneuvering) | 120-141 KIAS
VFE (max flap extended) | 119 KIAS
VLE (max gear extended) | 205 KIAS
VLO (max gear operating) Extend | 205 KIAS, Retract | 162 KIAS
VNO (max structural cruising) | 162 KIAS
VNE (never exceed) | 205 KIAS
VR (rotation) | 78 KIAS
VS1 (stall, clean) | 73 KIAS
VSO (stall, in landing configuration) | 69 KIAS

Piper Seneca V
The Miniature Cabin-Class Twin
Just over 50 years ago, a genius mind at Piper Aircraft considered the possibility of widening the fuselage of a proposed six-seat derivative of the single-engine Cherokee. Another seven inches of width, he reasoned, would make it possible to squeeze three people into the second row of seats. Charter operators would love being able to haul three couples with a 260-hp engine.
And so began the very-successful PA-32 Cherokee Six wide-body series, which subsequently begat the Piper Seneca twin and the Lance retractable single (later the Saratoga), capable airplanes in their own right. The fortuitous lateral enhancement of the stretched PA-28 fuselage made it possible for the Seneca to have a roomy twin-engine cockpit, complete with co-pilot instrumentation. And the cabin’s rear-door layout easily lent itself to a club-seating arrangement, with some entertainment and refreshment accoutrements, and even a bit of aft-cabin baggage.
Today’s Seneca V is, like most legacy designs, a far cry from the original PA-34 that appeared in 1972. A steady march of capability development and tremendous advances in instrumentation and avionics have created a Seneca that far outclasses its forebears. With a full Garmin suite of integrated avionics, the current Seneca V carries a complete turbine-like cockpit.
Five Decades Of Advancements
In the beginning, the Seneca was to be a plebeian replacement for the Twin Comanche, whose final demise came in the summer of 1972, when Piper’s old Pennsylvania factory was inundated with hurricane-induced floodwaters. Rather than replace the damaged Twin Comanche tooling, it was considered wiser to let the Florida-produced Seneca carry the company’s light-twin flag.
The first Seneca (which actually made it to market four years ahead of the single-engine Lance) used a pair of counter-rotating 200-hp IO-360 four-cylinder Lycomings, right out of the Cherokee Arrow. Given the airplane’s 4,000-lb gross weight (increased to 4,200 pounds after the first year), the little normally-aspirated engine did not allow for much single-engine performance, a trait similar to the T-C the Seneca replaced. Two-blade props, straight-ahead seating for six (or seven, if slim), and a manually-actuated flap system kept the price down to an astounding $49,900. Piper, as always, was able to produce “more airplane for the dollar” than just about anyone.
The cure for the Seneca’s lackluster engine-out performance was turbocharging and, rather than bolt on RayJay aftermarket blowers like the Turbo Twin Comanche had used, the nod was given to counter-rotating versions of Continental’s TSIO-360 engine, with six cylinders and automatic wastegate controls. However, the engine’s power output was limited to 200 hp in the PA-34T. The resulting Seneca II, introduced in 1975, could reach 13,400 feet on one engine, even with gross weight up to 4,570 pounds. Its aft cabin was also enhanced by club seating.
The Seneca II’s Achilles’ Heel was its 4,000-lb zero-fuel weight restriction, which didn’t allow for more than 700 pounds or so of cabin load, even if fuel was limited. Additionally, standard fuel capacity was only 93 gallons, although another 30 optional gallons was soon made available. A beef-up to handle more bending moment in the wing carry-through structure resulted in the 1981 Seneca III, grossing 4,750 pounds and, more importantly, offering an increase in zero-fuel weight to 4,470 pounds. The Seneca III also offered a boost in takeoff horsepower to 220. By this time, the base price had ballooned to 2 1/2 times that of the 1972 model, but the Seneca was coming into its own; a one-piece windshield and better fit and finish were now in place. During its production, the Seneca III saw changes like electric flaps in 1985 and a 28-volt electrical system in 1989.
After a 12-year run, the Seneca III was replaced by a slightly-upgraded Seneca IV in 1994, sporting circular cowling inlets and sculpted nacelles. The base price was now over eight times that of the first Seneca, a factor shared by the rest of the industry as sales became scarce and aircraft production rates plummeted. Nevertheless, a much-improved Seneca V appeared in 1997, with the intercooled -RB engine variant and 220 continuous horsepower available. Although numerous changes have since been wrought that would warrant a new Roman numeral designation, it is a Seneca V that remains part of the Piper lineup today.
Now equipped with a Garmin G1000 three-display electronic panel and a GFC-700 autopilot, the latest Seneca V can be thought of a mini cabin-class business airplane, more than capable of filling the role of a light company plane, for those trips that are too short to justify a jet or turboprop. It can easily carry 1,000 pounds in the cabin with enough fuel for a two-hour VFR mission.
Systems Details
Construction-wise, the Seneca V is primarily an aluminum airplane, with composite non-structural components like cowlings and fairings. The engines are tightly cowled, with a manually-adjusted cowl flap underneath. Polished spinners house the 76-inch swept-tip McCauley props. The three-blade props turn at only 2,600 rpm for takeoff (versus 2,800 rpm in the old Seneca III). The left engine will normally have a retractable door and louvered outlets for an air conditioner installation.
The combustion-type cabin heater is mounted in the tailcone, instead of in the nose. Baggage capacity is 200 pounds, 100 in the nose compartment and 100 behind the rear seats, where a swing-up door is provided for access. The 122 gallons of fuel is carried in interconnected wing tanks, requiring no pilot management, serviced by filler ports in the outboard tanks. The wingspan is less than 40 feet and height is under 10 feet.
The landing gear system is hydraulically-actuated, electrically powered by a powerpack in the nose. All three gears carry a 6.00 x 6 tire. The wide-span flaps are electric, and the tail sports a stabilator pitch-control surface, as pioneered by Piper on the 1960 Aztec. It and the rudder have anti-servo trim tabs.
Boarding the rear seats is accomplished via a low slide-in entrance, through a door on the left rear fuselage. The two front seats are reached through an over-wing door on the right side. Most of the cabin is four feet wide; there’s a foldaway worktable between the CEO’s right-rear seat and the facing chair.
Underway
Up front, the darkened G1000 screens await activation with power-up; redundancy is provided by primary and backup batteries. Starting differs from normal Continental fuel-injection procedure, in that the boost pump is switched on while mixture is in idle cut-off, advancing the mixture to prime the engine, then cranking with mixture full-lean until light-off. This works well, hot or cold. With both fans turning, taxiing is enhanced by the low glareshield and sloping nose. Run-up is performed at 2,300 rpm, with feathering checks done at 1,500 rpm. With trim and controls verified, cowl flaps open and boost pumps on, the airplane is ready for takeoff.
Power is gradually applied to the 38-inch redline limit, even though the wastegate controllers should restrain full-throttle manifold pressure to that number. Vmca is a low 66 knots with either engine failed, Vxse is 78 and Vyse is 92. Rotation begins at 81 knots, flying away around 90. Gear-up, a normal cruise-climb is established at 110 knots, tweaking the power back to 35 inches and 2,500 rpm. While best-rate climb will generate 1,500 fpm, the cruise-climb gives 1,100 fpm with a lower deck angle.
As with most turbocharged piston planes, the Seneca V can scoot along at nearly 200 knots if flown up near 18,000 feet, but normal flying will be done at non-oxygen altitudes, since the cabin is unpressurized. At 10,000-12,000 feet, 175 knots is a typical max-power cruise figure, using 30 inches m.p. and 2,500 rpm. That requires about 30-gph fuel consumption, while 70% power of 25 inches and 2,300 rpm knocks around 10 knots off the speed but lowers fuel burn to 24 gph.
Handling at cruise speed requires more muscle than during climb and approach, but the Seneca V is properly responsive and quite stable, even when flown manually. Slowed down, the stall speed is a very un-twin-like 64 knots in landing configuration, so a 90-knot approach is more than adequate, and one can even use 80 knots over the threshold for short fields. A 10-degree flap setting is allowed at 140 knots, which easily slows the aircraft to the gear-operating speed of 128 knots. Full flaps can go out below 113 knots, and 15 inches m.p. holds a glideslope nicely. If passengers are not in the back, the Seneca is a bit nose-heavy in the flare, but it’s easily managed with some additional trim applied. Runway lengths of 3,000 feet are adequate.
Facing only the Textron Aviation Baron G58 as competition, the Seneca V is 20 knots slower but less expensive to purchase and supply with fuel. Now well into its fifth decade of production, the Seneca V remains a dependable and flexible load hauler. With the latest instrument panel enhancements, it’s ready to continue its faithful service.
SPECIFICATIONS: Piper Seneca V
Powerplants
Seats6-7
Fuel122 gallons
Performance
Certified ceiling25,000 feet
Single-engine ceiling16,500 feet
Max. cruise speed197 kts.
Stall speed64 kts.
Takeoff distance
(50 ft. obstacle) 1,707 feet
Landing distance
(50 ft. obstacle) 2,180 feet
Max. range
(w/45-min reserve) 828 n .mi.
Climb rate-2 engines1,250 fpm
Climb rate-1 engine225 fpm
Weights
Ramp4,773 lb.
MTOW4,750 lb.
Zero Fuel4,470 lb.
Landing4.513 lb.
Empty, std3,442 lb.
Useful load, std1,331 lb.
Dimensions
Wingspan38.9 ft.
Height9.9 ft.
Length28.6 ft.
Cabin length10.35 ft.
Cabin width4 ft.
Cabin height3.5 ft.
Baggage200 lb.
2015 base price$1,031,550

Seneca V: Little Big Twin
At the risk of compromising my alleged objectivity, I have to confess a soft spot for the Piper Seneca. Back in the late ’70s, I spent two years with a Seneca II company airplane. I logged 500 hours in that twin, flying all over the States, Bahamas and Canada—operating solo or with six on board—and bouncing off strips from below sea level to America’s highest airport (located in Leadville, Colo.) at nearly 10,000 feet MSL.
One benefit of having spent several hundred hours with the old Seneca is that I have a special appreciation for the new one. I won’t bore you with the long list of improvements in an airplane that looks structurally similar to its grandfather, but take my word for it, the new Seneca V is several generations removed from that first turbocharged PA34.
For those pilots who’ve been living on the dark side of the moon for 30 years, the Seneca is essentially a Cherokee Six with retractable gear and dual 220 hp Continentals. Piper has always been one of the most innovative companies in adapting existing designs to new applications, and the original Seneca followed this formula.
The Lock Haven, Penn., company had a deserved reputation as a strong advocate of moderately priced, multi-engine airplanes. The bulbous Apache and Aztec of the late ’50s evolved into the Twin Comanche and Navajo of the ’60s. Senecas came along in the ’70s, and few would have guessed the airplane would survive the GA crash of the ’80s and march on into the next century.
Today’s Seneca V is one of only five surviving piston twins; it’s a considerably more refined and functional machine than the Seneca II I used to fly. The 2008 twin market includes the Diamond Twin Star, Adam A500, Piper Seneca V and Seminole, plus the Beech G58 Baron.
The six-cylinder Continental TSIO-360 engines, which have evolved from 200 to 220 hp, are now intercooled and employ automatic sloped controllers to maintain even power and avoid overboost. TBO has increased to its current 1,800 hours, and what was once a marginal powerplant has become envied and reliable.
Max takeoff weight has increased almost 200 pounds (a good thing since empty weight has gradually increased from 2,840 to 3,393 pounds), wing span has widened by two feet, and single-engine service ceiling has stepped up from 13,400 to 16,500 feet.
Over the last 30 years, the Seneca has benefited from numerous improvements: horsepower on each engine has increased from 200 to 220; TBO has gone up to 1,800 hours; and service ceiling is now 25,000 feet.
Well, duh! It’s not as if you wouldn’t expect some improvements in 30 years. Fact is, however, the Seneca’s survival in a marketplace that hasn’t looked all that favorably on twins is at least a partial vindication of the airplane’s configuration and mission. (Perhaps incredibly, there were about a dozen piston twins in production at the end of the ’70s.)
The Seneca is one of only two Pipers that’s managed to stay in more-or-less continuous production through the 1980s, 1990s and 2000s. The PA34 and Malibu Mirage were the only models to survive the partial shutdown of the company in the early ’90s.
The current Seneca remains essentially a multi-engine Saratoga. Considering that the Piper Seminole is pretty much a dedicated multi-engine trainer and the Beech G58 Baron is priced just over $1 million (nearly into entry-level VLJ territory), the Seneca V is virtually alone in its class. Base price of the Seneca V for 2007 is $756,500, and while that’s still a considerable sum, it buys an airplane with more talent than you’d believe.
Perhaps the most notable of these talents is simply the airplane’s large, comfortable cabin. Size matters, especially when you’re traveling in a machine that can’t be conveniently pulled over for a break. Airplanes, like people, tend to gain weight with age, but the Seneca’s cabin is a pleasant constant.
While payload has shrunk as empty weight has increased, cabin size is among the best in the industry. Cabin width is a spacious 49 inches, slightly wider than a Mirage and roughly the same dimension as the cabin-class Piper Navajo. The cabin does begin to taper toward the tail abeam the second row of seats, but there’s still enough room to load anything, from a coffin to a piano to people.
Piper loves to tout the Seneca’s excellent quick-change cargo capability, and it’s true the PA34 will accept a variety of loads. The reality is that the airplane will most often be used to carry people rather than things. Pilots board in the conventional manner via the right wing walk and luxuriate in the front office, but passengers relegated to the rear need not feel like second-class citizens.
Standard on the PA34 is the Avidyne Entegra glass-panel system, with TAWS and weather data showing on the MFD. Including the pilot, the aircraft seats six, and cabin width is a spacious 49 inches.
Boarding the aft cabin is probably easier than in any other airplane I can think of. Climbing aboard through the twin, aft, left doors hardly deserves the term “climb.” You merely step over the low floor and lever yourself into one of the big seats. Separation between the conference-style second- and third-row seats is generous to minimize overlapping legs. If you’re flying with no one in the opposing seat, you can put your feet up and feel like a business-class airline traveler with a luxury footrest. There’s even a side-mounted writing table on the airplane’s right side.
Over the years, useful load has declined from more than 1,700 pounds on the Seneca II I used to fly to more like 1,400 pounds on the new Seneca V. Subtract 122 gallons’ worth of fuel (732 pounds), and you’re left with only about 670 paying pounds. Leave 50 gallons in the truck, and you’d have nearly six folks’ worth of payload with two hours of fuel aboard. A strange-shaped baggage compartment wrapped around the nosegear and a large space behind the rear seats accommodates cargo.
Whatever the payload, the Seneca V’s turbocharged Continentals allow you to lift easily and efficiently. The airplane comes off the ground and starts uphill cleanly and without hesitation to catch its breath. Initial climb is listed at 1462 fpm, but most pilots prefer a 130-knot cruise climb, sacrificing perhaps 250 fpm of ascent in exchange for improved forward visibility.
There’s little to do on the way up except admire the view and marvel at the Seneca’s simplicity. Automatic wastegates keep the power stable to the airplane’s critical altitude (19,500 feet) where the horses begin to tire. If you’re climbing to any altitude below 16,000 feet, you can usually plan on averaging at least 1,000 fpm. Sixteen minutes after liftoff from sea level should yield 16,000 feet of height. Simple, huh?
In theory, the Seneca’s turbochargers allow cruise as high as 25,000 feet, and if you’re willing to strap on the cannula and climb to the flight levels, you can see speeds near 200 knots. Realistically, Senecas spend most of their time at lower altitudes that don’t demand supplemental O2. At 11,500 feet, with the engines dialed in at 75%, for example, you can expect an easy 180 to 185 knots on about 26 gph. That will deliver just under four hours of endurance for a nearly 700 nm range. For those strange people who buy fast airplanes to fly slow, 55% yields max range over 800 nm.
However long you elect to sit in the Seneca V, you’re bound to enjoy the experience. PA34s come standard with an Avidyne Entegra flat-panel display that incorporates all flight instruments, moving map, navigation and systems readouts on two large, 10.4-inch glass displays. Entegra offers overlays of weather uplink thru WSI InFlight and a full-time air-data computer to display en route wind vectors. Also, the system can be interfaced with Stormscope to survey electrical activity ahead, as well as Active-Surveillance Traffic Advisories, an active system that monitors possible traffic conflicts. TAWS information reads out on the glass panel and CMax electronic charts offer a worldwide library or approach and en route IFR charts. As if all that weren’t enough, the autopilot is coupled to the Entegra to make the in-flight environment as convenient and effortless as possible. (Honeywell’s RDR 2000 Vertical Profile Weather Radar is also available.)
The Seneca V is quiet with minimal vibration and excellent ventilation (including air-conditioning if your budget will allow), and the cabin is so friendly, you’ll make the trip with minimal fuss. The PA34’s fat, untapered, high-dihedral airfoil is as gentle as on any twin (past or present); the Frise ailerons impart plenty of roll rate; and both engines turn inboard to offset the critical engine problem. The combination produces a stability and gentle controllability more reminiscent of the Saratoga HP than of a middle-weight multi.
At 4,750 pounds gross, stall speed is a highly predictable 64 knots, so approaches are silly simple at any speed between 90 and 110 knots. The Seneca makes an excellent instrument platform, too. In the 21⁄2 years I operated “my” Seneca II, I flew it into snowstorms in Calgary, torrential rain in the Bahamas and ice fog in Maine. The airplane forgave my transgressions and consistently delivered me from evil, no matter how poor my decisions or rusty my technique.
(One approach I made to Janesville, Wis., in the late ’70s certainly demonstrated the airplane’s docile nature. I was shooting an ILS in miserable conditions. Weather was right at minimums, and I was being beat around pretty good trying to maintain the glideslope. The airplane was going to Janesville for maintenance, and one of the squawks was the left electric fuel pump. The left engine-driven pump failed about three miles out, and so did the engine, but I was so busy just trying to hold the needles, I hardly had time to worry about it. I broke out over the runway, and touched down as the left prop windmilled to a stop.)
Landings in the PA34 also fall into the “if you can walk and chew gum at the same time” category. The now-electric flaps deflect to a full 40 degrees, allowing the Seneca to sneak into short strips with relative ease, and the long-stroke oleo gear cushions the actual touchdown. Also, unlike the vast majority of airplanes, the Seneca can leap off the ground in slightly less runway than it needs to land. Both numbers are well below 2,000 feet, and that may be one reason PA34s sometimes wind up working for a living on dirt or grass strips. Main-gear doors cover only the top of the wheels, so there’s plenty of ground clearance with little risk of damaging a door.
(In operating out of the 2,000-foot grass strip at Ft. Atkinson, Wis.—long since paved and extended—I was sometimes intimidated by the tall corn at the south end. During one takeoff on a hot July day with the manual flaps set at the recommended full-up position, the corn was approaching way too fast. I reached down, grabbed the manual flap lever and pulled for one notch to get me into the air. Unfortunately, I pulled too hard and got two notches, and the huge flaps promptly rotated the lightly loaded Seneca’s main gear off the ground and balanced the airplane on its nosewheel. I hauled back on the yoke and cleared the corn by a few kernels. Won’t do that again.)
At $756,500 for the entry-level airplane, the 2007 Seneca V fills a niche that no other model can. The big cabin, easy loading and good short-field performance allow the aircraft to serve in a variety of missions: mail and check hauling, freight and corporate transport, charter and as many other jobs as you can imagine.
By any measure, the Seneca V is a flexible, talented machine, simple to fly and fairly easy on maintenance (compared to other twins). Add to that quick cruise and enough creature comforts for most normal-sized creatures, and you have all the ingredients that have kept Piper’s tough little Seneca in production for a surprising 35 years.

We Fly: Piper Seneca V
The Seneca has managed to stay in continuous production for so long by combining a solid airframe with a host of refinements and upgrades inside and out since the first PA-34 rolled out of the Piper factory in 1971. Today’s highly evolved Piper Seneca offers what a lot of pilots consider the ideal attributes of a personal airplane: two engines for redundancy in power and systems, respectable performance, stable handling, ice protection, the latest in avionics technology and lots of room in a comfortable cabin.
The latest Piper Seneca V, which is built in Vero Beach, Florida, is the best one yet, thanks to the addition of Garmin G1000 avionics up front and smart improvements inside of what was already one of GA’s widest cabins. A lot of airplanes benefit from Garmin technology, but in the Seneca’s case, G1000 is precisely what this gracefully aging twin needed. That it took Piper so long to figure this out is surprising considering the manufacturer’s emphasis on selling airplanes in the training market, but now that G1000 has arrived in the Seneca V, tire kickers from North America to Brazil and beyond are taking notice.
When Piper introduced the Seneca V in 1997, it represented a major improvement over the Seneca IV — and in the 17 years since then, Piper’s top-of-the-line twin has undergone major changes. For starters, it has courted a dizzying number of avionics suitors before finally settling down with G1000. First, there was a package centered around the Bendix/King KLN-90B GPS receiver, which wasn’t a bad choice at the time. Later, there was an optional electronic flight information system paired with a Garmin GNS 430/530 combination. Next, Piper offered Avidyne Entegra. And most recently, the Garmin G600 system mated to a pair of GNS430s became the standard avionics package. None of these panels did the Seneca justice, however.
That’s all changed with G1000, which looks as if it were tailor-made for the space. The three-display arrangement fits the wide panel almost perfectly. The upgrade from G600 to G1000 makes a difference not only in the size of the displays (6.5 inches versus 10.4 inches) but also in terms of capabilities. When Piper brought G600 to the Seneca, it seemed like a temporary fix — probably because it was. G1000, on the other hand, elevates the Seneca to a more level playing field with the Baron G58, which also features a G1000 panel.
Seneca’s standard avionics package also features an Aspen Avionics standby display, something the Baron lacks. This display provides all the information you’d need to keep flying in just about any weather and eliminates the requirement for electromechanical backups or even a whiskey compass.
Adding the three-display version of G1000 to the Seneca also allowed Piper to get creative with the shape of the glareshield. A flatter design improves the view outside, a change that is especially welcome on approach and during the flare, as I would find out when I flew the Seneca V out of Vero Beach with Piper engineering test pilot John Kronsnoble. The airplane I piloted was actually the avionics certification test mule with a cabin devoid of the usual club leather seats, plush carpeting and other touches. Still, it was no stretch to imagine what a comfortable long-haul airplane this would be once all the engineering test gear in back was replaced with production furnishings. Besides, I didn’t really care much about what the cabin looked like — I was too interested with what was new in the panel.
I’ve been flying G1000-equipped airplanes since G1000 first emerged, so it’s tough for me to get really excited about seeing yet another iteration of the ubiquitous Garmin cockpit. But the G1000 in the Seneca just seems so right — the layout of the engine and systems indications is exceptionally well executed, with no overlapping needles anywhere and flap and gear position indications front and center on the MFD. Crew alert messages are easy to read and understand. Among the new features are user-defined holding patterns that can be created at any point in space through a series of menu selections on the MFD. The Seneca’s S-Tec 55X autopilot (due for replacement by the Garmin GFC 700 flight control system later this year) will even fly the correct entry for you automatically.
Another welcome upgrade is the selection of the Aspen standby system in lieu of the usual mechanical backups that are normally required in G1000 installations. Together, they provide some exceptional redundancy. There are G1000 primary and backup batteries, dual alternators and a backup battery in the Aspen display — making the chance of a total electrical failure in the Seneca extremely unlikely. Thanks to the thought that has gone into the avionics design, flying in a degraded avionics mode is really a nonevent, Kronsnoble says. And anyway, not much can go wrong in this airplane without the pilot being warned about it through the G1000 alerting system.
My initial impressions of the latest Seneca were reinforced when I flew it. In truth, this iteration of the PA-34 handles about the same as any other — and that’s a good thing. The Seneca is fun to hand fly and rock solid in roll and pitch, thanks to its constant-chord wing, long ailerons and a nicely weighted stabilator at the back. The props connected to the Seneca’s 220 hp Continental TSIO-360-RB engines are counter-rotating, meaning there is no critical engine in an engine-out emergency — another advantage over the Baron. Those turbocharged Continentals can produce rated power all the way to 19,500 feet. Even down at 12,000 feet, the Seneca can true at 180 knots on 24 gallons of fuel per hour.
TO THE TEST
Lined up on Vero Beach’s Runway 11R, I put the power to the TSIO-360s and rotated in no time. Pitching for the Seneca’s best angle airspeed of 83 knots, I retracted the gear once a positive rate was established, and the useable runway slipped away below us. It was a humid day in South Florida, with some scraggly low clouds to maneuver around as we climbed briskly in VFR conditions out over the Atlantic. At 5,500 feet, I found a slice of airspace to execute a series of maneuvers, starting with 50-degree steep turns, power-on and -off stalls, and some brisk climbs and descents. Through it all, power response was smooth and control pressures balanced. The Seneca might not be quite the pilot’s airplane that a Baron is, but it’s close.
Next, I switched on the autopilot, so Kronsnoble and I could dig deeper into the G1000 system. With some prompting, I was able to program a hold at my current position and let the autopilot fly a smooth teardrop entry into an oval racetrack pattern. I then hit the autopilot disconnect switch on the yoke and hand flew a circuit in the hold. It really couldn’t have been easier thanks to the G1000’s fight director cues and the Seneca’s natural stability keeping us on a precise track. Some pilots prefer a conventional elevator to the Piper’s stabilator, but I had no complaints. It felt right.
For our next technology demonstration, Kronsnoble called up the satcom page on the MFD and showed me how to place a telephone call. I dialed the number he gave me using the straightforward G1000 interface, and just like that, the phone was ringing in my headset. Somebody back at the Piper factory picked up and confirmed they heard us loud and clear. They sounded good on our end too. Thanks to the Iridium satellite network’s global coverage, calls can be made and received literally anywhere in the world. The same goes for emails and text messages sent using the service. (Keep in mind, though, that outgoing calls cost $1.50 per minute and incoming calls as much as $4 a minute.)
There wasn’t any icing for us to sample, but this Seneca was fitted with full and approved deicing equipment. Ice protection is optional, but virtually all Senecas come with it. Another option this Seneca had, which is probably well worth the extra cost in hot climates, is PiperAire air conditioning — it will set you back an additional $22,000, but you’ll be glad you sprang for it when the asphalt is scorching.
Piper claims a max speed of just over 200 ktas at the Seneca’s 25,000-foot ceiling. I saw cruise speeds at our lower altitude on the day of my test of around 173 ktas. That’s still respectable speed, though a bit slower than a turbo Baron. At 2,500 rpm, the airplane was burning around 12.5 gph per side. Throttling back slowed us to the mid 150s and fuel burn dropped to around 10 gph per side.
Next, we headed back to the airport to try a few circuits in the pattern. Here’s where the Seneca shines, in my opinion. Turning final with two notches of flaps (25 degrees) at 90 knots provides a nicely stabilized descent path. Once the runway was ensured on my first try, I selected full flaps and rounded out for a nice landing. For the next try, I flew with two notches of flaps all the way down final, which allows for a nice tail-low touchdown. I found that the reshaped instrument panel affords good visibility in the flare, providing just the right visual cues to ensure consistently smooth arrivals.
Engine-out performance in the Seneca V is respectable, with a single-engine rate of climb at sea level of 253 fpm. That’s at a lower speed than some other light twins too, so the single-engine climb gradient is comparatively better. At 8,000 feet and ISA+10, the Seneca V will still climb at better than 143 fpm. Even at 16,000 feet and max gross weight, the airplane will barely manage a climb, providing just the peace of mind pilots who opt for twins expect.
As mentioned earlier, sales in Brazil have been a bright spot for Piper, precisely because of the Seneca’s engine-out capability. Flight schools are also taking a closer look at the Seneca, along with Piper’s other light twin, the Seminole. It should come as no surprise that there has also been a good deal of renewed interest among personal fliers and even air taxi outfits. Add them all up, and the Seneca V’s long list of positive attributes compares favorably against the competition.
Not that the Seneca V has much competition, of course. The Beechcraft G58 Baron, Piper Seminole and Diamond’s DA42 are the only other all-weather piston twins in production today, and none of them goes head to head with the Seneca. The Baron is a better performer with a price tag to match. The DA42 and Seminole seat only four, a limitation that eliminates them from consideration for many light twin shoppers. That leaves the Seneca in a market niche all its own.
Piper is doing an admirable job of capitalizing on the dearth of new piston twins in the market by making the Seneca’s cabin even more comfortable and convenient with a variety of amenities, including a cooler integrated into the center armrest. An attractive two-tone paint scheme is another nice touch in the modern-looking space. The Seneca’s large and comfortable cabin also helps accentuate its big-airplane feel, as always. The fact that buyers are left with few alternatives when shopping for a new light twin shouldn’t be a deterrent. For a great many buyers looking for a complete personal airplane with cockpit technology to match, the Seneca V answers the call.

New Piper Seneca V Tough Bird
New Piper Seneca V
Tough Bird
November 5, 2002 By Thomas A. Horne
A proven design still earns its keep
These days, conventional wisdom holds that the market for new piston twins is all but finished — a tiny and shrinking slice on the pie chart of annual general aviation sales. Can it really be that we're watching the twilight of the multis, that their glory years are gone for good, that turbine singles and next-generation mini-fanjets will finish them off completely?
Yes and no. True, the market for twin-engine piston aircraft is comparatively small. But that's always been the case, even from the mid-1950s through the late 1970s. If piston singles rolled out factory doors by the thousands each year back then, piston twins were built by the hundreds. So it's a matter of scale: Piston twins represent a small chunk of the total market, and that market is certainly smaller today than it was 40 years ago.
If the trends realized at The New Piper Aircraft Inc. are any indication, then the demand for piston twins is secure, starting with the Seneca V — the flagship of New Piper's piston fleet. Even with a standard-equipped price of $583,900, the company delivered 41 Seneca Vs in 2001 — which represents almost 10 percent of its 441 total deliveries for that year. This year, New Piper plans on selling 37 Seneca Vs. And most buyers will go for options that push prices closer to $690,000.
Who buys new Seneca Vs? Chris Layson, president of Northern Air, a Grand Rapids, Michigan-based New Piper dealership, says that the typical Seneca V buyer has owned a New Piper Saratoga II for two to three years, although some "come right out of an Archer, just to build multiengine time." For this reason, Layson schedules demonstration flights in Seneca Vs after his Archer and Saratoga buyers pass the two-year mark.
John Lowe, president of Des Moines Flying Service — the oldest Piper dealership in the nation — says that the optional known-icing package ($25,015) is an important draw. "It's a good winter airplane, it can get in and out of 2,700- to 3,000-foot strips easily, it has an excellent single-engine service ceiling, and the turbos give it good performance at high density altitudes," he says. Most of Lowe's Seneca Vs are sold to small- to medium-size companies and serve in corporate fleets. They provide transportation on shorter trips, or swing into action when the company jet is unavailable.
Layson echoes the known-icing draw. "It's not so much that it's got a second engine — though that's a big factor for those who spend a lot of time crossing the Great Lakes — it's that the airplane can get in and out of Michigan and the other states up north in the winter."
As for price resistance, Lowe says that hasn't been a factor. As always, some customers simply want a new airplane and like the security of flying under a warranty. "Besides, a new [Beechcraft] Baron without turbos goes for about $1.1 million, and you can operate two Seneca Vs for the price of one Baron," he says.
New Piper officials point out another reason why some owners are drawn to the Seneca V. Some pilots would like to buy New Piper's turboprop single, the Meridian, but can't meet insurance prerequisites for flying a turbine-powered airplane as pilot in command. The desire for certification for flight into known-icing conditions seals the deal.
Although the Seneca V is based on a 1972 design — the Seneca I — it's the beneficiary of refinements made over the years. The first Senecas came with 200-horsepower Lycoming IO-360 engines. In 1975 the Seneca II offered 200-hp turbocharged Continental ?ngines. The Seneca III came with a 28-volt electrical system, one-piece windshield, Continental TSIO-360 engines of 220 hp, three-blade propellers, and a redesigned Royalite-free instrument panel. The Seneca IV added high-end instrument options, a deicing package, a leather interior, and optional air conditioning. The V came out in 1997 and brought intercooling to the turbocharged Continentals.
The 2002 Seneca V flown for this article was decked out with popular options: copilot instruments ($8,305); Honeywell Bendix/King RDR 2000 vertical profile weather radar ($35,375); air conditioning ($13,490); yaw damper ($4,270); and the known-icing package. It's interesting to note that New Piper won't sell you ice-protection equipment piecemeal. You either buy the full, approved FIKI (flight into known icing) package or nothing at all. This includes pneumatic leading-edge deice boots, electric windshield and propeller heating elements, electrically heated pitot-static probes and stall warning vanes, plus an ice light for illuminating the left wing leading edge to check for ice buildups when flying at night.
The system is effective, but like any ice-protection system it is not designed to take on he worst icing conditions, or to let you mill around in ice-laden clouds for indefinite periods of time. The system merely allows you some extra time to escape icing should it be encountered.
The standard-equipped panel comes with a Garmin GNS 530/430 setup, which gives you a pair of IFR-certified GPS, VOR, localizer, and com radios. A slaved compass system and S-Tec System FiftyFive X autopilot are also standard, as are Garmin's GTX-327 transponder and GMA-340 audio panel with marker beacons and intercom.
If you want even more large-display acreage, then you can order up what New Piper calls the Situational Awareness Package — which was also aboard our demonstration airplane. This adds a Goodrich WX-500 Stormscope and Goodrich SkyWatch traffic advisory system, plus Avidyne's FlightMax 750 Flight Situation Display (FSD). Moving map, lightning, aeronautical charts, radar imagery, and Stormscope returns can all play on the FSD's large color display. The Situational Awareness Package is an extra $41,740, but the Stormscope and SkyWatch option can be bought independent of the Avidyne FSD and play on the Garmin 530 instead.
The panel has a professional look to it, let there be no doubt. The vertical stack of dual Horizon Aerospace engine gauges is a big part of that look, and so is the Flightline Digital Display Monitoring Panel (DDMP). The DDMP is at the top of the engine instrument stacks, and has a rotary mode selection knob that lets you display a wide range of system and performance data. These include engine power output, fuel and electrical system status, temperatures, and any excessive values — such as engine overtemps — along with the duration, peak value, and time of day and date of the exceedance. The DDMP can be set up to show just about any combination of parameters. Especially helpful is the percent-power display. This lets you adjust the engine controls and watch the percent-power display change until.it shows the power output you want.
Fly a Seneca V and you'll quickly understand why Archer and Saratoga pilots make smooth transitions. The control feel is very much like that of a Saratoga — kind of trucky, what you'd expect from a 4,750-pound airplane — and so are the target airspeeds used in the pattern. On short final, the Seneca V can be flown as slow as 82 knots and yes, the airplane is easy to land.
Setting power is no sweat, thanks to the V's automatic wastegates. You simply throttle up to the manifold pressure you want, and the wastegates hold that value as you climb to the critical altitude — the altitude where the wastegates are closed and power output begins to drop off, approximately 19,000 feet according to New Piper. Even so, the V's Rajay turbochargers let you cruise as high as 25,000 feet — but up there you'll need the built-in oxygen system option ($7,406).
The day of our visit to New Piper, five Seneca Vs and seven Seminoles were being readied for delivery. The Seminole also figures prominently in New Piper's sales mix. It's the only multiengine trainer in production, and last year 62 were sold. This year New Piper thinks it will sell 70. Add that to the Seneca Vs planned for 2002 delivery and you've got reason to convince yourself that there will always be a market for hard-working new piston twins like these.
E-mail the author at tom.horne@aopa.org.
SPEC SHEET
New Piper PA-34-220T Seneca V
Base price: $583,900
Price as tested: $740,100
Specifications
Powerplants220-hp (ea) Teledyne Continental TSIO-360
Recommended TBO1,800 hr
PropellersHartzell two-blade, 76-in dia
(three-blade McCauley, 76-in dia, optional)
Length28 ft 7 in
Height9 ft 11 in
Wingspan38 ft 11 in
Wing area208.7 sq ft
Wing loading21.2 lb/sq ft
Power loading10 lb/hp
Seats6
Cabin length10 ft 4 in
Cabin width4 ft 1 in
Cabin height3 ft 6 in
Standard empty weight3,413 lb
Max ramp weight4,773 lb
Max takeoff weight4,750 lb
Max zero fuel weight4,479 lb
Max useful load1,337 lb
Max payload w/full fuel605 lb
Max landing weight4,513 lb
Fuel capacity, std128 gal (122 gal usable)
768 lb (732 lb usable)
Baggage capacity
Forward, external100 lb, 15.3 cu ft
Aft, internal85 lb, 17.3 cu ft
Performance
Takeoff distance, ground roll1,143 ft
Takeoff distance over 50-ft obstacle2,180 ft
Accelerate-stop distance, 0 flaps2,650 ft
Max demonstrated crosswind component17 kt
Rate of climb, sea level1,460 fpm
Single-engine ROC, sea level253 fpm
Cruise speed/range w/45-min rsv (fuel consumption)
@ High-speed cruise, 10,000 ft182 kt/635 nm (28 gph)
@ Normal cruise, 25,000 ft200 kt/645 nm (24 gph)
Max operating altitude25,000 ft
Service ceiling25,000 ft
Single-engine service ceiling16,500 ft
Landing distance over 50-ft obstacle2,180 ft
Landing distance, ground roll1,143 ft
Limiting and Recommended Airspeeds
V R (rotation)81 KIAS
V X (best angle of climb)83 KIAS
V Y (best rate of climb)88 KIAS
V XSE (best single-engine angle of climb)83 KIAS
V YSE (best single-engine rate of climb)88 KIAS
V MC (min control w/one engine inoperative)66 KIAS
V SSE (min intentional one-engine operation)85 KIAS
V A (design maneuvering)139 KIAS
V FE (max flap extended)113 KIAS
V LE (max gear extended)128 KIAS
V LO (max gear operating)
Extend128 KIAS
Retract107 KIAS
V NO (max structural cruising)164 KIAS
V NE (never exceed)204 KIAS
V S1 (stall, clean)67 KIAS
V SO (stall, in landing configuration)61 KIAS
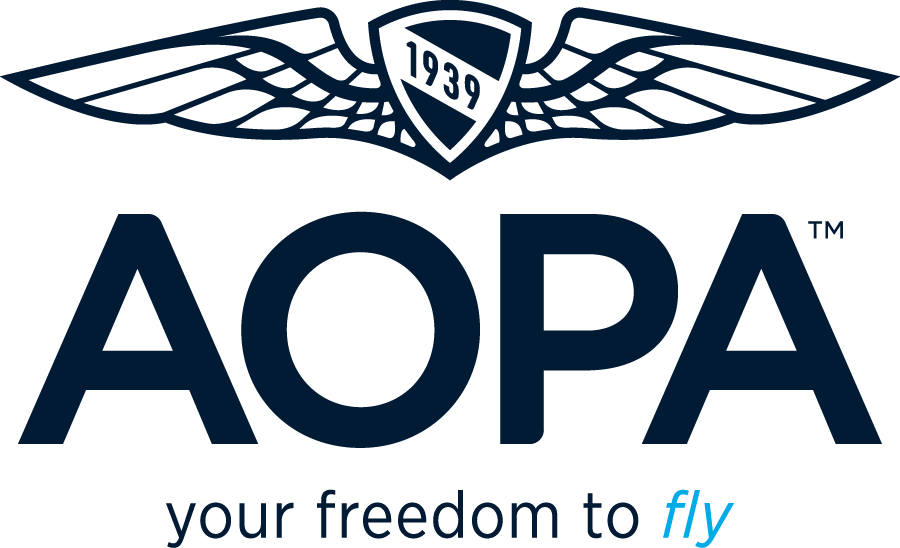
Beechcraft King Air 90
Beech has produced six different basic King Air models, with the 90 series the smallest. The first Model 90 King Air was introduced in 1964; it was basically a Queen Air with turboprops. After its introduction, the 90 series went through a number of airframe and powerplant modifications. The King Air competes with other turboprops such as the MU-2, Conquest, and Cheyenne 400 LS. Beech airplanes are now being built by Hawker Beechcraft Coorporation.
The original Model 90 was powered by a Pratt & Whitney PT6. The PT6A-6 did not have a reverse-pitch prop. Over time, both the engine and the powerplant grew. The A90 came along in 1966 with reverse pitch props, increased cabin pressure (3.1 psi to 4.6 psi), the PT6A-20 engine, and a gross weight increase of 300 pounds. In 1968, the B90 brought an increase in wingspan, recontoured rear fuselage, balanced controls, and a 350-pound gross weight increase. The C90 was next to be introduced in 1971, with a new cabin pressurization system that used bleed air from the engines (which increased cabin noise and reduced engine power). In 1976, the C90 received a new engine, the PT6A-21. Another increase in cabin pressure (to 5 psi), a 15-knot cruise speed increase (due to an increase in the interstage turbine temperature [ITT]), a stronger horizontal stabilizer, and a new cabin door (borrowed from the King Air 200) was introduced in 1982 on the C90-1. The C90A brought redesigned engine cowlings that reduced drag and boosted ram airflow to the engines (resulting in a 12-knot increase in cruise speed), an electrical landing gear system, and a rudder boost system that eased the pilot work load during single-engine operations. Also included on this model (due to concerns about wing strength and cracking wing bolts) was a bonded spar cap, running the length of the wing using shear fittings instead of bolts. The E90 featured a PT6A-28 engine in 1972, and in 1979, the F90 appeared with a T-tail, 750-shp engines, and a 600-pound increase in useful load. The PT6A-135A engine was placed in redesigned cowls, which once more decreased drag and increased ram air recovery, allowing for an increased cruise speed of 15 knots and improved climb/takeoff distance in the F90-1 in 1983. Due to extremely high overhaul costs and difficulty in locating parts, beware when purchasing a King Air with PT6A-6 and -20 engines. Some mechanics even refuse to overhaul the PTA6-6 engines. Parts aren’t generally hard to find for the rest of the King Airs, but they are expensive. A 1,250-hour hot section inspection is recommended. The King Air typically has the club seating arrangement, and a fifth "side-facing" seat is available for the back. Some of the modifications available for the King Air include four-blade Hartzell props, dual aft body strakes, main gear landing doors, wing lockers, and exhaust stack fairings.
When compared to the Mitsubishi MU-2, the Beech King Air has modest performance, not its strong selling point. The King Air is best known for excellent handling characteristics and comfortable, spacious cabin. Pilots describe the controls as "light and pleasant," and the transition from a piston twin to the King Air as relatively easy. In some of the Model 90s, cruise speeds are only slightly over 200 knots. One pilot noted that "above 20,000 feet, performance diminishes." Single-engine performance is described as docile and landing characteristics as good. Cabin noise level is lower than the MU-2.

Beechcraft C90T
Beechcraft King Air C90GT
The Beech King Airs owe four decades of success to having the best mix of cabin comfort, performance, excellent flying qualities and famous reliability. The new C90GT keeps the comfort and wonderful flying feel that pilots love and deliversa lot more performance. It can't catch the light jets, but it has dented their speed advantage without giving up cabin and cockpit room and comfort. The C90GT airframe is the same basic size as the original King Air with four to five passenger seats and the roomy squared-oval cabin shape. What makes it a "GT" are new Pratt & Whitney PT6 engines, and new four-blade propellers, that increase cruise speed by at least 25 knots and improve climb rates by as much as 50 percent at higher altitudes, all without shortening range on the same amount of fuel. The C90GT formula isn't magic. In fact, there are field modifications that exchange the original for more powerful engines on existing King Airs. But the GT is a new airplane, not just new engines. The PT6A-135A engines on the GT are rated at 550 shaft horsepower just like the Dash 21 engines they replace. But the new Pratts are really 750-shp engines that have been restricted to the lower maximum output for takeoff. That means as the GT climbs, the new engines can keep putting out full-rated horsepower to a much higher altitude. The earlier King Air 90s hit max speed at about 16,000 feet, but the C90GT hits its stride at 25,000 feet, or higher.
I got to fly the first C90GT and the climb performance was unlike a regular King Air 90. It was the prototype and lacked a complete interior, but our takeoff weight was just 600 pounds under maximum with full fuel and some other equipment onboard. Immediately after takeoff the C90GT climbed steadily at 2,200 fpm and held near that rate up to 15,000 feet, and then maintained an 1,800 to 2,000 fpm climb through 18,000 feet. We were still going up at 1,500 fpm when I leveled at 25,000 feet just 15 minutes after takeoff, with that time including a brief leveloff. That's an easy seven or more minutes less time to climb than the previous model.
Article Continues Below:
Aerobatics with Matt Chapman at Oshkosh 2016
Flying magazine met up with airshow performer Matt Chapman in Oshkosh for ...
Level at 25,000 feet, the C90GT accelerated until the indicated airspeed hit the Vmo limit of 186 knots, and that translated into 270 knots true airspeed. Total fuel flow was around 440 pounds per hour. That's a solid 25 knots faster than the earlier C90B at its best altitude, and 40 or more knots faster at 25,000 feet. Fuel flow was higher at that level, but the speed was so much greater that useful range is the same because flight time is reduced.
The C90GT is certified to 30,000 feet, and with the new engines can quickly climb to that level and cruise at nearly 260 knots, but I don't think many pilots will use that flight level often. One reason is that with five psi maximum cabin pressure, the cabin altitude is near 12,500 feet when flying at 30,000 feet. That's legal, but not comfortable for every pilot. Also, there is the issue of reduced vertical separation minimum (RVSM) requirements to fly above 28,000 feet. The King Air can meet the requirements, but it's an extra hassle for not much return in fuel efficiency. The cockpit of the GT is noticeably quieter thanks to props that turn a maximum of 1900 rpm compared to 2100 rpm before. The cabin on the 90 series King Airs has always been remarkably quiet and comfortable, but the cockpit is quite close to the prop tips and therefore not as quiet. The lower prop rpm really helps up front.
But the reduced maximum propeller rpm would have added to takeoff runway requirements if Beech had not made some operational changes. Though the new propellers and operating rpm are very efficient at climb and cruise, they cannot match the static thrust of the high rpm props for takeoff. So, for the first time a C90 King Air uses flaps for takeoff. With the first notch of flaps down, the new C90GT uses the same amount of runway for a sea level takeoff as the C90B. At higher elevation airports, particularly on hot days, the GT uses many hundreds of feet less for takeoff because of the new derated engines ability to continue to deliver maximum power under hot or high takeoff conditions.
Automatic propeller feathering has been available on the C90 King Airs, but was an option and not part of the airplane's required equipment as it is on the larger King Airs. For the C90GT autofeather is now standard, as is rudder bias. If an engine quits on or shortly after takeoff, the autofeather system automatically brings the dead engine propeller to feather and the rudder bias steps on the opposite rudder to keep the airplane flying straight. The rudder bias system uses bleed air pressure from the operating engine to push the rudder in the proper direction. It's a very simple system with no electronics or complicated parts. You will need to add a little foot pressure to the pedal on the good engine side yourself, but in those critical seconds after an engine failure, the C90GT with rudder bias and autofeather takes care of itself while the pilot concentrates on airspeed control. I am lucky to have the chance to fly many business jets of all sizes, and whenever I get back into a King Air cockpit I'm always pleasantly surprised by the room, particularly the headroom. King Air's have more cockpit headroom than all light jets, and even many of medium size. Pilots on the tall side will really appreciate the headroom, but pilots of any size can find a seating position that gives good visibility over the nose and to the sides. I'm 6 feet 2 inches tall, and I raise the seat in the King Air from its lowest setting, something I never do in the light jets, or even some medium-sized ones.
You won't confuse the C90GT cockpit with any brand new design turbine airplane because this King Air still has toggle switches, gauges for various systems, and only basic electronic flight instruments. But there is no denying the big airplane feel of the C90GT. The windshields are heated electrically instead of with engine bleed air and there are wipers to clear rain. The control wheels and power levers have a confidence inspiring heftiness. And you sit up high looking down on lesser airplanes, including many jets.
Passengers appreciate this same sense of size and sturdiness when they climb the airstair. There is room for a private potty in the rear of the cabin, and baggage space is internal so your stuff can be reached in flight. Beech has upgraded the C90GT cabin furnishings, including using the chairs from the top of the line King Air 350. Beech experimented with a recommended propeller 1700-rpm cruise setting, which did quiet the cockpit a little. However, when the sound level was "mapped" inside the passenger cabin, the level was higher at 1700 rpm because the noise damping had been designed to be most effective at 1900 rpm.
The logical question many ask about the C90GT is, why not buy a jet? The Cessna Citation Mustang is priced about the same, or maybe a little less, than the King Air, and is expected to have a top cruise speed almost 70 knots faster and a ceiling 11,000 feet higher. The answer for many owner-pilots is that the King Air's attraction is that it is not a jet.
The new light jets will have a cruise speed advantage on the C90GT, but it will be measured in just a few minutes over trips of several hundred miles. And if the little jets are held down low below their optimum altitudes-as is likely in congested parts of the country-the turboprop will save money at the fuel pump.
The King Air 90 family has an excellent safety record while being flown by owner-pilots. It is a logical step up from a piston twin with essentially nothing new for a pilot to learn in basic airplane handling. Pilots can have confidence in their ability to fly the GT, and more importantly, insurance companies understand the risks. The new crop of light jets has the potential to be very safe, but the industry has little experience with large numbers of single-pilot owner flown jets so there will be an abundance of caution by all.
The C90GT is already a hit with annual sales more than double the previous model, and orders are accelerating. It's an old-fashioned airplane in many ways, but gains in performance without sacrificing any of its proven qualities. As has happened so many times in the life of the King Air, it's time to take another look.
Beech King Air C90GTThe airplane flown for this report was the first one off the production line.It was equipped with Collins Pro Line remote-mounted avionics, including four-inch electronic flight instruments on the pilot's side. A Garmin GPS 400is also included. All information comes from the airplane manuals and represents standard day conditions at maximum weight unless noted.
Typically equipped price $2,952,000 Engines P&W PT6A-135A, 550 shp each TBO 3,600 hrs Propellers Hartzell 4-blade, 90-in dia Passenger seats (typical) 5 Cabin height 4.8 ft Cabin width 4.5 ft Cabin length 12.6 ft Overall length 35.6 ft Overall height 14.3 ft Wingspan 50.3 ft Wing area 294 sq ft Wing aspect ratio 8.6 Max ramp weight 10,160 lbs Max takeoff weight 10,100 lbs Typical empty weight 6,950 lbs Max useful load 3,010 lbs Zero fuel weight none Max fuel capacity 2,573 lbs Payload, max fuel 637 lbs Max landing weight 9,600 lbs Wing loading 34.4 lbs/sq ft Power loading 9.2 lb/shp Ceiling (certified) 30,000 ft Pressurization 5 psi Sea level cabin to 11,065 ft Takeoff runway 2,719 ft Climb to FL 250 17 min Climb rate 1,777 fpm Engine out climb rate 474 fpm Engine out climb gradient 708 ft/nm High speed cruise 270 kts Long range cruise 206 kts IFR range at max cruise 1,068 nm 600 nm mission 2 hr, 23 min Trip fuel 1,360 lbs Landing distance 2,290 ft Vmo 226 kts
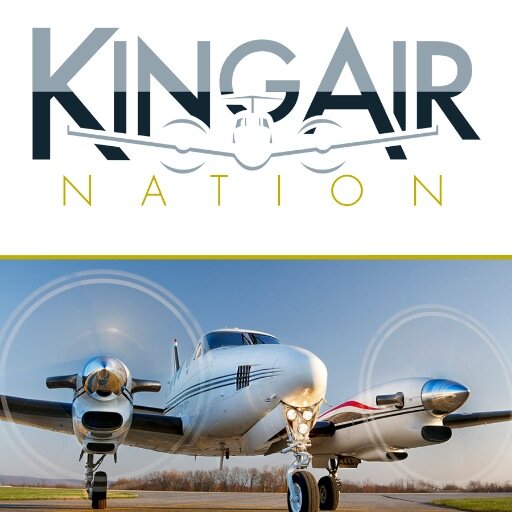
King Air 90
The Model 90 King Air began its life as the Model 120 in 1961. In May 1963, Beechcraft began test flights of the proof-of concept Model 87, a modified Queen Air with Pratt & Whitney Canada PT6A-6 engines. Two months later Beech publically announced the Model 87 with orders began being accepted for the “King Air” a month after that. The first definitive prototype was designated the Model 65-90 and flew for the first time on January 24th, 1964. Deliveries would occur later that year on October 8, and by the end of the month, 152 aircraft had been ordered with seven being built before year’s end.
Over the following decades, Beechcraft began to introduce new models which updated and improved the Model 65-90 design. The Model 65-A90 came with PT6A-20 engines. The Model B90 came with a 9650 TOGW, improved ailerons, increased wing span, improved instrumentation and pressurization and had an extra side window. The Model C90 began using the Model 100 cabin environment and pressurization system and came equipped with 550 shp PT6A-engines. The Model C90-1 came with an E90 tailplane and improved power output and an increased maximum cabin pressure differential.
Next, the Model C90A was built which featured improved landing gear retraction, improved electrical system and used the F90-1 pressurization and heating system. The C90A had two updated versions: the first was the C90B, which featured an improved airframe, four-bladed propellers, and propeller synchrophasing; with the focus on reducing cabin noise. The second, the C90SE (Special Edition), was a cheaper version which had three-bladed propellers, standardised interior and mechanical instruments instead of the Electronic Flight Instrument System (EFIS) fitted to the C90B.
In July 2005, Beechcraft introduced the C90GT at the Oshkosh Airshow. It featured PT6A-135A engines, (750 shp flat rated to 550 shp), for better climb and cruise performance. Two variants would follow: the C90GTi which featured the “glass cockpit” Collins Proline 21 avionics suite and then the Model C90GTx with Winglets as a factory-standard and an increased maximum take-off weight of 10,485 lb (4756) for better full-fuel payload flexibility.
Additional models include:
E90 - broadly similar to the Model C90, which it was produced in parallel with. The E90 featured PT6A-28 engines.
F90 - A further refinement of the 90 series. Featured the T-tail of the Model 200 King Air mated to the fuselage and wings of the E90, with PT6A-135 engines.
F90-1 - superseded the F90; offered improved performance by offering PT6A-135A engines (885 shaft horsepower at max takeoff power, compared to 850 power for the -135).
H90 - a trainer version of the U-21, designated the T-44A Pegasus. Was used to train United States Navy, Marine Corps, Coast Guard, and Air Force pilots to fly multi-engine aircraft.
King Air 90 Technical Data
Select a model
model 90
MFG Info
Type Cert # 3A20
In Operation 25
Years Made 64 - 66
SN's Eligible LJ-1 through LJ-113 (except LJ-76)
Deminsions LxHxWS 35.5' X 14.7' X 45.1'
Cabin Dimensions LxHxW 12'8" X 4'8" X 4'8"
Fuel Capacity (lbs/gal) 2,573/384
Operating Costs
Engine Info
Performance

Beechcraft King Air 200 Transformation
Beechcraft first introduced its twin-turboprop series in 1964 with the King Air C90. Its roots sprouting from Beechcraft's Twin Bonanza and Queen Air seeds, the airplane became so successful that the Wichita, Kansas-based company quickly decided to launch a larger commuter version called the Beech 99, introduced only a few years after the King Air first entered the market.
The King Air has expanded into a wide variety of models within four main groups: the 90, 100, 200 and 300, of which around 7,400 have been delivered to date. While the 100 series has been dropped, Beechcraft offers four models: the King Air 90GTx, 250, 350i and 350ER under the Textron Aviation umbrella.
Today's King Airs are delivered with Rockwell Collins' highly capable Pro Line 21 avionics, the exception being the King Air 250, for which customers can choose the company's sleek Fusion touch-screen suite.
However, as with anything new, you pay a premium for a King Air rolling out of Beechcraft's delivery hangar in Wichita, Kansas. The smallest version, the C90GTx, costs right around $3.8 million, and if you want more space and performance the price follows with size. So, for King Air owners who suffer from panel or performance envy, it may make sense to make upgrades through modifications under supplemental type certificates (STCs). We'll focus this article on STC upgrades that are available for one of the most popular models, the King Air 200/B200 series.
The first step toward making your airplane look and feel new is through paint and interior upgrades. There are terrific paint and interior shops all over the country, and they can help you customize the airplane to your own desires, limited to some degree by the FAA, but mostly limited by your own imagination and budget.
With a massive leap in avionics technology in the past couple of decades, one of the most appreciated upgrades for the pilots is avionics. If you want a full glass panel there are some great options to be had as aftermarket STC'd installations.
While it is great to have a fresh look and new tools to provide greater situational awareness — inflight weather and all of the other benefits glass can offer — performance and efficiency rank very high for pilots and passengers alike. No matter how much people love to fly, they rarely argue against getting to the destination a few minutes earlier or climbing away from the granite more quickly.
There are a few ways to get that highly desired performance, whether by structural modifications or simply a more powerful power plant. Seattle, Washington-based Raisbeck Engineering has a long list of mods for all King Air products, some of which have been adopted into factory-new models.
One of the most effective mods for the King Air 200 is the ram air recovery system, comprised of small, flaplike pieces and seals installed at the rear end of the air intake of the PT6A. This system increases available horsepower by as much as 8 percent, reduces fuel burn by 8 to 11 percent and drops interstage turbine temperatures by about 20 degrees.
Raisbeck's enhanced performance leading edges not only increase cruise speed and reduce stall speed, but also make the intercooler for the air-conditioning system more effective. Last but not least, the high-flotation gear doors (used only with wide-tire-equipped gear) reduce drag and increase speed by 8 to 12 knots.
A couple of Raisbeck's mods are not designed to improve performance, but they make the cabin occupants a whole lot happier. The swept four-blade propellers (co-designed with Hartzell) reduce noise significantly, and the dual aft-body strakes (two fins below the aft fuselage that redirect airflow) reduce vibration and noise. A customer at West Coast Charters, which operates three King Airs, has seen enough of a difference that he won't fly in a King Air without strakes, says Kenneth Stave, the company's senior pilot and training captain.
Raisbeck's Epic Platinum package for the King Air 200 and B200 includes all of these above-mentioned modifications and costs $208,714 plus installation (or $163,880 without the high-flotation gear doors). Raisbeck claims this combination can result in a reduction in takeoff distance by as much as 1,000 feet, a reduction in time by as much as 12 minutes to climb to 33,000 feet, and an increase in cruise speed by as much as 14 ktas at 33,000 feet.
Another more obvious way to get a performance upgrade is by swapping the two Pratt & Whitney PT6A power plants to more powerful ones. If you want a double whammy you are in luck as Raisbeck's King Air 200 mods are compatible with STC-approved engine upgrades that are available for the King Air 200 through two companies: StandardAero and Blackhawk Modifications.
StandardAero, based in Scottsdale, Arizona, has done repair and overhaul work on PT6A engines for more than 20 years, but about five years ago the company also began offering engine upgrades for Piper Cheyennes, King Air 90s and King Air 200s. Meanwhile, Blackhawk Modifications out of Waco, Texas, has acquired several STCs for turboprop engine upgrades since it started with the Cessna 425 Conquest I in 1999. Blackhawk has upgraded more than 500 PT6A installations on Beechcraft King Airs, Cessna Caravans and Conquests and Piper Cheyennes. More than 200 King Air 200s have received the popular power boost through the company's XP61, XP52 and XP42 programs with Dash 61, Dash 52 or Dash 42 PT6As, respectively, since Blackhawk took on the type project around 2007.
Both StandardAero and Blackhawk claim that the difference in cost of a complete engine overhaul compared to an upgrade to a new engine is low enough that the benefits of the latter clearly outweigh the price, particularly for airplanes with high-time engines. Pratt & Whitney Canada has made several modifications to its highly popular turboprop in the past couple of decades. Blackhawk's senior vice president of sales and marketing Edwin Black said that since the original version of the PT6 engine was first delivered in 1963, there have been more than 230 service bulletins and product improvements. All of those have been addressed or incorporated into the latest models.
The operating cost of an upgraded King Air may also be lower. According to a study conducted by Conklin & de Decker in 2009, the annual cost savings for a Blackhawk XP61 upgraded King Air 200 over a Dash 41-powered one for an airplane flying 100,000 nm was greater than $50,000. With fuel prices being higher six years later, the delta is likely even higher today. At five years or 2,500 hours, the warranty on a new engine is also far superior to that of an overhauled one.
Both the Dash 41 and 61 engines have the same power rating: 850 shp. However, the Dash 61 produces full torque, 2,230 foot-pounds, all the way up to 22,000 feet, while the Dash 41 can only produce full power to 10,000 feet. The improvement in climb and cruise capability at higher altitudes with the upgraded engine is significant.
I had a chance to check out the performance improvement of one of Blackhawk's King Air upgrades at Cutter Aviation at the Phoenix Sky Harbor International Airport (KPHX) in Phoenix. N350C, the King Air I climbed into at KPHX, is one of 12 airplanes on charter with Cutter, a company that first started out in the charter business when William P. Cutter opened the doors of Cutter Flying Service in Albuquerque, New Mexico, in 1928. The company has remained in the family through the decades and is now operated by president and CEO William W. Cutter. Charter is only one of many service offerings at the company's facilities in Albuquerque, Dallas, El Paso, Colorado Springs and Phoenix, where there is a second facility at Deer Valley Airport. Each location has its own service offerings, which in addition to charter could include maintenance and full FBO services.
N350C is a 1980 model King Air 200 that Cutter purchased about three years ago, says Gordon Paige, the company's director of flight operations. Being a high-time airplane in excellent condition despite 35 years on its wings, it was a perfect candidate for an engine upgrade.
Cutter decided to go with Blackhawk's XP61 upgrade. The facility at Sky Harbor is an authorized Blackhawk dealer, so Cutter's own maintenance team did the installation.
Cutter is one of several dealers around the country that Blackhawk works with for engine installations. Blackhawk's flight operations and sales manager Chris Dunkin claims the installation for the XP61 engine upgrade for the King Air 200 takes about two weeks. Cutter's installation took longer because other non-Blackhawk-related changes were made as well, such as painting the trusses, swapping out the hose kit and adding Frakes Aviation exhaust stacks, says Kevin Reedy, Cutter's service manager. The airplane kept the same four-blade Hartzell propellers.
Despite the fact that the new engine is bigger, there is no cowl mod required. The only things that give away the goodness beneath the cowls are a small access panel on one side of each and the shiny, curved exhaust pipes that protrude on both sides.
Before the mod, N350C would cruise at right around 260 ktas, burning 260 pounds per hour per engine at 27,000 feet at 97.5 percent Ng, 1,800 rpm and 1,300 foot-pounds of torque, according to data collected by Blackhawk. We had a fairly light load with four people on board, but it was a typical smoking hot day in Phoenix when we took off from Sky Harbor at the end of August. Despite the 100-degree temps, the airplane took off in about 3,500 feet from a rolling start while staying below the maximum ITT.
I watched the gauges as we climbed out at 160 kias, about 30 knots faster than Vy, to keep the engines cooler. Despite the faster speed, the airplane maintained a climb rate of 2,200 fpm. At 11,000 feet, indicating 155 knots, we saw around 2,500 fpm.
At 19,000 feet, I asked if we could check the single-engine performance. Paige, who was in the captain's seat, approved. Without blinking an eye, he feathered the left engine and the airplane kept right on climbing at 500 fpm at 130 kias.
I was not able to record a time-to-climb value as the busy Phoenix airspace required the controllers to level us off multiple times, and the heat had us climbing at higher airspeed. But at a constant 2,500 fpm climb, we would have made it to our target altitude of 27,000 feet in less than 11 minutes.
Once at FL 270, it was time to compare the cruise performance with the numbers N350C was showing before its Blackhawk transformation. At ISA+15 Blackhawk's proprietary engine gauges indicated 98 percent Ng, 1,800 rpm, and 1,700 foot-pounds of torque — a 400 foot-pound increase. At those settings, we were burning about 320 pounds per hour of fuel per engine. But we were indicating 190 knots, which translated to 295 ktas, about 35 knots better than with the original engines at comparable power settings.
While I found this impressive, Dunkin said he was disappointed. "On an ISA day, we would have seen well over 300 knots," he said.
Dunkin said the price for the Blackhawk XP61 STC, which includes two Pratt & Whitney Canada PT6A-61 engines, is $945,000 plus the cost of installation for the King Air 200 series. The upgrade is also available for the King Air 250 for $999,000. With run-out engines, the upgrade appears to make a lot of sense.
There are many variables to consider before making a final decision on whether to upgrade an older airframe or purchase a new one. That new airplane smell is always a compelling argument and there are often tax incentives that go along with a new airplane. But if you are happy with your airplane, these upgrades will help you take the satisfaction of ownership into the modern era.
See more King Air 200 photos here.
Pratt & Whitney Canada PT6A-61
Pratt & Whitney Canada's PT6A series turboprop engines range in power ratings from 500 to 2,000 shp. The company has produced more than 69 versions of the PT6A for a wide variety of aircraft, serving anything from executive business travel to rugged cargo deliveries in extreme climates. The engines have been famously reliable with more than 335 million flight hours accumulated by more than 41,000 engines.
The PT6A is a two-shaft engine with a multistage compressor driven by a single-stage compressor turbine. Air enters the engine through a reverse-flow inlet with a screen preventing foreign object debris from entering into the combustion chamber. The Dash 61 engine used in Blackhawk's XP61 upgrade that was installed in N350C incorporates a two-stage axial power turbine. An independent shaft couples the power turbine to the propeller through an epicyclic concentric reduction gearbox, which converts the turbine power to propeller speeds ranging from 1,700 to 2,200 rpm. Because the power-producing part of the engine is not directly coupled to the propeller, the engine design is called a "free turbine."
Performance Boost
At 850 shp, the power rating is the same for the PT6A-41 engines installed in the stock King Air 200 and the Dash 61s in Blackhawk's XP61 upgrade. However, the thermodynamic power rating of the PT6A-61 is much greater because it can withstand higher temperature, pressure and turbine speed. Therefore, the Blackhawk XP61-modified King Air can produce full power, or more torque, at much higher altitudes than the original King Air 200 engine could.
As a result, the XP61 engine modification delivers impressive performance improvements. Here are some specs provided by Blackhawk for a stock King Air 200 versus one with the Blackhawk XP61 engine STC.

Beechcraft Super King Air 200
Years ago the airlines and other turbine-aircraft operators were paying as little as 11 cents for a gallon of kerosene. But, in an unexpected flash of history, bargain-basement fuel prices vanished forever.
Fuel consumption had been a relatively unimportant factor when considering the purchase of a new vehicle, but OPEC changed all that. As a result, large cars are yielding to small ones, and pure-jet aircraft find themselves competing against the slower, but less “fuelish” turboprops.
This partially explains why many aircraft purchasers are willing to pay for a Beech Super King Air 200 when some of the less expensive business jets sell for very little more. For it is after the purchase is made that the economic curves often bend in favor of the turboprop, especially when stage lengths aren’t particularly long.
Beech’s T-tailed entry, for example, carries nine people on a 500-nm flight while burning only 156 gallons of kerosene in the process. This results in a fuel consumption of 33 passenger-miles per gallon. Small business jets, on the other hand, do not approach this level of fuel economy.
The pure jet aircraft is, of course, significantly faster, but on a 500-nm flight, the difference in flight time is on the order of 20-30 minutes. The prospective buyer must determine how much extra fuel he is willing to burn to save half an hour en route.
There are other turboprop advantages. These aircraft are not banned from certain noise-sensitive airports, and a turboprop can be flown by a single pilot; jets must be operated by a crew of two. And because the Beechcraft Super King Air tips the scales at only 12,500 pounds, the lone pilot is not required to seek a type rating from the FAA.
Other features of the relatively new aircraft are comfort, an extremely quiet cabin, extraordinary stability, excellent control response and beauty. There’s no denying that the T-tail gives the Super King Air a long, lean, aesthetically pleasing profile.
But the lofty horizontal stabilizer (it’s 15 feet above the ground) serves more than cosmetic purposes. Since it is well above the downwash of the wing, flap deployment and retraction results in the need for very little trim correction.
Without going into a lot of colorful adjectives, the Super King Air’s flight characteristics are easily summed up as being simply marvelous; it’s an easy airplane to maneuver. The only flight characteristic likely to catch the uninitiated off guard is the airplane’s extraordinarily efficient elevators. These create a tendency to overcontrol slightly in pitch during the landing flare when only a small amount of elevator back pressure is needed. After a few touch-and-go’s, however, the adjustment to this becomes automatic.
The Super King Air is a “go anywhere, go anytime” airplane and is certificated for flight into known icing conditions. The engine inlet ducts are heated with exhaust gas; an engine oil heat exchanger automatically heats fuel to prevent ice crystals from collecting in the fuel controller; pneumatic fuel-control lines are wrapped in electrically heated blankets; and the fuel tank vents, which are situated in such a way as to preclude the possibility of icing, are provided with electrical heating in case the impossible becomes possible.
Inertial separators (a pair of movable deflectors located in the intake ducts) prevent the engine inlet screens from choking with ice. These separators can also be used during operations on unimproved runways and taxiways to prevent the engine from ingesting foreign objects.
The windshields are electrically heated; the leading edges of the wings and horizontal stabilizers are protected with electro-pneumatic boots, and both pitot masts and propellers are electrically heated. To prevent damaging the heating elements on the propellers, a timing device alternately routes electrical current to each propeller for only 30 seconds at a time, which is sufficient to protect the blades during the worst conditions.

NASA Armstrong Fact Sheet: B200 King Air Mission Support/Research Aircraft
NASA Armstrong Fact Sheet: B200 King Air Mission Support/Research Aircraft
Two Beechcraft King Air mission support aircraft in flight over California's Mojave Desert.
Credits: NASA Photo
NASA Armstrong Flight Research Center operates two Beechcraft B200 Super King Air aircraft for flight research and mission support. One of Armstrong's King Air aircraft, NASA 801, (N801NA) serves as a testbed for various research projects, and is also flown for a range of mission support activities. The other aircraft, NASA 7 (N7NA), can carry up to 11 passengers and is primarily used for pilot proficiency and for transporting personnel on NASA business to locations not served by regular airlines.
Experiments flown on King Air #801
King Air N801NA has been the test aircraft for a variety of flight experiments, among them:
The Hi-rate Wireless Airborne Networking Demonstration (HiWAND). This research project flown in late 2005 demonstrated wireless modem and data transmission capability over the Internet from the aircraft via a line-of-sight telemetry link.
The X-38 Space-Integrated GPS Inertial Navigation System experiment was flown on 801. It led to the GN&C system now on ISS.
The Flying Infrared for Low-Level Operations project, an experiment flown on NASA 801, dealt with night vision devices and low altitude operations.
About the Aircraft
The Beechcraft King Air is a widely deployed general aviation aircraft, commonly used for business travel, express cargo delivery and related purposes. The U.S. military also operates the King Air as the C-12 Huron utility transport. Based upon the earlier King Air 100, the King Air 200 was developed in the early 1970s with the first flight of the prototype in October 1972. The King Air 200 was awarded its airworthiness certificate by the Federal Aviation Administration under FAR Part 23 in December 1973.
The B200 Super King Air is an evolutionary aircraft that has better performance than the original King Air 200 due to upgraded engines. NASA acquired its two Super King Air aircraft in the early 1980s; NASA 7 in 1981 and NASA 801 in 1983.
NASA's Beechcraft B-200 Super King Air is shown on the ramp at the Armstrong Flight Research Center. The twin-turboprop aircraft, used for research and mission support functions, recently was fitted with wingtip winglets that improve aerodynamic efficiency and reduce fuel burn.
Credits: NASA Photo / Carla Thomas
Aircraft Specifications
Wingspan: 54'6"
Wing aspect ratio: 9.8 to 1
Wing loading, maximum: 41.3 lbs/sq ft
Length: 43'9"
Height: 15'
Empty weight: 7,315 lb
Maximum takeoff weight: 12,500 lb
Engines: Two United Aircraft of Canada PT6A-42 turboprop engines rated at 850 shp. driving three-blade constant-speed full-feathering reversible propellers.
Crew: Two pilots, with full dual controls and instruments.
Payload: Up to 11 passengers, depending on cabin configuration. Up to 400 lbs baggage in rear compartment. NASA 7 also has additional cargo stowage in an underbelly container.
Service ceiling: 32,800 feet
Maximum speed at 15,000 feet: 289 knots (333 mph)
Cruising speed at 25,000 feet at average weight: 273 knots (313 mph)
Stalling speed, full flaps: 76 knots (87 mph)
Maximum Range: 915 to 1,800 nm (1,053 to 2,075 statute miles) at 27,000 feet with full fuel, depending on payload.
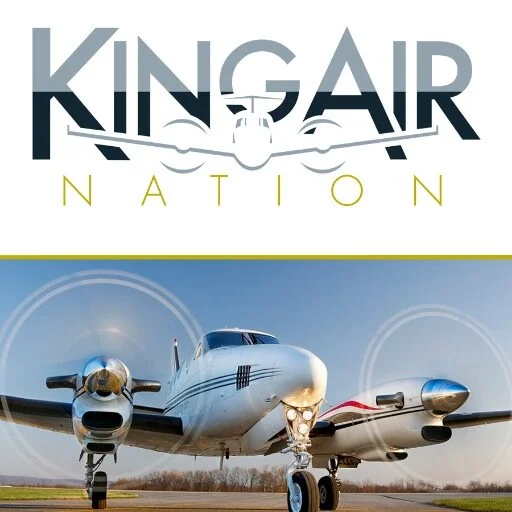
King Air 200
King Air 200
About the King Air 200
Originally conceived as the Model 101 in 1969, the Model 200 was a development of the Model 100 King Air. It had essentially the same fuselage as the Model 100, with changes to the rear fuselage to accommodate a new T-tail and structural changes to allow higher maximum pressurization. Changes included Pratt & Whitney Canada PT6A-41 engines rated at 850 shp and increased wingspan and extra fuel capacity over the Model A100 then in production. The first prototype flew October 27th, 1972 with a second prototype took to the air on December 15th that same year. The 200 received civil certification in December 1973 with the first civil delivery took place February 1974.
The Model 200T was the next model in the series, developed in 1976. This was specially designed for aerial surveying or reconnaissance. Modification changes included changes to the belly aft for photography with a vertical camera, a surveillance radar in a pod under the fuselage, dome shaped windows on the sides of the rear fuselage allowing observation, and a 50-US-gallon (190 L) fuel tank on each wingtip to increase the aircraft's range. In 1979, the Model 200C was created with a large cargo door, allowing a large range of items to be loaded into the cabin. They quickly became popular with operators who fitted them out internally as air ambulances. In 1981, Beechcraft modified a Model 200C as the Model 200CT fitted with the same wingtip fuel tanks as installed on Model 200Ts.Only one was created, but it lead to the Model B200 which entered production that same year.
The Model B200 was fitted with PT6A-42 engines that resulted in greater aircraft performance. Maximum pressurization was increased (to 6.5 psi differential) and changes to the cockpit layout. The Model 200C gave way to the Model B200C the same year, with the first Model B200T and Model B200CT being modified from a B200 and B200C respectively, the following year. The next major innovation occurred in 1984 with the B200, B200C and their derivatives being fitted with a revised landing gear retraction mechanism. This replaced the earlier electro-mechanical retraction system of gearboxes, driveshafts and chains and sprockets that was a throwback to the Twin Bonanza. The propellers fitted were changed from 3-bladed Hartzells to 3-bladed McCauleys.
Over the following years, various models were offered including the Model 1300, a 13-seat high density configuration with a belly cargo pod marketed as a commuter airliner. Also, from October 1995 Beechcraft offered an updated B200 with Electronic Flight Instrument System (EFIS) avionics and marketed it as the “B200SE Super King Air.” “Super” would be dropped from all marketing/advertising the following year. In October 2003, Beechcraft began fitting the B200 with the Rockwell Collins Pro Line 21 suite.
Hawker Beechcraft would announce the Model B200GT on May 21, 2007 during the 7th Annual European Business Aviation Convention & Exhibition. An updated version of the B200, the B200GT comes fitted with the PT6A-52 engine; developed to deliver maximum power to an even higher altitude than the -42 it replaced, further improving aircraft performance. Variants with the popular large cargo door option were designed and put into production after receiving Federal Aviation Administration certification on November 16th 2007.
King Air 200 Technical Data
Select a model
model 200
MFG Info
Type Cert # A24CE
In Operation 688
Years Made 74-83
SN's Eligible BB-2, BB-6 through BB-733, BB-735 through BB-792 BB-794 through BB 828, BB-830 through BB-873, BB892, BB-893, BB-895, BB-912, BB-991
Deminsions LxHxWS 43.8' X 15.0' X 54.7'
Cabin Dimensions LxHxW 16'8" X 4'8" X 4'8"
Fuel Capacity (lbs/gal) 3,645/544
Operating Costs
Engine Info
Performance


Quick Look: Beechcraft King Air 350
Quick Look: Beechcraft King Air 350
Fill ’er up!
October 5, 2014
Beechcraft’s largest iteration of the King Air family, the 350, was certified in 1989 and first appeared as a 1990 model. The 350—and the 300 before it—is certified under the FAA’s Part 23 Commuter category since both weigh more than 12,500 pounds. Because of that weight, the 300 and 350 are the only King Airs that require a type rating of its pilots. The Commuter category certification assures that the 350 has single-engine safety margins identical to those of a jet certified to Part 25 standards.
With a 300-knot cruise speed, the King Air 350 competes well against jets on trips shorter than 400 nautical miles, for example. In such a race, the 350 will arrive only about 15 minutes later than competitive jets while carrying a bigger load and using much less fuel. And unlike jets, the King Air and other turboprops are basically recession proof because of their proven efficiency. While many companies dump their jets when fuel prices spike, turboprops rise in value.
Another hallmark of the King Air 350 is its ability to haul big loads out of short runways when compared to a jet. This makes the 350 a valuable asset to a regional corporation or state government, for example. It shines on multi-leg short hops to medium-sized (4,000-foot runway) or larger airports. Because of its massive useful load and equally large fuel capacity, pilots often fuel the airplane in the morning and fly multiple legs throughout a day on a single load, which can be advantageous if you get a decent fuel price at your home base.
On longer trips, the King Air 350 can vault as high as FL350 where, at a long-range-cruise power setting, speeds are in the 230- to 240-KTAS range while burning a miserly 360 pounds (54 gals) per hour. In go-fast mode, the 350 can do 310 KTAS on 773 pounds (115 gals) per hour at FL240. Owners have a very wide speed/efficiency margin to work with in the 350, unlike the jets—which must fly high to achieve efficiency.
Unlike jets, however, the King Air 350 lacks fully integrated systems in its avionics suite. Systems dating back to the King Air’s 1964 roots cohabitate with modern avionics in the new 350i. It also lacks FADEC engine control like modern jets. There are many versions of 350 available: air ambulance, reconnaissance, freighter, and the new 350iER extended-range model. The 2009 Model 350i introduced factory installation of Raisbeck wing lockers to enhance the baggage-carrying volume. Older 350s have only a rear-cabin baggage compartment.
According to Vref, average values for the King Air 350 range from $1.5 million for a 1990 model to $7.5 million for a 2014 model.
While a turboprop never has the sex appeal of a jet, there’s no denying the impressive speed/efficiency flexibility found in the King Air 350. Add to that the no-compromises ability of the 350 to carry a huge load out of short runways, and it is a worthy competitor to jets.

Beech King Air 350: Just Load It Up and Go
Beech King Air 350
The Beech King Air 350 is for people who want to make their airplane budget in ink, not pencil. Its rugged design, more than 40 years of heritage and robust systems make the 350 one of the most dependable and predictable turbine airplanes around. The entire King Air fleet has logged an estimated 40 million flight hours since the first one was delivered in 1964, and more than 6,000 have been built.
That's why Spartan Chemical bought the 500th 350 built. This is the third 350 that Spartan, a maker of environmentally friendly specialty cleaning chemicals, has owned in sequence, and it uses the airplane to visit more than 500 distributors plus current and prospective customers from its headquarters near Toledo, Ohio.
And - I don't want to jinx the airplane and its crews - the 350 has not been involved in a reported accident in the United States since the first one entered service in 1990. The King Air fleet has posted one of the best safety records of any business airplane, but the 350 stands out as the best. The 350 is the biggest King Air with a cabin nearly three feet longer than the model 200. That provides room for a spacious dual club seating arrangement, plus a large and private lavatory in the rear. With full fuel tanks and a 200-pound pilot, 1,600 pounds of payload remains, so a full-sized person plus baggage can be carried in every seat. And 55.3 cubic feet of baggage can be stored in the aft compartment of the fuselage where it is heated and pressurized and accessible in flight. Long items such as skis or fishing poles fit nicely in the engine nacelle lockers. If you want to haul more people than baggage, two more seats can be put in the aft baggage compartment, and another person can sit on the belted potty seat.
The 350 is a rare airplane that can carry full fuel and full seats, and it can do it under extreme conditions. High air temperature robs all airplanes of takeoff performance, but the 350 has enough margin to safely take off at maximum weight at sea level on a 126º F day. Move up to Denver and it can still take off at maximum weight on a 90º F day. And if for some reason you need to fly a short hop, no problem, because the maximum landing weight is the same as max takeoff, 15,000 pounds. If you guessed the landing gear and airframe structure must be super strong, you'd be right.
The takeoff performance of the 350 is even more impressive when you consider that it is certified in the commuter category of FAR Part 23. That means pilots must have a type rating to fly it and must observe minimum runway requirements that assure a margin of safety if an engine fails during takeoff, just as the rules do in jets.
The required takeoff runway length in the 350 is the distance needed given weight, air temperature, wind and so on to accelerate to decision speed, have an engine fail, and stop on the remaining runway; or the distance needed to lose an engine after reaching decision speed and continue the takeoff to an altitude of 35 feet above the runway; or the distance needed to take off and climb to 35 feet above the runway with both engines running increased by 15 percent. In piston twins or other turboprops that are not certified in the commuter category - which is nearly all - there is no required runway and pilots can legally plan on a "two engine" takeoff with no margin built in.
On a standard day the 350 needs 3,330 feet of runway to take off, or under 5,000 feet at Denver. Even on that 90º F day in Denver the runway requirement is only 8,000 feet, and runways in that part of the country are routinely longer than that. And, remember, those numbers are for full fuel - enough to fly 1,500 nm or more with reserves - and a hefty body in every seat. For a mere 500 nm trip with a cabin full, runway lengths drop well under 3,000 feet on a standard day. It is a very versatile airplane.
The huge 355-cubic foot cabin is the 350's primary attraction, but until recently there wasn't enough cooling capacity to make the cabin comfortable on the ground and early in flight on very hot days. Beech solved that problem with a new environmental control system that increases cabin airflow by more than 250 percent. The system was developed by air conditioning experts at Keith Products and has now been incorporated into production airplanes. Included is an automated temperature control system that allows pilots to select the temperature for the cockpit and cabin individually. There are now seven outlets in the glareshield to cool pilots sitting in the hot sun, and the entire system weighs 35 pounds less than the manually controlled, less powerful system it replaces.
One of the best features of any King Air cabin is the big, round windows, and the 350 has seven of them on each side. The structure between the windows is so narrow I have the sensation of the whole cabin side being one big window. You can rotate a polarized inner window pane to reduce sun intensity. Several years ago Beech had problems with the polarization fading over time, but that seems to be resolved and every passenger can select their own level of light coming in the window.
Beech also has restyled the cabin chairs with recessed headrests, retractable armrests, and inboard and outboard tracking. The cabin overhead has indirect lighting that glows softly from a geometric pattern that surrounds cabin air outlets and reading lights. And cabin furniture has been upgraded with a large hot and cold beverage unit forward, plus pyramid-shaped cabinets between the seat backs. The entire cabin and exterior fit and finish, as well as materials, has returned to what most of us know as traditional Beech quality after a period where the company had failed to live up to its reputation.
Collins Pro Line 21 avionics, with dual flat-screen primary flight displays (PFD) and central multifunction display (MFD), are standard, along with the basic file server that allows the system to show weather and charts. The Pro Line 21 system includes a single flight management system (FMS) that can be used for all navigation, including the new GPS approaches with vertical guidance. You can dial com and nav frequencies using the FMS keyboard or the knobs on the single radio management unit in the panel. And I'm pleased to report that the automatic flight control mode selection panel is located on the glareshield instead of down in the pedestal where it resided out of sight for many years.
The 350's systems, as they must be to meet commuter category rules, have a high level of redundancy. The main electrical bus is fed by both generators and the battery, and this triple-fed bus can support essential equipment from any of the three sources, which are in turn isolated from each other. Nonessential loads are automatically shed if generators are lost. The fuel transfer system from tank to tank and to the engines is automatic with no pilot intervention required. And an all-electronic standby display in the middle of the panel shows attitude, heading, airspeed, altitude and nav guidance independently of the primary air data computers or attitude-heading reference systems.
With its up-to-date flat glass panel, but its traditional toggle switches and big throttles and propeller control levers, the 350 is an interesting mix of the old and new. In most respects, I generally forget that the airplane is a turboprop and not a jet, because the avionics and size of the airplane are so like a jet. And I think passengers don't think much about the propellers, either - except on the ground.
The 350 has automatic propeller feathering and rudder boost to immediately feather the prop if an engine fails on takeoff and to step on the proper rudder to overcome the asymmetric thrust. An engine failure in the 350 is virtually identical to the loss of an engine in a jet because the autofeather immediately eliminates the drag of the windmilling propeller on the failed engine. As you can imagine, autofeather and rudder boost are required items, and that means they need to be tested once each day. The test requires a ground run-up to high power to check each system, and that's when passengers are reminded the 350 is not a jet. Pilots who want to give their passengers the best possible experience will do the high power run-up before loading the people on the first flight of the day.
The airplane flown for this report was the 500th King Air 350 delivered by Beech. The standard 350 is very complete with only a few optional avionics and cabin furnishings. Warranty on the airframe and avionics is five years, with five years or 2,500 hours coverage on the engines, and a two year warranty on systems and components. Raytheon's "Support Plus" maintenance service plan can lock in all hourly maintenance and repair costs. All data here is from the airplane manuals and reflects standard day conditions at sea level unless noted.
The engines are mounted further outboard on the 350 than on other King Airs, and the propellers are further forward, moving their tip noise away from the cabin. The leading edge of the wing root between the nacelles and fuselage is extended forward and drooped to give the 350 more lift and good stall behavior. The huge wing has a span of just under 58 feet, and its structure is certified for infinite life, a demanding standard in the commuter category. The winglets appear to help in all phases of flight, but probably add the most at high-altitude climb and cruise. The 350 is certified to 35,000 feet and will get there at most weights and air temperatures, and that is the level where it delivers the lowest fuel burn and longest range, but cabin altitude is around 10,000 feet, so most pilots fly lower unless a very long trip or a strong tailwind lures them to the certified ceiling.
With nearly full fuel and two of us onboard, we weighed 12,600 pounds for takeoff at Beech Field in Wichita. The V1 decision speed was 97 knots, with rotation at 104 knots, and V2 engine-out climb speed at 111 knots. Those speeds are for a flaps-up takeoff. As in most airplanes, using flaps reduces takeoff speeds a few knots and shortens runway roll in the 350, but also reduces engine-out climb performance, so it's a trade-off. With plenty of runway and climb reserve, I like the flaps-up takeoff better. I think it makes for a smoother rotation and initial climb, but the choice is up to each pilot.
Initial climb rate topped 2,000 fpm, and in 15 minutes the 350 was level at 27,000 feet, despite air temperatures at least 9º F above standard all the way up. The high 20s are good altitudes for the 350 because it cruises right around 300 knots true airspeed with a fuel flow of about 650 pounds per hour. The mid-to-high 20s are not crowded altitudes, and the tanks' full range at maximum power is at least 1,000 nm with enough reserves to continue to an alternate 100 nm from the destination.
Except for takeoff, all climb and cruise is conducted with the propellers set at a slow 1500 rpm. At that setting you are aware of the props in the cockpit, but in the aft club chairs the sound could be as easily coming from a jet engine as a turboprop. And the vibration level compares very favorably with a business jet.
For several years Beech had included an active noise attenuating system to quiet the cabin. As in headsets with active noise reduction, a network of microphones detects ambient noise, and then speakers deliver an opposing sound that is 180 degrees out of phase with the unwanted noise. The clash of the two sound waves cancels most of the noise. The active system works well, but proved to be a maintenance issue. There were some failures of the electronic equipment, but more often an adjustment of microphone position or other tweaking was required to make the system work properly. So, Beech has now replaced the active electronic system with a passive noise reduction system that uses 83 "tuning fork" sound absorbers and insulation sealed in plastic bags. The tuning forks are bolted firmly to the airframe structure, and their vibrations, tuned to the propeller frequency, absorb sound energy and help stop it from being transmitted via the metal airframe. There is zero maintenance to the system, and no electrical power is required, but it does add 30 pounds to the empty weight compared to the electronic system. The flying qualities of the 350 are as predictable and dependable as the rest of the airplane. The wind was gusting to 30 knots when I flew the airplane last December, and as you can imagine, it was bumpy down low. The control forces on the 350 are heavy, but the harmony of forces between ailerons, elevator and rudder is excellent. But most importantly, there is lots of power in those control surfaces. It takes muscle to move the controls, but the 350 responds with precision and smoothness, and despite the gusts, my landings were darn good.
Many people wonder how long the King Airs can go on given the host of business jets on the market and in development, but I don't doubt their future because other airplanes can't do what the 350 does in terms of payload, speed, range and runway requirements. Given the continual improvements Beech makes to the airplane, and the welcome return of the company's famous top level of quality, a lot more than 500 King Air 350s will be loading up and taking off in the years to come.
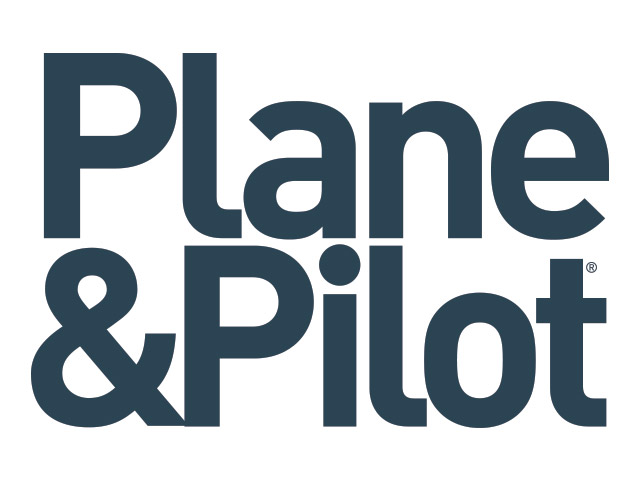
Second-Generation Pilatus PC-12
Second-Generation Pilatus PC-12
Pilatus takes another look at its PC-12 and makes a good airplane even better
Bill Cox, Photography By James Lawrence
AddThis Sharing Buttons
Share to Google BookmarkShare to FacebookShare to TwitterShare to Facebook MessengerShare to More9
One of the realities of delivering corporate airplanes for part of your living is that you don’t get every job you bid. For a variety of reasons (many of which have nothing to do with price), you’re lucky to be awarded one out of 20. Some jobs just go away because the planned delivery never happens. Others get assigned to someone’s brother-in-law who used to fly fighters in Korea, and still others wind up flown by a factory pilot. I probably realize less than 5% of my bids because I’m becoming pickier (i.e., more expensive) in my bidding after 30 years. The older I get, the better I used to be.
One trip I sincerely regret missing out on entailed taking a new Pilatus PC-12 from Connecticut to Ulan Bator—yes, I had to look it up. Turns out it’s the capitol of Mongolia, and the trip was supposed to take place in the early summer of 2001. It was planned for a far northern, semi-great-circle route, about 6,000 nm, with refueling stops in Churchill, Manitoba, Canada; Fairbanks and Nome, Alaska; Petropavlovsk, Kamchatka, Russia; and probably someplace else with a name I can’t spell. For a combination of reasons, the ferry flight never happened. Spilt milk, I guess. Trips such as that don’t come along very often.
With a max payload of 2,866 pounds, the
PC-12 NG can carry up to nine passengers or fill the huge cargo area, accessible via a forklift-loadable door in back.
So here I am in Broomfield, Colo., seven years later, snug in the left seat of the newest PC-12 NG with Peter Duncan, chief pilot for Pilatus Business Aircraft Ltd., North America, riding shotgun to protect me from evil. In truth, there really isn’t any evil associated with this airplane. It’s comfortable, totally without artifice or deception, friendly in every mode and an easy machine to transition into. It’s about as close as you can come to a giant panda with wings. Pilatus Manager Mike Haenggi and Pilot Journal photographer Jim Lawrence luxuriate in the back in a vain attempt to bring gross weight closer to some representative number.
Though this is a finished airplane, most of the PC-12s in residence in Broomfield aren’t. The planes are flown in “green” from Stans, Switzerland, sans paint and interior; they’re then configured to customer demands in Colorado.
Before our flight, Duncan and I walked around the airplane, discussing the old and the new of Pilatus’ corporate turbine single. There was plenty to discuss. The new PC-12 is a much improved version of the airplane I flew for this magazine’s premier issue in 1999. That model was a capable load hauler, but the new version is better in a variety of ways, and only one of those improvements is the new, all-glass Honeywell Primus Apex avionics.
Still, Apex is perhaps the most impressive aspect of the new airplane. Pilatus looked at a variety of options before choosing a glass panel for the PC-12, and the Apex is indeed talented, playing through four 10.4-inch displays. This is more typical of a midsized jet system than a turboprop single.
Describing an avionics operating system in print is a little like trying to learn brail by reading about it, but the Apex is about as intuitive as they come. This is avionics by computer, and if you have a semblance of computer smarts, you’re bound to catch on quickly. Electronic charts, XM Weather, synthetic vision and the gamut of readouts make the Apex multi-capable. Entries are through a keypad and transferred to the specific box. If you have even modest facility with the Garmin G1000 system, Apex won’t present any special challenge.
Considering the limitations inherent in FAA-certification requirements, the changes labeled “Next Generation” on the 2009 PC-12 represent a veritable thunderclap of innovation. Pilatus apparently listened to its customers and made enough improvements to make the PC-12 NG a different airplane in essentially the same skin.
Typical of so many Swiss products, the PC-12 is beautifully constructed, exquisitely appointed and heroically designed. If you have any engineering experience, you can’t help but shake your head in wonder at the airplane’s remarkably intelligent systems design.
Updates start with the new Pratt & Whitney Canada turbine engine. It represents a significant improvement on the same basic design. The new PT6A-67P enjoys the same power, 1,200 shp, but it’s now continuous rather than limited to five minutes. That’s because the new mill features higher heat tolerances, owing to better compressor and turbine-blade design.
Max cruise power is still 1,200 shp, and the engine maintains it to a higher altitude, resulting in better cruise numbers. At just under 10,500 pounds max ramp weight, the PC-12 is far from overpowered. Rather, the match of horsepower to airframe seems about right.
If you compare the old PC-12 with the new, you’ll notice the winglets are notably different. Pilatus optimized the tips, switching from the first-generation, tall, vertical winglets of old to the newer, shorter, angled, blended shapes that integrate nicely with the radar dish out on the right wingtip.
Inside the cabin, the new interior is the result of a collaboration between Pilatus and BMW DesignworksUSA. As you might expect in a $4 million airplane, the interior is about as luxurious and comfortable as it’s possible to make. There’s plenty of room for passengers to unwind in back. The cabin is five feet wide, broader than in some medium jets, and you can choose from a variety of wood veneers, fine leathers and audio/video options to suit any taste.
Flying from Rocky Mountain Metropolitan Airport on a warm afternoon, density altitude was probably at least 8,000 feet, yet the PC-12 settled easily into an 1,800 fpm climb at 140 knots. ATC stepped us up to altitude so we couldn’t time a continuous climb, but the book boasts of 30,000-foot climbs in 26.5 minutes in ISA conditions, and I believe it. (All PC-12s are RVSM ready, by the way, though few pilots operate above FL280.)
Max cruise numbers sometimes mean more to piston pilots than to turboprop and jet aviators, primarily because the fuel burn can be disproportionately cheaper on turbine engines at lower power, and the difference in cruise numbers may not be that significant. Level at FL270 with everyone breathing 8,500-foot air (max pressurization differential on the PC-12 NG is 5.75 psi), we saw 275 knots, about five knots better than book, meanwhile burning 375 pph. That’s slightly faster than book speed on less than book fuel burn, a combination that’s hard to beat.
One of the new PC-12’s main assets is its state-of-the-art, four-screen Honeywell Primus Apex avionics panel. The two PFDs and two MFDs integrate flight information, engine monitoring, aircraft configuration, pressurization and environmental controls. Flight and weather data, charts, aircraft system information and trip-planning functions are also incorporated into the system.
The PC-12’s POH suggests the airplane will manage to touch 280 knots at 20,000 feet while guzzling 491 pph. With 2,704 pounds of fuel aboard, that means you’ll be looking for a place to land within about four hours on an IFR mission. At 28,000 feet, the airplane’s range is nearly 1,500 nm at 260 knots.
Range/payload is where the PC-12 truly shines. This is a long-range airplane by any definition, with or without a big cabin payload. When I was considering the solo flight to Mongolia, it was encouraging to know the 402-gallon fuel capacity was more than adequate for the long legs involved.
If you’re willing to settle for 218 knots at the 30,000-foot service ceiling, you can enjoy a burn of only 279 pph. Your endurance at FL300 is nearly eight hours plus reserves, worth almost 1,700 nm between pit stops. That’s a 22% reduction in cruise speed in exchange for a 43% improvement in fuel burn. That should make sense to any executive with an eye on the bottom line.
All the same, time is money in this airplane, and many PC-12 pilots think nothing of loading up with six to nine passengers and then choosing a setting halfway between the two extremes above; they’ll still enjoy block speeds of 230 to 240 knots in exchange for perhaps 350 pph. In piston speak, that’s 52 gph, about 4.5 nmpg, but you could be transporting the entire first-string Los Angeles Dodgers plus a batboy in the bargain. It’s true the PC-12 isn’t exactly “bonkers fast” like the TBM 850 (310 knots cruise) or Epic Dynasty (330 knots cruise), but those are pure six-seaters. What you sacrifice in pure speed, you more than make up for in payload.
Whatever the weight, the PC-12 handles it better than ever before. That’s because Pilatus has made a major improvement in roll response. When I flew the original airplane a decade ago, I felt that aileron effectiveness was somewhere between heavy and ponderous. It’s true the Pilatus is a large machine that doesn’t lend itself to light controls, but the current PC-12 handles far better than the original, with anti-servo tabs on the ailerons providing significantly lighter roll forces and what at least feels like a quicker rate. There’s certainly no question you’re directing more than five tons of airplane around the sky, but the PC-12 NG nevertheless maneuvers with panache.
That becomes especially significant when it’s time to return to earth. As with most turbines, the trick is to stay as high as possible for as long as possible, then descend with dispatch. That often means with the thrust lever at the backstop and nose pointed downhill at 1,500 fpm. The PC-12 doesn’t employ speed brakes, because it doesn’t need them. Simply reduce thrust to idle, and the big single will descend like a falling Baldwin. Planning pattern entry or joining an ILS is no tougher than programming a Mirage or P210 for landing. Prop rpm remains 1,700 for the entire flight, and you need merely adjust the thrust to home in on the proper power setting.
If patterns are relatively idiotproof, landing characteristics are even more benign. Vso at max takeoff weight is a low 66 knots, and that means you can trundle down a VFR final at 80 knots without violating the 1.2 Vso rule. Veteran PC-12 pilots like Duncan report that 100-knot approaches work perfectly in the clag. The flare is easily predictable, and you can plant it on the mains and stop in a hurry, with or without help from beta.
Pilatus worked with BMW DesignworksUSA to equip the PC-12 NG with an ultraluxurious cabin.
The trailing-beam gear is famous for cushioning the most ham-handed efforts, and even without finesse, the airplane will grind to a stop in less than 2,000 horizontal feet. If you do use beta, it’s considered poor form to maintain it below about 40 knots. Above that speed, there’s almost no possibility of ingesting any FOD material, even on a rough gravel strip.
The day after our evaluation flight, it was time for the air-to-air photo session, and mine was the cushy job, especially in view of the PC-12’s improved aileron response. We flew to Leadville, the highest municipal airport in America. Leadville is 10,000 feet closer to the sky than the sea, technically perched 9,927 feet tall in the Colorado Rockies. Our photo ship was a defenseless Skylane RG, 30 feet ahead at two o’clock, with our photographer pointing his Canon in my direction as we gradually lofted above the big rocks. The long, hot climb wasn’t a problem for Duncan and me with 1,200 hp out front, and pressurization, air-conditioning and peeled grapes in the back. Fortunately, I only write the stories these days. I no longer have to shoot them as well.
The PC-12 NG is targeted at companies or individuals who need a choice of lots of seats, seats and cargo, or a huge cargo area (along with a forklift-loadable door in back), 270-plus-knot speeds and the reliability of Pratt & Whitney’s near-legendary turbine engine. So far, some 200 folks have anted up for the newest PC-12, roughly $800 million worth of airplanes.
It’s true there’s only one turbine out front, but in the case of the PC-12 NG, that’s all you need.

Pilatus PC-12 Versus the World
Pilatus PC-12 Versus the World
We fly the PC-12 NG on a cross-country outdoors adventure and learn firsthand why everybody wants a piece of Pilatus.
By Robert Goyer June 25, 2013
Pilatus PC-12 NG Feature
** Photography by John Dibbs**
"This is what flying is all about," I thought to myself as we sped along the surface of the Willamette River, the beyond-crisp western Oregon air rushing past. Our trusty fishing guide extraordinaire, Chad Wiest, from On the Line Guide Service, directed our boat by intuition, through the near darkness to a spot that promised to contain the treasure we were seeking: spring Chinook salmon. Our chariot to this spot was the Pilatus PC-12 NG, and back at the cozy little GA airport in nearby Scappoose, the big single was stuffed to its gills with gear for this ultimate long weekend. We had packed bikes, coolers (in optimistic anticipation of our legal take of Chinook), golf clubs and, thanks to an afternoon sortie the day before, several cases of Willamette Valley wine.
It had already been a good trip. Twenty minutes later, it started to get a lot better, as first I landed a 20-pound hatchery Chinook (a keeper), and then my buddies Aaron and Jed followed suit, each taking a big (though not quite as big, I reminded them) salmon over the next few hours.
Yes, the Pilatus PC-12 NG was our ride for this excursion, and it'd be hard to imagine a better one. Coming out of Colorado a few days before, we crested the Rockies, went nonstop to Seattle, then cavorted around the San Juan Islands, collecting photographs and memories along the way. It really was what flying is all about. Magic carpet stuff.
Swiss Niche
The question "What airplane would you buy if you won the lottery?" seems as though it would have a lot of different answers, depending on what pilot you asked. The truth is, the most common answer by far, at least in my experience, is "a PC-12 NG." It shouldn't be surprising that more than a few pilots would want to buy one with their winnings. A lot of pilots with the means to buy one do just that. It is a remarkably versatile airplane. But the fact that so many pilots looking for very different kinds of lift — a rugged toy hauler, a sleek and spacious business transportation machine or a fanciful portal for adventure — would all pick the same airplane says something about the Pilatus PC-12 NG. It's about as perfect a compromise as one could imagine.
The Pilatus PC-12 NG is not a one-of-a-kind airplane. There are a few other pressurized singles: the Piper piston-powered Mirage and turboprop Meridian, and the quick and pretty Daher-Socata TBM 850, as well as a few emerging models. There are other rugged turboprop singles, including the seminal Cessna Grand Caravan and the slightly smaller Quest Kodiak. And there are other nine-passenger near-midsize cabin transportation airplanes, including the Citation CJ2 or CJ4, the Beechcraft King Air and the Embraer Phenom 300. There are other would-be competitors, all of which do one or two things better than the PC-12 NG. The Phenom is faster, by a lot, the TBM 850 is also substantially faster, the Caravan is less expensive to operate, the Meridian costs about half the price, and the King Air has that extra engine.
But when all is said and done, it's tough for any of the PC-12 NG's competitors to measure up across the board, or to even come close. Let me summarize its remarkable features. The PC-12 NG is rugged enough to set down on a short gravel strip at high altitude, it's pressurized for hopping weather and keeping passengers comfy, it's fast enough to make it a great regional flyer, it's got great range for when the mission stretches out, and it boasts a reconfigurable cabin roomy enough to let you play FedEx with a large load or pile in the passengers and their gear for a long weekend in the woods. The big side-loading door aids in loading gear, up to dirt bikes. And when you head to the front of the airplane, you'll discover a cockpit that rivals those of many high-end bizjets. What other airplane matches this description? That's right, no other airplane does, and Pilatus and its would-be competition know it.
Now, this is not to say that there are no competitors of the PC-12 NG. There are, and great ones too. They generally offer something that the PC-12 NG lacks, most typically high cruise speeds. But in every case, you're giving up something when you choose not to go with the PC-12 NG.
In a world where compromise is built into the game, the PC-12 NG represents a product that is very cleverly conceived and very delicately positioned. It occupies its own niche and, in so doing, has, ironically, created a universe of competitors in neighboring niches below and above.
Describing the Beast
Launched around 20 years ago now, the PC-12 NG has sold consistently well for longtime Swiss airplane maker Pilatus (named after a mountain near the factory, in Stans, Switzerland). The project was far from a slam-dunk. The concept of a single-engine pressurized turboprop might sound like a natural today, but that's only because the PC-12, along with the TBM 700 (now 850), proved the concept. The concern with a big and fast single is, of course, what to do if that one engine fails. The advantage of a turboprop engine, compared with a piston, is that not only is it more powerful — a lot more powerful — but it's also a lot more reliable. Engine loss, in Pilatus' view, was an acceptably small risk. That is the argument today, and it was the argument a couple of decades ago, when Pilatus launched the bird. At the time a certain percentage of people bought it and sometimes, consequently, bought a PC-12 as well. Today, the concept of a turboprop single is a no-brainer. A friend who's been selling PC-12s since the model's inception told me that in the early days the single-engine safety discussion was a big part of the sales process, whereas now it hardly comes up.
Today's model is the PC-12 NG, "NG" standing for "next generation." The sweeping enhancements associated with the NG change came in 2008, though some of the upgrades were worked in slightly earlier and others have kept coming. Keeping straight what improvements came when requires an advanced degree in PC-12 history from the University of Stans, but ultimately today's PC-12 NG has a higher gross weight than the original model as well as aerodynamic improvements, including mid-winglets, that make it a faster, better-performing airplane than before. There's better lighting, a more durable and more comfortable interior, and more power than ever. In all, the PC-12 NG represents a huge improvement to an already remarkable airplane.
Chief among the improvements is the update to the Pratt & Whitney PT6-67P, which upped the horsepower from 1,000 to 1,200 shp for takeoff and climb and also improved the engine's thermodynamic rating. This means you can run it hotter, which means you can ask for more power under both higher and warmer conditions. Pilots will see shorter takeoff runs and better climb performance, areas in which the PC-12 already excelled. The increase in power also means better cruise speeds, around 10 to 15 knots better versus legacy airplanes, making the PC-12 NG's speed, if not competitive in terms of cruise, then at least less of a disadvantage.
The PC-12 NG is a big airplane; people who see it for the first time on the ramp are often taken by that fact. It's nearly the size of a C90 King Air, but because it's a single-engine airplane, it somehow seems outsized. It's also a no-nonsense-looking airplane, which you'd expect from the Swiss. It's made of metal (as is the newly launched PC-24 bizjet), made very ruggedly and made to last. It's got big, beefy gear for landing in the rough, oversize wing spars, and a reconfigurable cabin for swapping from executive transport to cargo or big toys.
One of the biggest surprises for me when I first flew the PC-12 NG years ago is that it is in every respect a serious turbine-class product with exactly the same kinds of systems and the same kinds of hardware you'd see in a King Air or, for that matter, a Citation. And, when you think about it, why not? The PC-12 NG has every system, except those related to a twin instead of a single, as those other airplanes do. The PC-12 NG is a single-pilot airplane (most King Airs and many Citations are as well), so it's laid out to accommodate that, with controls and switches arranged to keep them within reach. At the same time, flying the PC-12 NG is not like flying a high-performance single. There are systems to be learned, from pressurization to turbine management, there's a nicely implemented crew alerting system (CAS), emergency oxygen and emergency gear extension, among many others. The FAA doesn't require a type rating for the PC-12 NG, as it's neither a turbojet (a seemingly arbitrary distinction these days) nor a 12,500-pound airplane. Training in an airplane such as this is critical though. Luckily, the insurance companies have stepped in to mandate regular recurrent training for their customers who fly PC-12 NGs (as well as other similarly complex airplanes commonly flown by owner-pilots).
Apex Excels
One of the least well-understood facets of the PC-12 NG is the new-with-the-NG avionics system from Honeywell, known as Apex. Today's Apex, Build 8, is better than ever, and it was remarkably good to begin with.
For those of you not familiar with Apex, the system is based on Honeywell's Primus Epic, just like the EASy flight deck in the Falcon. For a time, Honeywell seemed happy to let people think that Apex was a stand-alone light-GA product, not closely related to its world-class big bizjet Epic system despite the fact that the lineage is obvious to those who have flown both. This is not to mention the impossibility of developing such a remarkably complex and capable system for a small market; the PC-12 NG is by far the most noteworthy airplane to date with Apex in it.
Since the last time I flew the airplane, a couple of years back, Apex has gotten even better. The main improvements are the addition of synthetic vision — which, in my opinion, Honeywell does better than anyone — and the greatly improved integration of charts, now geo-referenced, and weather data into the system. There's also the adoption of the excellent L-3 Trilogy all-in-one standby instrument, along with dual FMSes.
Flying Apex is a very air-transport kind of experience. The fit of the displays — indeed, of the entire cockpit layout — is clean and sharp, a perfect complement to the PC-12 NG's style. Every display can be windowed, in essence giving you a dozen or more customizable mini displays. Depending on your phase of flight, you can have an approach chart showing on one display, systems information (perhaps a fuel system page) in a window on another, and flight-plan information on another. Pilots can set up the system not only to their liking, but also to best fit their current needs.
While the system feels very different from Garmin's popular G1000 suite, common in aircraft of this class, once you get the hang of using it — which does take a bit of time — the capability is nothing short of remarkable. Pilatus here benefits from a decade of work by Honeywell and its partners in creating Epic. It's a big-airplane feel in a turboprop single, but pilots will be delighted with Apex.
Muscle and Beauty
That night, my three fishing buddies and I met up again at a dive along Route 30 to have a few beers and swap lies. In the process, we engaged in some flight planning. We'd head out of Scappoose the next a.m. At that point we'd top the tanks on the 12 with jet-A and ride the prevailing westerlies nonstop to Austin, a five-plus-hour, 1,500 nm trip we'd likely fly at 270 at best true.
The Oregon morning dawned wide and blue. After rousting ourselves we headed for bacon and eggs at the local eatery named, so far as we could figure, "Restaurant," and then made a quick stop at Dutch Brothers for coffee and more coffee and headed to the airport.
With all of the gear and full fuel, we were at just under 10,000 pounds for takeoff from Scappoose. Good thing we had not caught more fish.
Flying the PC-12, as opposed to learning how to manage the systems, was not a particularly challenging transition for me when I was first introduced to the airplane nearly a decade ago, and I felt comfortable in the big Boeing-style pilot's seat in the 12 as we started up and taxied out from Scappoose (a great grass-roots GA airport, I'd like to add).
Apex (along with Jed, who is possibly the highest-time PC-12 NG pilot on the planet) guided me through the bizjet-style preflight checks. Starting the PT6 is an easy affair, or maybe I'm just getting used to flying turbines, a thought that makes me smile. Taxiing out, I remembered how remarkably maneuverable the PC-12 NG is, though it's important to remember how big a wingspan — 53.3 feet — it has.
At the departure end, I advanced the power lever and felt the airplane accelerate quickly. The PC-12 NG more levitates than rotates as it reaches flying speed. We were climbing strongly through the cool air despite our heavy weight and quickly got cleared by the controllers right through what would have been our intermediate altitudes as we headed directly up to FL 270. It took us 24 minutes to get there.
Fuel management is one of my favorite parts of flying the PC-12 NG, because there is essentially none required. The tanks are self-balancing. If one tank gets a bit heavy, the system automatically sends from it until things are once again in harmony.
At FL 270 we were initially seeing 265 knots while burning just under 400 pounds per hour. The airplane we were flying, the factory demonstrator, was not yet RVSM certified, so we weren't able to head up to 290, but Jed told me that he typically sees a savings of around 50 pounds per hour at that altitude with a slight reduction in cruise speed.
The trip back to Austin was a pleasure. We experienced headwinds of 100-plus knots going out of Denver to Seattle earlier in the week, whereas on this flight, our tailwind did the trick, averaging 20 to 40 knots.
After crossing the Rockies and gazing down at the Wasatch Front before Salt Lake below, we continued our cruise to Austin. As usual, we got slam-dunked on the arrival, to the point where our cabin rate of descent was a whopping 650 fpm compared with our over 2,000 fpm actual rate of descent — just one more reason to love pressurized airplanes.
My last landing of the trip back in Austin was anticlimactic and telling. We kept our speed way up on the way in to keep the controllers happy. Speed control in this airplane is an absolute piece of cake. Pick your speed and make it happen using a combination of speed brakes, power reductions and gear. We landed long ("long" being a relative descriptor when it comes to the PC-12 NG) and made the reverse high-speed turnoff. Back on the ramp, we divvied up the salmon. Man, was it good eating. Not as good as the fishing or the flying, but still pretty darned good.

We Fly: Pilatus PC-12 NG
We Fly: Pilatus PC-12 NG
We test the legendary Swiss turboprop in its element at a secret landing site — no runway required.
I’m sitting on a remote dry lake bed in Utah, having a fabulous catered lunch consisting of a variety of scrumptious fresh berries, sandwiches and cookies. It’s as far from the hustle and bustle as you can get.
The faintest wind gust is audible, and each step I take on the fine-grained sediment creates a crunching sound. As I look up from the spread on the large picnic table, a wall of tan desert dust approaches. I cover my food and duck down under the table to shield myself from the sudden onslaught. Thirty seconds later the gust has subsided, the crystal-clear blue skies above reappear and the calm and quiet resumes. Only in the desert can you get a surprise like that, I think.
How did I get here? And where did all the fresh food come from? I arrived in one of the most versatile aircraft in the world — the Pilatus PC-12 NG — a large single-engine turboprop. Whether the plan is to travel quickly from point A to B, fly in executive comfort, carry massive amounts of cargo or land on a short dirt strip to get away from the masses, the PC-12 will do it all and do it well.
Nestled in the Swiss Alps, Pilatus has its headquarters at the Buochs Airport in Stans, where it opened its doors in 1939. The name of the company comes from Mount Pilatus, a mountain with several peaks as high as almost 7,000 feet, towering over the quaint town. The mountain’s name originates from Pontius Pilate, whose body, legend claims, was disposed of in a lake on the mountain. Legend also has it that the intense storms that occasionally rise from the mountain stem from Pilate’s restless ghost rising from the lake to wash the blood of Christ from his hands.
By far the most noticeable upgrade in the latest iteration of the Pilatus PC-12 NG is the five-blade Hartzell composite propeller, which gives a boost to the already impressive performance of the Swiss turboprop.
Pilatus Aircraft Ltd
Pilatus’ airplanes emulate the strength, power and beauty of the Alps. The company started out building the SB-2 Pelican, designed specifically for mountain flying, with terrific short field and climb performance capabilities. An immensely successful mountain-flying and STOL performer came along in 1959 when Pilatus introduced the PC-6 Porter. The company has also seen much success with military training platforms.
Pilatus is privately owned, and the leadership has made smart development decisions in its nearly 80-year history. As a result, the company has no debt and has never had to lay off any employees, says Thomas Bosshard, president and CEO of Pilatus Business Aircraft — a U.S. subsidiary based in Broomfield, Colorado. The most successful airplane the company has produced to date is the PC-12, but the recently introduced PC-24 twinjet may give it a run for its money.
The PC-12 was first introduced in 1994, when it received certification from both the Swiss Federal Office of Civil Aviation and the FAA. PC-12s are born in Stans, where the airframes are assembled and painted white, and avionics are installed along with basic insulation and the flat floor that contributes to the PC-12’s versatility.
The naked airplanes then get a tour of Iceland, Greenland and Canada before landing in Broomfield to be outfitted per the customers’ specifications. With the success of the PC-12 in the United States and the upcoming certification of the PC-24 “super versatile jet,” which is expected to enter the market at the end of this year, the Broomfield facility is being expanded. A modern 118,000-square-foot completion center is being built on the west side of the runway, opposite the current headquarters, which are spread over 14 hangars and multiple offices in the Rocky Mountain Metropolitan Airport terminal.
The flashy Ferrari-inspired paint scheme on the PC-12 NG demonstrator blended well with the desert landscape.
Pilatus Aircraft Ltd
Pilatus Business Aircraft’s chief pilot Jed Johnson, vice president of marketing Tom Aniello and photographer Mitch Bowers picked me up at Camarillo Airport in Southern California to allow me to experience firsthand what the sleek yet sizable turboprop is all about. An older PC-12 happened to be parked next to us, making it easy to see the improvements made with the latest version, the PC-12 NG.
Since the PC-12 first rolled off the production line, it has gone through a continuous evolution. The company has played around with different sized winglets, the first of which were aptly named “biglets.” Today’s PC-12 has much subtler winglets — just a slight upward bend of the wingtips.
The original PC-12 was powered by a Pratt & Whitney PT6A-67B, which was rated at 1,520 shp reduced to 1,200 shp for takeoff and 1,000 shp for cruise. While the takeoff and climb power ratings have remained the same, the -67P that powers the PC-12 NG has 1,840 shp, allowing the airplane to produce maximum power at higher altitudes. The engine is not fadec-equipped, but has a torque limiter that helps prevent damage at full power. However, the pilot is responsible for monitoring the gauges. Beta range helps with short landing distance — as short as 2,170 feet over a 50-foot obstacle — and can provide up to 900 shp in reverse.
The turboprop engine of the PC-12 NG is wrapped in a sleek composite cowling for good aerodynamics, and mounted at the front of a pressurized aluminum fuselage with retractable landing gear. The airframe’s fatigue life is based on 20,000 hours, or 50,000 hours through Pilatus’ Life Extension Program.
The electrically actuated trailing link landing gear smooths landings on unimproved surfaces.
Pilatus Aircraft Ltd
For this latest PC-12 NG model the Pilatus engineers switched out the hydraulically actuated gear for a simpler, quieter, lower-maintenance electrical system, and made several aerodynamic modifications to allow the airplane to add a few additional knots to its cruise speed. The aileron hinges were covered to reduce drag, the antennae were aligned under the belly, fairings were improved and the scoop under the engine cowl was modified. LED lights were installed throughout to make the airplane more visible and to provide improved lighting inside the cabin.
One of the most impressive and noticeable recent mods is the addition of the five-blade Hartzell composite propeller. Its scimitar blades make the turboprop more efficient, improving the time to climb by about 10 percent. During our flight, we were climbing at 1,300 fpm at 13,000 feet, and through FL 250 the Pilatus was still cranking out 850 fpm. The new prop also emits less noise, which was evident inside the airplane, where we could have carried on a conversation without headsets while seated right behind the big PT6A. With the cabin being even farther away from the fire-breathing monster, passengers do not need to use a headset.
The leading edge of the composite prop is covered with nickel, and it has a stainless-steel mesh for extra protection. The construction is strong and durable enough that the propeller blades have no life limit. However, the propeller system has a 4,000-hour or six-year time between overhaul, whichever comes first. When metal propellers are overhauled, the leading edge sometimes gets shaved down to eliminate rough spots, a process that reduces the performance over time. But Hartzell’s propeller never changes shape and therefore provides full performance over its life span.
With all the recent mods, the PC-12 NG gained 5 knots all in all, topping out at 285 ktas. While 45 knots slower than the Daher TBM 930, that’s a respectable speed considering its carrying capacity. However, Pilatus customers have asked for a faster PC-12. The answer was the PC-24, which will cruise at 425 ktas while maintaining the DNA of the PC-12: short, unimproved runway capabilities; an oversize cargo door; a wide CG range; and a large, comfortable cabin. However, the turboprop will win big over the twinjet when considering operating costs.
The PFD on Honeywell's Primus Apex suite uses an intuitive flight path symbol and, while not displayed, supports Honeywell's SmartView synthetic vision. For the complete breakdown of the Apex displays, check out the August issue.
Pilatus Aircraft Ltd
Stepping into the PC-12 NG through the forward airstair door, which eliminates the need for the pilot to walk through the cabin, I was immediately lured into the cockpit, with its Honeywell Primus Apex displays. Two PFD screens — one for each cockpit seat — and two MFDs mounted on top of each other in the center of the panel make up the integrated avionics suite. Beneath the MFDs is a keypad and, behind the power lever, a cursor control device from which the pilot can manipulate the system. Many functions can also be selected through soft keys on the sides of the screens.
I found the Apex system to be a highly capable avionics suite, and while the logic is completely different from any systems I had played with before, it didn’t take long to figure out. The menus are easy to use, and only a few clicks with the cursor control unit are required to make modifications or select an approach. One part I loved in particular was the flight-path marker on the PFD (most commonly used in military airplanes), which makes it easier to keep on track than the single-cue or dual-cue flight directors used in most civilian business aircraft. Wireless updates make the system management easier as well. My only beef with the Apex is that the data processing speed could use a boost.
The seats in the cockpit allow for multiple adjustments, and I easily positioned myself comfortably, high enough for good visibility over the nose. Johnson, who is 6 feet 4 inches tall, does not use the lowest setting on the seat, and he had ample headroom on the copilot’s side. The cockpit is a full 5 feet wide, so there was no need to rub elbows. Design features that make the pilot and copilot extra comfortable include two cup holders on each side and a side pocket for an iPad, notepad, phone, glasses and more.
The massive cargo door makes it easy to load oversize items into the aft cabin and cargo compartment.
Pilatus Aircraft Ltd
Aniello and Bowers had six plush seats to choose from in front of the massive standard cargo area, which has a 40-cubic-foot and 400-pound capacity. The luggage of four people, several bags of camera gear, a large picnic table and chairs, and a large cooler added up to about 200 pounds of stuff that was easily and quickly loaded through the oversize cargo door, the opening of which is 4.4 by 4.3 feet. Had we needed more space, an extended cargo net allows for 80 cubic feet and 500 pounds of cargo.
Despite the heavy load in the back, there was no need to put a stand under the tail. The Pilatus is well-balanced and has a wide CG envelope. With full fuel, our takeoff weight was 10,342 pounds — about 100 pounds below max gross. We would, however, have to burn about 400 pounds of fuel to get below our max landing weight.
We took off from Camarillo into 400-foot overcast skies. The temps were warm enough that we didn’t have to worry about icing, and above the shallow layer of clouds near the Pacific coastline it was severe clear as far as we could see. Had there been potential for icing, the Pilatus would have pushed us through, with boots on the wings and tail, heated engine inlets and electrically heated windshield, prop and AOA vanes. The AOA vanes will activate a stall-warning horn and the stick shaker if the angle of attack becomes critical. If a recovery is not initiated, the stick pusher will reduce the angle of attack. The critical angle of attack is indicated on the speed tape and takes into account flap settings and icing conditions.
The most common executive configuration has six plush seats in the cabin ahead of an impressive cargo compartment.
Pilatus Aircraft Ltd
The fact that we had filled the fuel tanks near the top would have allowed us to keep flying for a very long time. It took us 22 minutes to climb to 27,000 feet, where the pressurization system, which uses bleed air, kept the cabin at a comfortable 8,000 feet. Once leveled off, we could have kept flying for well over six additional hours. In fact, we could have kept flying nearly all the way to the Atlantic Ocean with the tailwind we had. Those who need to travel that far will appreciate the lavatory, which is located behind the copilot’s seat.
Our mission was not a long-range flight, however. It was pure play. Our target was not even an airport. It was a secret lat-long point in Utah that took us to a spectacular dry lake bed surrounded by rugged, colorful rock formations.
We were not in a big hurry, so at 27,000 feet we set a normal cruise setting, which produced 261 ktas in ISA+10 conditions — spot on with the PC-12’s performance calculator app on the iPhone. Johnson said that in the approximate 700 hours he’s flown using the performance calculator, it’s been within a few knots and, over a trip, the flight-planned fuel-burn numbers are generally within 50 pounds of the actual numbers.
At 27,000 feet, the time of useful consciousness without the pressurization is only about three minutes. However, the PC-12 can get down quickly, using emergency descent procedures. With power to idle, gear down and a target of 180 knots, the airplane would drop at 8,000 to 9,000 fpm. I had seen this in FlightSafety’s simulator in Dallas a couple of years back, and since we didn’t want to make our passengers uncomfortable, we didn’t do a real-life test.
In flight, I “poked and pecked,” as Johnson called it, my way around the Primus Apex to get more familiar with it. A few features stood out. Amending a route requires only a couple of clicks on the cursor control unit, and you can review a proposed route without committing to the switch. Jet routes and airways are really quick to enter too, and you can use either an identifier or the name of a waypoint for the exit point. Another terrific feature is the track-based synthetic-vision display, which puts the runway in the center during instrument approaches even in a strong crosswind.
In about an hour and 45 minutes, we had been transported from the hustle and bustle of Southern California to a completely different landscape, far from the light pollution of any city. I wished we had brought some camping gear, since this would be the ideal place to watch the Milky Way. And with the PC-12 you could live large while camping, fitting any gear you would like to bring. Well, perhaps not an RV, but you get the point.
The dry lake bed we landed on was as solid as concrete, but the PT6A engine and Hartzell prop stirred up an impressive amount of dust.
Pilatus Aircraft Ltd
Landing on the lake bed was smooth thanks to the 14 inches of travel on the trailing link landing gear. The brown-red-and-yellow paint scheme on N1677 blended in well with Utah’s desert landscape. The BMW Designworks interior was a subtle tan color to match the lake bed, with supple leather covering the seats that move forward and aft, inboard and outboard, swivel, and recline. The armrests, headrests and lumbar support are adjustable.
Many manufacturers offer a small number of paint schemes and colors to keep the fleet uniform. Pilatus offers customization at no charge. Owners can choose from several paint schemes and interior setups. However, if they want to go completely haywire with the paint schemes — a design that requires an airbrush artist to come in, for example — there will be additional charges.
To reduce the spec process and make life easier for the customer, options are now offered in packages. The only avionics suite offered for the new PC-12 NG is the integrated Primus Apex system. There are, however, several options within Apex, such as different levels of database coverage, Internet service and satcom. Aspen’s connected cockpit for Pilatus allows for worldwide database updates in about 15 to 20 minutes without the need to plug anything in.
Returning to civilization at the PC-12 NG’s U.S. home at the Rocky Mountain Airport near Denver after our short Utah adventure, I was not surprised at the success the Swiss manufacturer has had with its flagship turboprop. Over its 23-year history, the PC-12 fleet has accumulated more than 6 million flight hours, and by the time you read this, Pilatus will have delivered its 1,500th PC-12.
Super Versatile Turboprop
While the PC-12 NG shines in unusual environments, such as dry lake beds, grass strips and on dirt, its missions are as varied as its paint schemes. The first customer of the versatile turboprop was the Royal Flying Doctor Service in Australia, which still provides medical services in remote areas, where it operates more than 30 PC-12s along with other types of airplanes. RFDS will add several PC-24s to its fleet once they are ready to deliver.
With its large cargo door and sizable cabin, the airplane is ideal for emergency medical transportation, but it can do so much more. The executive configuration can seat up to eight passengers in the back. Up to four of those seats are quickly removable for those who want to load up oversize items, such as mountain bikes, ATVs, wild game or whatever your perfect adventure requires.
The configuration options range from a full aft cargo area to up to nine seats in the back. Fractional-ownership company PlaneSense on the East Coast and membership airline Surf Air on the West Coast have seen great success with their PC-12 fleets.
And if that’s not enough, the PC-12 is also being used for law enforcement, charter, airlines, special military missions and more. It’s worth noting that 70 percent of RFDS’s and the Royal Canadian Mounted Police’s PC-12 missions are to unimproved fields, such as gravel runways and even frozen lakes.
But 25 to 30 percent of the PC-12 fleet belongs to owner-operators who use the airplane for missions as varied as the surfaces of Mother Earth.
Interns at the Pilatus factory in Stans, Switzerland, have a chance to get firsthand experience working on the airplanes.
Pilatus Aircraft Ltd
Pilatus Inspires the Next Generation
Pilatus has an extensive internship program in Stans, Switzerland, with about 110 apprentices at the headquarters at any time. This program is now being brought to Broomfield, Colorado. Pilatus Business Aircraft has selected a group of high school students in Broomfield to come for a week or two this summer. The top three candidates will start their apprenticeships in August. The kids will work 2½ days at the Pilatus facility and go to school 2½ days at Front Range Community College. Then they transition to three days of work and 1½ to two days of school.
About 70 percent of young adults do an apprenticeship, says Pilatus Business Aircraft president Thomas Bosshard. Apprenticeships are available in nearly all industries: banking, healthcare, insurance, hospitality management and much more. They are funded by companies and regulated by the government to ensure the standards are the same nationwide.
At Pilatus in Switzerland, the young adults do a variety of apprenticeships, such as logistics, polymechanics, automation, administration, IT and aircraft painting. They get paid a salary, and their schooling is paid for. “So they come out after three or four years with college credits, solid education, solid training and no debt,” Bosshard says.
At the completion of the apprenticeship, some young adults go to university, some start working for Pilatus and others go to work for another company. “The whole principle is that you have to forget about your own company's interest,” Bosshard says. “A young adult you train can go somewhere else, but someone who apprenticed for another company may end up at Pilatus. I’m a big believer in the concept.”

Pilatus PC-12: The Value of Only One Engine
Pilatus PC-12 NG
Pilatus
__Many pilots want to fly a 1,000-mile trip nonstop. That’s about the distance from New York to southern Florida, or from Chicago to Miami, or from Atlanta to Aspen. And people want to take along all of their family, friends and stuff on these trips.
A bunch of airplanes can fly the 1,000-mile trip downwind, or on that mythical flight-planning day when there is no wind, but very few can make it nonstop every time upwind, particularly in the winter months when the wind aloft at turbine airplane altitudes often exceeds 100 knots. And even fewer airplanes can make the trip upwind with a big payload.
The exception is the Pilatus PC-12 NG single-engine turboprop, which can lug at least 1,200 pounds of payload over 1,000 miles against the strongest headwind and do it every time. And the PC-12 NG can fly the trip at maximum cruise speed of around 260 knots, not the much slower long-range speed. The reason it can reliably make the flight so many pilots want is because the PC-12 has more than 1,500 miles of still air range with a 1,200-pound payload. That means the PC-12 has the range to nearly span the continent downwind, and can always make it across the country upwind with only one stop.
Having great range is a terrific asset for any airplane, but there is an adage in aviation that an airplane can “outfly its cabin,” meaning the endurance of the passengers expires before the fuel supply does. While most pilots are willing to sit in a cramped cockpit for hours on end to avoid a fuel stop, nonpilot passengers are not. They demand room to move around, a private and usable lavatory and access to drinks and food.
Again, the PC-12 stands out for having a cabin almost 17 feet long and 5 feet wide, with 4 feet 10 inches of headroom. There is a private lav, and luggage is accessible in the rear of the cabin while in flight. The cabin equals, or at least rivals, some midsize business jets that have similar range.
All of the size, range and payload capabilities of the PC-12 flow from the fundamental design choice of using only one engine. Carrying the fuel to feed a second engine, plus the weight and drag of the engine itself, all cut into range and payload. The second engine and its costs also mean the twin-engine turboprop that comes closest to the PC-12 in cabin size and full fuel range falls hundreds of miles short when the same payload is aboard, and costs at least a million dollars more to buy.
It seems the Swiss engineers at Pilatus were thinking more of utility and operating flexibility than personal and business travel when they created the PC-12 in the early 1990s. That’s why the airplane has a huge cargo door in the aft fuselage, landing gear designed for the roughest runway, and a big fuselage to haul stuff. Early sales went to utility operators such as physicians in Australia who bought the airplane to fly into the bush to treat people in the remotest of areas. But when pilots in the United States learned what the PC-12 could do, they wanted to use it to fly their own missions that other airplanes just can’t accomplish.
Pilots flying utility missions into the wild have long made peace with the idea of having only one engine. Engine failure is, of course, a risk, but the list of risks in bush flying is so long that having only one engine is certainly not at the top. But would pilots and their passengers pay millions of dollars for an airplane with only one engine? Pilatus couldn’t be certain, so, as Cessna did when it created the Caravan, Pilatus aimed mostly at the utility market, and any business and personal use of the airplane would be a bonus.
A combination of good market timing, high fuel prices, the simplicity of single-engine operation for the owner pilot and, of course, the legendary reliability of the Pratt & Whitney PT6 turboprop engine made the single-engine PC-12 acceptable, and even desirable, to a huge segment of business aviation. Many understood immediately that the PC-12’s remarkable capabilities are a result of having only one engine, and that it would cost so much more to get the same capabilities in a twin-engine airplane.
The Spin Question All single-engine airplanes, including turboprops, must demonstrate the ability to recover from a one-turn spin in no more than one additional turn after recovery controls are applied. For an airplane the size of the PC-12, and considering its very long CG range, that spin recovery requirement could prove difficult to meet.From the outset, Pilatus engineers decided to address the requirement by including a stall barrier system as is found in most larger jets. Dual angle-of-attack sensors mounted on probes near each wingtip on the PC-12 sense when the wing is approaching a stall and command a stick pusher to forcefully move the control wheel forward. Because the pusher prevents an aerodynamic stall, there can be no spin and thus no need to demonstrate spin recovery.To the Federal Aviation Administration, the stick pusher delivers safety equivalent to that in the spin recovery demonstration. In another finding of equivalent safety, the FAA has certified the NG to stall at 67 knots at its maximum takeoff weight. The FAA determined that the crashworthiness of the PC-12 seats, restraints and airframe provides the same degree of safety as there would be without those elements - and thus approved the stall speed increase from the general requirement of 61 knots maximum for singles.* * * Real Dual Electrics Many single-engine airplanes now have dual generators or alternators, but the NG has a complete split-bus dual electrical system just like recently designed jets have. There are also two batteries, one for each bus, and an additional emergency battery to power backup equipment should all else somehow fail.As in the jets, both generators have the same capacity, 300 amps. The generator on the No. 2 bus also serves as the starter. After engine start, the two electrical buses are independent of each other, so a single short or other failure can't damage the other bus.Unlike in most singles with dual generators, both units on the NG are gear-driven by the engine instead of belt-driven. Belt failure is just one more thing an NG pilot doesn't need to worry about.
The faith in the PT6 engine is so great that some flight departments that operate medium- and long-range business jets have added a PC-12 to their fleets for missions that don’t make sense in the jets. There is a booming passenger charter business flown in PC-12s, and passengers don’t give the single engine a second thought. And in real-world operation the PC-12 safety record has been better than that of turboprop twins. The comparison is complicated by the fact that there are so many more twins flying, and the PC-12 fleet on average is much newer, but it is still conclusive that the PC-12 has not yielded anything to the twins in terms of overall safety.
During the 15 years or so that the PC-12 has been in service, Pilatus has made many improvements to the original design. Maximum takeoff weight has gone up, a more powerful engine is now used, and the entire avionics system was transformed about two years ago with certification of the Honeywell Apex system. Pilatus renamed the airplane PC-12 NG when Apex was introduced, with the NG standing for Next Generation.
Apex uses four big 10.4-inch flat-glass displays with the two MFDs stacked in the center as they are in some newly designed large-cabin jets. In fact, much of the display symbology and system operation is derived from Honeywell’s Epic avionics system, which is used in many larger business jets. Apex has a full CAS (crew advisory system), meaning all crew alerts are presented in plain language on the displays. The messages are prioritized in order of urgency and emphasized by using different colors. Transitioning from the “idiot lights” of an annunciator panel to a full CAS is a really big deal in terms of complexity and cost, but a CAS is so much more informative and useful for the pilots.
The PC-12 has always had a very stout and hardworking look about it, both inside and out. In the cockpit, the knobs, switches and flight controls all looked like they belonged in a bigger airplane, even though the PC-12 is plenty big. But Pilatus hired BMW Designworks to create the cockpit in the NG version, and the impression is more sleek and modern. I felt as though I were in the newest business jet instead of a single-engine airplane when I got to fly the NG.
The PT6A-67P in the NG is one of the most powerful in the PT6 turboprop family, with the capability to produce 1,845 shp. Pilatus restricts maximum output to 1,200 shp, so the difference between that and the maximum power potential is available on very hot days, or at higher altitudes. This “flat rating” is common in turbine engines, but the NG has one of the largest percentage differences between maximum engine power potential and the amount of power actually transmitted to the prop. The huge amount of flat rating means the NG can operate from very high-elevation runways on hot days, and can cruise faster at its 30,000-foot ceiling.
The quality of the metalwork in the PC-12 has always been first-rate, but executive interiors had not matched other business airplanes of its size in terms of sophistication and materials. With the NG, however, the cabin appointments are better and the airplane is getting closer to its competition in that category. Pilatus offers a variety of interiors for executive, high-density, cargo or a combination of cargo and passenger missions. Even with a typical six-seat executive interior, there is still gobs of space in the aft cabin for baggage. You can even load your Harley through the big cargo door, as Pilatus has demonstrated at many airshows.
The wing is long and slender with a span of more than 53 feet and an aspect ratio of 10.2. The flaps extend along about 80 percent of the trailing edge, leaving room for rather short-span ailerons. The flaps need to be very large because certification rules limit the maximum stalling speed of single-engine airplanes — including single-engine turboprops — to 61 knots. An effective flap is a good way to lower stalling speed while keeping total wing area small enough to be efficient at cruise.
Short-span ailerons are typically less effective and require more stick force than longer-span surfaces do, and that is true in the PC-12. However, Pilatus added servo tabs to each aileron several years ago, which greatly reduced roll force. The PC-12 is still not light on the controls, but the harmony of forces is pretty good, and it’s easy to fly the airplane smoothly.
The Apex avionics system makes use of what Honeywell calls INAV, for integrated navigation. What that means is that you can perform most flight-plan and other avionics entries using a cursor and menus. Pilatus recently installed a track ball on the center pedestal so you can use your fingers to position the cursor on the four displays. Graphical flight planning is as easy as putting the cursor on the moving map over the fix you want to add to the flight plan and clicking. Drop-down menus are a click away to select frequencies, view checklists, look at system synoptic pages and so on.
As in some jets, you can see everything you need to fly the NG on the PFD (primary flight display) in front of you, including engine, navigation and communication frequencies. Of course, you can move data around by opening and closing windows and can pretty much configure everything except the actual primary instrument display to your liking. With a host of line-select keys on the edges of each display, it doesn’t take long to figure out how to operate the system. Synthetic vision and enhanced GPS navigation based on WAAS are expected to be available later this year.
Pilatus chief pilot Peter Duncan and I had the Apex system programmed for takeoff and quickly worked through the mercifully short checklists in just a few short minutes after engine start. As you can imagine, setting enough rudder trim for takeoff is a big deal with that much power going to a single propeller, so you dial the trim way over to counteract the torque. I realized a couple of minutes after takeoff that I wasn’t pushing on the rudder pedals even though I had forgotten to adjust the trim from the takeoff position. What I had done is turn on the yaw damper, which is now a smart system, and it adjusted the trim automatically. One more issue with a single-engine airplane resolved.
The autopilot in the Apex system is excellent and shows off its jet heritage by flying the NG with smoothness and precision. I watched the Apex system fly several approaches, including automatically entering holds and procedure turns and exhibiting all of the stuff that is expected for new avionics systems but is still amazing. One of the most unusual features of Apex is that it has coupled go-around, meaning when you push the go-around button on the throttle, the autopilot remains coupled. In other airplanes, without an autothrottle the autopilot typically uncouples at go-around and you need to re-engage the system. I like the autopilot-coupled go-around, but some certification types worry the human pilot will forget to advance the power if the autopilot is flying. That makes no sense to me, and I think Pilatus and Honeywell got it right.
The PC-12 can use rinky-dink runways of less than 2,000 feet, but it can also fit in smoothly at busy airports, because you can extend the landing gear at up to 180 knots and approach flaps at 165 knots. And I don’t think you can ever be flying too fast on final in the airplane because of the massive speedbrake mounted on the nose. When you pull the power back to idle, the propeller blades go to flat pitch and the propeller becomes a huge disk of drag. You can fly amazingly steep approaches with the engine at idle, or can slow from jet approach speeds to a normal landing in almost no distance by chopping the power.
The long-stroke trailing link main gear is designed for unimproved surfaces, so a normal landing on pavement is a thing of beauty. With reverse thrust from the big propeller, you hardly need brakes.
The PC-12 has demonstrated that people will fly single-engine turboprops, and pay more than $4 million for them. For the big majority of pilots, the answer to the question of how many engines you need is “enough to do the job,” and in the case of the PC-12, the magic number is one.
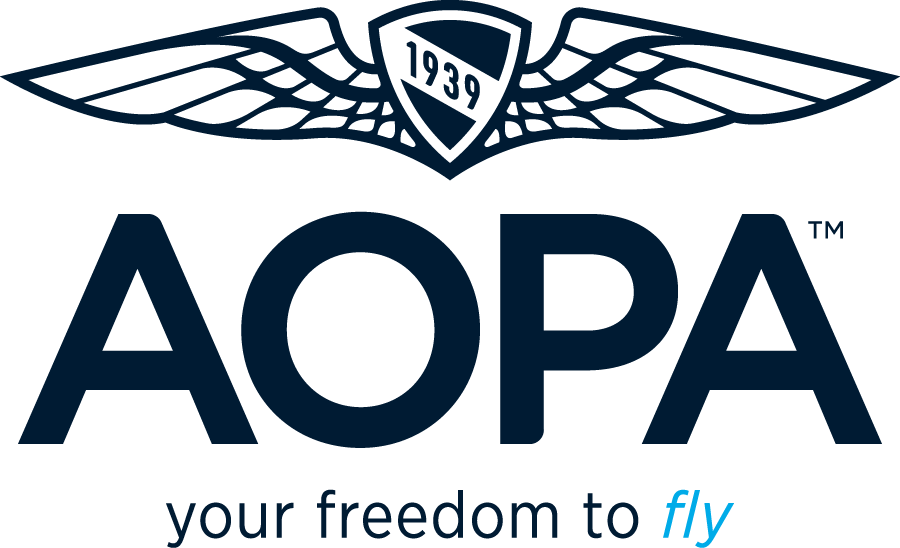
Cessna 208B - Caravan
Already a member? Please login below for an enhanced experience. Not a member? Join today
Go Fly Aircraft & Ownership Aircraft Fact Sheets Cessna 208B - Grand Caravan
Cessna 208B - Grand Caravan
Overview
Performance Summary
Specifications
The Cessna Caravan was big to begin with; now it is gargantuan. The Caravan is the largest single-engine airplane ever produced by Cessna. Comparing it to a Cessna 182 is like standing a pro basketball player next to a jockey — the 182 is lost in the Caravan's shadow. The latest version, the Grand Caravan, is even more imposing. It is 4 feet longer than the original Caravan and is the largest single-engine turboprop utility aircraft currently in production.
Cessna has produced four Caravan models, plus several variations: a special-missions version available with roll-up cargo door and pod for carrying eavesdropping electronics, a military cargo version, and a floatplane. The Caravan is available with either straight or amphibious floats. The Wipline floats are huge affairs — on dry land, the top of the amphibious float is 40 inches high. Fifteen float-equipped short-body Caravans have been sold. (Floats are not available for the stretch Caravans.)
The prototype Caravan first flew in December 1982. It was intended as a replacement for Cessna 206s, 208s, and other smaller, aging utility aircraft doing hard labor in remote regions of Africa and other places where facilities can be crude and avgas scarce.
Even before it was certified in 1984, the Caravan found a big home in the U.S. Federal Express Corporation ordered a specially equipped, windowless version, the 208A Car to expand and extend its overnight small-package pickup and delivery service to medium and small communities. Since then, Cessna's Caravan business has been driven largely by Fedex's needs, and after putting its first batch of Caravans in service, Fedex discovered the airplane was limited by volume rather than weight. Cessna's solution was to add 20 inches to the Caravan's fuselage ahead of the wing and 28 inches behind the wing. The stretch added 34 percent more volume to the fuselage and resulted in the 208B Super Cargomaster.
The 208B will hold 340 cubic feet of cargo. If that still isn't enough, Cessna offers an optional 111.5-cubic-foot, 1,090-pound-capacity belly pod. Rumor has it that animals and even people have been carried in Caravan pods — illegally, of course, and without question uncomfortably.
Cessna increased the 8,000-pound maximum takeoff weight of the Cargomaster to 8,750 pounds for the stretched Super Cargomaster (of the additional 750 pounds, 450 pounds is available for payload) but stuck with the same 600-shaft-horsepower Pratt & Whitney PT6A-114 turboprop engine. However, the Super Cargomaster was restricted to 8,000 pounds for flight in icing conditions because of reduced climb performance at the higher gross weight. Cessna corrected the problem by upgrading to a 675-shp PT6A-114A engine.
The Grand Caravan, fourth in the Caravan series, was introduced in October 1990. It incorporates all the best features of the other models, including the more powerful engine, longer fuselage, and cabin hardware that enables it to be quickly converted from a people-hauler to a cargo truck or a combination of the two.
Lovely it is not, although there is a certain stately appeal to the utilitarian, efficient look of the Grand. Because beauty wasn't even on the first page of Cessna's priority list for the Caravan, designers concentrated on features that help the airplane and pilot do their work better. Ease and cost of maintenance also were primary considerations, starting with the propeller, a fat, three-blade McCauley. Originally, the Caravan used a composite Hartzell. The switch was made to metal because it costs half as much to buy and repair, according to Cessna — which owns McCauley.
The Grand Caravan has four doors: one for each crewmember, a right- side airstair door, and a yawning left-side cargo door. The cabin has 14 seats. There is plenty of room for more, but few countries allow more than 14 people in a turbine airplane without imposing some extensive and expensive additional requirements, according to Cessna. (The FAA permits a maximum of nine passengers and two crew.) Firing up the Pratt & Whitney is a simple matter of toggling the battery, fuel boost, and start switches. As the gas generator (Ng) speed passes through 12 percent, the fuel condition lever is moved to Low Idle position. At 52 percent Ng, the starter switch goes to Off. Except for cockpit checks, that's it.
Occasional use of the Beta range to reverse propeller pitch keeps the taxi speed to a manageable clip and helps save the brakes, which are very effective. Mash either pedal, and the Grand Caravan will pivot on a main tire.
Pete Hall, a Cessna demonstration pilot and my guide for the day, suggests two notches (20 degrees) of flaps for the takeoff roll. Even though we are about 1,500 pounds under maximum takeoff weight, the initial acceleration is slow, but we don't cover much ground before rotating at 65 knots. Ground roll for a maximum gross weight takeoff in sea level standard conditions is 1,365 feet, according to handbook figures.
Put the nose on the horizon, and the airplane cruise-climbs at 110 knots and between 900 and 1,000 feet per minute. In low-altitude level cruise at 1,900 rpm, the airspeed creeps up to just below the 175-knot VMO. A more representative scenario is a quieter, more comfortable 1,750 rpm at 6,000 feet. Those numbers should yield a true airspeed of 180 knots on about 415 pounds per hour (62 gallons) of fuel, according to the handbook. A cargo pod would scrub about 9 knots off the cruise speed.
With 332 gallons of usable fuel, the Grand will fly for 4.6 hours at maximum cruise power with a 45-minute reserve, according to specifications. Our demonstrator for the day, N208CC, is loaded with most of the options on Cessna's list, including Bendix/King KFC 150 autopilot/flight director system and RDS 81 radar, yet it could still take on full fuel and 1,715 pounds of payload. Reduce the fuel load to half and the power to best-range cruise, and you can carry 2,800 pounds of people and cargo and cruise for three hours at 147 KTAS on 47 gallons per hour.
If there is no comparison in size between a Grand Caravan and a 182, there is in flying qualities. In fact, once you acclimate to the height and the spaciousness of the cockpit, you tend to imagine yourself in a smaller Cessna.
It’s remarkable that the Grand Caravan can take on two tons of fuel and payload and still handle like a much smaller airplane. Long, single-slotted flaps that incorporate leading edge vortex generators and trailing edge angles (to keep airflow attached and thus maintain the effectiveness of the flaps) enable the Grand Caravan to easily beat the 61 knot stall requirement for singles.
Long flaps mean short ailerons, so the Grand Caravan has spoilers to augment roll control. Roll forces are light considering the huge wing, and there is almost no adverse yaw.
The pilot has excellent control over the entire speed range of the airplane. To demonstrate, Hall has me transition from cruise to approach by pushing the prop control full forward, pulling the power back to the stop, and selecting full flaps. The airplane noses down as if we are on a ski slope, but the airspeed lounges at around 80 knots. You can pretty much pick the patch of ground you want to plunk down on, even if you're high and close in to the runway.
We have fun shooting spot landings at Maize, a 2,100-foot-long grass strip within sight of Wichita's Mid-Continent Airport. We try everything — no- flap landings and takeoffs, short- and soft-field approaches and departures, and slips to landing. I quickly feel very comfortable aiming the big airplane at the little strip. From there, we return to Mid-Continent and are given a place in line with arriving jet traffic. Tiny Maize or expansive Mid- Continent — the Grand Caravan is at home in any environment.
Cessna Grand Caravan
Mark R. Twombly, AOPA Pilot, June 1991
Exciting Career Opportunities with AOPA
Interested in working for the most influential general aviation association in the world? If you're energetic, dedicated & passionate about general aviation, we invite you to consider joining our growing team!
ABOUT AOPA
©2017 Aircraft Owners and Pilots Association
421 Aviation Way Frederick, MD, 21701
800.872.2672

Cessna Caravan Perfected?
Today the airplane is more popular than ever. FedEx, Cessna's biggest Caravan customer, operates about 260 Caravans, the Super Cargomaster model, done up with baggage compartments in every nook and cranny. And the airplane remains a mainstay in the developing world as a go-anywhere people and freight hauler, in coastal regions as a carryall water taxi, in the outback as a rugged-minded air ambulance and with special missions operators worldwide.
And thanks to its voluminous cabin and fancy optional Oasis interior (which Cessna sells in partnership with KICT neighbor Yingling Aviation), the airplane has become a hugely successful private transportation tool. It's a turboprop single with a light bizjet-size cabin that excels at flying regional hops while giving the folks in back a fine level of comfort. And it can carry them into just about any kind of landing strip you could imagine, from remote Alaskan outposts to a grassy strip on the Vineyard. The executive market is not a little niche. Cessna says it accounts for a big percentage of Caravan sales.
Despite the Oasis option, until now the cockpit of the Caravan was lacking the kind of flat-panel avionics system that is standard in just about every production airplane you can name, even Cessna's own basic four-seater, the 172 Skyhawk.
Not too long ago, when everybody began to realize that flat-panel avionics systems would become available for just about every class of airplane imaginable, there were some who thought that utility airplanes-cargo haulers, bush planes, remote air taxis and the like-might take a decade or more to come into the digital fold, if they did at all. Those predictions seem silly today.
When it comes right down to it, flat panels have it all over steam gauges in just about any conceivable application. They're more durable, more cost-effective and more easily replaceable, key factors to fleet operators because they mean less down time and more profit.
So to the surprise of no one, when Garmin looked to upgrade the Caravan, it went with the Garmin G1000 integrated avionics suite, a decision that makes G1000 standard in every single-engine Cessna airplane (except the SkyCatcher, which will have a new and different Garmin flat-panel system).
And G1000 is a brilliant addition for the Caravan. As you can see from the accompanying photograph, there's no sense that the G1000 system was shoehorned into an existing panel. It looks like it was born there. The scale of the displays, three 10.4-inch LCDs, is just right for the panel, and the backup instruments, switches and the flight guidance panel are all conveniently and logically located in the clean layout.
Of course, this is helped tremendously by having the engine instruments on the MFD. Especially for start-up and takeoff, having the clean, intuitive graphical displays right there in front of you makes managing power and temps on the big PT6 a breeze.
In addition to the skillfully executed engine instrumentation, the G1000 solution in the Caravan includes two huge improvements over the airplane's previous functionality, the integration of the excellent Garmin GFC 700 autopilot and the addition of WAAS.
As we've been saying about it since its introduction, the GFC 700 is a revolution, and these days when I get a chance to fly another airplane into which it's been adopted, I've pretty much stopped being surprised by its silky smooth performance and widebody bizjet features. So as I'd expected, the integration in the Caravan is very nicely done. The flight guidance panel-the same unit as in the Mustang light jet-sits directly above the MFD, in easy reach of a pilot flying from either seat. And the addition of WAAS to the system gives Caravan pilots a whole new level of precision-including WAAS approaches with vertical guidance down to ILS-like minimums.
In an airplane such as the Caravan, one that gets flown by a single pilot, often in demanding conditions, there's no doubt that all of this adds up to greatly increased safety and capability. Adding to that is the MFD, which offers a wide variety of standard and optional safety utilities. Standard fare includes Garmin's SafeTaxi airport diagrams, its terrain and obstruction database, and Garmin FliteCharts electronic approach charts. Options include XM Weather, Jeppesen electronic approach charts, L-3 Stormscope, TAWS, the Bendix/King KTA 870 active traffic system, among others. The result is twinjet avionics capability in a turboprop single.
The 2008 Grand Caravan comes standard with the Garmin G1000 integrated avionics suite with three 10.4-inch LCDs, two primary and one center-mounted multifunction display, with the GFC 700 digital autopilot with panel-mounted flight guidance panel. Also standard are dual AHRS, dual air data computers, integrated Garmin audio system and more. Available utilities include Garmin's SafeTaxi runway diagrams, terrain and obstruction database and FliteCharts. Options include the TKS icing protection package, air conditioning, built-in oxygen system, Garmin GWX 68 color weather radar, XM satellite weather, the Bendix/King KTA 870 active traffic system and more. All specifications are for an airplane without the cargo pod. Figures are from the manufacturer and are for standard conditions unless noted.
Ice Off
The other big improvement to the airplane is one that the passengers might not even notice (other than aesthetically, that is), the switch from pneumatic boots to TKS "weeping wing" ice protection.
With the addition of TKS, the Caravan gets a lot of additional protection, and some hidden benefits, too.
While boots have their strong points and are the obvious choice for some airplanes-Cessna puts them on its Mustang light jet-they have real limitations in other settings, especially on an airplane like the Caravan with so much surface area and so many appendages (landing gear, cargo pod, wing struts).
Boots work, as you know, by inflating-they're powered by an engine-driven pump-and shedding any accumulated ice. As such, they are deicing and not anti-icing devices. Historically, there's been a great deal of controversy over when and how often the boots should be cycled. The current thinking on the subject is, early and often. But the fact is that boots don't do anything for areas they don't physically cover. With the TKS system, the fluid seeps rearward with the airflow, protecting airframe components downstream, including the windshield and cargo pod. TKS can't replace pre-takeoff deicing on the ground, but it's more effective than boots at protecting the airframe against some forms of inflight icing, like freezing rain and freezing drizzle.
In contrast to boots, the TKS system-which is also certified for flight into known icing on the Caravan-works by seeping a glycol-based fluid out of tiny pores on a machined titanium leading edge, as well as through a prop slinger. The airflow streams the fluid back, coating the surface area of the airplane and preventing ice from forming or adhering. The outflow of fluid off of the prop protects the windshield and cargo pod. According to Cessna-I didn't do any ice flying in the Caravan I flew-the system works very well at keeping the airplane ice free.
Including the wing, tail and wing strut leading edges, plumbing and dual pumps, the TKS system weighs only about 75 pounds installed, which is close to a wash when you remove the boots and attendant hardware. The downside is that the fluid is heavy. With the 20-gallon tank full, you've got an additional 184 pounds on board. The good thing is, handling that kind of weight increase is doable for a Caravan. Moreover, since icing is a seasonal issue for nonpressurized airplanes, operators won't have to tanker a passenger's worth of glycol around with them in the summertime. And with this airplane, finding a place to put a 20-gallon TKS fluid tank was easy: in the pod. For those few Caravans sold without a pod, Cessna is developing what it calls a "blister," to be located on the belly of the airplane solely to house the TKS tank. Of course, for airplanes that operate in tropical and hot and dry climates, there's no need for the system, an option at around $77,000.
But for those operators who do face icing challenges, TKS represents a real change to the Caravan. Is TKS superior technology to boots? It really depends on the airplane. But that said, in the case of the Caravan, it's clearly the better choice, and Cessna has enthusiastically embraced the technology.
Flying the G1000 Caravan
There are, as you might know, three different Caravan models, with the Grand Caravan, a 4-foot stretch version of the original, being the most popular for personal, corporate and charter use. The airplane I flew was a preproduction Grand Caravan with a lot of brightly colored, heavily wired test equipment in back, but with enough room still for myself, Cessna engineering test pilot Scotty Jurgenson in the right seat and Cessna's media relations manager Pia Bergqvist in back.
I'm not the first to say it, and I won't be the last, but flying a Caravan is very much like flying a really big, really powerful 182, except that it flies even a little nicer than the Skylane. With its Pratt & Whitney PT6 up front putting out 675 horsepower, the Caravan with its humongous, high-lift wing is no speed demon, but it climbs impressively, even at high weights.
We were light, and it was a bit gusty as we lined up on KICT's Runway 1R and prepared to head out to the west to play. One of the things that G1000 brings to the Caravan, graphical engine indications, came in immediately handy as I set the power and we began to roll. After having put in a little too much juice, which Scotty promptly pointed out, it was easy to see where to come back to, simply by bringing the power indication back into the green range on the tape.
The Caravan was the eighth airplane I'd flown with a G1000 panel and the fifth with the GFC 700 autopilot, and I expect that list to keep growing. While I'm not an expert in the system yet, it sure felt familiar, and I thought about how the system was turning into a standard of sorts in airplanes from light singles to jets, something the aviation industry has never really had (though King's Silver Crown stacks of the '70s came awful close). With G1000, even if you're new to the airplane, you're not new to the panel, so the transition will be easier, as it was for me in the Caravan, and you can concentrate on learning to fly the airplane instead of spending your time learning which buttons to push.
As I said, I found the autopilot integration very pleasing. Even though the Caravan is a big airplane with a big wing, lots of lift and a ton of power, the autopilot drove it around the sky very smoothly. I was impressed. And the use of the flight guidance panel, as in the Mustang, makes using the GFC 700 extremely intuitive.
I won't go into a lot of detail on flying the G1000 Caravan, as we've written extensively about both the airplane and the avionics suite before, except to say what Cessna has already figured out. Once Caravan pilots get a sniff of the flat-panel goodness that is G1000, they're going to want it.
The G1000 Effect
One of the real benefits of the G1000 avionics suite isn't felt by the operator but by the company that puts Garmin's immensely popular flat panels in its airplanes. Mooney came right out and said at Oshkosh a couple of years ago that the introduction of the G1000 in their airplanes might have saved the company. Many others have reported immediate and steep sales growth once they had G1000 in the cockpit.
But how could the same thing happen with the Caravan, an established, already successful and somewhat specialized airplane? I wouldn't have thought so, and neither did Cessna, until it happened, that is. Once the company launched G1000 at the NBAA Convention last fall, orders went through the roof and Cessna had to briefly stop taking fleet orders for fear of not being able to build enough airplanes fast enough. The end result: Cessna plans to build more than twice as many Caravans in '08 as it did last year.
Not bad for an airplane that was supposed to be long gone by now.
0 Comments

2008 - 2010 Cessna Caravan 675
2008 - 2010 Cessna Caravan 675
Cessna Caravan 675 is a single turboprop engine, fixed-gear short-haul regional airliner, built by Cessna and also stands out by its flexibility and performance.
Specially designed for the abuse of unimproved runways, this aircraft keeps up with the most demanding requirements, whatever your destination is, it can take you there and it can land in places at your choice.
Year:
2008- 2010
Make:
Model:
Engine:
Pratt & Whitney PT6A-114A turboprop
Top Speed:
213 mph
Price:
1,969,050
That’s why Caravan is the preferred aircraft for transporting people and cargo around the world.
If you are hunter or fisherman, Caravan 675 can get you in virgin and beautiful places.
There are twelve aircraft passengers’ seats, with a single person crew. There is plenty luggage space and room for your best friends.
The main characteristics for 208A Caravan 675 are: versatility, fuel-efficiency and also cost-effectiveness.
Exterior
Caravan has the necessary equipment to handle difficult situations.
The large wings offer some advantages to Caravan 675, great visibility, stability, sun blocking and also weather protection.
Another characteristic of the 208A Caravan 675 is the easy access to pilot, passenger and cargo doors. The durable aluminum from which is built Caravan makes it easy for maintenance and repair. The airframe has no life limits.
"Caravan 675 has a McCauley 106-inch diameter"
There are still many things to say about function and design. Caravan 675 is an excellent aircraft of land, air and sea, no matter what kind of weather is, it can make your wish came true.
Having for the main gear a flexible design ideal for grass, gravel and even rough airstrips and noticing that the nose gear is engineered to absorb both vertical and lateral force by transmitting the impact to the fuselage, we can affirm that versatility and flexibility are other principal characteristics of Caravan 675.
All aboard
A durable airstair is created to help the passengers to board quickly. Also the door is easily closed or opened from outside or inside.
Powerful propulsion
The Caravan 675 has a McCauley 106-inch diameter, three-blade, metal, constant speed, full-feathering, reversible pitch propeller. The propeller is equipped with an overspeed protection system that is controlled by a governor, reduction gearbox and is backed-up by an overspeed governor as a redundant safeguard.
DimensionsCaravan 675
Exterior
Height14 ft 10 in (4.52 m)
Length37 ft 7 in (11.46 m)
Wingspan52 ft 1 in (15.87 m)
The Caravan 675 Interior
Interior If you are flying either with your family or for business interest the Cessna Caravan 675 is the best decision you can take. In this aircraft can fit 12 passengers, it has 340 cubic feet (9.6 m3), also you can carry a lot of cargo and your excursions will be excellent.
Executive Floor Plan:
Comfort – is another word to describe the interior of this aircraft. The design is an elegant one.
Interior Highlights:
The leather seats - redesigned, the wood trim, the cabinetry, the flat-panel video displays make this an elegant aircraft. You can reposition or remove the seats to help passengers or cargo, for a better positioning. Caravan 675 has a double cargo door which greatly eases your work. So we realize that it will be a better access for loaders.
Cabin DimensionsCaravan 675
Cabin
Height54 in (1.37 m)
Width64 in (1.62 m)
Length17 ft 4 in (5.28 m)
Standard Seating Capacity8
Baggage Capacity31 cubic ft (0.9 cubic m)
Caravan 675 Avionics:
On April 28, 2008, Cessna announced that the Garmin G1000 glass cockpit will be standard equipment on all new Caravans.
We can notice here the Garmin G1000 glass cockpit which integrates all primary flight, also a powerful engine and a sensor data, necessary for flight. The system is composed of some important elements like a dual Nav/Comm/GPS, a fully integrated transponder, Two LCD primary flight displays.
Another significant element is the Multifunction Display from center that show the real-time flight-critical data, including traffic, digital attitude,heading, engine, airframe Indication and Crew Alerting.
We also have to take into account the capabilities of Garmin’s new digital, fully-integrated GFC 700 automated flight control system. With all these things your safety and confidence will be at maximum.
Flight Control System
The controls for the Garmin GFC have innovative features like: airspeed hold, pitch hold and coupled VNAV, overspeed protection. We should add here an important thing like the lateral and vertical guidance; also the capabilities formerly are available only on the most sophisticated business jets.
Color Weather Radar
The weather is a major problem for many aircrafts.
So, for detecting and avoiding rough weather, the G1000 glass incorporates the Garmin GWX 68 Airborne Color Weather Radar, that will give to the pilot the best detailed pictures of flight conditions, which increases safety of Caravan 675.
Caravan 675 Engine
This aircraft has over 300 million total flight hours to its credit.
The overhaul of the Caravan’s Pratt & Whitney PT6 engine should be done at the interval of 3,600 hours and a hot section inspection at 1,800 hours.
In less than 15 minutes, the cowling can be removed, showing the engine and accessories. So you can keep this splendid aircraft in the sky, where it belongs.
This engine is flat-rated to 675 shaft horsepower at 1,900 rpm. The engine indication system shows numeric readouts of critical engine fuel and electrical indications for torque and other. Also it’s installed a wet type standby engine torque gauge.
Caravan 675 Safety
Safety is another word that characterizes Cessna for more than 80 years. Caravan customers have a lot of benefits: first is the insurance, second – the lower costs, third – the confidence.
We can enjoy the full benefits of this aircraft like a smooth landing, a flexible design and large rough-field tires.
Peace of mind
The Caravan customer feedback about the fusion between the design and refinements is an excellent one.
The high-wing design offers many advantages like a great stability and a superb visibility, for the pilot and passengers, also the easy access for they and for cargo.
Highly skilled at cockpit organization
The Garmin G1000 glass cockpit integrates all primary flight, sensor data and engine. So, you have to stay without any charts or clumsy books, just enjoy the fly!
Specification
PerformanceCaravan 675
Single Pilot CertifiedYes
Maximum Cruise Speed186 ktas (344 km/h)
Certified Ceiling25,000 ft (7,620 m)
Airport Performance
Takeoff Distance2,055 ft (626 m)
Landing Distance1,625 ft (495 m)
Rate of Climb at Sea Level1,234 fpm (376 mpm)
Range946 nm (1,752 km)
Maximum WeightsCaravan 675
Ramp Weight8,035 lb (3,645 kg)
Takeoff Weight8,000 lb (3,629 kg)
Landing Weight7,800 lb (3,538 kg)
Zero Fuel WeightN/A lb (N/A kg)
Usable Fuel Capacity2,224 lb (1,009 kg)
Typically-Equipped Empty Weight4,751 lb (2,155 kg)
Useful Load3,284 lb (1,490 kg)
Maximum Payload3,049 lb (1,383 kg)
Full-Fuel Payload1,060 lb (481 kg)
Specifications
PowerplantCaravan 675
ManufacturerPratt & Whitney
Model (Number)PT6A-114A (1)
Time Between Overhauls3,600 hr
Pricing and Cost
Price is $1,969,050
Operating CostsCaravan 675
Cost per Mile$2.06
Cost per Hour$358
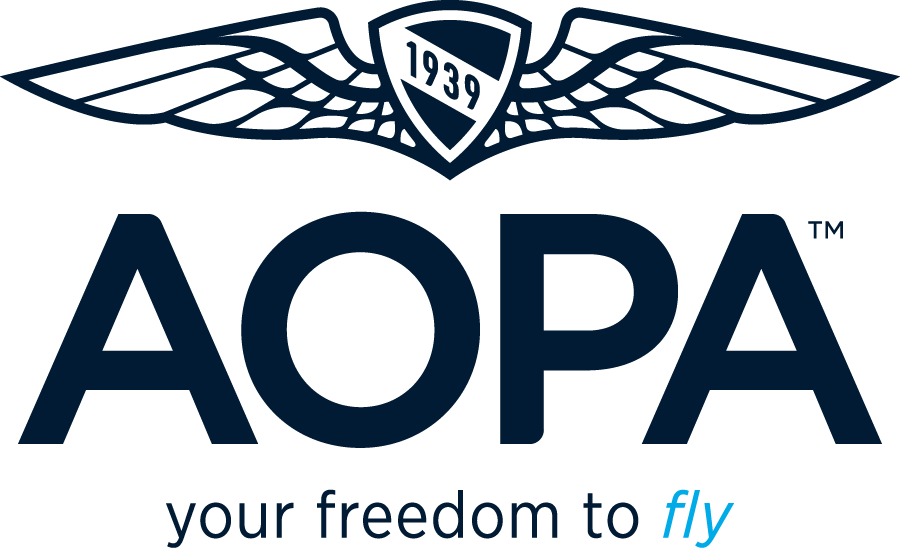
Quick Look:TBM 700 Daher-Socata's 'very fast turboprop'
The TBM 700, powered by a 700-shaft-horsepower Pratt & Whitney PT6A-6, is an outgrowth of the Mooney 301—a 360-horsepower, six-seat, pressurized, piston-engined airplane that made its initial flight in April 1983. After a French consortium purchased Kerrville, Texas-based Mooney Aircraft Corporation in 1985, the U.S. company and France’s Socata (Aerospatiale’s general aviation division) formed a joint venture—TBM International—which began development of a larger, faster, and more powerful turboprop derivative of the Mooney 301.
The first of three TBM 700 prototypes initially flew in July 1988. French certification was achieved in January 1990, followed by FAA approval in August of that year. Two production lines were planned—one in Texas at the Mooney factory to serve the U.S. market, and the other in Tarbes, France, to build aircraft for the rest of the world. Interesting factoid: “TBM” stands for “Tarbes-Mooney.” Shortly after delivery of the first production TBM 700A in late 1990, however, Mooney withdrew from the program.
Initially, the only competitor to the high-speed TBM 700 (capable of cruising at 300 knots at 31,000 feet) was the much slower Cessna Caravan I, which was designed primarily for utility operations. Eventually the more powerful Pilatus PC–12 and smaller Piper Meridian entered this market as well, although the TBM 700 remained the fastest of the single-engine turboprops.
The TBM 700A, which featured Bendix/King avionics, was replaced in 1999 by the 700B, which offered a larger, wider rear door; an optional forward pilot door; increased maximum zero-fuel weight; and other improvements. The TBM 700C1—which included a reinforced structure, new air-conditioning system, and other enhancements—was certificated in 2003. The TBM 700C2, which featured new avionics (including dual Garmin GNS 530s) and a substantial increase in maximum takeoff weight (to 7,394 pounds), was the production model until it was superseded in 2006 by the TBM 850, powered by a 850-shp Pratt & Whitney PT6A-66D. Since 2009, TBMs have been built by Daher-Socata, a company created when French manufacturer Daher bought a controlling interest in Socata.

TBM 850: A Jet With a Prop
TBM 850
__Flight level 280 in a TBM 850 was just perfect for us coming out of Peachtree in Georgia, headed down to cozy North Perry Airport near Fort Lauderdale in south Florida. On a really long trip we could have climbed up to FL 310, lost a few knots, saved a few gallons per hour and been perfectly happy. But the airplane we were flying, while RVSM-ready, wasn’t yet RVSM-approved. On that trip, it didn’t matter. We were happy with the few extra knots we got down at 280.
The airplane we were flying was a very special TBM 850 built to commemorate a milestone the likes of which none of us has seen before, the 100th anniversary of an airplane manufacturer.
Article Continues Below:
Aerobatics with Matt Chapman at Oshkosh 2016
Flying magazine met up with airshow performer Matt Chapman in Oshkosh for ...
Our trip out of Atlanta was a typical trip for the 850, but then again, there aren’t many that aren’t typical.
I flew into Atlanta Hartsfield-Jackson International from my home base of Austin, Texas, on Delta, and got a lift over slow, rainy Atlanta highways up to Daher-Socata’s sales office at DeKalb-Peachtree Airport (PDK), where the TBM awaited. The weather was cruddy, about 400 overcast with light rain, but I knew from my airline trip into town a little earlier that the ride was decent and the tops weren’t very high, maybe around 15,000 feet. In this case, I was able to provide my own pirep.
The 100th anniversary TBM — its N-number is 1911Y; get it? — is a gorgeous airplane, with a special paint scheme, gold-plated air vents, creamy leather upholstery and commemorative placards. I tried to think of what else the company could have done to distinguish it. There’s not much, really. Just about every TBM comes out of the factory loaded, with air conditioning, the Garmin G1000 avionics system with GFC 700 autopilot and sumptuous interior. There aren’t even that many options, and the best feature is standard: 320 knots.
The airplane gets its letter-designation from a combination of the company’s home base of Tarbes, France, and the “M” standing, as improbable as it sounds, for “Mooney,” which was French-owned for a time and which participated in the design of the TBM. Plans were to produce the airplane in Texas, but because of a combination of corporate drama and a market downturn, that never happened.
Instead, every TBM is built in Tarbes and is made ready to deliver with paint, interior and systems before being flown to the United States via the North Atlantic route: Scotland; Iceland; Greenland (usually); Goose Bay, Newfoundland; Bangor, Maine; and then down to North Perry. Because of the 850’s impressive range, no ferry tanks are required to make the trip.
Now, the TBM has the reputation for being a bit of a tight fit, which is entirely undeserved. The electrically operated door is huge, and the cabin is very comfortable. The rear occupants, who sit in a club seating arrangement, have plenty of room to sit facing each other without their knees coming close. (Intertwining knees is the way it’s done on more than one club-seating airplane.) The atmosphere, thanks to lots of glass, is airy, and with the introduction of the 850, there was another big cabin improvement — dual zone heating and cooling, which keeps both pilots and passengers happy.
One gripe that is at least somewhat deserved is that it’s a tight fit between the seats for the pilot to thread his way up front after getting in through the airstair door. Daher-Socata answers this shortcoming with one option that is popular with charter operators: the crew door, a forward-of-the-wing portal that allows the crew to get to their places without disturbing the passengers. It’s a $90,000 option that adds around 45 pounds to the weight of the airplane while detracting only very slightly from outside visibility. The airplane I flew did not have the crew door. If I were ordering the airplane, it would be a tough call. It’s not a cheap option, but it gives the pilot and front-seat occupant a great way to get out of the airplane in an emergency, and it does keep the cabin and cockpit separate.
The biggest news on the TBM, and it’s not all that recent, is the Garmin G1000 panel, which has been around for a couple of years now. At the time of the flat-panel makeover, Daher-Socata was reluctant to join the LCD crowd, but once it did, the move made nothing but sense. Daher-Socata vice president of sales Michel Adam de Villiers told me that, in all the time that the company has been ferrying G1000 airplanes across the North Atlantic, there hasn’t been a single avionics squawk. Before Garmin, it was a regular occurrence. This is, of course, just one in a long list of advantages that promote seeing the glass completely full.
The G1000 also saves a lot of weight, around 120 pounds. That’s a nearly grown kid, a giant dog or a couple of duffels filled with toys. Plus, the flat panels give you room to take that extra weight, since the greatly reduced depth of the displays opens up the entire forward baggage space, an area that previously was lost to the depth of the EFIS boxes. You can fit a couple of modest-size golf bags in the compartment, I’m told.
Moreover, G1000 cleans up an admittedly well-designed panel even more, allowing for a much cleaner look and, more importantly, greatly enhanced ease of use. Every switch, knob and lever is grouped into sensible clusters, some of them on a smartly designed overhead panel. To free up space in the cockpit, the quick-donning masks are located on the side-walls just behind the pilot and copilot seats.
You’d think that one G1000 installation would be pretty much the same as any other G1000 installation, but you’d be wrong. The location and size of the displays, controllers and keypads are set up differently from model to model because of panel restrictions and the need for additional components, especially the keypad, a nice addition to any installation. In the TBM there is a 15-inch center mounted MFD and dual PFDs. The huge MFD not only allows the pilot to see a lot of information, but it also allows for a big map along with engine instruments. On the TBM 850, as is the case on many other Garmin-equipped turbine airplanes, the crew alerting system (CAS) is handled through the displays, so you don’t have to monitor a Christmas tree full of warning lights. There’s a master warning light and a master caution, and that’s it. Everything else on the CAS resides in the displays.
850 versus 700
The introduction of the TBM 850 in 2006 took an arguably great airplane and made it even better, thanks to the addition of power, which always seems to do nice things for airplanes. The additional oomph came with the change to the Pratt & Whitney PT-6A-66D, which is limited to 700 shp for takeoff and landing but which can be asked to produce up to 850 shp for cruise. The result is an airplane that went from around 285 knots true to around 320 knots true, a huge increase in speed, while keeping the range about the same, at around 1,500 nm, as in previous TBMs, even though it burns a couple more gallons per hour than the 700. In case you were wondering, Daher-Socata uses gallons per hour for the 850, instead of pounds per hour, which is the more typical unit of measure in turbine airplanes.
In addition to the extra speed, the 850 also got a weight increase, up to 7,430 pounds maximum ramp weight, an increase of better than 800 pounds over the B-model. (The increase was first added to the C-model.) The additional weight meant that the company needed to get an increase in landing speed, up to 65 knots from 61, which it did without a stick pusher by earning credit for more crashworthy seats and better belts, among other measures. As fuel burns off and the weight comes down over the course of the trip, the stall speed comes down too, of course.
Besides the additional power, there are only very subtle outward differences between the 700 and the 850. The latter, by the way, is officially a 700 too, the 700N. The 850 designation is a marketing name. I guess the company wanted to make it clear that 850 was the superlative horsepower figure. I’d want prospective customers to know that too.
Up at cruise, when you want to “shift” from 700 to 850 hp, you do it in an ingenious way. The additional power is accessed via a detent built right into the flap lever. It is located one notch above the zero flap setting, so you physically can’t have any flaps and increased power. If you haven’t already returned to normal output when you bring in landing flaps, you have to do it then. It’s a fail-safe solution.
Flying High, Flying Fast
Cleared for takeoff by the Peachtree tower, I rolled out to the centerline of Runway 20L, held the brakes, brought in the power to just under 100 percent and let it run. With 700 hp available for takeoff, the 850 is clearly a powerful airplane, and it accelerates briskly but predictably. I rotated at 80 knots, let it accelerate, raised the gear, then flaps and started our climb.
We were in the soup a few seconds later and getting bounced around a bit. Hand-flying the airplane with the flight director, it was clear to me that this was no lightweight — our takeoff weight that day was around 7,000 pounds, more than 400 pounds below our maximum but still a thousand pounds heavier than a fully laden Eclipse jet. The yokes in the TBM give you a great deal of leverage, and the trim, while not lightning-quick, got the job done. Before I knew it, I had
it trimmed up for our quick 2,000-foot climb to our initial altitude of 3,000 feet.
Under the shelf of the Class Bravo, I had to pull power back — my right-seater, Daher-Socata’s Mike Sarsfield, correctly informed me from experience that 80 percent power would give me right around 200 knots, and it did.
Takeoff out of Peachtree was in our southerly direction of flight, but as is the case with some busy reliever airports around the country, a climb directly to our requested altitude of 28,000 was simply not in the cards. The controller gave us 3,000 feet and we just kind of stayed there, occasionally getting a vector five degrees this way or five degrees that way but never getting higher. I asked Mike how long they were going to keep us down here. He replied, “It will seem like forever.”
“Forever” finally passed, and we were cleared in quick steps up to 260 and then, after a bit, to 280.
The wind wasn’t much help, 45 knots almost directly across the bow, a fact that still left us with better than 315 knots groundspeed. It would be a quick two hours en route while using right around 120 gallons of jet-A.
Arrival
As we passed Ormond Beach, Florida, along the Atlantic coast, ATC started descending us. The vertical navigation capabilities of the G1000 make descent planning almost embarrassingly easy. Set in the desired altitude next to the waypoint, hit vertical nav, check to make sure the map shows your top of descent point (TOD), and you’re good to go. Descending is fast, which is nice. With a Vmo of 270 knots, much higher than most of the competition, you can stay fast all the way down and get to your destination sooner. The speed limit below 10,000 feet is 250 knots, so you do need to be aware of that restriction.
By the time we were in the terminal area, we were still fairly high, though descending in a pressurized airplane is a piece of cake compared with doing so in a nonpressurized model. The human ear can take only so much pressure change so fast. I was, I admit, a little nervous about landing a big turboprop, single or not, on a 3,255-foot-long runway, but Mike was so sanguine about the prospects, I figured he knew something I didn’t.
There are no speedbrakes on the 850, but the flaps and gear come in at 178 indicated, so there’s no real need. Mike counseled 85 to 90 on final, which you can do with a pronounced nose-down attitude, unlike on the Cirrus I regularly fly. The big prop on the Pratt is the world’s best speedbrake.
Another pertinent figure is 3,255, the length in feet of Runway 9 Right at North Perry.
With Runway 9R being the longest of four runways, they don’t get a lot of jet traffic at North Perry. The airport is home to a lot of Piper and Cessna singles, a few banner towing operations and a couple of flight schools.
Strangely enough, it’s also home to Daher-Socata North America, and a busy sales and service center. How many thousands of landings at North Perry TBMs have made over the years I can only begin to guess. It is an airplane, a 315-plus knot airplane, I might add, that feels right at home here.
As has been written countless times, you flare lower than you think you should. I was about 10 feet high but had a little residual speed. It was a firm arrival, nothing to write home about. A little beta, another huge advantage of the prop, and we were down and stopped with plenty of runway to spare without any brakes at all. It was immediately clear to me just how suitable cozy little North Perry is for the TBM.
VLJ Versus TBM
It’s a little hard to compare the TBM 850 with any other airplane. In the market, it competes with the Cessna Citation Mustang and the Embraer Phenom 100, though both of those airplanes are twinjets, require type ratings and, while inexpensive to operate in jet terms, cost more per hour than the TBM. They’re both faster too, and they both fly higher than the 31,000-foot ceiling of the 850. The Eclipse is a strong competitor to the 850, though it is not yet back in production. A more apt comparison might be with
single-engine jets, though, again, there aren’t any that have yet achieved certification. Once it’s on the market, the Piper Altaire might be a strong competitor, though turboprops have notable advantages over jets at altitudes below 30,000 feet.
Then again, the TBM might survive just fine, just as the Beech King Air has outlived by several decades predictions of its imminent demise. Besides enjoying low hourly operating costs, projected at just $450 per hour by Daher-Socata, the TBM 850 is an easy airplane to transition into. Sarsfield told me that the typical customer is a Cirrus or Meridian owner who wants to step up to a faster airplane that is still within his or her comfort level. The TBM fits that bill perfectly. A typical transition time is 15 to 25 hours, though some pilots, he said, are ready to fly themselves well before that.
Daher-Socata has worked to eliminate one big qualm that some prospects have, the lack of a potty. The company has introduced an optional potty, complete with privacy curtains, that replaces one of the rear-facing seats.
Sarsfield emphasized that once pilots get a TBM, despite it being “just” a turboprop single, they stop flying on the airlines.
“Even on a transcontinental trip,” he said, “door to door the TBM wins nearly every time.”
And this is coming from a guy who once flew nonstop from San Diego to Atlanta in an 850.
Trials and Triumph
After 21 years and nearly 550 TBMs, the airplane has approached what seems to be an extremely mature state.
The early reception was tepid at best, though not through any fault of the airplane. At the time there wasn’t any competition in the pressurized turboprop niche — the Pilatus PC-12 would come around a few years later and, if anything, help validate the concept. For several years the company built only a relative handful of airplanes before the market caught on. Ever since the mid-’90s, TBMs have been rolling off the production line at Tarbes at the rate of between 35 and 45 a year, with the high water mark being 85 a few years back, a rate of production that, de Villiers told me, took a tremendous investment to achieve. Even with the recession, the TBM has continued to sell well. Last year Daher-Socata sold 35 TBM 850s. At just over $3 million a copy, it’s a profitable business.
Thanks to advances in technology, the airplane will get better — this we know from experience — but that’s an article of faith: While you’re flying the TBM 850, it’s hard to focus on anything but the

Pilot Report: Daher Socata TBM 900
A 325-kt cruise speed may seem slow by light jet standards, but it’s pretty impressive when the aircraft you’re flying only is burning 400 lb. per hour. Daher-Socata’s TBM 900, the latest iteration of the TBM 700, is at least 14 kt faster than TBM 850, based on our flying both aircraft back-to-back. It also needs less runway and climbs faster, plus it uses less fuel and is quieter both inside and outside.
Last Thursday, we strapped into the left seat of TBM 900 S/N 1014 with Daher-Socata’s chief pilot Stéphane Jacques at the firm’s plant in Tarbes, France, for a two-hour evaluation of the myriad improvements wrapped into the new model. The preflight walk-around revealed much about what makes the aircraft faster and quieter than its predecessor. Most obvious are the aircraft’s new composite Hartzell five-blade prop and winglets.
The Hartzell five-blade incorporates the latest 3-D aero computer modeling, one that analyzes the airflow of the prop around the nose of the aircraft. Socata officials say they looked closely at an advanced prop from MT-Propeller but opted for the Hartzell because the aircraft cruises 3 to 5 kt faster.
The winglets were designed in-house at Socata. Their principal benefit is drag reduction at the higher angles of attack encountered during takeoff and climb. They also were added for aesthetic value.
On close inspection, it’s apparent that dozens of subtle drag-reducing mods were made to TBM 900, including adding inner main landing gear doors, recontouring the tail cone and reshaping the engine nacelle. A small, sharp strake, ahead and below of the left wing leading edge, helps tame the entertaining, if not colorful, stall characteristics of earlier TBM models.
It’s tougher to spot the changes made to the engine air inlet, plenum and exhaust stacks. Socata’s aero engineers undertook the industry’s first full-scale CFD analysis of a PT6A engine inlet. They optimized the size and shape of the opening and internal contours to increase ram recovery and thus boost available torque. The exhaust stacks were reshaped to increase thrust output and to reduce aft-section airflow stagnation that caused much of the soot accumulation on the sides of the nacelle and fuselage.
TBM900 doesn’t have a 700-shp limitation for takeoff, as did all previous TBM models. All 850 shp from its Pratt & Whitney Canada PT6A-66Ds are available all the time, subject to ITT limits. The additional 150 shp, combined with TBM900’s more efficient air inlet, reduces takeoff distances over a 50-ft. obstacle by as much as 23%. Initial climb gradient and time to climb to FL310 also are improved because the improved air inlet ram recovery enables the engine to produce rated power at lower ITTs.
Several ergonomic improvements have been made to the cockpit. It’s simpler, and functions are more automated. A new single power lever, mainly designed by Capt. Jacques, integrates the power, prop and condition lever controls. The power lever has moves through h-pattern gates, not unlike an auto’s manual gearshift lever. The right side of the h has idle-cutoff, low-idle and high-idle positions.
During the start sequence and at low idle, bleed air automatically is shut off to prevent thermal stress on the engine. Moving the power lever to the left side of the h provides normal-range power control and prop-reverse functions.
TBM900 has automatic torque limiting, so it offers “set and forget” power management for takeoff and initial climb. The upgrade is most appreciated by pilots because precise high-power setting of a PT6A can be challenging of ram recovery with speed change and use of the inertia separator. The torque-limiting function, though, is no substitute for a FADEC.
The cockpit has many other detail improvements. The avionics switch on the overhead panel, for instance, has been eliminated. Changes to electrical load distribution allow the Garmin G1000 avionics system to be powered up as soon as the battery is switched on, with minimal battery drain. The engine-start switch has been changed to a solenoid design that automatically pops back to “off” once the start cycle is complete.
Version 14.01 software for G1000 upgrades the displays with an ISA temperature deviation indication, integrates weather radar with the MFD map and provides automatic landing field elevation inputs to the pressurization controller, among dozens of other small changes.
Takeoff weight at Tarbes was 7,100 lb. and we taxied to Runway 02. Computed takeoff distance for TBM900 was 2,450 ft. compared to nearly 3,100 ft. for TBM850. Setting 100% power was easy because of auto torque limiting. The prop stabilized at 2,020 rpm; we accelerated and rotated at 85 KIAS. After gear and flap retraction, we settled into a 170-KIAS climb. Passing through FL210, we transitioned to a 0.40 indicated Mach climb, reaching FL310 in 20 minutes, 4 minutes later than the book predicted because of warmer-than-ISA OAT and some vectoring for air traffic control.
At FL310, the aircraft, then at a weight of 6,940 lb. and in ISA-1C conditions, settled into a 325-KTAS cruise while burning 400 lb. per hour [pph]. The pilot’s operating handbook predicted 324 KTAS and 384 pph.
Down at FL280 and at a weight of 6,860 lb., the speed was the same, but fuel flow increased to 440 pph. The PIH predicted 327 kt and 429 pph. The airplane actually will cruise as fast as 330 KTAS at FL280, but only at a svelte 5,500-lb. gross weight.
At both cruise altitudes, we found the cabin to be noticeably quieter than that of TBM850 because of the new five-blade Hartzell prop. Vibration levels also are appreciably lower because the engine is more isolated from the airframe. The new air inlet and engine, for instance, are separated by a soft sealing gasket.
Next we descended to 11,000 ft. for a stall series. In the clean configuration, stall break occurred at 78 KIAS with a pronounced but controllable wing drop. Stalling with gear and flaps extended at 63 KIAS, wing drop was gentle and easy to correct. Setting 77% torque in the clean configuration, we gradually increased pitch to 31-deg. nose up. Stall occurred at about 60 KIAS with a sharp wing roll off to 30 deg.
During all three maneuvers, stall recovery was immediate when we crisply reduced angle of attack. Then we headed back to Tarbes.
Crossing the field at 11,000 ft., Jacques next demonstrated an inflight engine shutdown and relight. In preparation, we extended the landing gear over the runway and stabilized the aircraft at 120 kt at idle thrust. Jacques then shut down the engine. Even with gear down, the aircraft has an excellent power-off glide ratio, providing confidence that we could have executed a power-off landing after spiraling down to the runway.
We restarted the engine and returned to Runway 20 for two landings. Our first approach was an ILS to a touch-and-go. Over the runway, we flared a bit high and settled onto the pavement with no grades for style. During the second approach, we flared close the runway and touched down more smoothly.
Conclusions after the two-hour mission? With its greater speed, TBM900 more effectively competes against light jets. It’s actually faster on a 600-nm mission and it burns 26% less fuel than the Cessna Citation Mustang, according to B&CA’s May 2014 Purchase Planning Handbook. Unlike light jets, TBM900 offers full-tanks and full-seats loading flexibility. It can fly between Geneva and Moscow; Athens and Le Bourget; or Shannon, Ireland, and Helsinki.
Admittedly, TBM900 lacks twin turbine redundancy, but during the past 40 years the PT6A has proven to be one of business aviation’s most reliable powerplants. Daher-Socata plans to build 50 TBM900 aircraft in 2014, and it has buyers for virtually all of them.

Flight Test: Citation Mustang
Pilot Web goes into extreme detail the specifications of the Cessna Citation Mustang and how it may be the best business jet. The article begins with a short history of Cessna Aviation and the first production jet then proceeds to give a thorough analysis of the Mustang. Going further in depth than many other articles on the use of the aircraft in a business setting and the capabilities for users and their storage.

Hello TBM 900
The TBM series of turboprop singles has proven a winner in the marketplace, with more than 684 sales since deliveries began in late 1990. Part of the reason for this success has been a pattern of constant design evolution. First came the “small door” TBM 700s with 700-shaft- horsepower Pratt & Whitney engines, then the “big door” TBM 700C2 variants with higher max takeoff weights, then the 850-shaft-horsepower TBM 850, followed by the Garmin G1000-equipped TBM 850s. But the newest in the TBM series represents more of a revolutionary overhaul of the TBM idea. It’s the brand-new TBM 900.
No, the new airplane doesn’t have a 900-shaft-horsepower PT6A engine— but it might as well, thanks to changes in several key design areas. “We’ve calculated that the TBM 850 would need to have a 934-shaft-horsepower engine in order to realize the performance we’re seeing in the TBM 900,” said Nicolas Chabbert, senior vice president of Daher-Socata’s Airplane Business Unit.
Simply put, the TBM 900 is the fastest, most economical TBM to date, with maximum cruise speeds of 330 to 335 knots (compared to the TBM 850’s advertised 320 knots), the shortest takeoff distances in the fleet (2,380 feet under ISA conditions, a 16-percent reduction over the TBM 850), the fastest times to climb (17 minutes to FL310, a 14-percent improvement over the TBM 850), and the longest ranges (1,582 nm with NBAA IFR reserves; 1,730 nm with 45-minute standard IFR reserves—eight- and nine-percent improvements over the TBM 850, respectively). As for summertime hot-and-high takeoffs at Aspen-like elevations, the 900 consumes 3,940 feet to 50 feet in ISA +30 temperatures—a 21-percent improvement over the 850. And all of this while using the same 850-shaft-horsepower PT6A-66D engine as its predecessor. “We were hoping to gain 12 knots when we began work on the TBM 900 project,” Chabbert said of the 900’s cruise speeds. “But instead we got almost a 20-knot boost.”
Aerodynamic cleanups
When the original TBM 700 was designed in the late 1980s, engineers used “classical design” techniques, according to Raphel Maitre, deputy vice president of the Socata Airplane Division. These were general aviation’s pre-computer assisted design (CAD) days, when light airplane manufacturers simply built what they thought were sleek and efficient airplanes—even though they often weren’t. Engineers didn’t know where they got things right, and where they blew it, so to speak. It takes a thorough examination under the unforgiving eye of computational fluid dynamics (CFD) to understand airflows, critically examine initial assumptions, and come up with solutions. Four years ago, that’s what Daher-Socata did with the TBM 850. It generated a numerical model of the airplane and let a CFD program called Fluent do the work. The result? “Let’s face it, the TBM was not an optimized design,” Chabbert said.
One big trouble area took in the propeller, cowling, engine air intake, and induction air plenum. The propeller disc was too far away from the air intake, which itself was too narrow and circular. This made for a lot of drag at the cowl and air intake leading edges, and created turbulent airflow within the induction plenum. The drag penalty? Six knots. On top of that, the exhaust stacks were angled too sharply, and this created turbulent flow within the exhaust stream, causing another one to two knots’ worth of drag. In plain language, the 850’s engine wasn’t breathing as well as it could.
For the 900, a new, swept, five-blade carbon fiber Hartzell propeller is used for more takeoff thrust, but it’s also set to within two inches of the pitot-style air intake (the 850 propeller is about six inches from the intake), which is slightly narrower, wider, and canted at a slight angle compared to the 850. Now the propeller pulses are treated symmetrically within the induction plumbing, and yield a smooth flow into the engine. The 900’s exhaust stacks have more rounded bends, a change that not only eliminated drag, but also added what amounts to 50 horsepowers’ worth of “free thrust,” according to Daher-Socata. Another three knots were picked up by removing the old-style inboard main landing gear doors.
Although the new propeller helps takeoff and initial climb performance, more available horsepower is the real hero in these phases of flight. TBM 850 pilots know that when moving the flap switch to the 10-degree takeoff position, a torque limiter kicks in that restricts power to 700 shaft horsepower; it’s only after you’ve fully retracted the flaps that all 850 shaft horsepower are available. With the 900, all 850 shaft horsepower are on tap, thanks to tests that confirmed better low-speed roll authority granted by the 900’s winglets, another change incorporated in the new TBM design. Directional stability is enhanced by a new, larger dorsal fin. Incidentally, the 900 will continue to produce 850 shaft horsepower all the way to 28,000 feet. The TBM 850 begins to peter out at 26,000 feet.
Front office changes
The TBM 900 was first revealed to AOPA Pilot in a February 12 visit to the TBM factory in Tarbes, France. There, an evaluation flight demonstrated not just the performance boost, but some major changes in the cockpit and aircraft systems as well.
Daher-Socata chief experimental test pilot Stephane Jacques was our minder and demonstration pilot for the flight, and there was a lot to see. Complaints about access to the front seats were fixed by narrowing the pilot seats, shortening the center console, and rounding its corners at floor level. Now it’s much easier to make a graceful entrance from the cabin. The forward pilot entry door, which used to be optional in previous models, is now standard.
The start sequence is easier, too. A new, 300-amp starter generator (up from prior 200-amp units) and an automatic switch from starter to generator function at 50-percent NG makes for faster starts with less workload. To start, just turn the overhead start switch On, wait for 13-percent NG, and move the single power lever into the low-idle position. After that, within 28 seconds the starter cuts out, and by 40 seconds ITT has stabilized and the start is complete. Battery starts on previous TBMs could take twice as long. By the way, a new GPU system lets you not only make assisted starts, but allows the power cart to charge the battery in case it’s depleted.
The TBM 900 has a single lever that incorporates both power- and condition-lever functions. Don’t look for a propeller control because none exists. The single lever rides in a lower-case “H”-shape gate system. The right side of the “H” controls the condition lever actions, so for a start you lift the lever and move it up and into the first detent to introduce fuel and put the engine into low idle. Move it forward once more and you’re in high idle. To operate it as a conventional power lever, move it to the left and into the run for calling up forward thrust, beta, and reverse-thrust functions.
Gone is the old propeller governing system, so don’t look for that little bump on the cowl that faired the old-style governor. The 900 uses mechanical stops to prevent prop overspeeds, and an electrical governor made by Czech manufacturer Jihostroj to keep rpm between 1,950 and 2,040. This means there’s but one prop setting, always kept very close to the 2,000 rpm redline—and thus no need to manually adjust the propeller. It’s all automatic, and all fail-safe. If there’s an electrical problem, the propeller continues to govern. If for some reason it begins to inadvertently feather, pulling the prop circuit breaker restores normal governing.
The most obvious cockpit improvement must certainly be the new control yokes. They’re both beefy and ergonomically correct, with seven switches and a recessed area that acts as a thumbrest. Customers complained about the clunky-looking old yokes, and Daher-Socata listened.
There are new landing gear, pressurization, and alternator systems as well. The landing gear lever illuminates when the hydraulic pump is running, and when the gear fail to extend. Pressurization is all automatic, and only requires entering the destination airport’s elevation—which can be called up automatically when
the destination is entered on the MFD’s flight plan page. Also new is a 100-amp standby generator.
In flight
We lined up on the Tarbes-Lourdes-Pyrenees’ airport’s Runway 2, pushed up the power, and soon were at the 85-knot rotation speed. Seconds later we were in a 170-knot climb doing 1,700 feet per minute. We were held at 5,000 feet, then 8,000 feet during the climb, but we were still climbing at 400 fpm by the time we approached FL310, 20 minutes later. (The POH said we’d get there in 17 minutes.)
Up at FL310—the 900’s maximum operating altitude—we set torque at the top of the white carat on the torquemeter for a maximum cruise power setting and saw a 327-knot true airspeed while burning 60 gph in -54 degree Celsius (ISA -10) conditions. A glance at the G1000 multifunction display’s map page showed that we could continue cruising for three hours, 10 minutes. At a long-range cruise setting we cruised at 262 knots and fuel burn went down to 39 gallons per hour. Daher-Socata’s TBM factory is at the Tarbes airport in the far southwest of France, very near the Pyrenees Mountains. At this power setting the MFD’s range ring put our 45-minute reserve range well to the north of Scotland—and that was with a 30-knot headwind.
A descent to level off at FL290 gave us the best cruise speed at our near-ISA temperature conditions and our weight of 7,050 pounds (maximum takeoff weight is 7,394 pounds). At 100-percent torque we saw 330 knots on 65 gph. We’d been flying for 38 minutes at this point, but we still had a 1,000-nm range according to the G1000.
An emergency descent demonstration to 10,000 feet pegged the vertical velocity indicator past its 6,600-fpm limit, but the automatic pressurization kept the cabin in control by keeping its descent to 830 fpm.
Then it was time for some stalls. There was an approach to landing stall, which produced plenty of buffeting as a warning, but no tendency to drop off on a wing; same deal with departure stalls. Then Jacques demonstrated the sorts of aggressive stalls he’d performed during certification flight testing. To the tune of 40 degrees, up, up, up the nose went until an abrupt stall caused the left wing to start a drop. But Jacques showed there was still aileron control. He countered the rolloff with full opposite aileron and the airplane hung there with wings level—thanks, he said, to the stabilizing effect of the winglets.
Back at Tarbes we flew an ILS using 25-percent torque, 10 degrees of flaps, and gear down and full flaps at one dot above the glideslope. The result was a very stable 85-knot trip down the final approach course. There is the impression of being nose-low on short final, but it’s best to resist the temptation to flare too soon. Save that for the last 20 or so feet of altitude; go to idle thrust, hold the nose off, and you’ll see that the 900 can indeed make nice landings—even though some say the landing gear can make for some hard arrivals on occasion. Once the nosewheel settles to the runway, pull a gob of reverse thrust, apply brakes, and chances are you’ll stop in well under 1,000 feet. The POH said our ground roll distance that day would be 1,200 feet, but that’s without reverse thrust.
A new commitment
In 2009 French industrial conglomerate Daher bought a controlling interest in what was then EADS-Socata, the manufacturer of the TBM (and before that, a line of piston singles). The TBM 900 is the first airplane to be certified under the new ownership, and proof that Daher is as enthusiastic about building airplanes as Socata was.
For the past four years a team of 75 employees at the Tarbes facility has been working in secrecy on the TBM 900, under the “Century” project name. The team was fixated on product improvement, knew that the TBM was a good design, but also knew that unless they made it better the market would not tolerate any deficiencies, real or perceived. “That’s why we invested so heavily—even though it was the worst of economic times,” Chabbert said.
The investment seems to be paying off. At a customer meeting in March, Daher-Socata said orders for 10 TBM 900s were placed, sight unseen. Ditto 30 more orders by distributors convinced that the customer base would respond. That’s 40 orders—the same number of TBM 850s sold in all of 2013. The 900 is priced at $3.711 million.
At the factory, production of TBM 850s was stopped at serial number 684. From now on, the TBM 900 is the future of Daher-Socata’s airplane business unit, and things are looking up. When we left Tarbes, four TBM 900s were on the ramp and eight more were on the line. And the airplane had not yet been announced to the public.
Email tom.horne@aopa.org
Photography courtesy of Daher-Socata
Spec Sheet
Daher-Socata TBM 900
standard equipped price: $3.71 million
Specifications
Powerplant | Pratt & Whitney PT6A-66D, 850 shp
Propeller | Hartzell HCE5N 3CX7, swept 5-blade, 91-in diameterWingspan | 42 ft 1 in
Wing loading | 38.2 lb/sq ft
Power loading | 8.7 lb/hp
Height | 14 ft 4 in
Length | 35 ft 2 in
Seats | 6
Basic empty weight | 4,573 lb
Max ramp weight | 7,430 lb
Max takeoff weight | 7,394 lb
Max payload | 1,376 lb
Max payload w/full fuel | 720 lb
Max zero fuel weight | 6,032 lb
Max landing weight | 7,024 lb
Usable fuel | 1,956 lb/292 gal
Performance
Takeoff distance over 50-ft obstacle | 2,380 ft
Max cruise speed/fuel burn/range w/45-min reserve, 28,000 ft 330 KTAS, 64 gph, 1,410 nm
Long range cruise speed/fuel burn, range w/45-min reserve, 31,000 ft
290 KTAS, 35 gph, 1,585 nm
250 KTAS, 30 gph, 1,730 nm
Max operating altitude | 31,000 ft
Landing distance over 50-ft obstacle | 2,430 ft
Landing distance, ground roll, no reverse thrust | 1,840 ft
Limiting and recommended airspeeds
VA (design maneuvering) | 158 KIAS
VFE (max flap extended), Takeoff setting | 178 KIAS
Landing setting | 122 KIAS
VLE (max gear extended) | 178 KIAS
VLO (max gear operating)
Extend | 178 KIAS
Retract | 150 KIAS
VMO (max operating speed) | 266 KIAS
For more information contact Socata North America, Inc., North Perry Airport, 7501 South Airport Road, Pembroke Pines Florida 33023; 954-893-1400; www.tbm900.co
All specifications are based on manufacturer’s calculations. All performance figures are based on standard day, standard atmosphere, sea level, gross weight conditions unless otherwise noted.
Extra: The TBM 900 is seven knots faster at FL310 than the TBM 850 is at its fastest altitude—FL260.

TBM 850 is Even Faster
The TBM 700 could bump up against 300 knots true airspeed at standard air temperature in the mid-20 altitudes, but when cruising at the more fuel-efficient altitudes near the airplane's 31,000-foot ceiling, the speed dropped down to about 250 to 260 knots. The new 850 can top 300 knots at any weight, hit 320 knots at optimum altitude and maximum weight, and can come close to 320 knots true at its ceiling at typical cruise weight. The key to the speed increase is a new version of the Pratt & Whitney turboprop engine, and a different way of tapping bleed air for pressurization. The new 850 uses the PT6A-66D engine, which is capable of producing 1,825 shp at sea level. The engine is in the same family of PT6 engines used on the big Beech 1900 regional airliners and the new speedy Piaggio Avanti twin turboprop pusher. The PT6A-64 that powers the TBM 700 can generate 1,580 shp at sea level, so you can see the size of the potential power increase.
A turboprop engine, like any engine, is nothing more than an air pump. The greater mass of air that an engine can compress and burn, the more power it makes. As air density thins at altitude, the engine has less mass of air to work withand power output drops. That's why so many turbine engines are flat rated, meaning that they can make much more power at sea level than the airplane can use. But you need to start with a reserve of power potential to have the power you want left up high for cruise. And the new TBM 850 has a bigger flat rating margin than any other airplane I can think of. The 850 at sea level has more than double the power potential available than it will use for takeoff and initial climb.
But the engineers at Pratt and TBM worked even more magic to obtain additional power and efficiency at cruise by modifying the engine-bleed air system that pressurizes the cabin. As in many large jets, the new 850 has a dual-bleed air tap that provides a reliable and steady source of pressurization at all power settings at any altitude in the operating envelope.
To pressurize the cabin in a turbine-powered airplane, engineers tap high-pressure air from the engine compressor section before the air enters the combustion chamber. This is called "bleeding" air, and it's an accurate description because the high-pressure air that goes to the cabin doesn't go to the engine burner section, so less power is produced. The engine is literally bled of power.
The new Dash 66D engine in the 850 has four stages of axial compressors plus a final stage of centrifugal compression. Obviously, the pressure is increased by each stage of the process. When the engine is operating at cruise power, only a small portion of the compressed air must be bled to maintain the 6.2 psi cabin pressure and keep the TBM cabin pumped up. But, the rules require-and every pilot would want-that the cabin pressure must be maintained when the engine power is low. In other words, you must be able to chop the power at the certified ceiling without the cabin altitude climbing. To meet that requirement, the TBM 700 tapped bleed air from a higher pressure section of the compressor than was needed for normal cruise and descent and that used more engine power. The new 850 has two engine-bleed taps to satisfy normal cruise power pressurization and the low power high-altitude condition.
When the 850 is operating at any typical cruise power setting all the way up to the 31,000-foot ceiling, the new bleed air system taps a lower pressure section of the engine compressor, which robs less power from the engine. If the pilot wants to make a rapid descent from high altitude and reduces power to at or near idle, a system of valves move and tap bleed air from a higher pressure section of the engine compressor and the cabin stays pumped up and nobody's ears pop. TBM pilots can select to use the high-pressure bleed air continuously and give up the extra power, but the automatic mode is the norm, and will be used except in abnormal conditions. As I said, this is a typical pressurization bleed system in many jets, but is a new level of sophistication in this class of airplane, and for the price of some additional plumbing and valves, increases high-altitude cruise for almost no more fuel burn.
Since the design objective for the 850 was to increase high-altitude cruise speed, and everybody was pretty happy with the TBM's takeoff and initial climb performance, the decision was made to keep takeoff and initial climb power at 700 shp. The 850 weighs the same as the 700, which can use runways of 3,000 feet, so the decision makes sense. The 850 also retains the 700's torque limiting system during takeoff and normal airport maneuvering, which protects the engine and reduces pilot workload.
The flap selector in the 850 has a new, fourth position. It retains the flaps up, takeoff, approach and landing positions of the 700, but when you move the selector to the new detent beyond flaps up, the torque limiting system is disengaged and the full power of the new engine is available for climb and cruise. In this mode the pilot must observe torque limits by restricting power lever movements, but this mode is the normal mode in nearly all other PT6-powered airplanes.
I had a chance to fly the first TBM 850 off the production line at the company's U.S. headquarters in North Hollywood, Florida. No matter how closely I looked, I couldn't spot an external difference between the 850 and 700s that were parked nearby. The reason is that there aren't any, except for the most subtle reshape of the exhaust stacks on the new engine. When you open the cowling you can see the second shiny bleed air pipe for the dual tap system, but that's about it for external differences. The 850 weighs about 20 pounds more empty than the 700C2 that it supersedes, and most of that weight is accounted for by the pipes and valves of the new bleed air system.
The new TBM 850, like the 700, is a very complete airplane as standard. The dual Garmin GNS 530 GPS/flight management systems are standard, as is the electronic flight instrument system (EFIS) from Bendix/King. Pilots can choose XM Weather or the Bendix/King system to deliver weather to the cockpit. Everything else you need, including the equipment for reduced vertical separation minimums (RVSM) to fly above 28,000 feet, is available. The one major airframe option is a crew door that allows the pilots to enter ahead of the wing after passengers have been loaded and the huge main cabin door closed. This has become a popular option, though if it were my airplane, I would leave it off. The TBM cabin is large enough to climb into the pilot seats from the main cabin without unusual gymnastic ability. The cockpit space and room to maneuver is certainly on par with existing light jets.
The TBM cockpit has a big airplane feel about it, as you would expect from a company whose parent is part of the group that builds the Airbus. The systems are of modern design, which means they have a high level of automation. There is little to system management in flight, except to make sure you have the necessary fuel onboard. The fuel selector is also automated and a big knob rotates from one tank to the other on its own, to maintain fuel balance. The TBM is, obviously, a single-engine airplane and that means it must stall at 61 knots or less at maximum weight, and has demonstrated that after one turn with pro spin controls applied, the airplane recovers in less than an additional turn even at extremes of weight and CG location.
Since the TBM was designed from scratch to be a single-engine turboprop, engineers knew they would need the most effective wing flap possible to meet the stall requirements. The long span Fowler flap covers most of the trailing edge of the wing, leaving only a little room for ailerons. To augment the authority of the small ailerons, the TBM has roll spoilers that extend after the aileron travels several degrees up to initiate the bank. Spoiler augmentation of roll control is common on larger jets for many of the same reasons. But unlike most jets, the roll control system on the TBM is entirely mechanical, operating by cables, pushrods and bell cranks. The control system is extremely smooth and has very little friction.
In late 2002 the TBM engineers demonstrated to the FAA that new 20G crashworthy seats and other modifications delivered the equivalent level of safety as the 61-knot stall speed limit at a 65-knot stall at maximum takeoff weight. The FAA approved the new stall speed, which allowed an 816-pound takeoff weight increase in the 700C2 model that carries over to the new 850. As soon as fuel burns off, the TBM maximum stall speed will decrease and be below 61 knots for most of a typical flight, so the equivalent safety finding covers only a small worst-case corner of the envelope.
Another unusual design feature of the TBM is its very high single value Vmo (velocity maximum operating) of 270 knots. Vmo, unlike the red-line limit of Vne (velocity never exceed) in a piston airplane, accounts for the effects of Mach at higher altitudes as well as the structural loads that increase with indicated airspeed. Mach effects include change in flying qualities and loads on the airframe. Air flowing over the wings and tail can approach Mach 1, the speed of sound, when the airplane itself is moving through the air at far less than that speed. For example, the air must accelerate so abruptly to pass over and under a thick wing section that a Mach shockwave can be created and change the performance of the wing or tail when true Mach is quite low.
Mach effects change with air density, becoming more critical as atmospheric density decreases with altitude. For that reason, nearly all turbprop airplanes adjust Vmo down as altitude increases, thus delivering a larger margin away from the detrimental effects of Mach as the airplane climbs. The creators of the TBM took a different tack and designed in enough airframe strength and flying qualities margin that the airplane exceeds all standards at 270 knots indicated airspeed at any altitude up to its 31,000-foot ceiling. The single red line Vmo of the TBM reflects both exceptional airframe strength, and very predictable and benign flying qualities at all altitudes. While some turboprops are limited by their Vmo at high altitude, the TBM never is. That is especially important on descent, where you can shove the nose over in the TBM on descent and gain back some of the time spent in climb by coming down at a very high true airspeed without a reduce red-line limitation.
Whenever I have flown the TBM I am always impressed by the low pilot workload on takeoff and initial climb. The engine has been so expertly positioned that there is very little of the torque effects to compensate for that you would expect in such a powerful single. There is a rudder trim rocker switch under your thumb on the control wheel that you use to set the trim in the takeoff "pie" on the indicator. With rudder trim properly set, directional control on takeoff is as easy as in other singles that have a fraction of the power.
You will, however, use your thumb on the rudder trim rocker switch several times during a TBM trip. Changes in power, attitude and airspeed all require rudder trim adjustments. It's just the nature of a single-engine airplane and quickly becomes second nature.
Another initial impression in the TBM is of a great reserve of power, much like a jet. When you haul the nose up on rotation there is no need to reduce deck angle after liftoff. The TBM just keeps going up, with 130 knots yielding the maximum rate of climb. Some pilots object to the limited view over the nose, but I always think that with a climb rate well over 2,000 fpm I'm not going to hit anybody right under the nose, but need to be looking up where the airplane is aimed. The traffic advisory system also lets you know about traffic nearby.
With the flap selector moved to the new, high power detent, the PT6 was able to deliver full-rated power and, despite a brief level-off down low, the new 850 reached 28,000 feet in less than 18 minutes. At that level with maximum cruise power set, the true airspeed varied between 306 and 310 knots, though air temperature was almost 20° C above standard and we were at maximum weight. Fuel flow, which is displayed in gallons per hour, unusual for a turbine, was 58.5 gph. If temperature had been standard, the handbook shows a cruise speed of around 320 knots, or a little more as fuel burned off. Under standard conditions at mid-cruise weight, the 850 delivers 320-knot true airspeed at 26,000 feet, but slows only to 315 knots at the ceiling of 31,000 feet, so there is very little penalty to climb. Fuel flow, however, drops from 66.6 gph to 55.8 gph for those five knots of airspeed.
The people at TBM don't know why, but the new engine is much easier to manage in the pattern and on short final. In most PT6 installations, the power lever becomes very sensitive at the lower power settings used around the airport. At low power the propeller is operating close to flat pitch and a small reduction in power drives the prop flatter, creating a lot of drag and a sinking spell if you are not careful. But the new engine in the 850 doesn't seem to have this power sensitivity band. Power response to movements of the throttle remain linear all the way to touchdown, and I found it very easy to gradually reduce power into the landing flare without any abrupt change that could cause the airplane to drop in. There is, however, a powerful visual illusion because the nose is so long that the TBM is pointed way nose down on approach, creating the temptation to flare too high.
After a couple of landings youget the proper sight picture in mind and landings become easy and predictable.
An obvious question in view of the 850's typical $2.8 million price is: Why a turboprop single when light jets such as the Citation Mustang will cost nearly the same? The answer is because the TBM is not a jet, that's why. The new 850 delivers speed close to that of the proposed new light jets, and undoubtedly more range, with only a single engine. Insurance companies are comfortable with pilots moving into the TBM directly from piston singles. No type rating is required, and the TBM doesn't have the runway limitations imposed on jets. And at today's prices, fuel has become a cost issue in any airplane, and you can't beat the efficiency of a single.
The TBM is really a personal airplane designed for the owner pilot who wants to go fast over long distance while carrying few, if any, passengers. In this airplane the pilot and his companion are the payload. The cabin is plenty roomy and comfortable for two couples, though six fit fine for shorter trips, but this airplane is about owner pilots, not passengers.
Bottom line, nothing goes as fast and as far for the money as the TBM 850, and it is being delivered now, is well established in terms of maintenance and insurance, and is available to virtually any pilot with an instrument rating. The airplane hit its target out of the box as the ultimate personal airplane, and with the extra speed of the 850, it just keeps getting better.
Falling Fast
sidebar - by Dick Karl
I squirmed around in my seat to see the instantaneous vertical speed indicator declare 6,000 feet per minute. Down. Portions of the Florida landscape filled most of the windshield. Both the pilot and copilot remained calm. The center controller kept asking for us to say our altitude. "22,000," came the reply. About 30 seconds later the same controller made the same request. "17-five," came the response. The altimeter unwound like a dizzy clock in an old movie. Our rate of descent had paralyzed the center's computer. We were "coasting."
I was sitting in the sumptuous back-facing seats of a brand new TBM 850. In the front sat Mac McClellan of Flying and Alan Griffin, TBM's chief pilot. I was joining Mac on a visit to Socata in North Perry, near Fort Lauderdale. While I was falling out of the sky, I was falling for this machine, the new souped-up TBM.
We had started with some preflight explanations about the differences between the TBM 700 and the 850, most of which went over my head. Then four of us hopped into this speed demon for a test flight. Mac sat in the left seat. In the back I admired the opulent surroundings, noted the adequate headroom and thought of our Cheyenne, with its nice interior, turbine reliability, but 25-year-old systems. Though the TBM felt marginally smaller in the back, it was roomier up front. And it is impressively faster and more economical to operate.
I had long thought that a TBM would be the perfect airplane for me. Fast and efficient, it can easily carry four with luggage and go a very long way. With no business associates to transport, I don't need the size of a King Air. At more than 300 knots, a TBM is close to the projected speeds of most of the VLJs, burns less gas and has a greater range. Just what I need.
After we landed at Lakeland, Florida, I was offered a go at the left seat and I jumped at the chance. The feel on takeoff was different than our airplane. It had been a long time since I'd flown a single-engine airplane of any type and the TBM has a long snout with a lot of power in the front end of it. I squirreled down the runway and rotated at about 85 knots, got the yaw damper on, flaps up and inertial separator stowed just in time to see 1,500 feet go by on the altimeter.
We turned downwind. I say "we" because Alan was doing everything but the flying-and he was probably doing most of that, too. On base I deployed approach flaps and pointed the nose down as instructed. The view was alarming compared to the deck angle of our airplane. It looked like we were going straight down. Alan cautioned me not to flare too early and I rewarded his instruction by ignoring it. I just couldn't help leveling this multi-million dollar airplane approximately five feet off the ground, where I sat transfixed as I ran out of airspeed and ideas at the same instance. Whomp. Alan said something about TBM's certification process for testing the gear strength, but I didn't catch it as we were on the go again.
The next landing was marginally better. We followed that with a balked landing (easy, plenty of power and airspeed), then headed up to 17,500 feet for the VFR trip back to Fort Lauderdale. We climbed at 2,000 feet a minute, leveled off, and found ourselves devouring Florida farmland to the tune of 345 nautical miles per hour. The glass/electronics were superb and too soon we were started down with North Perry in sight. Though Runway 9R is only 3,000 feet long, we turned off easily on a taxiway before the end.
What to say about such an experience? I know of no other airplane with this combination of attributes and these are exactly the characteristics I long for. The interior is beautifully done, the airplane is fast-fast, and the fuel burn is amazing considering the performance. The easiest way to explain my feeling as I got out of the pilot door is to say this: I want one.

We Fly: Daher-Socata TBM 900
When French company Socata launched the single-engine turboprop TBM 700 with Mooney in 1989, many observers wondered if the airplane would ever be anything more than an aerial oddity. That’s before people began to operate it and realized the many benefits of having a single Pratt & Whitney PT6 up front. That first TBM was long on range and speed — around 290 knots at high cruise — and miserly on operating costs.
That formula hasn’t changed in the past 25 years, but the TBM has, going through as many as nine iterations (depending on how one counts the model changes) and improving with every one. Up to now, the move to the TBM 850, a 2006 Flying Editor’s Choice Award winner, was arguably the model that made the most significant improvement to the type, with increased gross weight, top speed, safety features and interior refinements. I flew the airplane a couple of years ago soon after it got its Garmin G1000 panel and was happy that we saw a high-cruise airspeed of around 315 knots at 28,000 feet. That’s fast for a single. Heck, it’s fast for just about any turboprop.
Article Continues Below:
Aerobatics with Matt Chapman at Oshkosh 2016
Flying magazine met up with airshow performer Matt Chapman in Oshkosh for ...
With the 850, a lot of folks might have concluded that the company, despite its top-notch aerodynamicists and engineers, had reached the design limit. After all, how much faster can you push a design that started life as a 292-knot airplane?
Apparently, a lot faster. Thanks to a host of ingenious improvements and technology advancements, the new TBM 900 can cruise at 28,000 feet under standard conditions at 330 knots. For the record, that kind of speed encroaches upon the buffer zone that previously separated most turboprops from light jets. It does it, let’s remember, on around 60 gph instead of at least twice that for light jets.
I’ve been doing a lot of TBM flying the past couple of months, first in a TBM 700 belonging to Hartzell Propeller, the company with the household name (at least in aviation households anyway) located in quiet Piqua, Ohio, that has become the most advanced propeller maker on the planet. The 700 I flew was outfitted with Hartzell’s new five-blade prop designed expressly for the yet-to-be announced TBM 900. The flight from sunny Austin, Texas, to snowy Piqua was great fun, and fast too. We were seeing better than 280 knots true from the old bird, an increase in two knots, said Larry Zetterlind, Hartzell’s chief pilot, who has thousand of hours in the 700, so I’ll take his word for it. Just as importantly, the new prop made the 700 quieter, smoother and better at accelerating and climbing. I’ll let our readers debate the looks of the new mill.
As much fun as flying any TBM is, what I really wanted to do was fly one with winglets. I got my chance a week after Sun ’n Fun down in south Florida at Daher-Socata North America’s headquarters at cozy North Perry Airport. Before I got to fly the 900, though, I had the blessing and the curse of having to/getting to photograph it on two air-to-air missions, one in the evening and one early the next morning. I say it was a blessing because the airplane is very pretty to look at, especially from my vantage point peering at it though the barn-door-size opening where the Piper Seneca’s back door usually resides, and I say curse because I had to watch someone else fly it that whole time instead of me.
The experience of flying the 900 really is noticeably better than flying the 850, and some of the 900’s enhancements come with the benefit of improved safety and utility. More dramatic are those improvements associated with performance. The 900 is faster, it’s more fuel efficient, it climbs better, it uses less runway both coming and going, and did I mention how pretty it is?
I’m not sure what new feature I noticed first on the 900, but it’s one of two things, the new five-blade prop or the winglets. Some airplanes when they get winglets look as though they had them tacked on like an aftermarket spoiler on a cheap car. The TBM 900 looks like it was born with its new curled-up tips. It looks so good, in fact, that I’m betting some existing TBM owners put money down on a 900 just because it looks so great. It wouldn’t be the first time such a thing has happened.
You don’t get a 15- to 20-knot improvement in top-cruise speed by making an airplane prettier, however, and the truth is the company used a multiprong approach to dramatically improving the TBM’s already impressive numbers.
New in Many Ways
Very seldom are major aircraft manufacturers successful at keeping their secret programs secret, but in the case of the TBM 900, Daher-Socata kept the rumor-safe shut tight. The program, called the “Century Project” internally, has been in the works for a few years now and takes advantage of technologies not available to the company when the airplane was born a quarter of a century ago. Chief among these is computational fluid dynamics (CFD), which existed but was beyond the reach of a company like Socata at the time. In reworking the 900, Daher-Socata engineers made extensive use of CFD in order to minimize drag. While that sounds simple enough, nothing could be further from the truth. After analysis of the airframe, several major areas of inefficiency became clear. The cowling, now in carbon fiber, was extensively redesigned to cut drag and improve cooling, with a big inlet below the prop. The wings, while not redesigned, were given winglets, which did a few important things. First, they kept the spanwise flow along the wing from spilling over, adding efficiency mostly by decreasing drag. They also increased the effective wingspan of the airplane, again increasing lift. Finally, they improved the handling of the ailerons, with some reporting smoother roll response and others greater control feel. To me, it felt as if both were true. That’s a lot of bang for a pair of winglets.
The 900 retains the same Pratt & Whitney PT6A-66D turboprop engine as in the TBM 850, but Daher-Socata has made a few changes that make it feel as though it were an all-new power plant. For starters, the TBM can make use of 850 shp for takeoff thanks to a new torque limiter, so takeoff rolls are reduced. Takeoff at standard conditions at max weight requires only 2,380 feet over a 50-foot obstacle. That’s impressive for a 7,394-pound airplane.
The operation of the engine is all new too. While you can’t yet get a fadec PT6, the TBM is the next best thing, with a power control unit that combines thrust, propeller and condition levers by using an ingenious all-mechanical mixer. Pilots use a single lever that after start-up slides to the left to serve as the thrust lever, making it impossible to grab the wrong lever at the wrong time. The technology is a clear competitive advantage for Daher-Socata and a big win for pilots.
The yokes have also been redesigned. They are more compact, nicer to handle and attractive. I didn’t like how high the trim button rose from the end of the yoke horn. It was an awkward stretch for an action you need to perform almost constantly during departures and arrivals.
Flying a Fast Turboprop
I went flying the 900 with Daher-Socata pilot and formation flier extraordinaire Wayman Luy. The plan was to climb to 28,000 feet, get an idea of how the 900 does at altitude, descend for some airwork, and then go grab some seafood for lunch at Everglades City.
Another improvement for the 900 I’ll mention now is the standard pilot door. While a door had been available previously, it is standard on the 900, and the construction of the door, milled aluminum substructure instead of built-up construction, is new as well. Having a pilot door makes life easier, as all you need to do is climb in, pull up the step and close the door instead of having to go through the process of opening and closing the big main passenger door before climbing through the cabin to the front seats. The addition of the pilot door as standard is huge.
The start sequence isn’t different from that on previous TBMs, except that you use a single lever. After holding down the start switch for three seconds, you bring the lever off the stop to introduce fuel and then monitor the temps just as you’d normally do. Once you’ve got a good start, you move the lever firmly to the left. It is now the thrust (and reverse thrust) lever. A separate emergency override lever gives the pilot fail-safe control.
Taxiing the 900 feels faster to me, though Wayman doesn’t think it is. I think the five-blader gives the airplane a bit more thrust at idle. On the takeoff roll, the extra thrust from the 850 shp is an eye-opener. The TBM always seems to leap off the runway, but the 900 seems to accelerate much faster than the 850, an observation with which Wayman readily agrees.
Climb-out is fast. It was a very warm spring day, but at best rate of climb we were seeing a steady rate of 2,000 fpm. With three of us on board — photo ship pilot Bruce Moore came along for the trip — plus a good bit of gear and full fuel, we had a healthy load too.
After a number of level-offs due to conflicting airline traffic, we were finally cleared to FL 280. Daher-Socata says the 900 will get up to FL 310 in 18 minutes. I don’t doubt it, but we didn’t get to see it that day.
At 28,000 feet, the optimum altitude for the 900 compared with 26,000 feet for the 850, we saw 324 knots true airspeed at ISA+8, a single knot over book value, which lists 330 knots at ISA for that same altitude. At that level, we were burning around 60 gallons of jet-A per hour per engine, of which there is, of course, only one.
Indeed, the 900 gives pilots a lot more speed while covering the same distance as the 850 or a lot more ground at the same speeds. It’s a win in either direction for the new kid. The range and speed profile is impressive. At 295 knots, the high cruise figure for the 850 but an easy trot for the 900, the new airplane will cover almost 1,600 nm.
That means that trips that require a fuel stop for an airplane like the Citation Mustang or the Phenom 100 will be easy pickings for the TBM 900, just as they were for the 850. Only with the 900, you get there a lot faster.
The cabin is nice too. It’s a standard club cabin, but Daher-Socata offers it in an easily convertible form as well. You can add a potty chair, but privacy is not ideal. It’s a family or emergency affair. Then again, smaller airplanes, even transportation airplanes, are often compromised in this regard.
The increase in horsepower for the 900 wasn’t a question of structure or power but of controllability at extremely slow speeds and extremely high power. The addition of the winglets and newly designed strakes, Daher-Socata’s Michel De Villiers told me, went a long way toward proving the additional stability needed to pass that one critical test.
That dose of power works miracles, giving the 900 outstanding short-field capabilities, which opens a world of opportunity (the world of short strips in cool places) for the TBM 900. Everglades Airpark is only 2,400 feet long, but with my far less than elegant technique, I was able to get it down and stopped with a lot of room to spare. Getting out of town — after a tasty lunch of fried clams and shrimp and conch chowder at Triad downtown — was just as easy. I didn’t even have to hold the brakes.
The final landing of the day, back at North Perry, was about as good as my first few efforts, through no fault of the airplane. I would have liked to have flown for a few more hours and done a dozen circuits or so, but I’d learned plenty about the airplane, and it was heading off anyway. Wayman was taking it to a prospect in central Florida. Like all of the sales guys at Daher-Socata, Wayman has been busy the last couple of months showing the 900 to very interested prospects, many of them current TBM owners.
It comes as no surprise to me.
As has been the case with every new introduction to the TBM family, the latest, the TBM 900, is the best yet by a long shot. The gorgeous lines, the speed, the tech refinements and the improved performance across the board combine with all the strengths of a well-proven product to make the TBM 900 a tremendous success.

FLIGHT TEST: Piaggio Avanti II - Hard to beat
Piaggio Aero Industries has just delivered its 100th P180 Avanti, almost 20 years after the twin-turboprop business aircraft first flew. Many of those sales have been achieved since the long-established Italian manufacturer was reinvigorated by its mid-1990s takeover by a group of private investors. Now Piaggio has introduced its first major upgrade of the P180. With improved avionics and systems, the Avanti II replaces the original beginning with delivery of the 105th aircraft in November.
The P180 turboprop first flew in 1986 and was certificated and delivered to its first customer in 1990. Sales to date have been split roughly 60:40 between the USA and Europe. Production is running at around 20 a year and, with a backlog of 70 orders, a sale today translates into an early 2009 delivery. Airframe sections are produced at both Genoa and Finale, but final assembly and flight test are carried out at Piaggio’s plant at Genoa International airport. Aircraft can be completed either in Genoa or in the USA, currently at Stevens Aviation in Greenville, South Carolina.
The pusher-turboprop Avanti still looks as futuristic as when it first flew two decades ago. The small fixed forward wing gives the Avanti a fighter-like look and is unique in commercial aviation. Use of a lifting forward wing means that the rear horizontal stabiliser is also a lifting surface, resulting in a 34% decrease in main wing area. The three lifting-surface design is patented by Piaggio and even the fuselage is shaped to add to the aircraft’s total lift.
Up close the narrow-chord wing looks like it came from a high-performance glider. Piaggio says low-drag laminar flow is maintained to around 50% of wing chord, compared with around 20-25% for conventional tractor turboprops where propeller wash disturbs the airflow over the wing. The highly streamlined fuselage also maintains laminar flow to about 30% of its length, the company says.
An underlying reason for this ability to maintain laminar flow is the quality of surface finish. Although the Avanti is 90% aluminium alloy, the fuselage and wing look like they are moulded from composites because they are so free of surface imperfections. The reason for this is a Piaggio-patented construction method whereby the airframe panels are held in place in the jig during assembly by large vacuum pads so that the frames and ribs can be riveted from the inside. This makes for an exceptionally smooth surface finish and reduces drag.
The result is that the Avanti offers jet-like performance: a cruise ceiling of 41,000ft (12,500m), with a cabin altitude of only 6,600ft; a maximum operating speed of 260kt (480km/h) indicated/Mach 0.7; a maximum cruise speed of 398kt true; and a range of nearly 3,320km (1,800nm) with visual flight rules reserves. This range requires a fuel capacity of only 1,270kg (2,800lb) given that its specific air range at high altitude is 3.4km/kg (0.84nm/lb) compared with around 2 for current jets or 2.7 for other turboprops. The Avanti has no natural turboprop competitors, and its closest jet rivals are the Raytheon Premier I and Cessna Citation CJ2+.
Combined with certification for Category II instrument landings, steep approaches and flight into known icing, and the Avanti has the ability to operate on runway lengths of only 1,070m at maximum weight. The cabin provides a stand-up height of 1.75m and a width of 1.85m, dimensions only bettered by super mid-size jets. The cabin can seat up to nine in a corporate shuttle layout, six typically in the VIP role or two stretchers with attendants on a medevac mission. The Avanti is certified for single-pilot operation, but Piaggio say most operators prefer to fly with two pilots, and a crew of two is mandated for Cat II approaches.
Uprated engines
The principal performance upgrades in the Avanti II are the uprated Pratt & Whitney Canada PT6A-66B engines that give increased power at altitude and an increased cruise speed at maximum continuous power of 398kt at 30,000ft. The airframe has also been recertificated to raise maximum take-off weight (MTOW) and maximum landing weight (MLW). MTOW is increased from 5,240kg to 5,465kg and MLW from 4,965kg to 5,195kg. This equates to an extra two passengers at the maximum fuel load of 1,270kg, or 1,043kg of fuel with the maximum payload of 907kg. Either way this greatly increases the Avanti II’s flexibility and choice of cabin configuration.
The biggest advances since the introduction of the aircraft in 1990 have been in navigation and safety systems, and a completely redesigned cockpit is central to the Avanti II upgrade. This is designed to keep the aircraft abreast of current and proposed aviation regulations for the foreseeable future, and the combination of the latest avionics and jet-like performance should allow the Avanti II to hold its niche market position against the latest light jets such as the Citation CJ2+ or Premier I.
At the heart of the upgrade is the Rockwell Collins Pro Line 21 integrated flightdeck, featuring three 200 x 255mm (8 x 10in) liquid crystal displays. The outer screens function as primary flight displays (PFD) for each pilot and the central screen as a multifunction display (MFD) shared by both. PFD modes are managed by individual display control panels mounted vertically on the instrument panel adjacent to and inboard of the appropriate LCD. MFD modes are controlled by a cursor control panel mounted on the central console just aft of the throttles and forward of the single FMS-3000 control display unit (CDU). The FMS-3000 flight-management system is GPS-based and is linked to dual attitude/heading reference systems as well as DME and VOR receivers. The FMS provides both lateral and vertical navigation (LNAV/VNAV) guidance to the dual-channel, three-axis autopilot.
The main displays are complemented by a radio tuning unit (RTU) that is used to select all VHF communications, VOR, ILS, DME, ADF and Mode S transponder. Additionally, weather radar, TCAS 1 traffic collision avoidance system, terrain awareness and warning system, emergency locator transmitter and a digital combined standby instrument are fitted as standard. Options include the ability to display Jeppesen charts (airport, approach and en route) on the MFD.
Piaggio has not just placed electronic screens on top of an existing cockpit layout to create a part-digital, part-analogue flightdeck, but has totally redesigned, relocated and logically grouped all the other systems switches and gauges to present a cockpit that now looks clean and as modern and well laid out as any new competing type.
There is an adage in test flying that states that “equipment doesn’t equal capability” and this is equally applicable to avionics upgrades. Displays and functions may look great in a glossy brochure, but the acid test is how well they work. Based on my experience of EFIS-equipped aircraft, including fully integrated types such as the Bombardier Global Express and Hawker 800XP, and “hybrids” such as the Avro RJ100, my remit was to assess how well Piaggio has incorporated the new avionics in the Avanti II.
Piaggio chief test pilot Marcello Vitale was the safety pilot for my evaluation of the Avanti II in September, in Genoa. The aircraft was the Avanti II testbed, registered I-PJAR. This is an early P180 prototype that was modified as the test aircraft, and its cockpit represented the new avionics in virtually all respects.
After about 60min of cockpit brief and avionics familiarisation with Vitale, we were ready to start and taxi. Rather than undertake more extensive ground preparation, I felt that if I was instinctively able to operate the aircraft, manage the communications, navigation and autopilot functions and interface easily with the displays, then the overall package would work well for other pilots new to a fully integrated cockpit, but having the benefit of an extensive ground school and simulator type course.
Logical layout
The Avanti is a DC electrical aircraft and an external power cart allowed us to load all FMS and route data and keep the displays fully powered during the 60min briefing (the aircraft has internal DC power that allows the FMS to be programmed before engine start over shorter durations). All engine start and run switches are centrally and logically located in one panel at the forward end of the centre console just ahead of the throttles.
A rotary test switch on the base of the console was used to check all ancillary systems such as hydraulics, electrics and de-ice, and the aircraft was ready to taxi 3-4min after engine start. Take off was from runway 29; wind was 11kt from 030°; temperature 19°C, aircraft fuel was 1,090kg, giving a take-off weight of 5,020kg; V1/VR was bugged at 106kt indicated for the mid-flap setting. Final take-off speed was bugged at 160kt. The flight director (FD) was set to go-around mode (the vertical bar set to 8° nose-up to cater for engine failure).
Take-off roll and rotation were simple to achieve and the FD easy to follow, but the aircraft was rotated initially to a nose-up pitch attitude of 12° once a two-engine climb was assured. Modes were then changed to heading and flight level change and the FD followed to achieve a speed of 160kt. Hand flying to follow the FD was easy and natural in these basic modes with no irregularities. The PFD screens were clear and well defined. I liked the enhanced PFD overlays that showed sea (in blue) and coastlines, airways, danger areas and training areas.
Levelling off at flight level (FL) 080 (8,000ft) while hand flying was easy, although the 1,000ft-to-go caution horn was a little loud in my opinion (Vitale says the volume is being reduced in the production aircraft). Pro Line 21 does not provide an amber mis-compare alert if different altimeter pressure settings are used on the two PFDs, so good operating procedures dictated that we both ensure the standard pressure had been set on our own PFD.
I engaged the autopilot and evaluated its modes, including height capture both above and below present altitude using both flight-level change mode with varying speed selections and vertical speed mode with varying vertical rates. The modes were accessed through the glareshield flight guidance panel and the mode and engage buttons were well separated and labelled. The altitude, heading, speed and course change knobs were easy to distinguish, with good tactile cues to tell them apart. The flight guidance panel has no “preset” windows, and the buttons have no internal “selected” lights to show engagement, so all selected parameters are shown in the PFD.
The autopilot was smooth and linear in all “basic” modes. The same result was obtained in VOR radial capture mode and FMS LNAV capture mode. The PFD display of the boundaries of the training area we were using was excellent, including changes in displayed range and I knew at all times where I was in relation to the airspace around me. At present the aircraft does not have an autothrottle or a thrust rating panel that can be used to set speed or thrust settings. Speed changes were so smooth and the internal feel so “jet-like” that I had to closely watch my speed control, as the airspeed presentation was a standard vertical tape/rolling digit display.
The weather radar and TCAS 1 display modes were easy to operate. Communication/navigation frequencies and transponder codes were easy to set or change via the single central RTU, which could be reached and seen clearly by both pilots. The FMS CDU was well positioned on the console between the two pilots seats, but reprogramming it would be a task for the pilot not flying. The CDU was clear and logical, the buttons easy to find and press and I liked the use of colour and the data-required boxes that needed to be filled before operation.
Unplanned diversion
We then evaluated an unplanned diversion to Albenga to carry out a localiser/DME approach to runway 27. We had no Jeppesen paper charts; I had never been to Albenga and had not studied the approach; I had only been airborne about 25min in the Avanti II and gave myself less than 5min to set up the approach. With Vitale doing the radio we turned from the training area at FL080 towards Albenga about 40km away at a cruise speed of 200kt.
He entered a “new route to” in the FMS CDU; I bought up the approach plate in the central MFD, and set the required frequencies and course from the displayed chart. I descended, lowered flaps and gear, briefed Vitale on the height/range calls, and took radar headings and approach capture. The aircraft captured the localiser smoothly, with no sign of overshoot or non-linearity, and I flew the descent in vertical speed mode, adjusting my rate based on information given to me by Vitale, but which I could also read from the chart display on the MFD. At the minimum descent altitude, I was properly positioned to land at Albenga.
The Avanti II had passed the test: the aircraft, avionics and crew “package” had operated in harmony to carry out a non-precision approach safely and efficiently, and the avionics greatly assisted a pilot new to the aircraft, the airspace and the airport. At all times my situational awareness was high, and I was always in full control of the aircraft and its configuration. It was an impressive demonstration of the capabilities of the aircraft’s upgraded systems.
Instead of landing I carried out a go-around (GA). This entailed pressing the GA button on the left-hand throttle, following the FD, raising gear then flap, and selecting LNAV on the flight guidance panel to follow the full missed approach procedure as detailed on the FMS. The go-around in the Avanti II does not disconnect the autopilot, so the procedure was simple and straightforward. Since Albenga lies in a basin surrounded by high hills, I could see the TAWS display of the terrain surrounding the airfield. Terrain colour was coded in “pixel” fashion rather than solid colours used by the weather radar display. The display was clear and distinctive although, having followed the missed approach procedure correctly, no audio warnings were triggered.
We flew back to Genoa’s runway 29 to carry out in sequence a Cat I ILS to a roller landing, a Cat II ILS to a roller landing and a GPS approach to a full stop landing. During these approaches I evaluated the VNAV functions, RTU auto-NAV frequency tuning for approach and auto-LNAV/VNAV transition into ILS approach mode. The overriding impression was of a system bursting with capability, but one where the cockpit crew must interact well with each other and use good operating procudures to ensure each knows what the other is displaying on his PFD, what the pilot flying has selected for NAV source, what the pilot not flying has programmed into the FMS, what the autopilot will fly and when the pilot will intervene.
At final landing, flight time had been 2h 20min and we shut down, after a short taxi in, with 410kg of fuel remaining. It is clear from a short evaluation flight that the Avanti II upgrade is a successful integration. Although Pro Line 21 is an off-the-shelf system designed for aircraft in this class, the feel in the Avanti II is of a modern flightdeck designed from the ground up. The upgrade adds to Avanti’s safety with TCAS and TAWS, and adds to its capabilities with 8.33MHz VHF radios, datalink, precision RNAV, VNAV and ELT. Options include HF radio, cockpit voice recorder, satellite communications and electronic chart overlays. An automatic torque limiter/thrust rating panel and autothrottle would further reduce pilot workload, but these are desirables not essentials and, because the engines are not digitally controlled, may not be cost effective.
Easy to use
The avionics are easy to use and understand and the PFD/MFD screens outstanding in image quality and displayed information. The electronic chart overlay on the MFD reduces pilot work and is to be commended. But with all this capability comes the need for proper training and operating procedures, particularly if flying as a two-person crew.
Piaggio will have an Avanti II Level D full-flight simulator available from the second quarter of next year at FlightSafety International’s West Palm Beach, Florida centre. Rockwell Collins conducts a two-day Pro Line avionics course for new pilots and Piaggio provides an avionics computer-based training package with each aircraft sold. This is wise, as management of the avionics lies at the heart of getting the most out of the outstanding performance this aircraft offers.
The Avanti II really does have jet-like characteristics, which no other turboprop can match, so that its true competitors are the latest generation of light jets. If pure top speed is not the overriding criteria, the Avanti II’s combination of fuel efficiency, cruise speed, range, ceiling and cabin size are hard to beat. Piaggio has moved to secure the future of the Avanti with this avionics upgrade. The aircraft deserves its “Ferrari of the skies” title, and can hold its own against any similar sized jet. -

New Piaggio Avanti Evo Twin Turboprop Takes Flight
The new Piaggio planes are flying out of Southern California…
The newest edition of the Avanti P.180 twin turboprop, made in Italy by Piaggio Aerospace, now is flying in the United States, with a recent delivery to West Coast Aviation Services, at John Wayne Airport in Orange County, California. The P.180 is known for its unique aerodynamic performance, based on its three-lifting-surface configuration. The main wing is placed near the rear of the fuselage, while a second, smaller wing at the nose, known as a canard, provides extra lift and efficiency. A wing mounted on the tail provides the third lifting surface. Combined with the powerful turboprop engines, the aerodynamic boost adds up to more efficiency in flight, less fuel burn, and lower operating costs per hour compared to traditional aircraft of similar size.
Interior of the Avanti P.180. Paul Cordwell
Evo, the third generation of the P.180 design, is updated with five-blade scimitar propellers that boost performance, new cabin layout options, and added safety systems. The airplane is quieter and more fuel-efficient than earlier versions, and the service and support network has improved, the company says. With a ceiling at 5 feet 9 inches, the custom interior feels roomy for eight in VIP seating, with new leather seats by Iacobucci that recline and rotate fully, plus plenty of fold-down tables, adjustable lighting, connectivity, and baggage space. Low noise levels and a cabin altitude of just 6,600 feet help minimize passenger fatigue. Evo cruises at speeds up to 463 mph for more than 1,900 miles.

Piaggio P.180 Avanti II
From the beginning, Piaggio Aero intended the Avanti to be a turboprop that played in the same niche as light jets but with better economy and a larger cabin. It pulled the concept off. The Avanti II does indeed have a big cabin, the best in its class by far, and it also has good speed and range, and best-in-class fuel efficiency. Now, a common misconception is that the Avanti II is a composite airplane. It is not, at least not primarily. The fuselage, wings, tail and forward wing of the airplane are metal, though admittedly metal that has been shaped and smoothed in a way that makes a compound curve look like child’s play. Other parts, mainly fairings and the like, are composite, but for the most part, Piaggio Aero’s Avanti II is a sheet metal airplane.
The use of alloys instead of composites was a purposeful choice for Piaggio Aero, which certified the airplane more than 20 years ago at a time when there were few successful composite models and sheet metal seemed to augur a shorter approval program than plastics did. It wasn’t the only fast turboprop twin with a forward wing — the Beech Starship was a contemporary, though that company stopped production of the composite cabin-class twin shortly after it started it, admitting later that the composite model was so time-intensive to build that it was simply unprofitable. Piaggio Aero, on the other hand, is still steadily producing its model. It has delivered nearly 200.
The Shape of Fast
If materials were a conservative approach, configuration was not. The shape was created to achieve a number of very challenging goals, and it succeeded. The shape, you’ll see, is not simply for show, though ironically it shows very nicely.
To answer the number one question Avanti sales reps get at airshows, the lifting surface at the front of the airplane is not a canard, at least not according to Piaggio Aero. It is, instead, a forward wing. The difference between the two, they say, is that the forward wing, while a lifting surface, is not a controllable one. There is no “elevator” in it; hence, it’s not a canard. I’ll let Peter Garrison work out both the semantics and aerodynamics of the question (if those two disciplines would differ on the subject). I call it a three-surface design, with forward wing, main wing and tail.
Unlike what I think of as a canard, in the Avanti the elevator is back on the tail and the ailerons are on the trailing edge of the wing, along with some very serious flaps, which are designed to deploy slowly so as not to cause a dramatic pitch change — they succeed at that, by the way. The main wing of the airplane is very small (172.2 square feet, slightly less than a Cessna 210’s) and very highly loaded.
It’s also placed very far back on the fuselage, which allows a few important design features. First, with a far aft wing the engines — two Pratt & Whitney PT6s in a pusher configuration — can be mounted very far aft as well, which helps keep the interior noise low. Occupants can converse easily, as can the pilots. The problem with the aft mounting is that the Avanti II has a very distinct exterior noise signature that is problematic — while by all accounts the Avanti II is no noisier than other PT6-powered twins.
While the forward wing is not fitted with an elevator, it does have a flap, or set of flaps, depending on how you look at it. The surface, which like the tail has a considerable amount of anhedral, is ice-protected, as is the windshield, by electric heat. Bleed air would have been nice, but by the time it had traveled the distance from the engines, it’s not clear that it would have been very hot anymore, and the bleed air used to heat the wing leading edges robs the turboprops of a great deal of power to begin with. Along with the wings, the engine inlets and wing leading edge are deiced by bleed air; the tail does without, as do the props, which are heated directly by the engine exhaust blowing over them.
Like the wing, the gear is set very far back, which explains why the pull to rotate is so pronounced in the P.180. Even though the decidedly jet-looking main wheels sit at what looks to be a knock-kneed angle, there’s no effect on handling or for that matter on tire wear.
The other huge advantage of the configuration is that it opens up the fuselage, allowing a cabin that is closer to that of midsize jets than light jets. For private owners, charter customers and fractional owners, the big cabin is a major selling point. The cabin, interestingly, isn’t symmetrical; it’s a little cozier up front than in back. But with a main cabin height of 69 inches, it’s easy to move about. It’s also remarkably wide for an airplane of its size. At 73 inches across, the width allows for great shoulder room, easy entry though the airstair door and a very comfy hard-door lavatory.
In the end, the Avanti II’s configuration allows it to achieve light jet speeds in the same way as light jets do, by using a very small, highly loaded wing to go with a good dose of power. The Avanti takes that formula and pushes it to the design edge, achieving that performance with a great deal less power than in comparable jet products and with the best cabin in the class by a long shot. It’s a great formula.
Technology and Comfort
The airplane has been constantly improved over the past decade, with new interiors, higher max takeoff weight, higher Vmo and avionics upgrades galore. Today’s airplane has the Rockwell Collins Pro Line 21 avionics suite, with all the bells and whistles. With fully reversionary flat-screen displays with a host of safety utilities, including TCAS, TAWS, satellite weather and more, the avionics suite is top-notch, and Piaggio Aero has been working with Rockwell Collins since the introduction of the Avanti II to add upgrades as they became available. One that’s lacking is the single FMS. A fully independent backup navigator can be installed as an option. Some operators use a Garmin 430 mounted on the far left side of the panel.
The Avanti II, I should probably mention, is a single-pilot airplane; it doesn’t need a crew. Theoretically, a newly minted multiengine pilot with a high-altitude endorsement could hop right in and go flying. In reality, the P.180 is a fast, sophisticated, high-flying airplane that requires the same kinds of skills and training as any single-pilot business jet. Most charter operators fly the Avanti II with a crew of two.
Flying the Avanti II
I flew a new Avanti II out of Denton, Texas, home of Avanti completions in North America, with Piaggio America’s Grant Spigener. Grant has been flying the Avanti for years with thousands of hours of experience in the airplane, much of it under typical charterlike conditions. He was a good guide to have for my first flight in the airplane.
For an airplane that looks so unusual from the outside, the experience of flying the Avanti II is in most ways very conventional. The biggest problem I had was in remembering that I wasn’t flying a jet and that mounted 30 feet in back of me, completely out of sight, were two turboprop engines. As a result, the engine management chores on the P.180 are more complicated than those in today’s fadec-equipped light jets. The start-up sequence is pure PT6; it’s a completely pilot-controlled process. Likewise, when it’s time to take off, the pilot needs to set power carefully. It’s a hard transition for a pilot coming back to PT6s after having flown modern fadec turbofans from Williams and, yes, from Pratt & Whitney.
Taxiing feels conventional, though it’s accomplished using an electrically actuated, hydraulically powered nosewheel steering system. In ground idle and with power pulled back to idle, the airplane still has a tendency, like many turboprops, to get going too fast, so you need to use beta to keep things slowed down. Though the very basic levers don’t look as though they have reverse capability, they do, though it requires a healthy lift on the levers to get them back over the gate to provide propeller braking to slow things down on the ramp and taxiways.
Once on the runway and cleared for takeoff, we checked to make sure the flaps were set for takeoff and the steering was too — there are different modes depending on how fast you’re traveling though there’s no tiller — and that our trims and condition lever were correctly set. Acceleration feels fast, but steering through the rudders is positive and smooth, though it requires an easy touch to avoid darting about. We rotated at 105 knots, which is pretty darned fast for a turboprop, using about half of the available 7,000 feet at KDTO. I asked Grant to put the gear up on positive rate of climb, and soon thereafter I called for the flaps to be retracted. I stayed on the flight director as we climbed, quickly getting into IMC and getting rapid-fire climb-and-maintain clearances along the way. Grant handled the radio tuning.
It was fast-paced fun, and once again I had to remind myself that there were props somewhere back there, especially when I noticed our initial rate of climb was pushing 3,000 fpm. At FL 250 it was still better than 2,000 fpm at 170 knots indicated.
I was pleasantly surprised at how nicely the Avanti II handles. Despite the fact that it took me a while to get a feel for the trim button — there’s a little activate button in the center of the trim hat — the hand-flying was nothing short of delightful. I kept on the controls through a number of heading changes much up into the midteens before switching on the autopilot.
While the rate of climb is great, one thing the Avanti II doesn’t do is climb or descend at very high indicated airspeeds, the former a condition of available thrust. So as fast as it is at cruise, its block times suffer as a result of the climb speed and relatively low Vmo (260 indicated) and Mmo (Mach 0.70) limitations.
Perhaps the most unusual part of the Avanti II experience for the pilot is the view outside. As it wraps itself around the pointy nose of the P.180, the windshield stretches out for several feet in front of the pilots and wraps back around them tightly. The effect is a view that changes substantially as you point the nose up or down in various phases of flight. A traffic target can be out of view in certain positions, at around 2 o’clock for the left-seater or 11 o’clock for the right-seater. On climb-out, especially given the steep angle of attack of the impressive-climbing P.180, it’s hard to see much out front at all. On approach, however, the view is excellent.
Fastest Turboprop
The plan for my flight was to climb to 30,000 up to the Wichita VOR to do something I’d never done before, an RVSM check. I won’t get into the details of it here, but suffice it to say Grant was busy with taking notes as I flew the airplane. Once having completed that check, we asked for and got a climb to FL 380, a common long-range cruising altitude for the P.180, which has a ceiling of 41,000 feet. I could see why 380 is a preferred altitude. At that level we were seeing 380 knots or Mach 0.664 on 600 pounds of jet-A per hour, not per side but total. That’s slightly less than 100 gallons per hour, a figure light jets simply can’t touch.
After we’d checked figures at 380, we headed down briefly to FL 320 on the way back to Dallas. Once level, we were rewarded with what was nearly the top speed of the P.180, which was consistently 395 knots bumping up to that magical 400-knot figure on a couple of occasions, those figures at around 800 pounds per hour total. We were light and it was slightly colder than standard, both of which help boost true airspeed numbers by at least a few knots. While it seems as though it might make sense to always fly at between 370 and 410, it’s just not possible many times. This is another advantage of a turboprop. The fuel penalty for flying in the 20s is not as extreme as it is in turbofan airplanes.
The Avanti II gets its best range figures, up around 1,500 nm, at higher altitudes and lower fuel burns, and Grant told me that the range is real, commenting that he has never had to make more than one fuel stop going from any one point in the continental United States to another. This kind of range makes the P.180 a great bet as a regional airplane or one that’s based in the Midwest. Of course, with higher operating weights you won’t be able to carry as much fuel or, hence, get as much range, though the truth is that most flights in a 400-knot airplane are less than 1,000 nm anyway, and with a thousand-mile range as the target, you can liberally load the P.180.
This, along with the airplane’s great cabin and operating economies, has made the Avanti II the airplane that has helped create the remarkable success of charter and fractional operator Avantair, which operates 57 Avantis. In fact, Avantair late last year took possession of the 100th Avanti delivered in the United States, which has been far and away the model’s best market.
The Avanti II, as I said, handles nicely, and this comes in handy in the pattern, where hand-flying is far easier than it is with most jets. The Avanti feels very stable and is easy to maintain altitude in while hand-flying compared with other airplanes in and around its class.
Landing the P.180, as I’d heard previously, is interesting in that the attitude is very flat. Considering the shape of the nose in front of you, this is handy, because the runway stays in easy view the entire time. The approach speeds are very fast by turboprop standards. You fly final at around 120 knots; when you pull back on the power as you land, the nose rises slightly, the mains touch, and you relax back pressure and prepare to get stopped, a job that is greatly aided by big carbon brakes and extremely effective prop braking. At sea level under standard conditions, the Avanti II needs almost exactly the same amount of runway to land as it does to take off, just over 3,200 feet.
When Flying first flew the Avanti in 1990, we predicted that its great fuel efficiency would be a big selling point, and that has been true. What we didn’t fully realize is that over the next 20 years no light jet would emerge that could challenge the P.180’s remarkable combination of speed, fuel efficiency and cabin size, a trifecta of strengths that has made it a popular transportation airplane with operators for whom efficiency, comfort and high style are the hallmarks of having arrived.

Pilot Report: Piper PA46 M-500
The PA-46 M500 refines Piper’s pitch to well heeled, value-conscious general aviation pilots considering the transition from piston to turboprop, making its upsell not with increased power and performance but with enhanced safety. It’s the definitive answer to concerns safety experts, insurance companies and pilots raise about the challenges of stepping up to higher performance aircraft, questions the original PA-46 helped crystallize.
Piper’s pressurized, piston-powered PA-46 Malibu, introduced in 1982, created the modern cabin-class single, a category now dominated by turboprops, with Daher, Pilatus and Cessna offering interpretations of the concept. Meanwhile, Piper built out its PA-46 “M-Class” line, upgrading the Malibu into the Mirage and flanking it with the flagship Meridian–certified in 2000, which brought the Vero Beach, Fla.-based manufacturer into the single-engine turboprop echelon–and the entry-level, non-pressurized Matrix recip.
Earlier this year Piper revamped and rebranded the turboprop Meridian as the M500 and the Mirage as the M350, and also announced the M600, a more powerful version of the M500, expected to receive certification by year-end.
The successful growth of the PA-46 product line stands in contrast to its entry into service. In its first iteration, powered by a 310-hp Continental, a series of in-flight break-ups and other accidents prompted the FAA to issue an AD removing the PA-46 Malibu’s certification for flight into known weather, before the agency withdrew the directive after further testing of the design. The break-ups were attributed largely to pilot error, and subsequent PA-46 models demonstrated no such accident proclivity. The new upgrades aim to move loss-of-control accidents into the realm of impossibility.
The M500’s primary enhancement is electronic stability protection (ESP), incorporated into the Garmin G1000 autopilot flight control system. (The M350 also incorporates ESP, as will the M600.) ESP–operative whenever the autopilot isn’t engaged, and augmented by underspeed protection (USP) and overspeed protection–acts like an invisible copilot, ready to intervene any time the aircraft approaches the edges of its normal airspeed or bank angle envelopes. The M500 also has a coupled go-around and automatic level mode among its list of safety features.
Piper distributor Columbia Air Service, at Connecticut’s Groton-New London Airport invited AIN to fly the M500 (and the M350) and see the results of the upgrade. Columbia’s experience with Piper turboprops predates the PA-46 era; it was heavily involved in the Piper Cheyenne aftermarket before becoming a Piper dealer in the mid-1990s. Soon after, Columbia recruited Gordon Ramsay, a Hartford native who’s been buying, rebuilding and selling airplanes since he was a teen, to serve as Piper program manager.
The M500 Outside and In
Sitting relatively high off the ground, its long wings uncluttered by engine cowls, the PA-46 has always had a sleek, eye-grabbing ramp presence, and the small, horn-like exhaust stacks poking from the cowl of turbine-powered PA-46s add a brawny swagger to its visual appeal. Externally, the M500 and the Meridian are identical, distinguishable from piston-powered PA-46s by the extensions at the leading edge of the wing roots (for more fuel capacity); the 37-percent larger empennage; and vortex generators on the wings. There’s no nose baggage compartment, either, as the cowl is occupied by the M500’s Pratt & Whitney Canada PT6A-42A, flat rated to 500 shp.
Piper has been refreshing the interiors of the M-Class in recent years while also striving to differentiate them. All PA-46 models formerly shared the same basic interiors. Now Piper’s cabin appointments reflect the model’s position in the fleet, putting the M500 at the apex of its interior styling efforts. Its standard Premier Elegance color-coordinated leather seats, carpet and headliner are offered in two neutral-tone color schemes: Dune or Glacier. Meanwhile, new PA-46 cabins all benefit from work done by Boston’s Blokx Design, which Piper engaged to rethink and redesign cabin elements such as armrests, cup holders and stowable table, without changing production tooling. USB charging ports in the cabin and cockpit have been added to the M500.
The M500 offers a GSR-56 global satellite datalink Iridium satellite transceiver. Piper added the option with an eye on the international market, as a conduit for getting in-flight weather in areas without access to XM weather or similar services. It has found 90 percent of all buyers want the system, primarily for telephone and text communication.
The enhanced cabins dovetail with changing ownership demographics. Whereas previously about 90 percent of PA-46s were owner flown, today the figure is about 80 percent, the remainder flown by professional pilots with the owner riding in the back.
Getting into the cockpit is still a bit of a squeeze, eased by the fold-down captain and copilot’s seats, but once seated in front there’s ample room, and the uncluttered panel adds to the feeling of spaciousness. The Garmin G1000 flight deck is dominated by the two 10.4-inch primary flight displays (PFDs) and center-mounted 12.4-inch multifunction display (MFD). An Aspen EFD1000 standby instrument has replaced electromechanical backup gauges and wet compass, unifying the appearance of the panel and, more important, easing pilot workload in the event backup instruments are needed, as the data presentation basically mirrors what’s on the Garmin screens. Switches for electrical, engine start, lights, ice protection and other systems are on a pair of overhead panels, separated by a smaller control panel for cockpit lighting. The GCU 476 keypad on the pedestal simplifies entering flight plans and other data into the G1000.
Meanwhile, the landing gear safety lights now appear on the MFD instead of cluttering the panel with a dedicated display, and in another upgrade, system aural alerts and the stall horn are now audible through the headsets. The intercom has 3-D audio.
Engine Operation and Management
The greatest challenge in transitioning from piston to turbine is operating and managing the engine, and Piper has put lots of effort into making the M500’s turbine operations simple. There’s no prop lever on the pedestal. Once the engine spools up, it turns the prop at 2,000 rpm at all times, leaving only the throttle to control the power. Also, the condition lever is simply a two-position fuel control, either in the on or off position. Other turboprop installations typically require fine-tuning the idle setting with the condition lever on the ground, to meet changing demands for powering onboard equipment. The M500’s ground idle–a minimum of 63 percent NG–provides sufficient power in all situations. The fuel system is also a simple on-off design. Automatic crossfeed keeps the wing tanks in balance. In the event of an imbalance, a fuel pump automatically engages, raising fuel pressure on the overloaded side and accelerating its fuel feed, until the imbalance is corrected.
The manual bleed-air system requires more attention than an automatic or electrically operated design, but it keeps the aircraft’s systems simple. Bleed air is kept off during engine start to ensure all the air is used for cooling the engine, rather than diverted to run other systems.
The M500’s autostart function simplifies the engine start, among the most intimidating parts of the turbine transition. After the G1000 completes its self-test, the fuel pumps and igniter switches are set to manual from the pilot’s overhead panel and autostart is engaged, which starts the engine spooling. At 13 percent NG the igniters fire, and the ITT and NG both climb. At 56 percent NG the starter automatically engages. Turn the fuel pumps to auto, and turn off the igniter. The engine is now started. Activate the generator, alternator, avionics, cabin pressurization and bleed air. The M500 is now ready to fly.
Before-takeoff checklist items include the overspeed governor, to ensure it limits prop speed to less than 1900 rpm, and reverse lockout, which prevents the engine from going into beta range in the air.
Our destination was Westchester County Airport (HPN), a mere 76 nm west. ATIS reported the wind as 250 at 12 with gusts to 16, and a scattered deck at 4,500 feet. With the tanks half full and the two of us on board we had room for about another 450 pounds of payload before hitting our 5,092-pound mtow.
Flying the M500
Engaging the flight director and following the command bars on takeoff yields a 125-knot climb-out once the gear and flaps are retracted, and we ascended at 1,700 to 1,800 fpm. A 145-knot climb-out delivers about 1,100 fpm. The pilot advances the throttle manually during the climb to keep power between 1,250 and the maximum allowed 1,300 pounds of torque.
Ramsey describes the M500 as a “point and go” airplane: simply pick a hole in a scattered or broken deck, point the nose at it, and blast through cloud layers piston-powered aircraft would have to pick their way around to climb above.
Leveling at 15,500 feet, we reduced power to 1,140 pounds of torque and TAS crept up to 232 knots, with a fuel burn of 290 pounds per hour (just under 40 gallons). If you’re going to own and fly this airplane, this is about as low as you’d want to flight plan, so you can take advantage of the fuel savings and airspeed gains that come with altitude. Headwinds are rarely strong enough to negate the speed and fuel burn obtainable at altitude.
We didn’t need to get into the high 20s for our brief flight to HPN (service ceiling is 30,000 feet, where fuel burn in cruise is about 37 gph/248 pph), or to check the M500’s top cruise speed of 260 knots. (The M500 and Meridian have identical performance numbers; last year in a flight in a new Meridian at FL240 at -20 degrees C and some 350 pounds below mtow, I saw 264 ktas in cruise.) Range-wise, the M500’s 170-gallon fuel capacity can take it 1,000 nm with IFR reserves at economy cruise, but at normal power settings the range is about 750 nm.
Enhanced Protection Capabilities
We tried out the ESP as well as the other protection modes on a flight in an M350 immediately before flying the M500; the systems operate identically in both aircraft. ESP provides a “resistive force to the pilot deviating from nominal flight attitudes,” as Piper engineering test pilot John Kronsnoble explained in a subsequent debrief, likening it to a “flight instructor, to make you know you’re flying the wrong way.”
Piper isn’t the only OEM offering stability protection through a Garmin (or other) interface. It’s available on the King Air 200, the Cirrus SR-22 beginning with this year’s model, and experimental aircraft outfitted with Garmin G3X glass cockpits. But each OEM tweaks the system for its own aircraft. Piper’s ESP engages at 45 degrees bank, and the resistive force reaches its maximum at 60 degrees, disengaging when the aircraft is returned to 30 or less degrees of bank. The pilot can manually override the system by overpowering the resistive force, and the ESP, USP and overspeed protection can also be disconnected–during training, for example–through the Garmin Aux page. But as the default mode, full protection will be restored whenever the Garmin boots up.
USP engages when pitch attitude reaches 17 degrees nose up, with forward pressure increasing to its maximum at 21 degrees pitch up, and disengages when upward pitch drops to 14 degrees positive. In extreme high-pitch attitudes, USP disengages at 50 degrees nose up.
The addition of USP to the safety package enabled Piper to add coupled go-around to the M500, allowing pilots to fly a missed approach without disengaging the autopilot. Should the pilot forget to add power, rather than follow the command bars up into a stall the USP will override the autopilot and lower the nose, giving the pilot a chance to take corrective action.
Overspeed protection engages at 189 kias or minus 15 degrees, reaching maximum resistance at 196 knots or 21 degrees nose down, and disengaging when airspeed slows to 188 kias or pitch is shallowed to 12 degrees negative or less.
In the real world, or the skies over Connecticut in our case, this works out well. Normal maneuvers are unencumbered, but as the bank increases into steep territory, or the nose is pulled up or pushed down beyond what you’d use for normal operations, the force serves as a reminder and assistant. In addition to its corrective forces, the system provides aural alerts and visual caution warnings on the PFD when activated.
The M500 also has an automatic level mode, activated by a blue button–a panic button, if you will–in the center of the panel. When pressed, it engages the flight director and autopilot and restores the aircraft to straight-and-level flight.
Together, all these safety enhancements add peace of mind, confidence and a sense of lightened workload, particularly in single-pilot operations.
But there’s an additional concern facing transitioning pilots: the threat of hypoxia, which is believed to have had a role in several recent fatal accidents involving high-performance singles. The M500’s hypoxia recognition system provides alerts should the cabin altitude climb above 14,900 feet when the autopilot is engaged. However, Piper elected not to incorporate in the M500 the automatic descent mode (ADM) featured in the M350. When activated automatically by lack of pilot response to hypoxia warnings, ADM brings the aircraft down to an altitude at which the pilot can recover. But since the M500 cruises near its Vmo of 188 knots, engineers determined that quickly descending to a breathable altitude at cruise power could easily exceed the aircraft’s maneuvering speed, and Piper ultimately decided ADM is impractical in the M500. ADM will be incorporated into the M600, which will have a higher Vmo than the M500, thanks to its stronger wings.
Meanwhile, the Garmin integrated pressurization system simplifies regulating cabin altitude. Turn it on before takeoff and tell it the elevation of your destination airport, and the system pressurizes and depressurizes en route automatically.
Additional onboard systems further bolster safety margins for handling weather and traffic. The Garmin GWX 68 digital color radar augments the XM WX Satellite Weather services available through the optional GDL 69A, and an optional GTS 825 traffic advisory system coupled with the GTX 33ES provides ADS-B in and out functionality.
Flight into known ice capability, air conditioning and yaw damper are standard.
Operating in Real-world Conditions
While the M500 represents a step up for most buyers, it puts them in the company of many higher performing business aircraft. Twelve nm northwest of New Haven, we checked in with New York Approach and requested the Rnav 34 approach into our destination, to see the M500 fly a coupled approach. We wouldn’t know if we’d get the approach for a couple of controllers down the road–it was a sunny afternoon in the busy Northeast corridor–but we were given a squawk code and directed to descend to 3,500 feet.
Pulling back the power to 345 pounds of torque produced a 1,450-fpm descent at 225 knots. Reducing to 60 pounds of torque steepened the descent initially to 2,700 fpm and then to 3,200 fpm. For an emergency descent, drop the gear, pull the power and point the nose down, keeping the airspeed at its 168-knot indicated maximum gear speed. With the four-blade prop acting as a speed brake, the M500 can descend at 6,000 fpm.
The wind at HPN was from 290 at 7, gusting to 17. A couple of controllers later, on a seven-mile right base along the shoreline, we were told to expect the Rnav 34 approach, and keep our best forward speed for jet traffic seven miles behind. It was the type of scenario that tests whether airplane and pilot are ready for prime time. Could the M500, known for its piston-like pattern speeds, fly fast enough down low to keep the Challenger comfortably behind us, and how easily could a transitioning pilot handle the demands of the slam dunk arrival in a high-traffic environment and blustery crosswinds?
We had no problem maintaining 155 knots, and after capturing the glideslope and starting down, we disengaged the autopilot to hand fly final. As for crosswinds, the big empennage makes landings in turbine-powered PA-46s exceptionally smooth. With power reductions and the flaps deployed, and the gear extended over the final approach fix, we had slowed to 95 on short final. That’s a little hot for standard M500 operations, but whatever the approach speed, with a landing roll of 1,020 feet, there’s rarely need for using reverse thrust, another way the M500 keeps things simple. But having jet traffic behind us altered the equation. As soon as all three wheels were down, we put the throttle into reverse and were able to exit the active at Hotel, the second turnoff, leaving the runway clear for the Challenger. That’s the kind of flying that says a transitioning pilot has arrived. With a standard equipped price of $2.264 million, the M500 can get them there with simplicity and economy.

Piper Meridian M500 Versus the World: Comparison Specs
Piper Meridian M500 Versus the World: Comparison Specs
April 10, 2015
See how competitors stack up against the Piper Meridian M500.
Article Continues Below:
Aerobatics with Matt Chapman at Oshkosh 2016
Flying magazine met up with airshow performer Matt Chapman in Oshkosh for ...
Piper Meridian M500
Designed as a step-up product for owner/pilots transitioning from light piston singles and twins to turboprop power, the M500 Meridian is a light plane (around 5,100 pounds max weight) with a true cabin and airstair door, the latest Garmin G1000 suite and a comfortable if cozy cabin. At around $2.2 million, the G500 is about twice the cost of the piston-powered Malibu Mirage. That low-$2 million price point is surprisingly lonely in the turbine world, as most light jets and turboprops have shot to near the $3 million figure or higher.
Click next to see how these five planes compare to the M500.
_**
**_
1 of 6
2015 Piper Meridian M500
**
**
**Standard Equipped Price: **$2,264,250
**Max Zero Fuel Weight: **4,850 pounds
**Engine: **Pratt & Whitney PT6A-42A,500 shp
**Max Usable Fuel: **170 gallons
**TBO: **3,600 hours
**Useful Load: **1,698 pounds
**Cabin Length: **25 feet 2 inches
**Max Payload: **1,193 pounds
**Max Cabin Width: **4 feet 2 inches
**Full Fuel Payload: **315 pounds
**Max Cabin Height: **3 feet 11 inches
**Climb Performance: **1,556 fpm
**Seating: **5 plus 1 crew
**Takeoff Distance: **1,650 feet
**Length: **29.6 feet
**Landing Distance: **1,020 feet
**Height: **11.3 feet
**Max Cruise: **260 ktas
**Wingspan: **43 feet
**Max Operating Altitude: **30,000 feet
**Max Ramp Weight: **5,134 pounds
**Vmo: **188 knots
**Max Takeoff Weight: **5,092 pounds
**NBAA IFR Range: **1,000 nm
Unless noted, specifications are from the manufacturer and are for standard conditions.
Read more about the M500 here.
2 of 6
Eclipse 550
Price: $2,895,000
Seating: 6
Max Cruise Speed: 375 KTAS
Full Fuel Payload: 702 pounds
IFR Range: 1,125 nm
Takeoff Over 50 Feet: 2,433 Feet
Cabin Length: 12.3 feet
Max Cabin Width: 4.6 feet
At a price of around $2.9 million, the Eclipse 550 is a more expensive airplane. For that extra cost 550 owners get a lot of extra bang. With a top cruise speed of around 370 knots and a max range of around 1,500 nm with reserves, on paper the lightest certificated twinjet is more than 100 knots faster with 500 nm more range. Eclipse pilots need a type rating, the costs of operation are substantially higher than on the M500, and the cabin is small.
3 of 6
Cirrus SF50 Vision Jet
Price: $1,960,000
Typical Seating: 7
Max Cruise Speed: 300 KTAS
Full Fuel Payload: 1,200 pounds
IFR Range: 560 nm
Takeoff Over 50 Feet: 2,128 feet
Cabin Length: 10.9 feet
Max Cabin Width: 5.1 feet
While the Vision Jet will require a type rating, Cirrus has designed it to be an easy jet to fly. Like the Meridian, the SF50 has a ceiling of 29,000 feet, a 1,000 nm range and no lavatory. However, the SF50 is faster (300 knots), roomier and quieter, and at just under $2 million, it’s cheaper as well. One Meridian advantage: You can buy one today. Cirrus has booked more than 500 orders for the SF50, which is scheduled for certification later this year.
See more of the Cirrus SF50 Vision Jet here.
_**
**_
_**
**_
4 of 6
Piper Malibu Mirage
Price: $1,100,450
Typical Seating: 6
Max Cruise Speed: 213 ktas
Full Fuel Payload: 538.7 pounds
IFR Range: 1,343 nm
Takeoff Over 50 Feet: 2,090 feet
Cabin Length: 12.3 feet
Max Cabin Width: 4.1 feet
Oddly enough, one of the Meridian’s chief competitors is Piper’s own Malibu Mirage, which goes for around $1 million less than the very similar Meridian. The Mirage is powered by a 350 hp Lycoming six-cylinder engine, so its fuel burn and operating costs are much lower, and its cabin is nearly identical to that of the M500. The Mirage travels 50 knots slower than its turbine cousin, and its systems are not as beefy, but it has a longer range and great runway performance.

We Fly: Piper Meridian M500
Piper Meridian M500 (Photo: Robert Goyer)
Piper recently announced the latest iteration of its Meridian turboprop single, which it now calls the M500. I'll admit up front that my initial reaction upon hearing the news was this: Whenever a company makes a name change to a product and that new name includes a number (in this case, the number 500) I have to wonder what number is about to come next. OK, end of speculation.
In this case all we know is that the new Meridian is a high-tech gussying up of an underappreciated model that deserves a second look, not just for its noteworthy new features but for its original merits too. Since its introduction a decade and a half ago, the Meridian has made good on its main selling point, that it's the easiest turboprop single for pilots to step up to after flying, say, a Bonanza G36 or a Cessna TTx. The M500 gives a lot more than such fine piston singles without asking anything more of the pilot than the aviator skills a proficient pilot of high-performance singles or light twins is prepared to give.
Article Continues Below:
Aerobatics with Matt Chapman at Oshkosh 2016
Flying magazine met up with airshow performer Matt Chapman in Oshkosh for ...
At the same time, the airplane has always had shortcomings, and the M500 doesn't address some of the most noteworthy ones. The new edition does, however, give pilots a greatly improved cockpit experience over that of previous Meridians.
One of the main gripes pilots had with the first Meridian was that its cockpit was a hodgepodge of equipment, with the little-known Meggitt Magic EFIS displays anchoring a system of various components from various manufacturers. Meggitt's Magic was to be short-lived. Piper replaced it with the Avidyne Entegra system (with Garmin navigators doing the navcom chores). A few years later Piper settled on the G1000 glass cockpit for the airplane. That G1000 system, which has been continuously updated as Garmin has improved the product, is the foundation of the avionics in the M500. This is good for a number of reasons, chiefly that the implementation of the system, from the physical arrangement of buttons, knobs and switches to the kinds of safety utilities built into the system, is about as perfect as one could hope for.
MERIDIAN THEN AND NOW
In 1999, when Piper introduced the PA-46-500TP Meridian, many thought of it as a Malibu Mirage with a Pratt & Whitney PT6 bolted on. The Mirage, Piper's previous flagship single, is a piston-powered pressurized model that descended from the company's revolutionary Malibu pressurized piston single. Back in the 1980s, the Malibu broke new ground with its high-flying small-cabin performance in an airplane that gave an easy step up for pilots of nonpressurized high-performance singles and light twins.
While the Meridian is the spitting image of the Malibu Mirage, and even though it still bears the PA-46 designation, believe me, it's a lot more airplane. According to Piper, it has limited parts commonality with the original Malibu, with the turboprop boasting an all-new wing, horizontal tail and firewall-forward section, and bigger, beefier flaps, to name just a few key differences.
As different as they are on paper, and they are, it's still hard not to compare the two airplanes, in part because they do look so much alike and in part because their target audiences look so much alike as well. It's not much of a secret that potential customers are successful individuals who want to climb high, go far and go fast while reaping the personal rewards of doing the flying themselves.
Thank goodness, that's not a small market, and it's a motivated one. The move up from the smell of avgas to the aroma of kerosene is a big deal to us pilots, and the Meridian is all about taking that leap and getting the benefits while simultaneously minimizing the costs of turbine ownership.
PT6, BABY
Clearly, the most distinguishing feature of the Meridian is its 500 shp Pratt & Whitney PT6A-42A turboprop engine. With its vaunted reliability and unmatched field experience, Pratt's segment-defining turboprop gives pilots added peace of mind compared with what you get with a piston engine, which for obvious reasons is a big deal in a single-engine airplane. The jet-A burner also provides a powerful and robust core around which to build more redundant and sophisticated systems, from primary flight controls to flaps to anti-icing boots to the pressurization system. The Meridian is heavy iron done light but done right.
While it provides far greater thrust than the 350 hp Lycoming six-banger in the Mirage, the 500 shp PT6 is a very substantial dialing down of the ubiquitous turboprop's potential power output. Some models of the engine can produce as much as 2,000 shp, four times the juice of the mill in the Meridian. The lower power rating means a few good things for Meridian owners and their net worth.
That economical fuel burn gives the M500 industry-leading economy, with a burn at cruise of just 37 gph, which, coupled with its 170-gallon fuel capacity, gives it a 1,000 nm no-wind range, with reserves.
As with nearly every transportation airplane, that range figure is largely theoretical, because it is based on operating assumptions, full fuel and a light payload that are rarely the case in actual practice. Loading in any turbine airplane is a compromise, and in the Meridian the corridor for compromise is narrower than in most turbines. You can take three skinny people and no bags and fill the tanks with jet-A, true. But if you want to take more people and bags, and that's why you're buying a cabin class airplane in the first place, then you're going to have to leave fuel off and, therefore, not go as far. To state the obvious, the more fuel you leave off, the shorter your range. At some point, the Meridian becomes a shuttle.
As is often the case, the truest explanation is found somewhere in the middle. A typical mission for me — Austin, Texas, to Wichita, Kansas, which is just under 500 miles distant — illustrates the point nicely. In the Meridian, I could take along three FAA-regulation adults and a few bags, leave off 50 gallons of fuel and still make the trip with IFR reserves (under no-wind conditions) at around 250 knots at 25,000 feet in right around two hours. For drivers of high-performance piston singles, those are sexy numbers.
If those figures seem unspectacular from a turbine point of view, you're right — they are. At the same time, however, in the Meridian you can do this in a brand-new airplane for around $2.25 million very nicely equipped. As you'll see in our "M500 vs. the World" section, at this point you can't say that about any other new airplane (at least until Cirrus starts selling its jet).
MERIDIAN IN PERSPECTIVE
After going through initial flight training at SimCom in the Meridian, I've flown the Meridian more than a few hours, though it's been a while. Since the last time I flew it, I've found myself in a few airplanes that some think of as competing against the Meridian. These include the speedy Daher-Socata TBM turboprop single, the do-everything Pilatus PC-12 turboprop single, the speedy but cozy Eclipse 500 twinjet (since supplanted by the model 550) and Cessna's small turbofan twin known as the Mustang. All of them are faster and have better range than the Meridian, but they all cost a lot more too. The truth is, though, in terms of price point and number and type of engines, the Meridian doesn't have any real competitors in the new-airplane marketplace.
Regardless, over time I'd come to think of the Meridian as an airplane that, because of its limited payload and range, falls short of where it should be. The truth, however, is subtler than that. The Meridian is an airplane that, despite its shortcomings, has some strengths that make it a desirable airplane for many pilots looking for more in terms of performance but not much more in terms of cost and complexity.
FLYING M500
It was still pretty early on a late winter morning in Vero Beach, Florida, home to Piper Aircraft, and we'd already returned from a photo flight on which I'd had 90 minutes to stare through my camera's lens at the sleek lines of the M500. I couldn't have been more eager to go flying in it.
My companion for the flight that morning was Piper's longtime flight test pilot Bart Jones, who'd also flown the airplane for the photo shoot earlier. We walked around the airplane in the low morning sun, and Bart pointed out the many significant differences between the Mirage and the M500, including a number of bigger, stronger and more redundant systems that included the fuel system, flaps, gear and vertical empennage.
Apart from the pretty new paint scheme, the upgrades to the airplane were all inside the cockpit.
If you're used to flying light singles and twins, Cirrus SR22s to Barons, for instance, the M500 will feel like a real step up. The airstair door is the first hint of that. Like everything else on the M500, it's been done right, with the appeal and convenience of a high-end portal but without any notable complexity. The back four seats, laid out in a club configuration, are comfortable enough and a step up from even nice piston-level club style six-seaters, from the Saratoga to the Beechcraft G36. The cabin of the M500 won't remind you of any Gulfstream, however. Still, it's a nicely appointed and comfortable seating area, a real step up from the piston world.
From the get-go, there are noticeable changes to the panel, which features a trio of Garmin flat panels, including a 12-inch center MFD. A bright and detailed Aspen display has been added on the far left side as the dedicated standby instrument. The flight control (autopilot) panel has been moved up; a single audio panel is situated below the MFD. Start-up is easy, though the turboprop world has yet to get full-authority digital engine controls, like fadec. Still, spin the turbine, introduce fuel and monitor the start, and you're good to go. We taxied out.
Because there's no fadec, you need to add in power carefully for takeoff while monitoring the engine gauges to avoid overdoing it. Unless you've flown old-fashioned, turbocharged piston airplanes, the skill of adding power on takeoff will be a new one, a little like rubbing your belly while patting your head.
Climb-out is impressive by little airplane standards. We selected 145 knots and saw a rate of climb of around 1,300 fpm on the standard day — we were light, around 4,500 pounds, with just me and my notepad and pen, Bart and about half-tanks of jet-A.
I was soon reminded of just how pleasant an airplane the M500 is to fly. The controls are just right for an airplane of this class, solid and predictable but not too heavy. There weren't going to be any surprises on the M500. It's a mature product with well-known performance characteristics. We climbed to 15,500 feet to try out the new envelope protection system (Garmin's ESP).
BIG DEAL
Before I had a chance to wonder what the new designation M500 really meant, I'd been clued into the changes to the new model. These amounted to an extensive set of upgrades to the G1000 avionics suite and other systems, all of them adding considerable value in the form of enhanced safety, ease of operation, added redundancy or some combination thereof, and without adding much to the price of the airplane.
The marquee attraction of the avionics upgrade is Garmin's remarkable envelope protection utility, ESP (Enhanced Stability Protection). ESP is a passive system; that is, it operates in the background, watching the airplane's performance and taking action only when the pilot begins to stray outside the airplane's normal operating parameters. With ESP, the autopilot is, in practice, always on, even when it's turned off. At those times, it operates in the background with limited but critical functionality.
Nudge is a word that Piper uses to discuss the technology, presumably because the message is that the pilot is still the one in control and only gets a tap on the shoulder when needed. It's a pretty good characterization of ESP. For instance, ESP's overspeed protection keeps the pilot, when commanding a descent, from inadvertently letting the airspeed gallop past the red line, raising the nose slightly. Likewise, if you start to bank too sharply, ESP will, up to a point, put some artificial resistance into the ailerons, making it noticeably harder to maintain that bank angle.
On my demo flight, Bart and I explored every part of ESP, and it worked great. I banked hard and felt the system add in resistance to my input. I tried stalling the airplane and watched ESP alert me to the error of my ways while automatically keeping us just barely flying along — the M500 handles great at slow speeds, by the way.
Another important improvement for the M500 is coupled go-around capability, which is possible because of ESP's underspeed protection function. Like the overspeed protection, it keeps the airplane from stalling by softly nudging the nose forward to keep the airplane flying just above stall speed. This protection is great for level-off errors, in which the pilot forgets to add in power after leveling off from an autopilot descent at the selected altitude. Underspeed protection allows an autopilot-flown go-around because it keeps the airplane from stalling should the pilot forget to add in power when initiating the go-around procedure.
We put the coupled go-around to the test, letting the Garmin GFC 700 fly ILS to Runway 10R at nearby Fort Pierce. After descending to simulated minimums, I hit the go-around button on the side of the power lever, added power, cleaned up the airplane and let the autopilot fly the missed, including entering the hold. It's just one more safety feature to help the pilot during a busy and high-risk phase of flight.
Other upgrades include ADS-B In and Out standard, a 3-D audio panel, the autopilot controller relocated to the top of the panel, where it should be, and pressurization integrated into the G1000 system — all the pilot need do is enter the destination airport, and the system does the rest. Nice.
And don't forget the new blue button on the panel, a panic button of sorts. If for whatever reason the airplane gets out of whack attitudinally, like a badly behaved teenager, all the pilot has to do is push the blue button and the autopilot sets things right. One might quibble about the usefulness of such a button — if the pilot has screwed up so badly the airplane gets to the point where such a button needs to pushed, well, there are likely bigger problems behind it. Then again, maybe a last resort button is exactly what is needed in such an instance. Besides, it's hard to find a downside to it.
On the M500 I tried it out, getting the airplane nose up, uncoordinated and slow. A touch of the blue button and a touch of power meant all was right, and right side up, in the world.
After the missed at Fort Pierce we returned to a pattern at Vero all abuzz with training traffic, entering the right downwind for 12R. In the pattern the M500 is easy and predictable. The numbers, in fact, are just a touch faster than in my SR22, and the touchdown characteristics are similar, though the long gear of the Meridian makes it seem as though you're a little high when it's time to flare. You're not. Touchdown, a little beta, and you're done. The M500 is an airplane that, in the hands of a familiar pilot, needs precious little runway, another plus to the lightest turboprop single.
I'm sure there are things that Piper could do to the M500 to make it an even better airplane, but short of adding range and payload, which would require a complete engineering redesign and add a lot to the retail price, I can't imagine what those things are. The airplane remains that perfect turboprop for pilots transitioning from the piston world, providing a range of transportation capabilities that fit not only their personal and business needs but their piloting skills too, and offering a lot of extra capability but without a lot of additional cost or complexity.

M600, Piper
We Fly: Piper M600
A clean-sheet wing, more power, touchscreen avionics and stylish interior enhancements lift Piper’s latest incarnation of the classic PA-46 to new heights.
They say that when one door closes, another opens. The trick is to stop looking at the closed door long enough to see which door is ajar. For Piper, the closed door was the abortive Altaire single-engine jet, an airplane many likened to a mini DC-10 with its Williams turbofan engine integrated weirdly into the tail. The door that opened, meanwhile, was a new version of the Meridian turboprop, which Piper would end up naming the M600.
In October 2011, with the aviation industry still reeling from the effects of the Great Recession, Piper’s new CEO, Simon Caldecott, announced the “indefinite suspension” of the Altaire jet despite the program essentially being on time and on budget. The market for very light jets appeared less certain than it had in the midst of the real-estate-bubble-fueled frenzy prior to 2008, and so the big question for Piper at the time was: What the heck do we do next?
Article Continues Below:
Aerobatics with Matt Chapman at Oshkosh 2016
Flying magazine met up with airshow performer Matt Chapman in Oshkosh for ...
The answer turned out to be a further evolution of the Meridian turboprop single that would make it stand out against a backdrop of pricier turboprops and a new crop of light jets. To pull it off, four big changes were needed. The first, and the most important, entailed designing a new wing. Piper also decided to add the latest Garmin touchscreen avionics, boost the new model’s flat-rated horsepower and improve the interior.
Piper took some of what it learned from the Altaire program and applied it to the design and manufacturing of the M600. This latest iteration of the PA-46 now features a clean-sheet wing, Garmin G3000 avionics, an extra 100 shp compared with the M500, and stylish interior enhancements that elevate the airplane well above the original Malibu Meridian introduced to the market almost 20 years ago. The changes also now put the M600 in rarefied territory within striking distance of some pricier turbine options.
Photos: Piper M600
The M600’s new wing isn’t the same as the Altaire’s, but Piper engineers who were involved in the jet program applied their experience with wing design to the latest PA-46 model. Piper started the process in late 2011 by asking dealers and customers what they wanted from the Meridian. The consensus was that it needed to fly farther, carry more and go faster — and really, what else would they say? The hard numbers many asked for included a range boost to at least 1,000 nm, a payload of 800 pounds or better and a 250-knot vmo.
With the M600, Piper not only met those goals, it exceeded the parameters while also making other noteworthy improvements. Boosting the available power of the airplane’s Pratt & Whitney Canada PT6A-42A engine to 600 shp in the M600 helped to increase performance, but engineers knew that a limiting factor in achieving more dramatic improvements in payload and speed was the original PA-46 wing. Not only would a clean-sheet wing designed using new computer load analysis lead to performance improvements, a bigger wing could also hold more fuel — it turns out, the M600’s new wing carries an impressive 90 gallons more jet-A compared with the original.
The extra fuel coupled with the improved wing translates to a welcomed increase in range, from 1,000 nm in the M500 to 1,484 nm in the M600 at its long-range cruise speed of 184 ktas (with a 45-minute reserve). At the M600’s max cruise speed of 274 ktas, range still stretches to more than 1,000 nm. Most impressive to me is the M600’s ability to carry 1,000 pounds worth of people and bags on 800 nm legs. Since there’s no option for an onboard lavatory, that’s about as far as most owners will want to travel before a pit stop, anyway.
Piper took some of what it learned from the Altaire program and applied it to the design and manufacturing of the M600.
Jim Barrett
Flying the M600
The day of my demonstration flight, I arrived at the Piper factory in Vero Beach, Florida, in pitch darkness for our planned 5:30 a.m. wheels-up time. This ungodly hour was chosen to capture first light for the gorgeous air-to-air photography that accompanies this article. Boy, was it worth it. As the sun gradually began to paint pale hues in the morning stillness, I strolled onto the ramp with Piper chief corporate pilot Bart Jones for my first in-the-flesh look at the M600. Instantly, I could see this was no stock Meridian. The new wing, with its slightly upturned tips and thick chord line, looks right at home on the PA-46 airframe. The M600’s leading-edge cuffs, with integrated deice boots and a new in-wing radar pod that houses Garmin’s GWX 70, finish off the look.
Another reason for the early start was that the FAA was scheduled to fly the M600 later in the day before granting Piper its final production sign-off. The planned handover of the first customer airplane was scheduled for the following day. I was disappointed to learn during our preflight briefing that we would be limited to an altitude of 17,500 feet because the transponder check on the airplane I’d be flying was out of date. That seemed like an odd oversight. My host ensured me, however, that Piper test pilots had really flown all the performance numbers listed in the POH, and if anything the figures err on the conservative side.
Taxiing out behind a Piper Seneca photo ship with its left door removed so that the photographer could capture the M600 in the soft morning light, we applied full power and were rolling on Vero Beach’s Runway 30L as a flight of two. We climbed out in formation as the sun appeared from behind vermillion pillars of cumulus clouds lazing offshore. Beckoning like sirens, the combination of the sea, clouds and early light served as an irresistible backdrop for our photo flight — a Florida postcard, made to order — which lasted about an hour before we thanked the Seneca crew for making us look good and got down to business putting the M600 through its paces.
The new wing, with its slightly upturned tips and thick chord line, looks right at home on the PA-46 airframe.
The first thing I noted was the M600 has a heavier feel than the original Meridian, owing to that beefier wing and the fact that the M600 is, after all, a heavier airplane than its predecessors. I would have preferred a slightly lighter feel, but control harmony was excellent, as was low-speed handling, so I can’t imagine M600 buyers will complain much once they spend a few hours at the controls and become accustomed to the extra heft required to throw the airplane around the sky.
Climbing to 17,500 feet, I left the power up and watched the speed climb to 263 ktas at our midweight with the two of us aboard, plus 200 gallons of fuel and a temperature of ISA+15. Though I wouldn’t get the opportunity to experience it, the POH shows a climb from sea level to FL 280 at that temperature and max gross weight would take 31 minutes. The increase in flat-rated horsepower provides more impressive climb times at lower weights and temperatures, while the new wing enhances performance at altitude. You can expect to see a fuel burn of right around 39 gph at a reduced power setting cruising in the mid-20s, which compares quite favorably with the competition. Daher’s TBM 930, for example, flies 60 knots faster than the M600, but it burns 60 gallons an hour and costs about $1.5 million more to buy.
That’s one reason why I’d have no qualms labeling the M600 the budget-constrained buyer’s TBM. For a base price of $2.853 million, the M600 is a compelling alternative to the pricier and speedier TBM models from Daher. Popular options will put the M600 slightly north of $3 million, but that’s still well below the TBM 930’s $4 million-plus price tag. If you can’t swing the payments on the TBM, the Piper M600 isn’t a bad compromise.
The M600’s interior is a major step above the Meridian’s, featuring better materials, better lines and a better overall look.
Jim Barrett
Interior Improvements
Where Piper has upped its game considerably with the M600 is in the cockpit and cabin. Up front, there’s the Garmin G3000 cockpit similar to the TBM 930’s, and in back, the M600’s interior is a welcome improvement over the original Meridian’s. My initial impression as I climbed through the rear clamshell door into the M600’s passenger compartment was “wow, nice.” The first thing I noticed were the USB charging ports positioned within easy reach of all the seats. Next was the overall sleek look of the interior, which features nicely rounded table accents and lower side panels, and as Piper director of marketing Jackie Carlon pointed out to me, cup holders that can actually hold a can of soda, unlike those in earlier PA-46s.
The improvements to the cabin were made in the reverse order that manufacturers typically follow, but the positive results are undeniable. Piper hired an external company to build the M600 cabin mock-up, with considerable input from the internal marketing team. Once they arrived at a design they liked, the mock-up was brought into the interior shop in Vero Beach so that production specialists could figure out how to build each piece and assemble the resulting jigsaw puzzle — and then do it over and over again on the production line. (The M600’s new interior has proven such a hit that it’s being brought to the M500 as well.)
My initial impression as I climbed through the rear clamshell door into the M600’s passenger compartment was “wow, nice.”
The inclusion of G3000 avionics was an easy choice, and it would have been the standard package in the Altaire jet had that program not been halted. The system includes a comprehensive complement of envelope protection features that are appearing on several other jet and turboprop models (such as the TBM 930, HondaJet, Cessna M2, Embraer Phenom 300, Cirrus Vision Jet and more). They include Garmin’s enhanced stability protection (ESP), which automatically returns the airplane to controlled flight if certain pitch and bank parameters are exceeded; overspeed and underspeed protections (USP), which automatically lower or raise the nose if speed decays dangerously low or climbs above vmo; emergency descent mode; and, of course, synthetic vision and ADS-B capability.
Another notable safety enhancement is the coupled go-around feature in the M600, which keeps the autopilot engaged during a missed approach, utilizing USP to prevent a stall if adequate power isn’t added by the pilot. There is also a blue LVL button the pilot can press in case of an upset to return the airplane to controlled flight.
G3000 in the M600 features three main flight displays with split presentations that allow for seemingly endless configurations of information and data. For example, the PFD can be split 60-40 to show the primary view, with speed and altitude tapes next to the digitized Jeppesen approach plate. Below the primary displays are two GTC 580 touchscreens positioned in portrait format. The touch displays themselves are great, but I think I prefer them in landscape layout, since I had a hard time pressing certain areas such as the transponder buttons, which, in my opinion, are a bit too small. The backup flight instrument is the popular Aspen Avionics Evolution PFD.
The G3000 cockpit features an array of envelope-protection technologies designed to prevent loss of control. Three high-resolution displays are positioned above a pair of touchscreens that eliminate many physical buttons and dials.
Jim Barrett
Design Goals
After spending some time getting a feel for the M600 over Lake Okeechobee, which included a series of steep turns and power-on and -off stalls with the envelope protection systems turned off, we headed back to Vero Beach for takeoffs and landings. My first arrival was the RNAV LPV approach to Runway 12R, which I hand-flew using the flight director. At slower speeds, the M600 really is a joy to fly. I made a smooth landing at the conclusion of the approach, followed by an immediate application of power for a few circuits in the pattern. The extra 100 horses in the M600 are noticeable on takeoff, with full power calling for a max torque of 1,575 pounds versus 1,310 pounds in the M500.
At reduced-power settings, I found it somewhat difficult to fine-tune the setting I wanted to nail without a certain amount of finesse with the throttle. The trick that worked for me was to make small power adjustments by grasping the throttle very low on the handle with just my forefinger and thumb. At pattern altitude, I pulled the power back to 550 pounds of torque, dropped the gear, added the first notch of flaps, and then reduced power on final and added landing flaps (as is the trend in many airplanes today, the M600 has only three flap settings: up, approach and landing). Slowing to 80 to 85 knots on short final felt just right, and all my landings were smooth. The M600’s brakes are big and beefy, though beta thrust is somewhat lackluster.
With the M600, Piper has upped its game considerably, producing what some buyers will perceive as a less expensive and more economical alternative to Daher’s TBM 930.
Jim Barrett
The PA-46-600TP earned its type certification earlier this year, and a handful are now flying with customers. Piper has selected Legacy Flight Training in Vero Beach for M600 initial training. A five-day course is included in the airplane’s purchase price. Warranties on the airframe, avionics and propeller are five years, while the engine has a seven-year warranty from Pratt & Whitney. Despite the increase in power, engine TBO remains 3,600 hours.
Options available on the 2016 M600 include Garmin’s Surface Watch taxi safety system, an Iridium voice and data transceiver for worldwide calling and text, TCAS I traffic collision avoidance system, and a variety of bundled option packages. The GWX 70 weather radar, deice boots, USB charging ports, Aspen standby instrument, and envelope-protection safety features all come standard.
With the M600, Piper has met its design goals and then some. It delivers what the market asked for, which was a much-improved PA-46. With operating economics that are the envy of many other turboprop owners, and a cockpit and cabin finally on par with the top-tier competition, it’s not a stretch to say that certain buyers who are considering a TBM will also take a close look at the M600 and ask if the performance trade-offs are worth the savings. For some, the answer will undoubtedly be yes.
2016 Piper M600
Base price$2.853 million
EnginePratt & Whitney PT6A-42A (flat-rated 600 shp)
PropHartzell 4-blade
Cabin length12.2 feet
Max cabin width4.1 feet
Max cabin height3.75 feet
Seats6
Length29.8 feet
Height11.4 feet
Wingspan43.2 feet
Wing loading28.71 pounds/square foot
Power loading10 pounds/shp
Max ramp weight6,050 pounds
Max takeoff weight6,000 pounds
Standard empty weight3,650 pounds
Useful load2,400 pounds
Max usable fuel260 gallons
Payload (full fuel)632 pounds
Max range1,484 nm
Fuel flow (max cruise)48 gph
Fuel flow (long range)39 gph
Max operating altitude30,000 feet
Max cruise speed274 ktas
Stall speed (MTOW)62 kias
Takeoff, 50-foot obstacle2,635 feet
Landing, 50-foot obstacle2,659 feet

Putting the Cessna Mustang to Work
J. Mac McClellan takes the second Citation Mustang out for two days courtesy of Textron Aviation. The article goes in depth on many of the individual characteristics of the aircraft and how it flies in the hands of an owner-pilot.
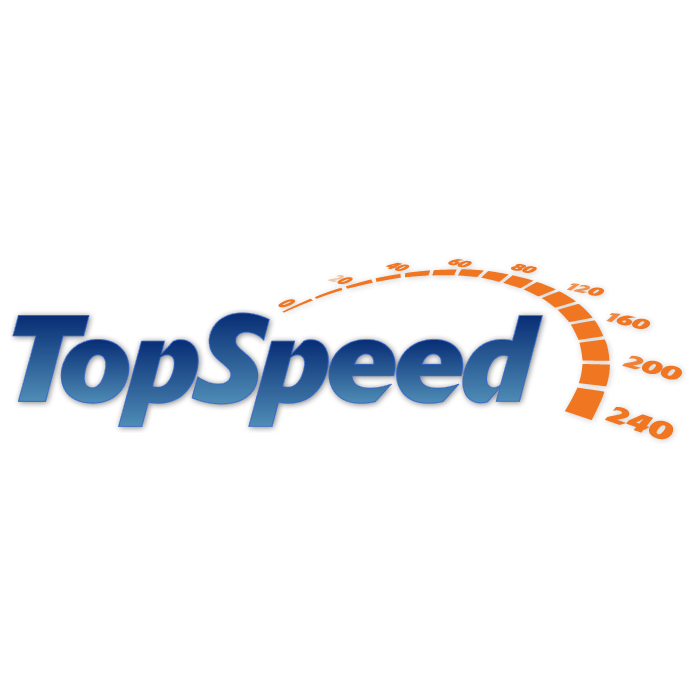
2006-2010 Cessna Citation Mustang
A complete guide to the light jet made by Textron Cessna. This source contains information about the aircraft during its production run from 2006 to 2010. Avionics, performance, costs, and flight characteristics are some of the many specific categories that the article expands upon. Read this article to gain further understanding of the components of the aircraft and how it may suit your flying needs.

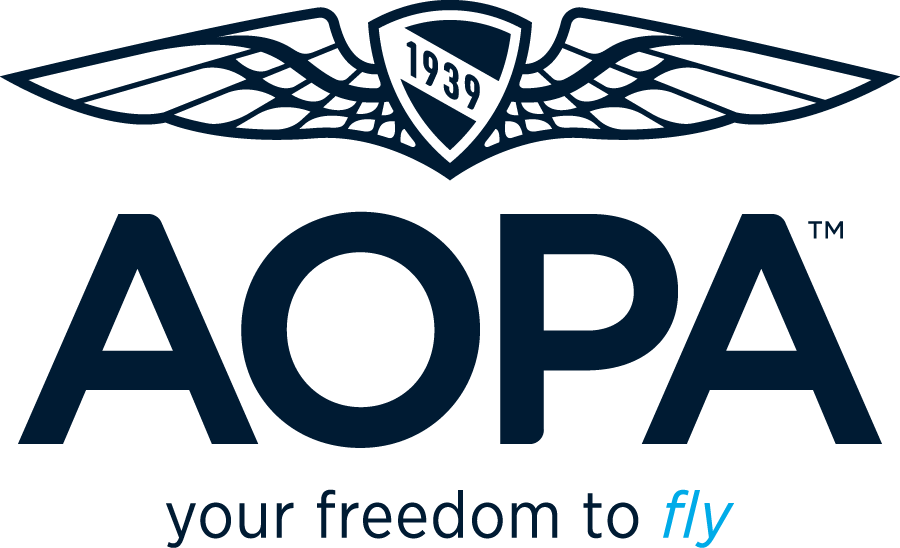
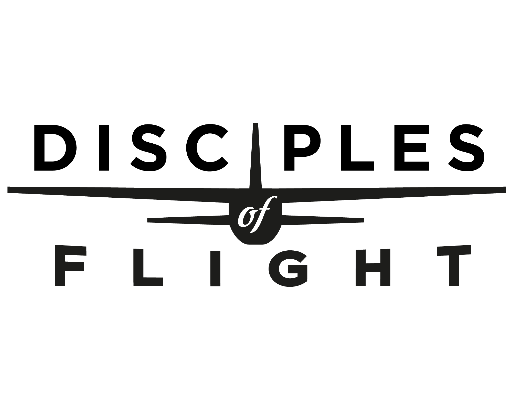


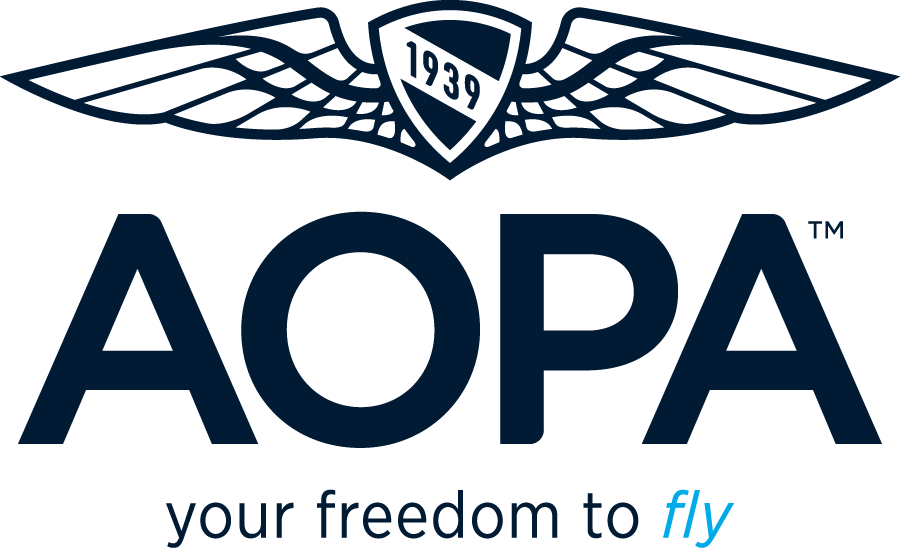


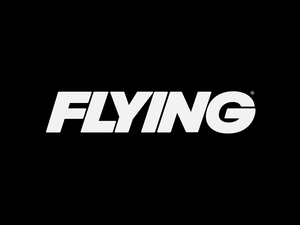
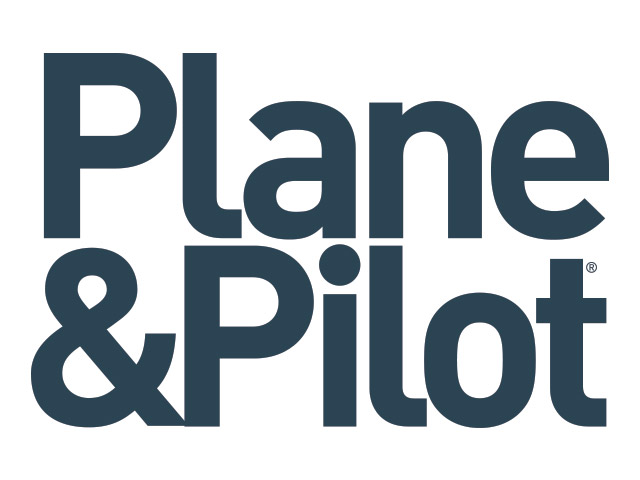


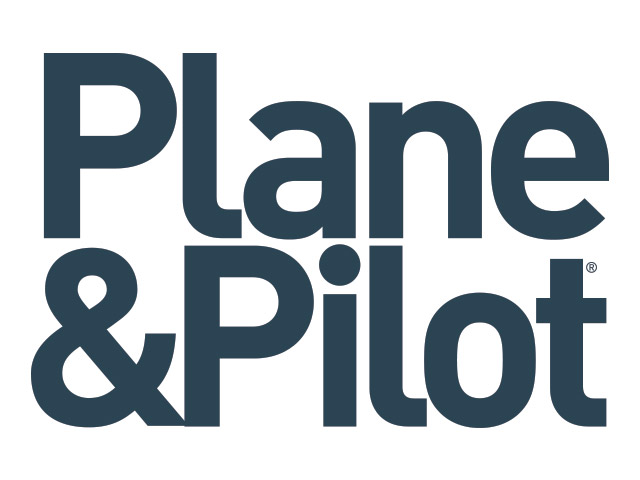
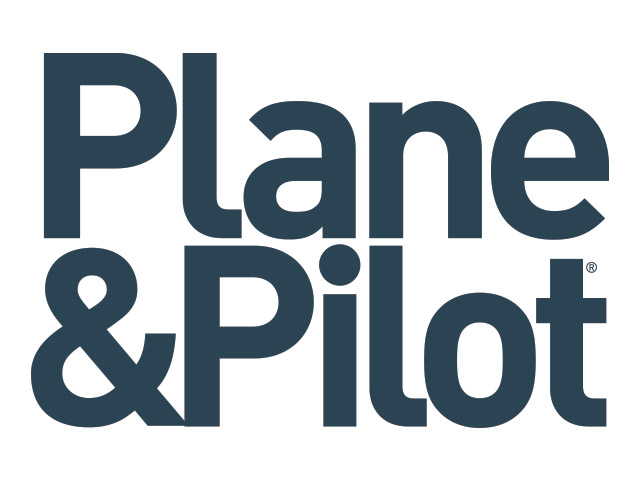



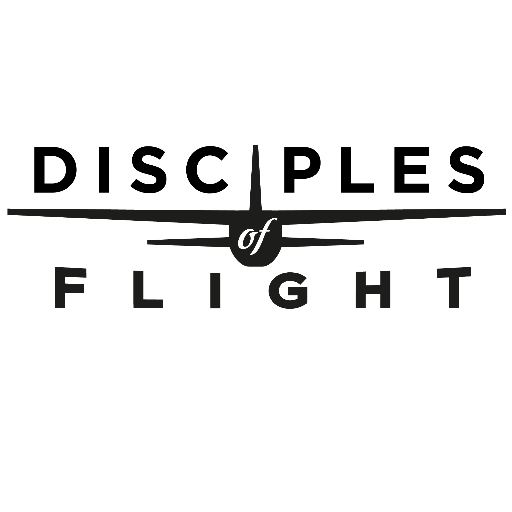


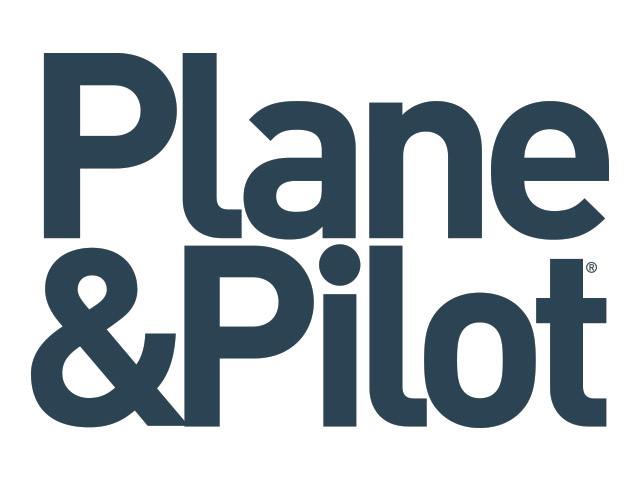


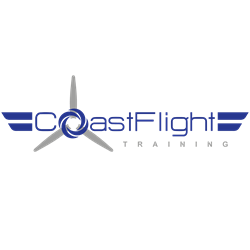
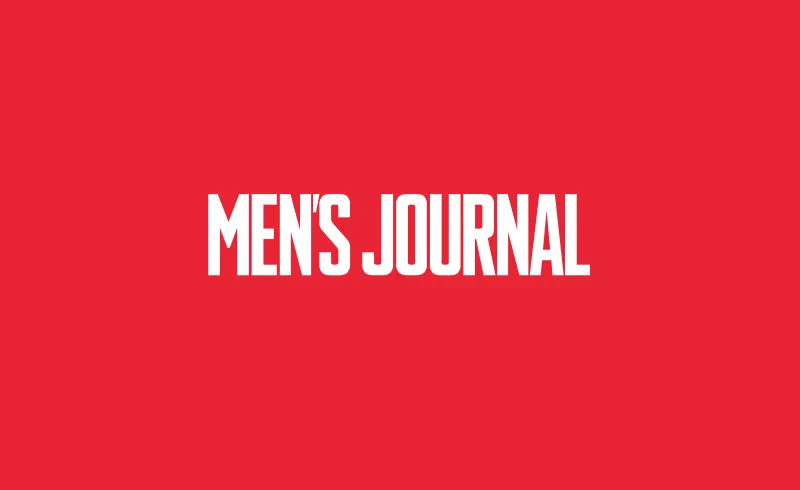
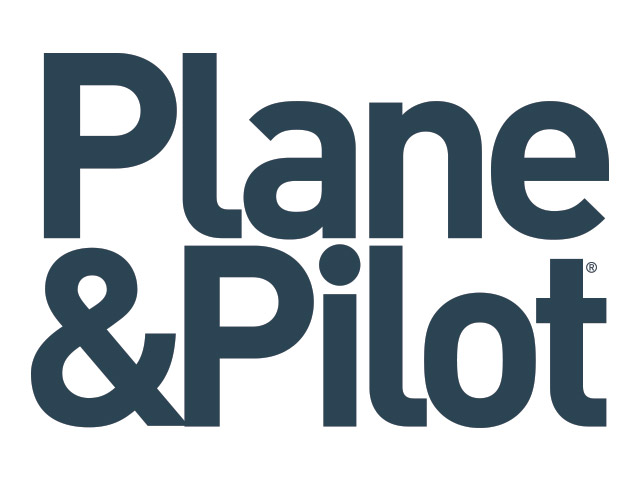




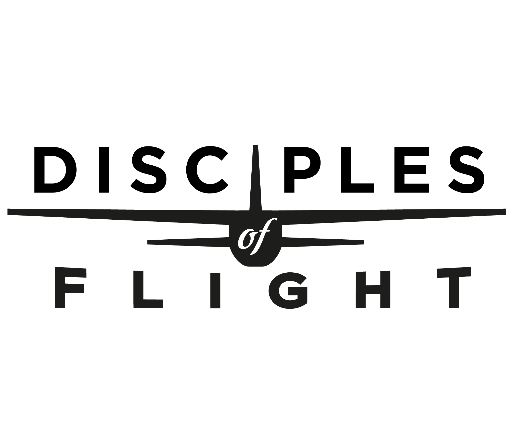


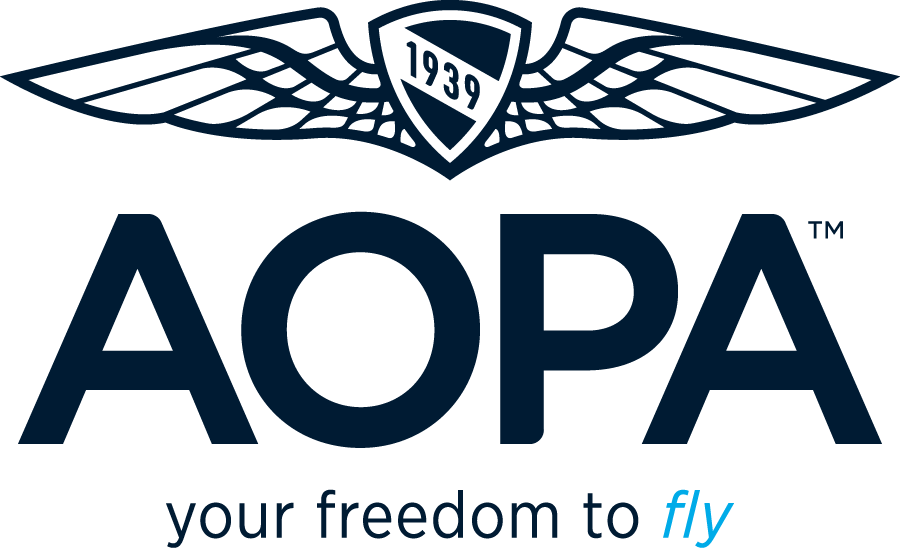




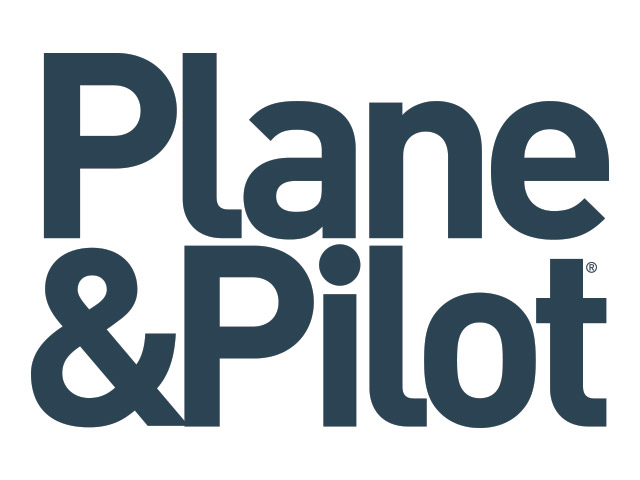






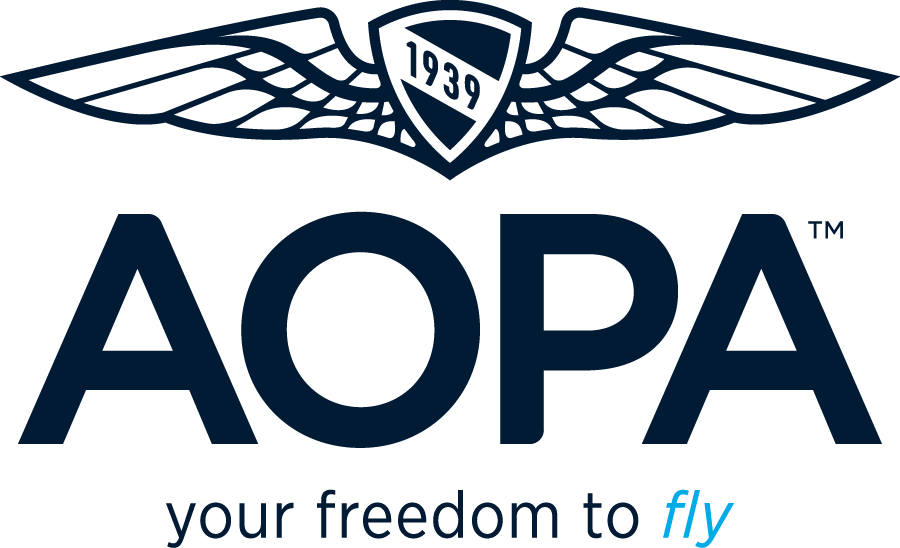

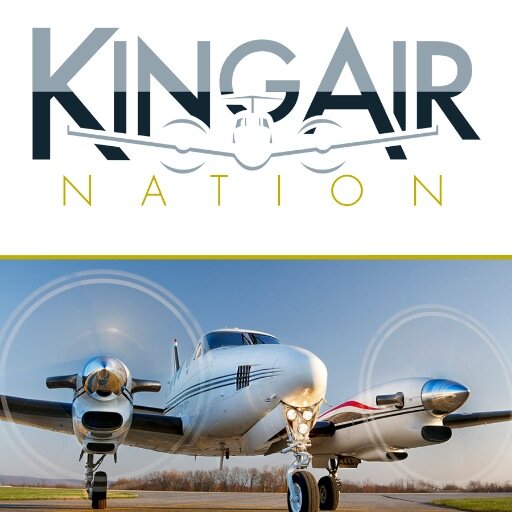



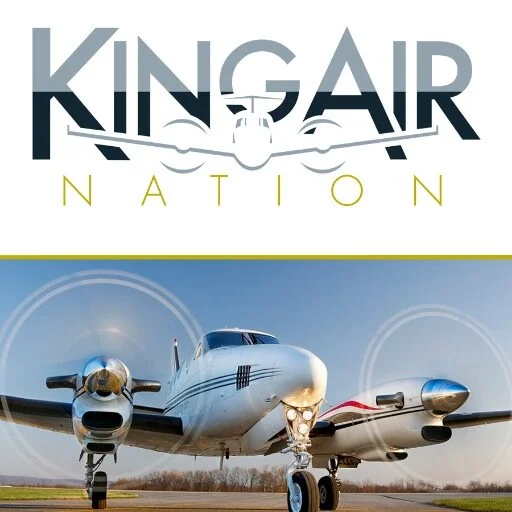




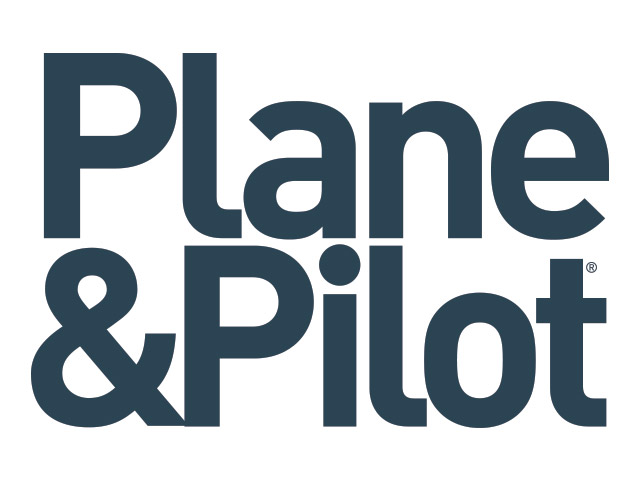



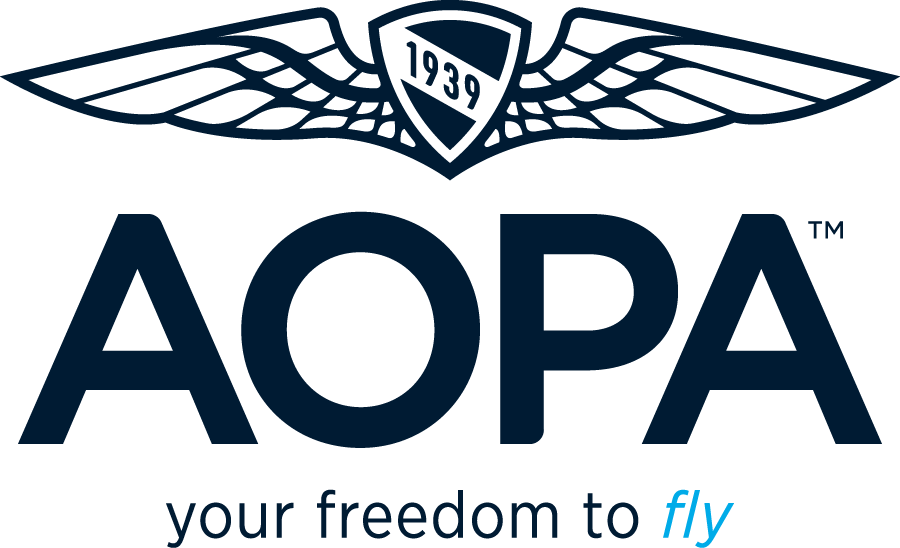



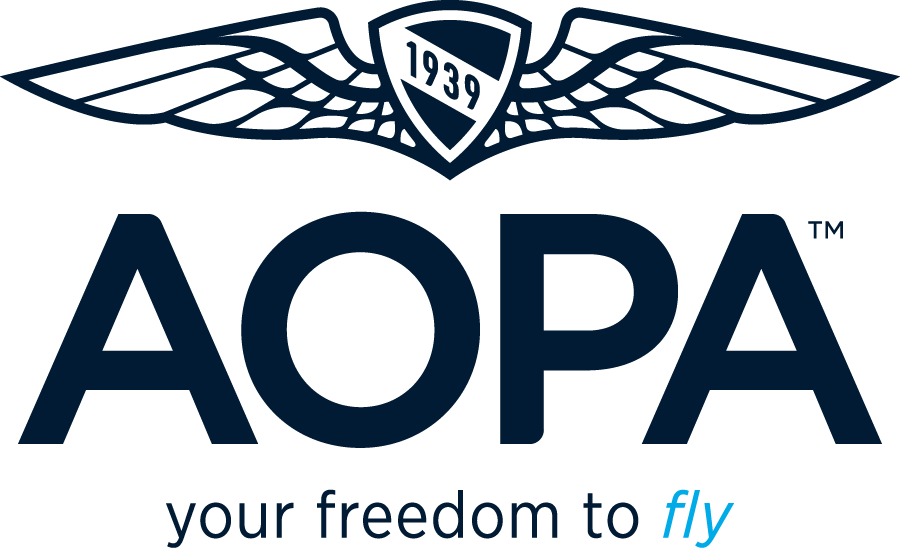
















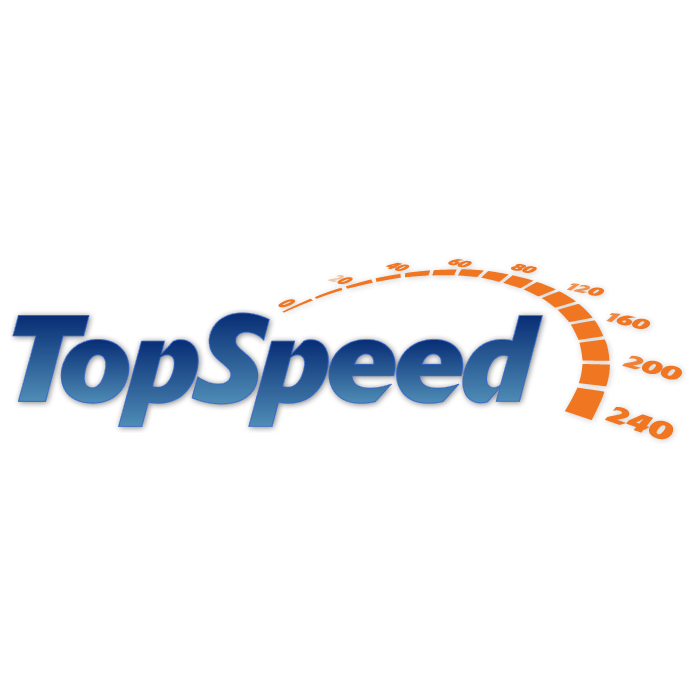

